【摘要】:图5-8 DoP型三维打印自由成形支架a)原理图 b)外形照片用DoP型三维打印自由成形工艺制备的支架孔径较小,且孔径与粉材的粒径有关。上述研究表明,三维打印自由成形技术在制备支架方面极具潜力。用有机溶剂(如氯仿)作粘结剂时,干燥一周后,在三维打印自由成形的支架中会有残留0.5%的氯仿。
1.DoP型三维打印自由成形支架
在铺设的粉材上喷射粘结剂的DoP型三维打印自由成形是支架制备方法中应用最广的一种成形工艺(见图5-8)[10],这种工艺操作简便易行,可用于多种粉末材料的成形,成本较低。其制备支架的过程如下:根据计算机设计的支架形貌,在预先铺设了粉材的工作台上,喷头沿X轴和Y轴运行,在粉材的表面选择性地喷射粘结剂,粘接临近的粉末形成支架的二维结构,然后,工作台下降一个层厚,在其上再铺设一层粉材,重复上述过程,直到三维支架成形完成。通过改变打印的速度、粘结剂的流速及喷射位置可调节支架的微观结构。
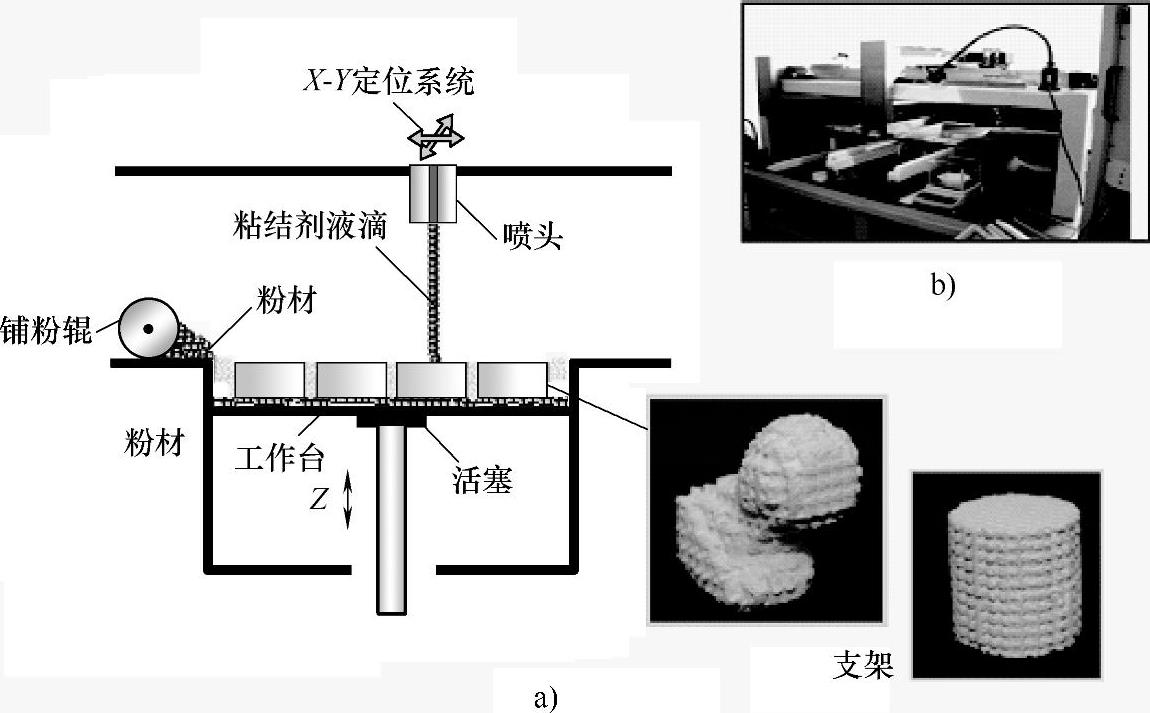
图5-8 DoP型三维打印自由成形支架
a)原理图 b)外形照片
用DoP型三维打印自由成形工艺制备的支架孔径较小(常小于50μm),且孔径与粉材的粒径有关。为了缩小支架的孔径、提高孔隙率,可将三维打印自由成形工艺与粒子沥出法相结合[18],例如,采用聚乳酸聚乙醇酸(PLGA)粉材和盐粒的混合物为原料,用有机溶剂作为粘结剂,可制得直径为8mm、高度为7mm的圆柱状支架,用去离子水沥出盐粒后,支架的孔径为45~150μm,孔隙率为60%。
由于打印过程中有机溶剂或粘结剂对细胞生长会产生不利的影响,可采用水基粘结剂(聚乙烯醇水溶液、去离子水)来制备天然高分子材料支架。例如Lam等开发了含有50%玉米淀粉、30%右旋糖酐和20%明胶的淀粉基支架,为了提高支架的机械强度和耐水性,再将其浸入75%PLA(聚乳酸)和25%PCL(聚己内酯)的二氯甲烷溶液中,浸入后圆柱状支架的孔隙率略有降低,由59%降为54.7%。还有研究者在经三维打印技术预先制备的模具中注入低温胶原乙酸溶液,利用乙醇溶解模具后,将胶原支架在液态二氧化碳中干燥,最终得到了保持生物活性的胶原支架。上述研究表明,三维打印自由成形技术在制备支架方面极具潜力。
用有机溶剂(如氯仿)作粘结剂时,干燥一周后,在三维打印自由成形的支架中会有残留0.5%(即5000ppm[1])的氯仿。根据有关规定,药物中的氯仿允许含量是60ppm。为克服上述问题,可以用液态二氧化碳提取三维打印支架中的氯仿,使其残留量小于50ppm。
三维打印自由成形的缺点是:难以清除支架深处复杂管道特征处的支撑粉材。
图5-9是采用DoP型三维打印自由成形的支架,其中图5-9a是未去除孔洞中无用粉材的支架,图5-9b是已去除孔洞中无用粉材的支架[4]。
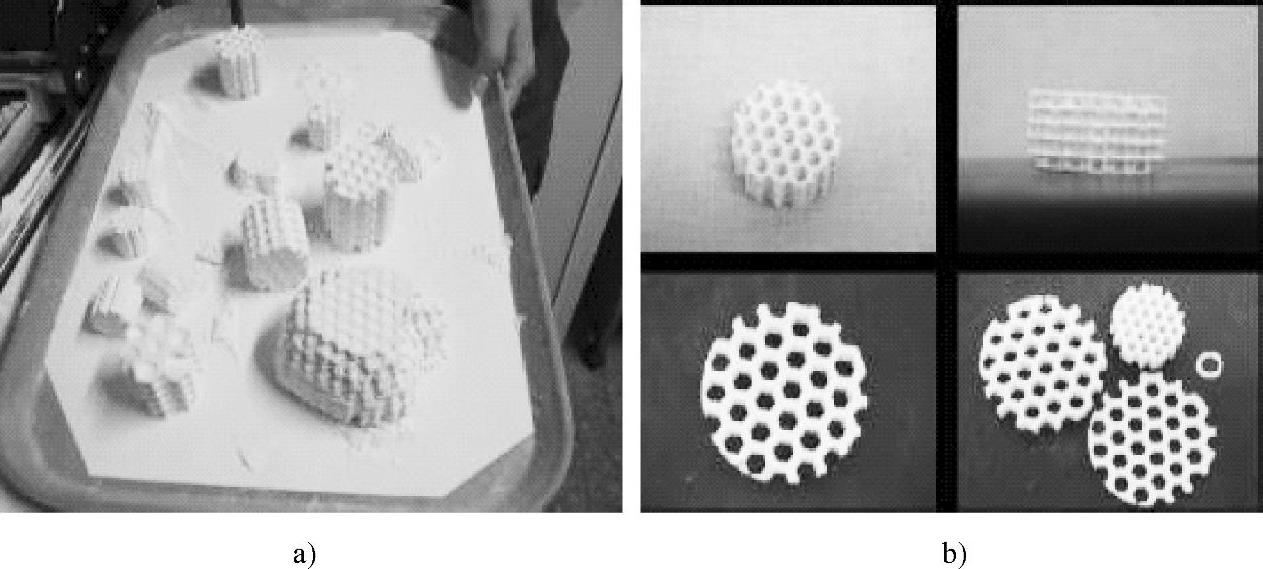
图5-9 DoP型三维打印自由成形的支架[2]
本章参考文献[13]报道,有人将磷酸三钙(tricalcium phosphate,TCP)、阿拉伯胶(arabic gum)和纤维素(cellulose)的混合粉材进行支架的DoP型三维打印自由成形,第一种配方为:65%(质量分数)TCP、20%(质量分数)阿拉伯胶和15%(质量分数)纤维素,第二种配方为:75%(质量分数)TCP、20%(质量分数)阿拉伯胶和5%(质量分数)纤维素。其中,阿拉伯胶在水中有高溶解度,常用作增稠剂和粘结剂,因此有助于将粉材粘接在一起。纤维素是用植物制成的一种多聚糖(polysaccharide),由β-D葡萄糖(glucose)组成,它的形态呈纤维状,有利于打印时使其他微粒保持在一起,并在去除粘结剂时用于产生贯通的孔隙。支架打印成形后在70℃下干燥2h,然后,以1℃/min的加热速度在700℃的炉中热处理1h,以便去除粘结剂,再以5℃/min的加热速度烧结至1200℃,并保持3h。
本章参考文献[15]报道,支架DoP型三维打印自由成形的材料可以是天然聚合物,他们包括:木薯淀粉(cassava starch)、麦芽糖糊精(maltodextrin)、纤维素纤维(cellulose fiber)和凝胶(gelatin),这些材料呈粉末状,颗粒尺寸为20~200μm。用蒸馏水作为粘结剂。渗透材料为光固化牙封闭剂(light cured dental sealant)。
三维打印件的后处理通常是在室温下进行渗透,为此,将成形件置于液态渗透剂(如树脂)中,使整个工件自然地受到毛细作用力,然后,用棉纸擦拭已渗透的工件,去除工件表面多余的树脂,再用卤素灯使渗透部分固化1h。
本章参考文献[26]报道,美国密歇根州立大学的Hollister等学者用三维打印自由成形技术制造蜡或PSA(聚砜酰胺)支架负型模具,并在填充HA(羟基磷灰石)浆体后经烧结工艺去除有机质,可形成复杂结构的HA多孔支架,然后将PLA(聚乳酸)浇注在HA支架上形成PLA/HA双层支架。其PLA部分孔径为600μm,HA孔径为500μm。Schek等人在此基础上,制作了PLA/HA双层软骨与骨复合支架,以PLA为软骨端,以HA为骨端,并在PLA和HA材料之间沉积一个PGA(聚乙醇酸)薄层,以防止细胞在软骨与骨区之间的迁移。然后,在该支架的HA骨端种植带有BMP-7(骨形态发生蛋白)的纤维原细胞,在PLA软骨端种植软骨细胞。
本章参考文献[30]报道,都柏林城市大学的Tamas Szucs用三维打印自由成形工艺制作了磷酸钙陶瓷(Calcium Phosphate Cements,CPC)支架(见图5-10),粉材的颗粒平均尺寸约40μm,粘结剂为磷酸钠水溶液。打印所得支架生坯件的平均弹性模量E=3.59MPa,平均抗压强度σy=0.147MPa,在1100℃下烧结1h后E=9.15MPa,σy=0.483MPa,支架的孔隙率为70%~80%。
2.DoD型三维打印自由成形支架
近年来发展起来的DoD型三维打印自由成形支架的方法如图5-11所示。
图5-12是台湾中央大学研制的一种成形组织工程支架的DoD型三维打印自由成形系统[2],它采用不锈钢注射器的针筒储存支架材料,借助氮气使加热熔融的支架材料从喷头(喷嘴内径为0.1mm、0.15mm、0.2mm、0.3mm)喷出,并沉积于移动工作台上,此工作台用固态干冰冷却至-15~-25℃。支架材料中预先加入了合适的溶剂,混合成均匀的溶液。这种溶液沉积在低温工作台上后会冷冻固化成形,然后将冷冻固化的支架置于冷冻干燥机上,去除其中的溶剂便可得到所需支架(见图5-13)。工作台也可不用干冰冷却,由喷出的熔融材料在室温下自然冷却成形(见图5-14成形的聚乳酸耳软骨支架)。
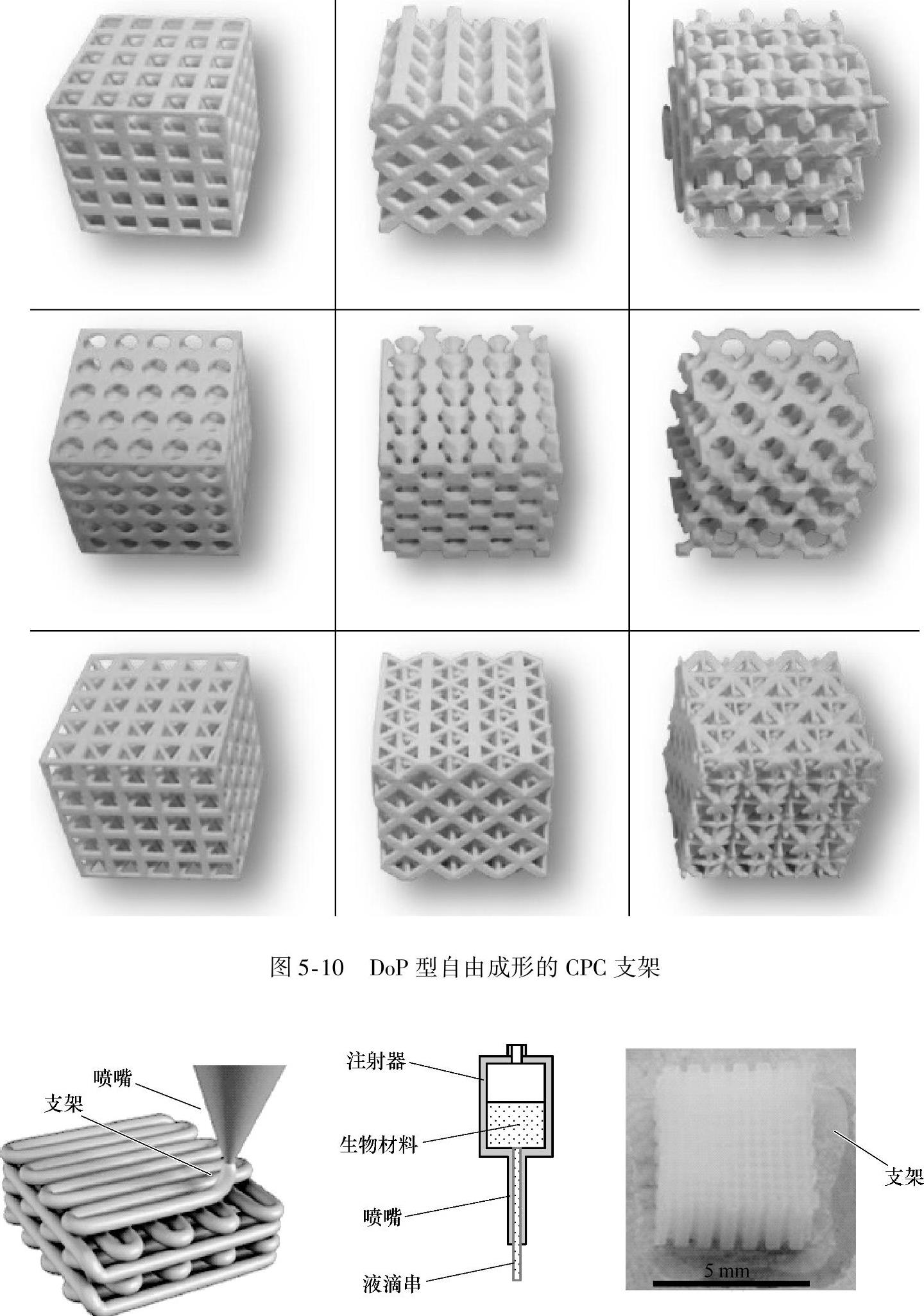
图5-11 DoD型三维打印自由成形及其制作的支架
图5-15和图5-16所示为两种采用反应相变固化原理的DoD型三维打印自由成形过程及其制作的支架。
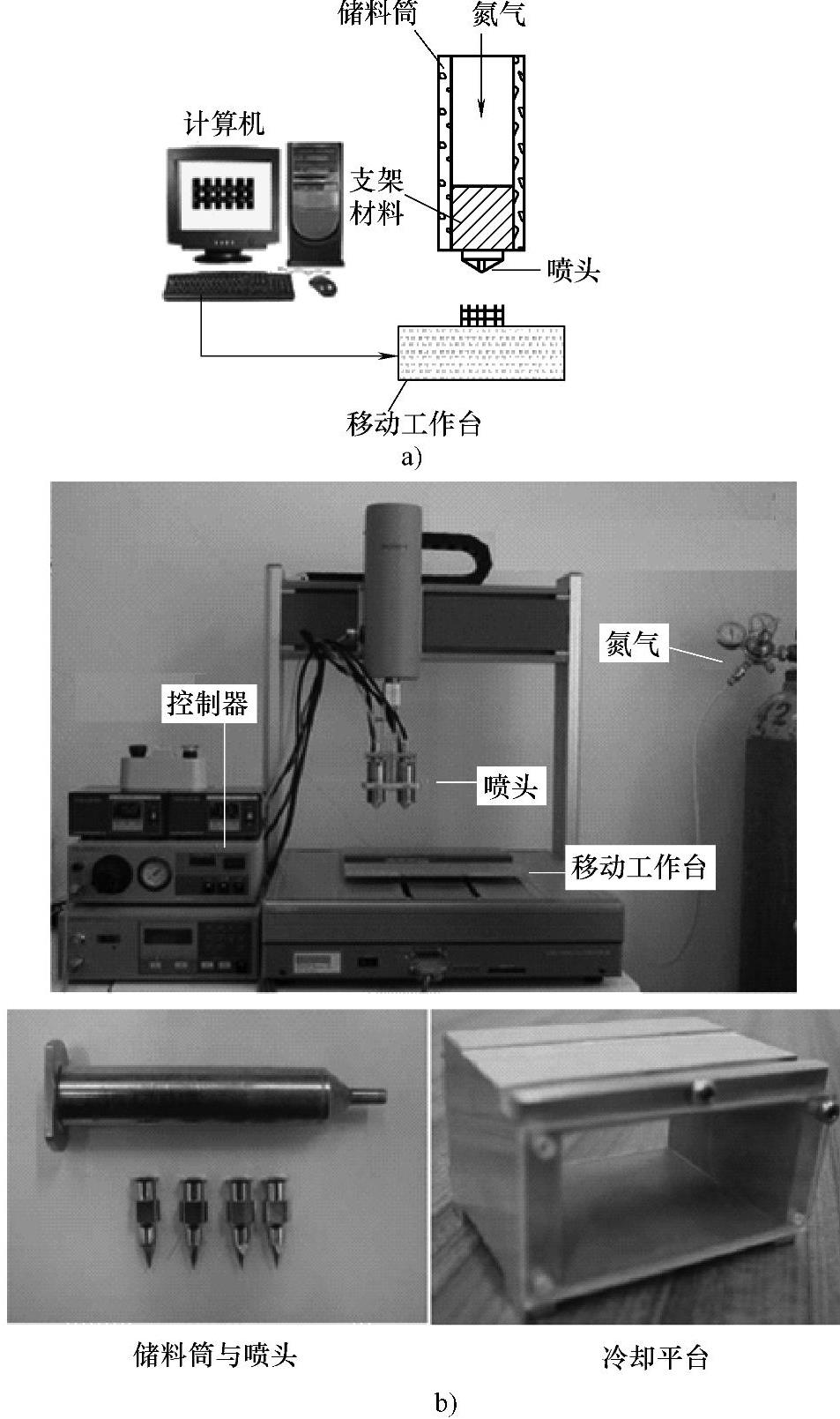
图5-12 PAM冷冻式支架DoD型三维打印自由成形系统[2]
a)原理图 b)外形照片
其中,图5-16所示系统常用于制备水凝胶支架,其关键是将流体或糊状成形材料分散于液体介质中,该技术适用于众多的合成材料和天然材料。由于生物体中的许多软组织具有类似水凝胶的结构,因而用该方法制备的具有确定外部形状和良好内部孔结构的水凝胶支架,会在药物释放载体、软骨支架和人工细胞外基质方面显示出良好的应用前景。
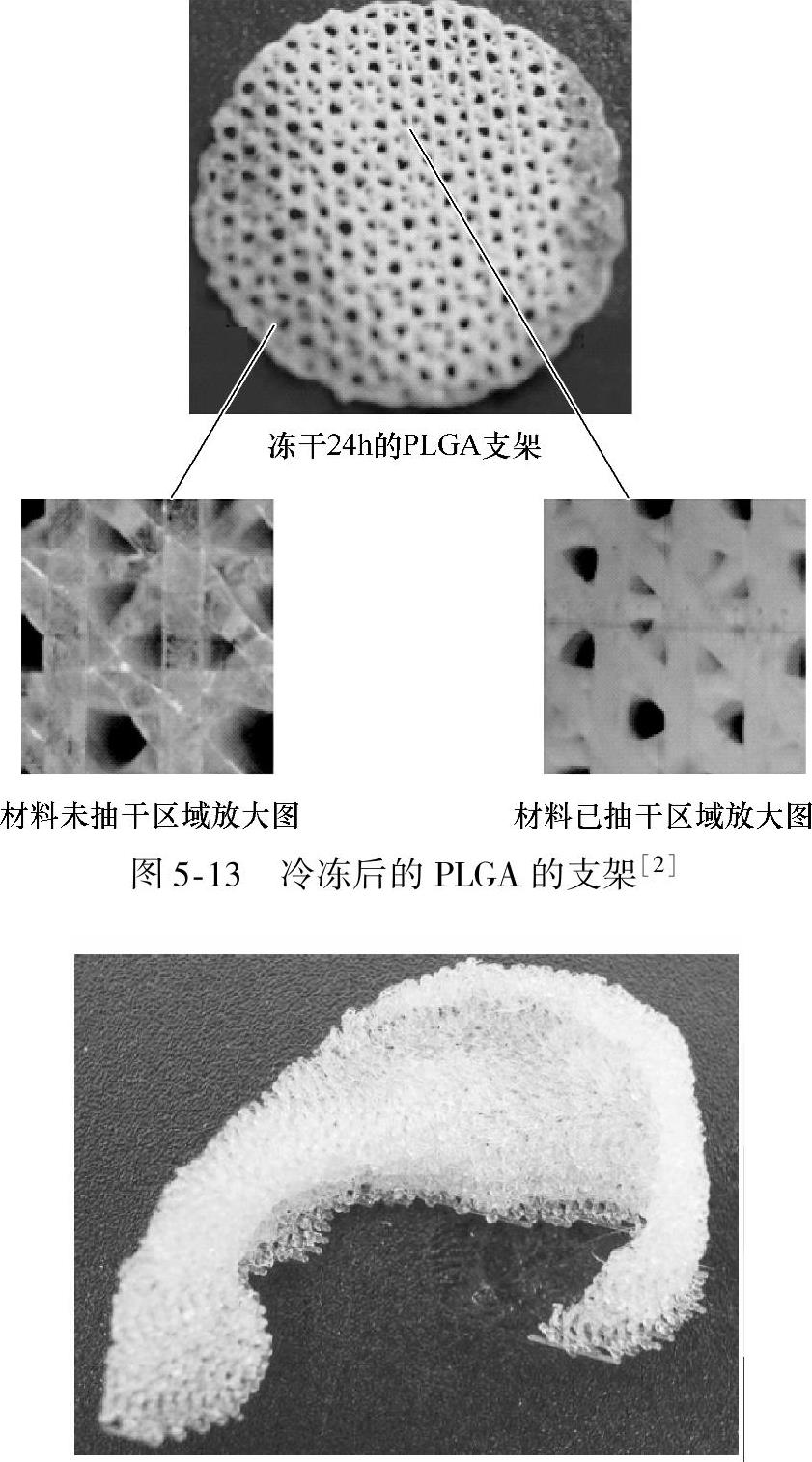
图5-14 成形的耳软骨支架
图5-16中的夹套用金属材料制成,其内注入了加热至250℃的热油,或者夹套用玻璃制成并用电加热,以便达到更高的加热温度。
3.静电纺丝自由成形支架[50]
静电纺丝技术基于电流体动力学原理,在静电纺丝系统中(见图5-17),注射器的针头(喷嘴)和接地的接收屏之间有几千至几万伏的高压静电,此电场力施加于针头中流体的表面并在表面产生电流,相同的电荷相斥导致电场力与流体的表面张力方向相反。当这两个力的大小相等时,带电的液滴将悬挂在毛细管的末端并处于平衡状态;随着电场力的增大,在毛细管末端呈半球状的液滴在电场力的作用下被拉伸成圆锥状(称为泰勒锥);当电场力超过临界值后,液滴将克服表面张力形成射流,射向接收屏并被电场拉伸,在接收屏上形成纳米纤维。
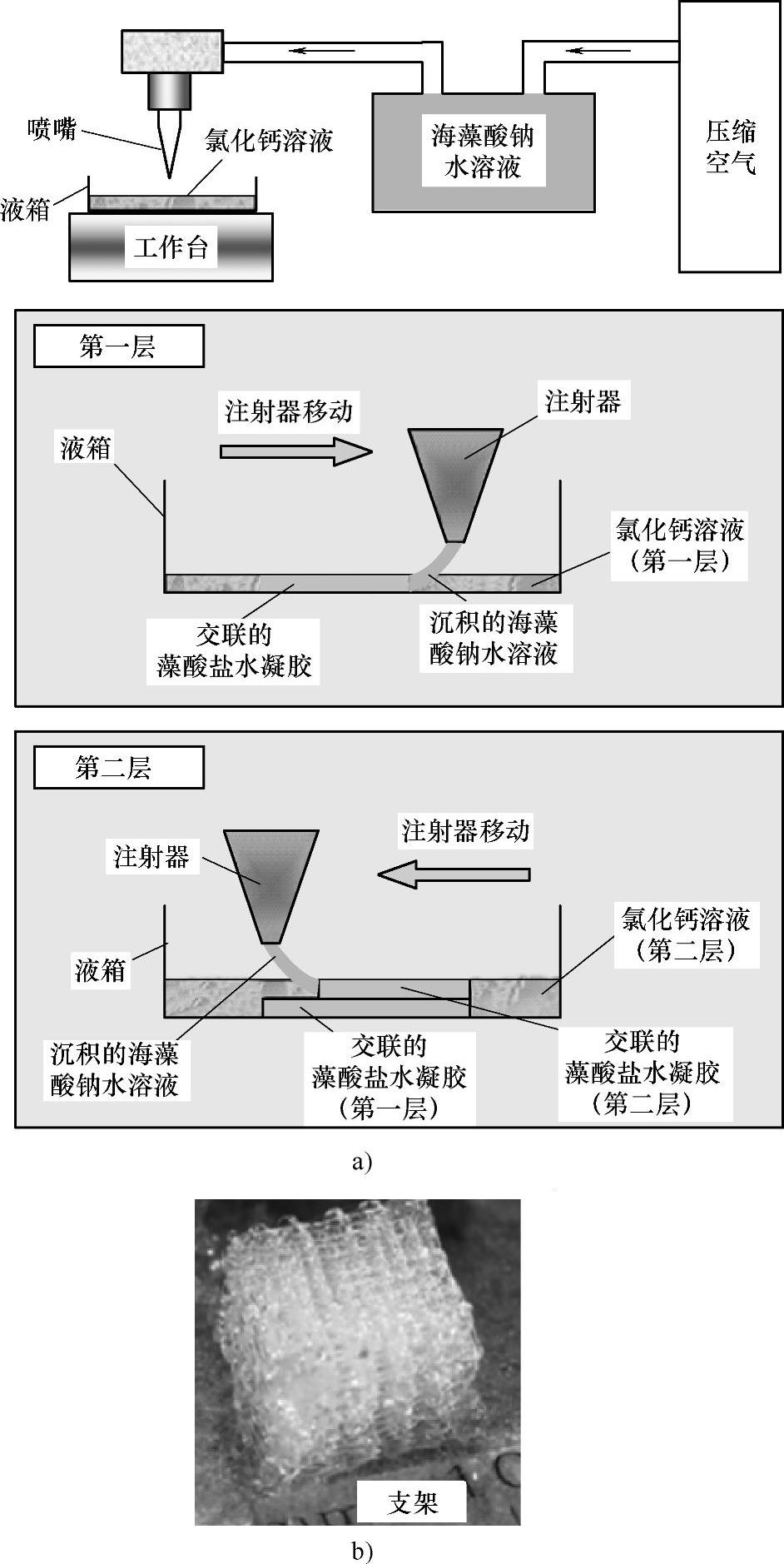
图5-15 DoD型三维打印自由成形过程及其制作的反应相变固化支架(1)[3,11]
a)成形过程b)成形的支架
通常成形支架的静电纺丝系统采用的原材料为溶液状态,因此称为溶液静电纺丝(solution electrospinning)。采用这种系统制作支架时,必须首先用溶剂(如氯仿、
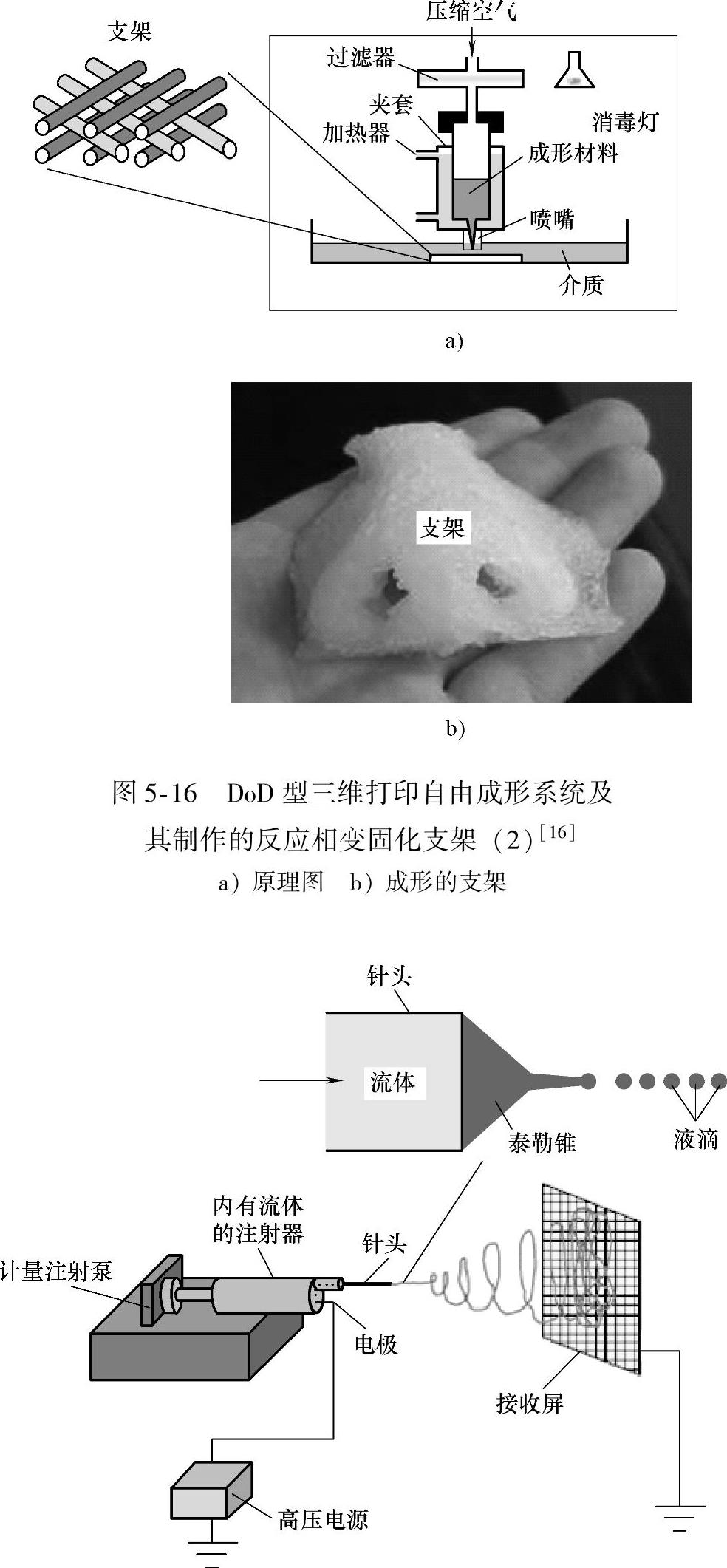
图5-17 静电纺丝系统
丙酮等)使支架的基料(如生物兼容聚合物)溶解为溶液,然后才能进行静电纺丝。由于所用溶剂有毒性,因此必须使支架中的溶剂挥发,这不但麻烦而且还可能因为有溶剂残留造成危害。为克服上述问题,出现了熔体静电纺丝(melt electro-spinning)系统,采用这种系统制作支架时,通过加热使支架的基料成为熔体便可直接进行静电纺丝,无需加入任何溶剂。
采用溶液静电纺丝系统时,聚合物的粘度不得超过4Pa·s;然而采用熔体静电纺丝系统时,聚合物的粘度可更高,在此情况下,可以用图5-18所示加热方法降低聚合物的粘度,使其适合静电纺丝。其中,电加热法(见图5-18a)是在注射器针头的外面设置电热元件(如电阻丝),采用这种加热方法时为避免电热元件因承受静电高压而损坏,可将高压直流电源的正极与接收屏相连,注射器的针头接地;加热枪加热法(见图5-18b)是用加热枪产生的热风加热针头,这种方法难以精确控制针头的温度;循环液加热法(见图5-18c)是在注射器的外面设置空心外套,并在外套中通入热循环液(水或硅油),这种方法能提供稳定和控制良好的热源,温度波动很小,用硅油加热时可达到255℃的高温;激光束加热法(见图5-18d)用激光束直接加热成形支架的固态聚合物丝料端头,聚合物被加热的部位很短,这对于热敏感聚合物的加热很有利。
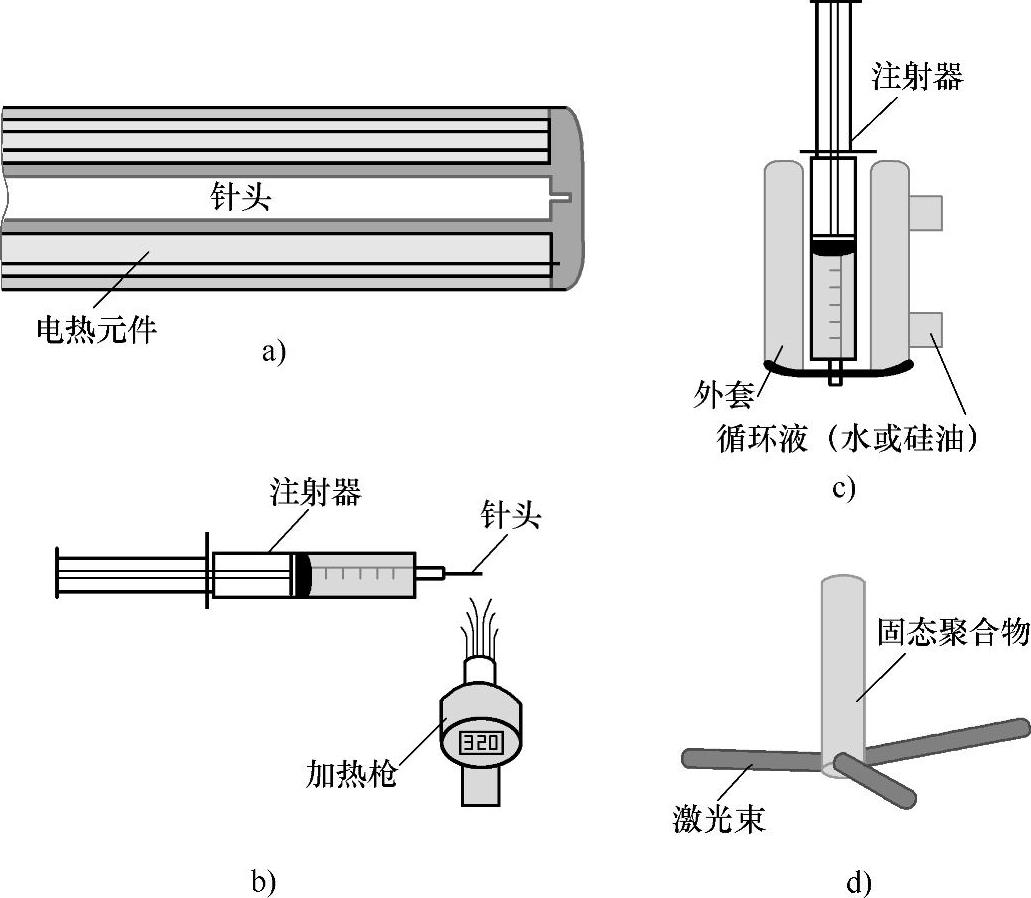
图5-18 熔体静电纺丝系统的加热方法
a)电加热 b)加热枪加热 c)循环液加热 d)激光束加热
熔体静电纺丝时常见聚合物的加热温度如表5-1所示。
采用静电纺丝时,成形支架的纤维直径与小孔尺寸的关系如图5-19所示,由此图可见,纤维直径必须小至4μm才能使小孔尺寸达到20μm。
表5-1 聚合物的熔体静电纺丝温度
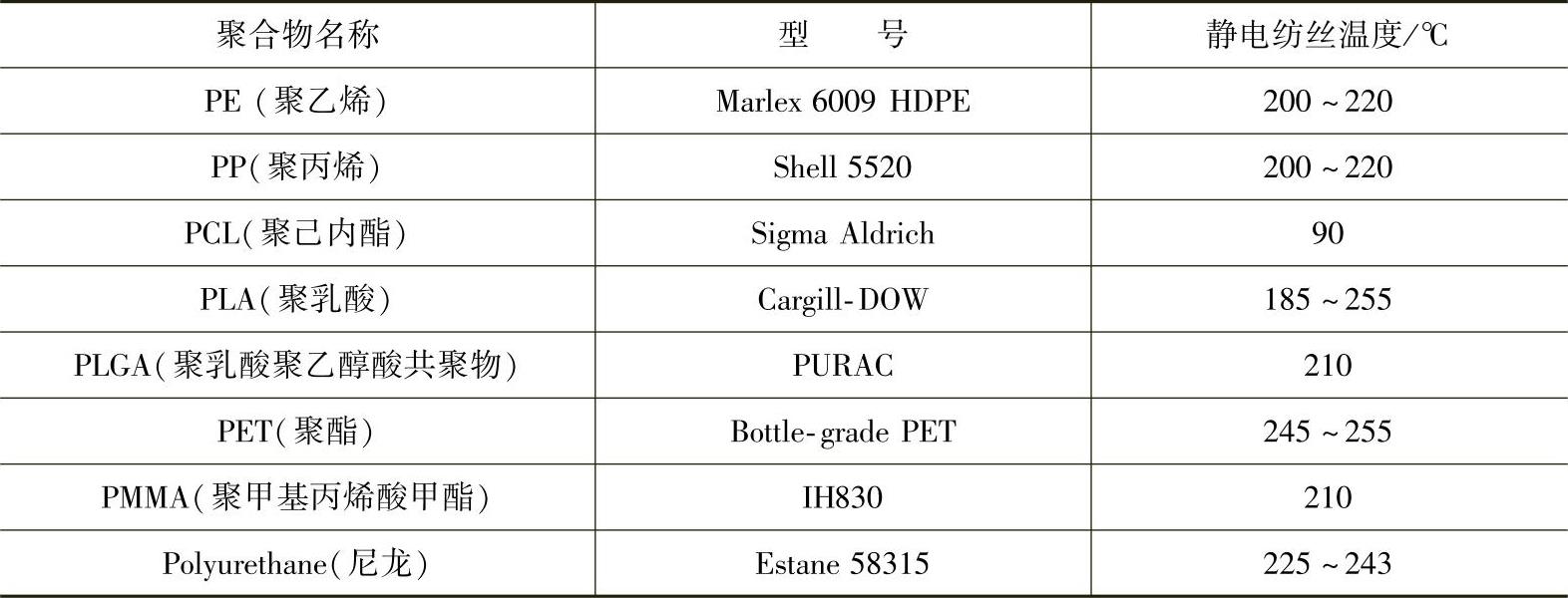

图5-19 溶液静电纺丝时成形支架的纤维直径与小孔尺寸的关系
也可组合应用溶液静电纺丝与熔体静电纺丝(见图5-20)来成形支架。其中,用溶液静电纺丝成形较小直径的亚微米级纤维(例如530nm±240nm),用熔体静电纺丝成形较大直径的微米级纤维(例如28.0μm±2.6μm或14.6μm±2.4μm),这种方法与单一注射器静电纺丝两种不同直径纤维相比,有更好的一致性。
中国的台湾成功大学用静电纺丝技术制造了组织工程血管支架(见图5-21)[49],材料为PCL在二甲基甲酰胺与二氯甲烷溶剂中的溶液,接收器为转轴,改变刀片相对转轴的角度和转轴的转速可改变喷射纤维的排列方向,从而得到具有弹性的管状血管支架(见图5-22)。在此支架中均匀植入体外培养的细胞后,将其置于生物反应器中(见图5-23),形成可植入人体的人工血管。
4.支架熔融挤压自由成形
采用熔融挤压自由成形工艺制备支架(见图5-24)的过程如下:首先将待用的支架材料拉成丝料,再用此丝料作为原材料,通过熔融挤压自由成形机的喷头,使丝料熔融并选择性地沉积在工作台上,逐层构成支架的二维结构,然后,工作台下降一个层高,重复上述沉积过程,直到形成三维支架。通过改变沉积的路径、宽度、间距,可成形不同层状结构和不同蜂窝状孔隙形态的支架,并可调控孔隙内部贯通性。所用丝料的熔点不能太高,常用的有脂肪族聚酯PCL和PCL/HA复合材料。有人曾经用熔融挤压PCL丝材来成形蜂巢状支架,其孔隙率可达48%~77%。
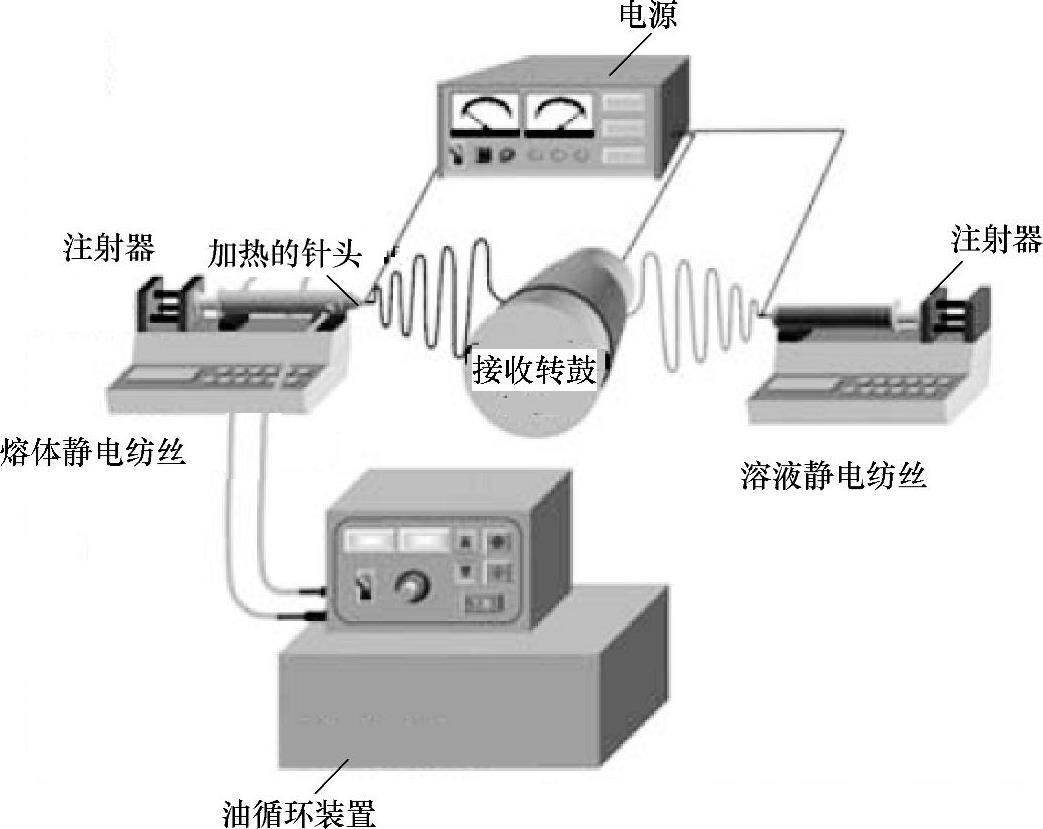
图5-20 溶液静电纺丝与熔体静电纺丝的组合
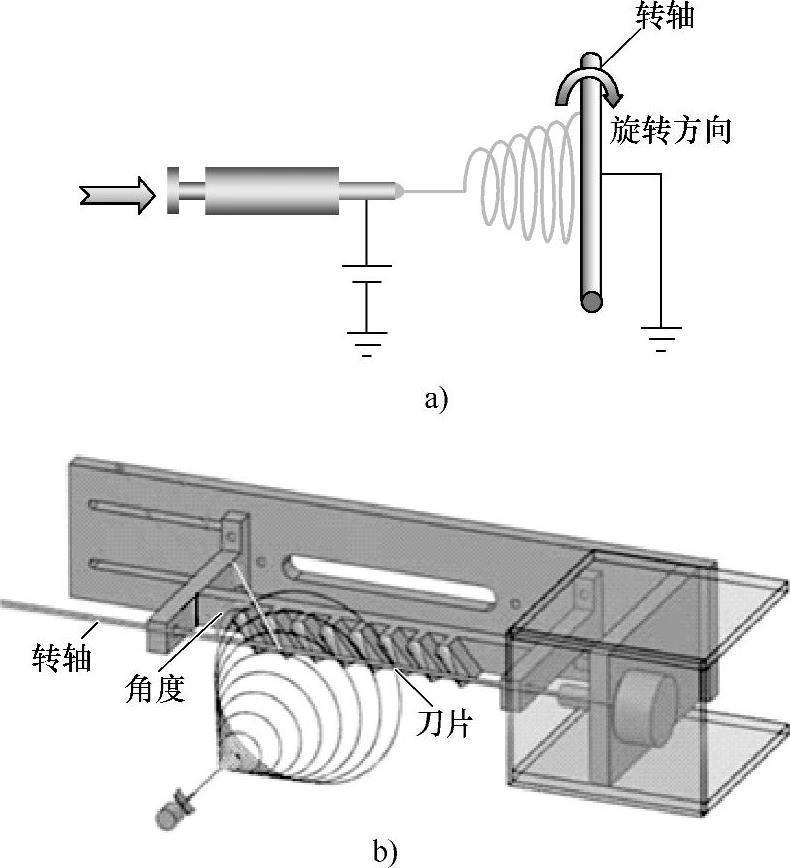
图5-21 组织工程血管之静电纺丝
a)原理图 b)结构示意图
也可用熔融挤压自由成形工艺间接构建陶瓷基支架。首先用熔融挤压自由成形工艺制备符合支架孔隙结构的蜡质模具;然后,在真空条件下,将氧化铝颗粒、分散剂和防沫剂组成的浆料注入模具,浇注陶瓷支架。这种方法成形的陶瓷支架的孔隙率为31%~55%,孔径为150~750μm,孔隙间完全贯通。
用熔融挤压工艺成形支架的优点是,不必采用有毒的有机溶剂。但是,熔融挤压工艺必须在高于100℃以上的温度下进行,从而限制了生物活性成分的介入。
图5-25[33]是熔融挤压自由成形的PCL支架,支架的孔径为400~700μm,孔隙率为48%~77%。
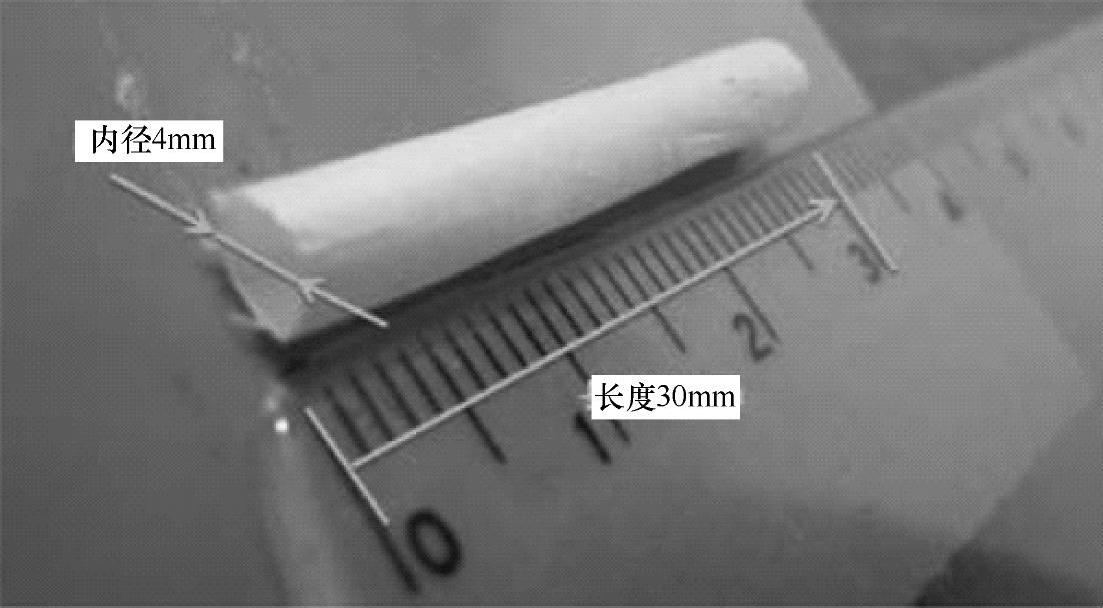
图5-22 组织工程血管支架
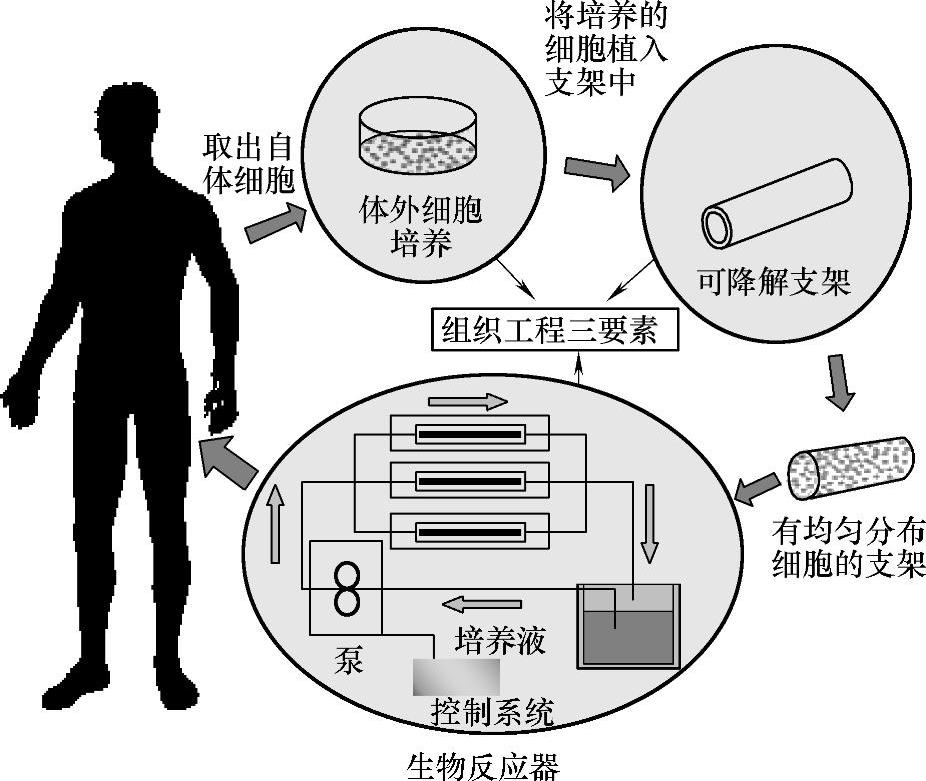
图5-23 组织工程血管制作过程
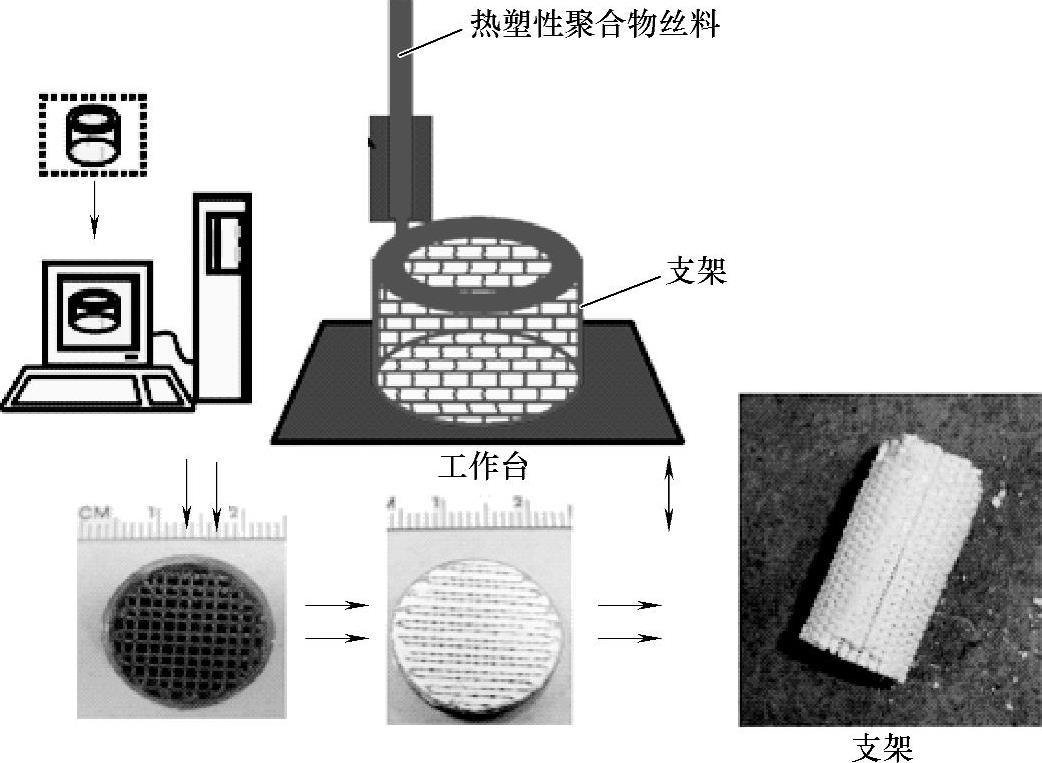
图5-24 熔融挤压自由成形支架的系统及其制作的支架
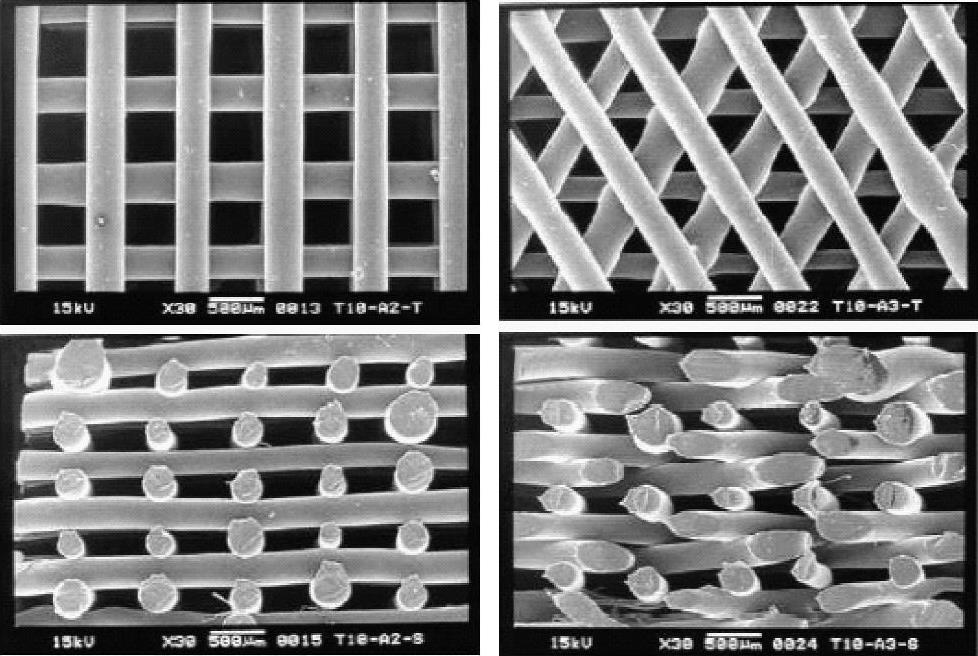
图5-25 熔融挤压自由成形的PCL支架及其截面
本章参考文献[26]报道,新加坡南洋理工大学Leong等人用熔融挤压自由成形机、HDPE(高密度聚乙烯塑料)和HA/HDPE线材制作了具有完整骨骼外形的多孔支架。新加坡国立大学的Hutmacher等人用熔融挤压自由成形机制作了PCL支架,孔隙率为(61±1)%。美国华盛顿州立大学的Bandyopadhyay等人用熔融挤压自由成形技术间接成形了生物陶瓷支架,即首先以有机线材制作支架负型,然后填充β-TCP浆体,经干燥和烧结形成多孔陶瓷支架,烧结中会出现22%~45%的收缩率,孔径为300~500μm,孔隙率为25%~45%。
相关推荐