【摘要】:影响PCB板喷印自由成形性能的主要因素有:喷嘴分辨率、喷嘴直径、喷射液滴体积和喷射频率、喷印分辨率、相邻液滴重叠率、基板的表面能与墨水的表面张力、固化状况、预处理与后处理等。显然,喷嘴分辨率越高,喷印PCB板的字符、图形越清晰,能喷印的最小字高越小。在接触角变化过程中,接触线的锁定对最终干燥喷印膜层的特征尺寸至关重要。
影响PCB板喷印自由成形性能的主要因素有:喷嘴分辨率、喷嘴直径、喷射液滴体积和喷射频率、喷印分辨率、相邻液滴重叠率、基板的表面能与墨水的表面张力、固化状况、预处理与后处理等。
1.喷嘴分辨率
一个喷头上通常有多个喷嘴,喷嘴分辨率(nozzle resolution)是描述喷嘴喷射的墨滴密集程度的技术指标。喷嘴分辨率用每一英寸上能喷射的墨滴数(dot per inch)表示,单位为dpi,dpi的数目越大,喷嘴分辨率越高。喷嘴分辨率也可用喷嘴间距(nozzle spacing)——相邻喷嘴的间距(μm)来表示,喷嘴的间距越小,分辨率越高。例如,KM512喷头的喷嘴分辨率为360dpi,喷嘴间距为70.5μm(25.4mm/360=0.0705mm=70.5μm)。
显然,喷嘴分辨率越高,喷印PCB板的字符、图形越清晰,能喷印的最小字高越小。现有压电式工业喷头的喷嘴分辨率通常为180dpi和360dpi,日本京瓷株式会社生产的KJ4系列喷头的喷嘴分辨率可达600dpi。
由于喷头制作工艺上的困难,如果一个喷头上的所有喷嘴排列成一排,则难以达到高分辨率(即小间距)。为克服上述困难,通常将一个喷头上的喷嘴分布成多列(例如3列,见图3-16),列与列之间交错排布,从而能得到更小的相邻喷嘴间距和更高的喷嘴分辨率。如此分布喷嘴之后,喷印时应通过控制软件使多列喷嘴喷印的墨滴重合为一列,得到最佳的喷印效果。
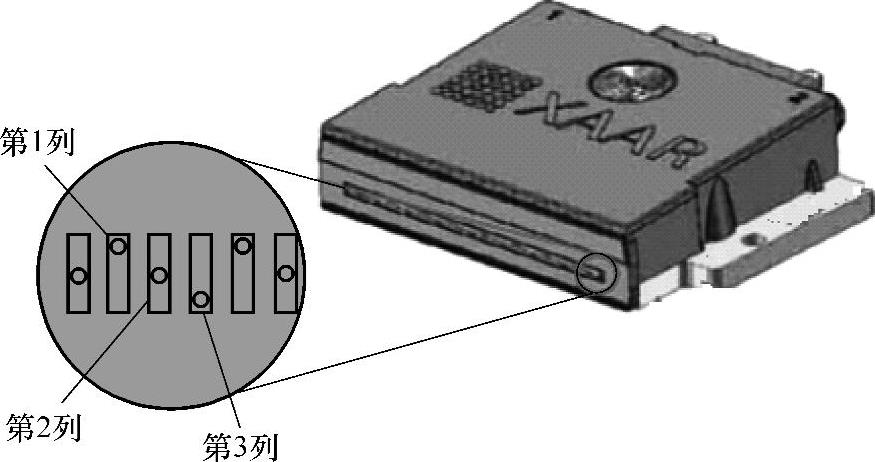
图3-16 呈3列分布的喷嘴
2.喷嘴直径与喷射液滴体积
喷嘴直径(nozzle diameter)越小,则喷射的墨水液滴体积(drop volume)越小,能在PCB板上喷印的最小特征尺寸(如沉积迹点半径、迹线宽度)越小,形成的图形更清晰。现有压电式工业喷头的喷嘴直径为27~52μm,最小液滴体积通常为4pL、6pL、14pL、35pL、40pL、80pL。
喷印最小特征尺寸取决于喷射液滴体积与滴落至基板后的扩散状况(见图3-17)[66]。
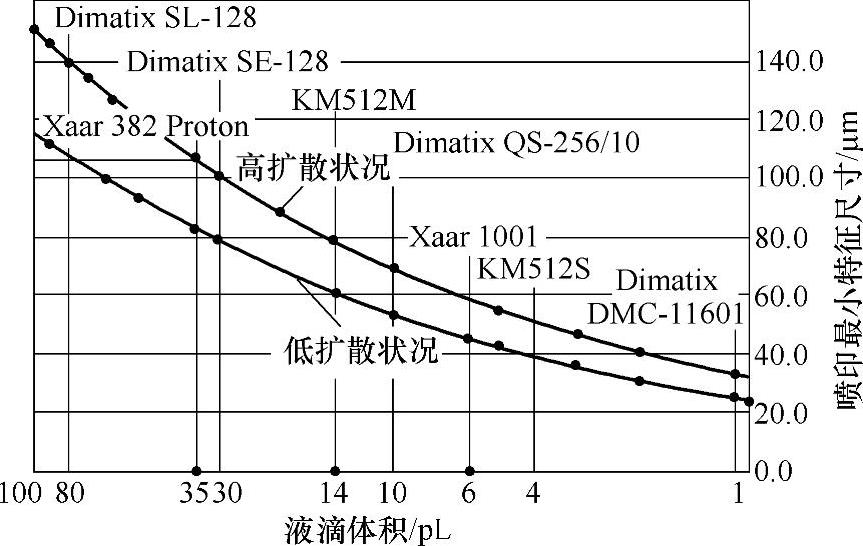
图3-17 喷印最小特征尺寸与喷射液滴体积和扩散状况的关系曲线
液滴在基板上的扩散状况取决于接触角,图3-18和图3-19是沉积在基板上的迹点(bead,液珠)尺寸与液滴体积和接触角的关系。由于基板表面在一定程度上存在粗糙不平或化学组成不均一现象(如缺陷、污染、墨水中溶质沉积),因此,迹点与基板的环形接触线会向前和向后移动,接触角会在相对稳定的两个角度之间变化,这种现象被称为接触角滞后现象(contact angle hysteresis),接触角的上限为前进接触角(advancing contact angle)θA,使接触线扩大;下限为后退接触角(receding contact angle)θR,使接触线缩小,二者差Δθ=θA-θR,定义为接触角滞后性,一般Δθ>10°。在接触角变化过程中,接触线的锁定对最终干燥喷印膜层的特征尺寸至关重要。
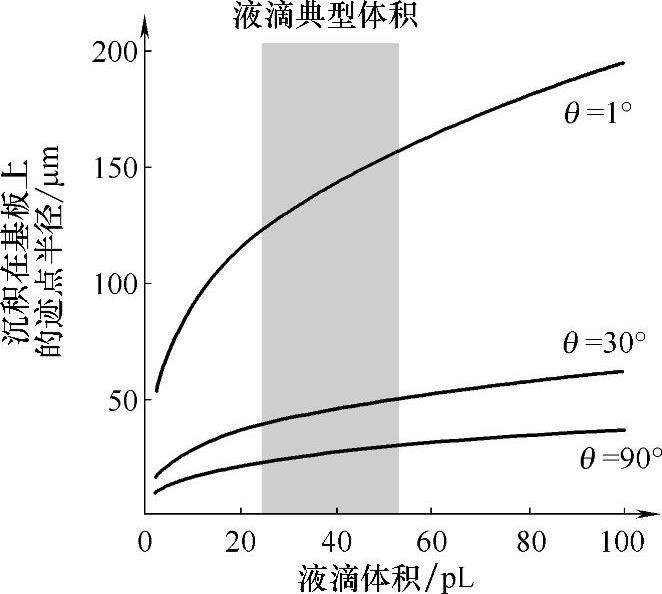
图3-18 沉积在基板上的迹点尺寸与液滴体积和接触角的关系(1)
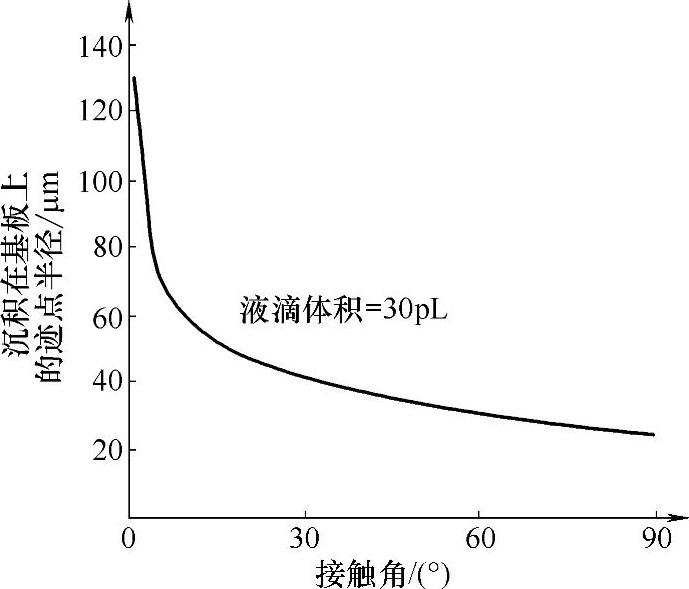
图3-19 沉积在基板上的迹点尺寸与液滴体积和接触角的关系(2)
据Inkjet Application Centre预测,几年内喷头将会有很大的进步(见表3-2),最小液滴体积可小至0.1~0.01pL,从而可喷印的最小特征尺寸可小至10~5μm。实际上,FUJIFILM Dimatix公司2010年已能生产1pL的DMC-11601压电式喷头。
表3-2 喷头喷印的特征尺寸与液滴体积预测

3.喷嘴的喷射频率
喷嘴的喷射频率(firing frequency,f)是喷嘴每秒钟能喷射的次数,喷射频率越高,则喷射的墨滴密度、喷印分辨率和喷印效率越高。
现有压电式工业喷头的喷嘴典型喷射频率通常为4~40kHz,日本京瓷株式会社生产的KJ4系列喷头的喷嘴喷射频率可达60kHz。
4.喷印分辨率
喷印分辨率不同于喷嘴分辨率,喷嘴分辨率是制作喷嘴时的自然分辨率(又称为物理分辨率,natural resolution),喷印分辨率是喷印时在基板上实际产生的分辨率。
对于多程扫描式喷印,沿基板横向X(即扫描方向)的喷印分辨率可按下式计算(见图3-20)[66]:

这表明,当喷嘴喷射频率越高、工作台相对喷头的运动速度越小时,X方向的喷印分辨率越高,即喷射的墨滴更密集。
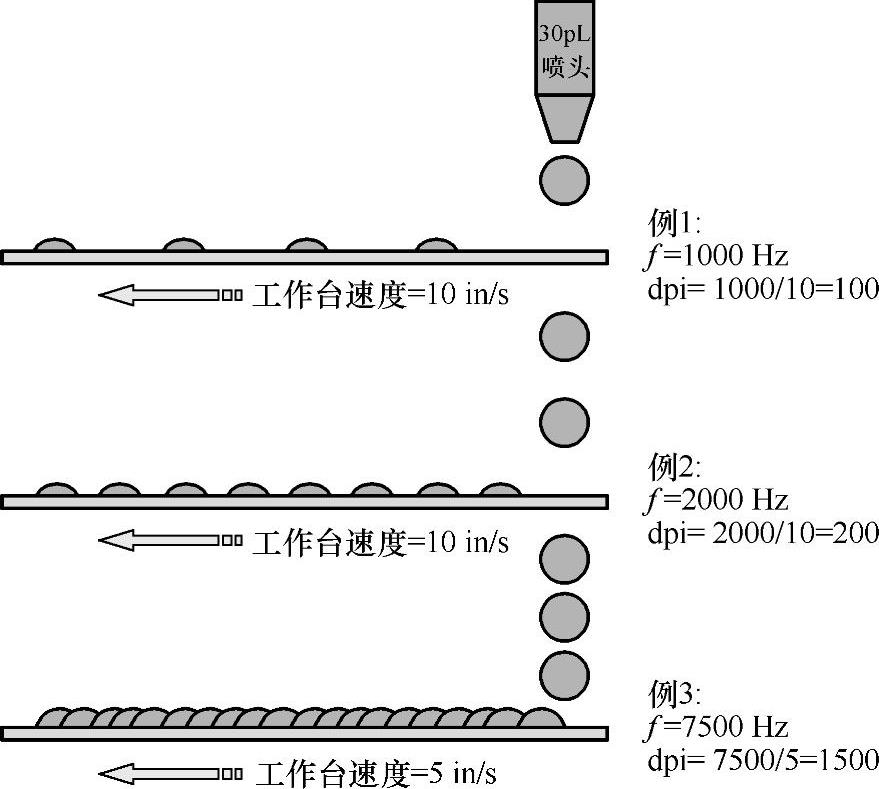
图3-20 多程扫描式喷印时横向X(即扫描方向)的喷印分辨率算例
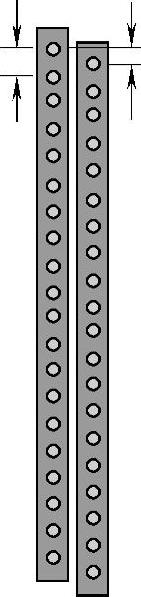
图3-21 错位排列的喷头
沿基板横向Y(即送进方向)的喷印分辨率等于喷嘴的自然分辨率,为提高此方向的喷印分辨率,可采用如下两种方法:
1)采用两个并列组合的相同喷头,并使它们在Y方向错位排列,导致组合后相邻喷嘴的间距缩小一半,即Y方向的喷印分辨率为喷嘴自然分辨率的两倍(见图3-21)。
2)在沿X方向喷印一个道次(pass)之后、喷印下一个道次之前,喷头沿Y方向移动1/2喷嘴间距,然后再进行下一个道次的喷印(见图3-22)。
对于单程非扫描喷印,在X方向布满喷头,无需进行扫描运动,在此方向的喷印分辨率与多程扫描喷印的Y方向喷印分辨率相同,即喷印分辨率等于喷嘴的自然分辨率,也可以采用如上所述错位排列喷头的方法来提高喷印分辨率。在Y方向,单程喷印分辨率与多程扫描喷印的X方向喷印分辨率相同,即按式(3-1)计算。
5.相邻液滴重叠率
为保证喷印线条宽度均匀、边缘光滑,喷射的相邻液滴的重叠率应为67%,即相邻液滴的中心距应为液滴直径d的1/3即0.33d(见图3-23)[66]。
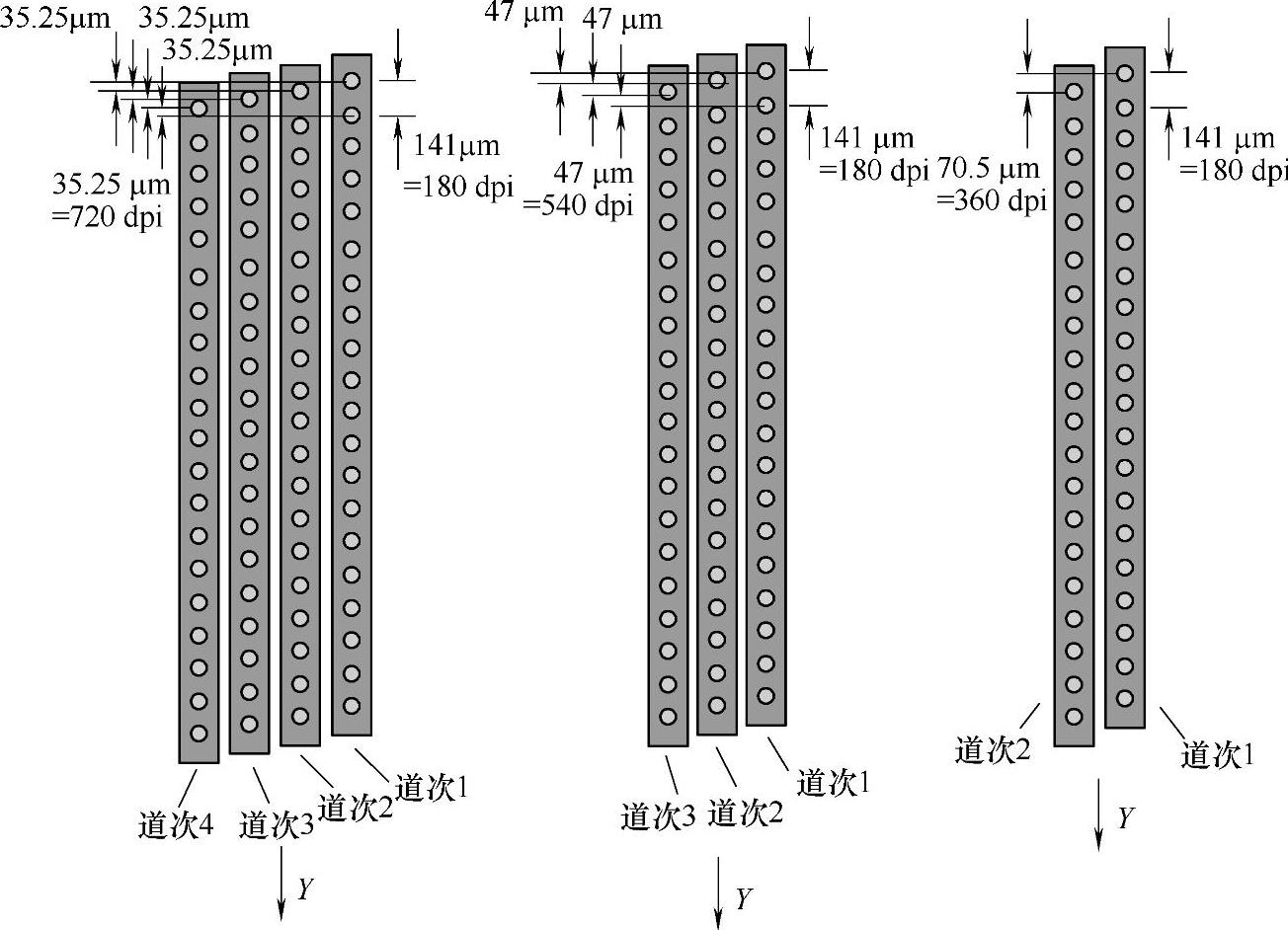
图3-22 多道次错位喷印法
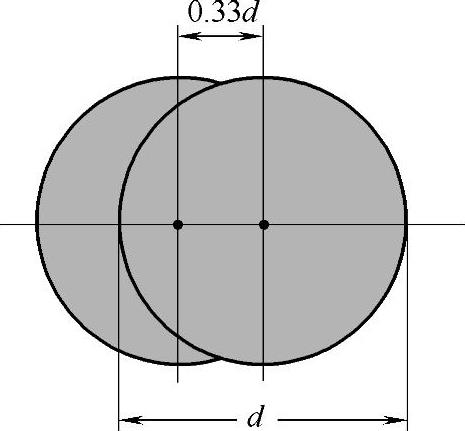
图3-23 相邻液滴的重叠率
对于不同扩散率的墨水,保证67%相邻液滴重叠率前提下的液滴体积与喷印分辨率的关系曲线见图3-24[66]。例如,喷射液滴体积为35pL的喷头,为保证67%相邻液滴重叠率,其喷印分辨率应为590~940dpi。
6.基板的表面能与墨水的表面张力
基板的表面能(surface energy)是指基板表面层分子比内部分子所具有多余能量。表面积越大,表面能越大。在温度和压力恒定时,这部分能量称为表面自由能(surface free energy),单位表面的表面自由能称为比表面自由能(单位为J/m2)。因为J=N·m,所以单位J/m2也可化为N/m(常用mN/m)。
墨水的表面张力(surface tension)是沿着与墨水表面相切的方向垂直作用于表面上任意单位长度线段上的表面紧缩力,其单位与比表面自由能的单位相同,可以用达因笔(Dyne pens)测量。但是表面张力与比表面自由能的物理意义不同,前者是标量,后者是矢量。
当墨滴落在基板之后,基板的表面能试图增加基板—液滴之间的界面面积,以便使其自由能最小,如此造成的基板表面拉力作用会使液滴扩散;而墨水的表面张力试图保持其表面积尽可能小。墨水扩散和润湿固体基板表面的能力可以用扩散系数SSL表示[75]:
SSL=γSV-γSL-γLV
式中 (见图3-25),γSV是基板的表面自由能(基板与空气的界面自由能);γSL是基板与墨水之间的界面自由能;γLV是墨水的表面张力。
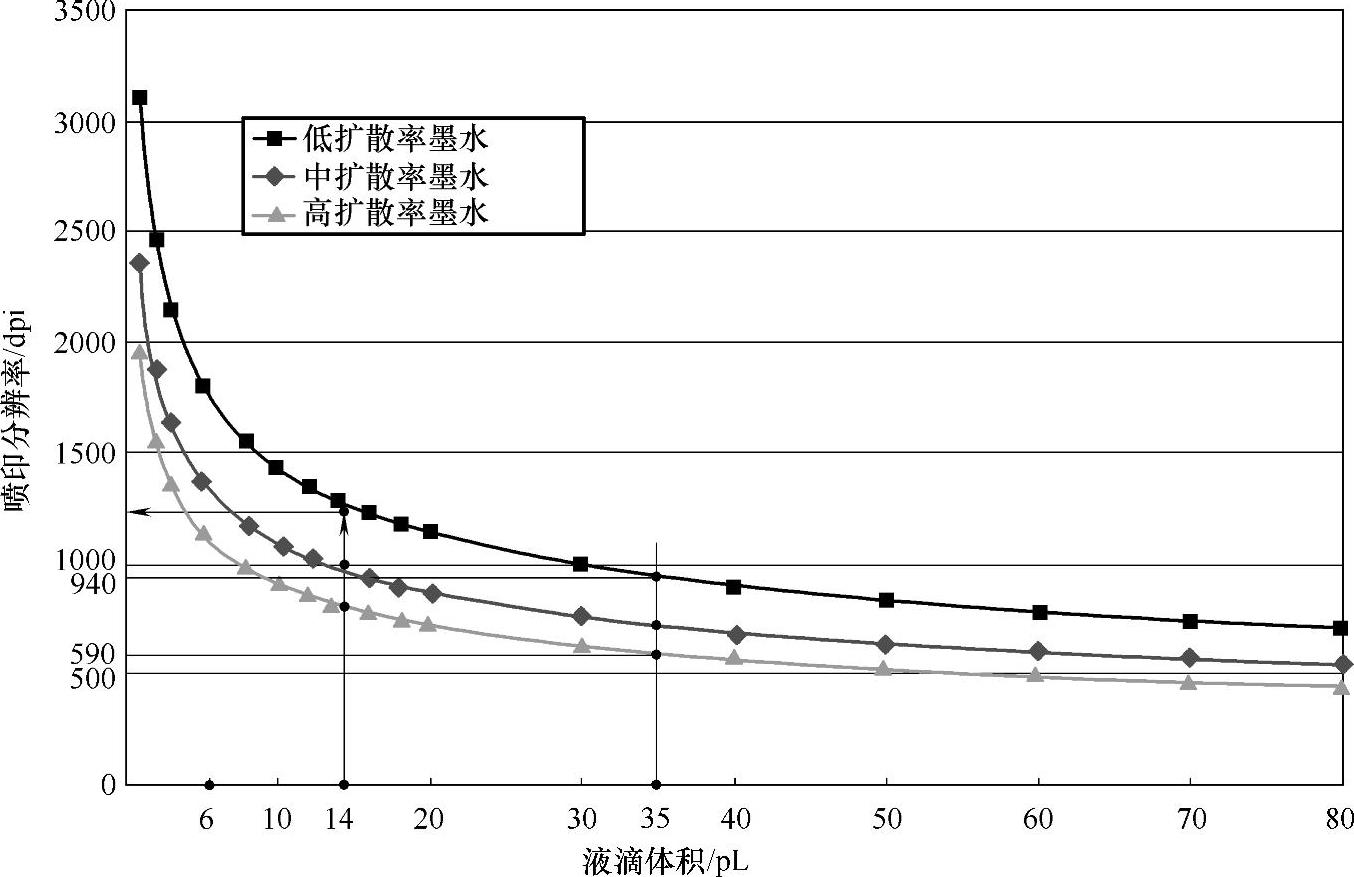
图3-24 保证67%相邻液滴重叠的前提下液滴容积与喷印分辨率的关系曲线
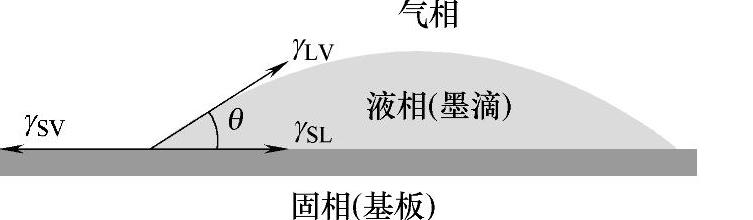
图3-25 墨滴—基板表面相互作用的能量平衡
固相、液相和气相等三相的热力学平衡条件如下式所示:
γSL-γSV+γLVcosθ=0
式中,θ为接触角。
如果墨水的扩散导致界面自由能降低,那么扩散系数SSL为正值。扩散系数SSL的正值越大,润湿特性越好,墨滴在固体表面扩散。扩散系数SSL为负值表示不良的润湿性。所以,如果与墨水表面张力γLV相比,基板有较高的表面自由能γSV,并且基板与墨水之间的界面自由能γSL较低(由于二者有较好的亲和力),则墨水对基板表面有较大的润湿倾向,接触角较小,墨水将在基板表面上扩散,形成均匀的润湿层;否则,墨水将趋于保持液滴状态。
研究表明,为获得良好的单程喷印效果应有以下关系[67]:
基板的表面自由能-墨水的表面张力≥20mN/m
从图3-26可见,符合上述关系式的喷印效果较好,否则,表面能较低时,墨水难以润湿被喷印材料,会在其上出现网状墨滴,即墨滴不能合并成连接的墨膜,而成为有相互间隙的大墨滴并可看见下面的基板。
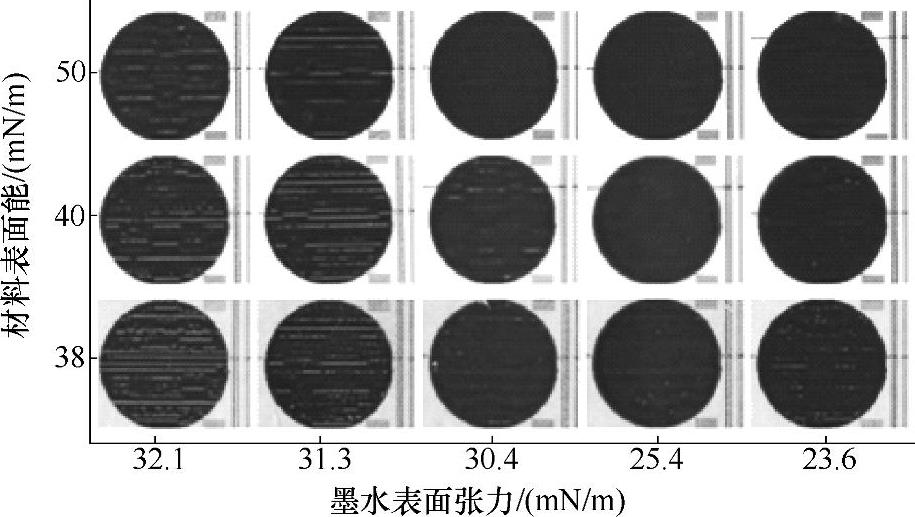
图3-26 材料表面能与墨水表面张力的关系(360dpi,单程喷印)
7.固化状况
喷印PCB板字符、阻焊层或抗蚀刻电路时,常在喷印之后用紫外光(UV)固化喷射的墨水。UV固化状况是影响喷印品质的重要原因,其中有四个主要因素:UV照度(irradiance,即强度,intensity)、波长(wavelength)、剂量(dose)和红外辐射(infra-red radiation)。不同的墨水对UV峰值照度(peak irradiance)和不同的波长有很不同的反应,因此,必须鉴别固化灯的特性并使其与墨水的光学特性相匹配。影响固化的光学特性包括:①光谱吸收率(spectral absorbance);②反射系数(reflectance)和散射(scattering);③光密度(optical density)和红外吸收能力(infrared absorption)。
喷印与固化之间的时间称为固化延时(Cure Delay)。本章参考文献[67]表明(见图3-27),当墨水有相当低的表面张力(24mN/m)、基材有相当高的表面能(52mN/m)时,二者差别很大。在分辨率为360x360dpi(液滴容积为14pL)、固化延时为1.8s时(见图3-27b)有较好的喷印品质;当固化延时为1s时(见图3-27a),喷印图像的浅色区域呈单独墨滴状,墨滴尚未合并成膜;当长固化延时(5.3s)时(见图3-27c),墨膜又破裂成网状,喷印品质不能再接受。
墨水形成连接膜和喷印品质可接受的时间范围称为固化延时窗(cure delay window),此时间范围约为1.5s<t<3.5s。其他的UV墨水有较大或较小的固化延时窗,但网状墨滴通常出现在固化后约1s的时间内。
固化延时的优化时间也随材料(基板)的表面能而变化。低表面能材料(材料上的墨水难以润湿材料中)有较长的优化固化延时(见图3-28)。由此图可见,固化延时为几秒的数量级。但是现有许多喷印机仅可在100~200ms后固化墨水,这个时间太短,会导致喷印品质下降,并需要多道次和更多的墨水来实现可接受的介质材料覆盖度。
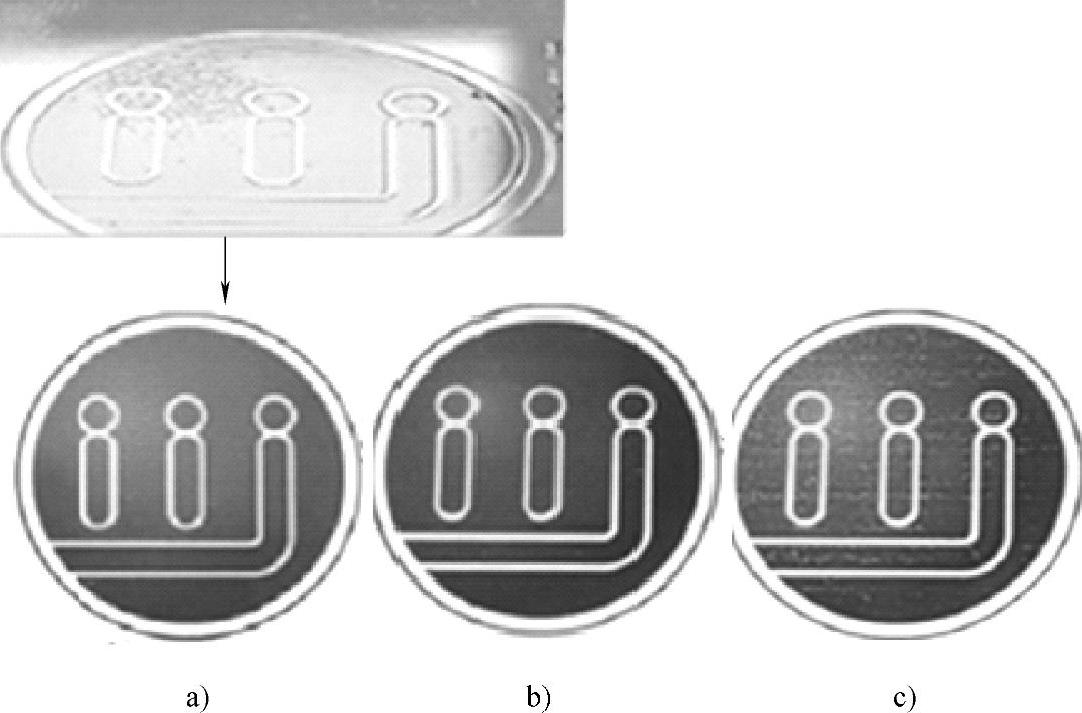
图3-27 固化延时的影响
a)1s b)1.8s c)5.3s
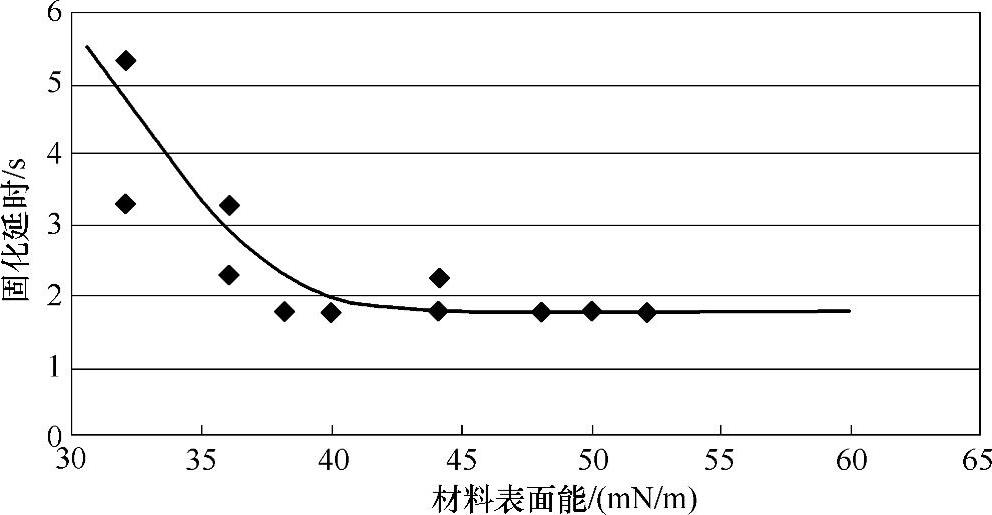
图3-28 不同材料表面能与优化固化延时的关系曲线
8.预处理与后处理
(1)预处理
PCB板的基板材料通常是聚合物,聚合物一般有较低的表面自由能,接触角θ较大,难以润湿沉积的墨水,影响喷印品质。尤其是采用纳米银导电墨水在PCB板上喷印电路时,由于银是贵金属,与非贵金属相比呈现化学惰性,难以形成金属—聚合物结合层。因此,喷印前应进行基板表面改性预处理,以便提高墨水与基板之间的界面附着力。预处理的常用办法是使基板变粗糙,有等离子蚀刻(plasma etching)和脉冲激光烧蚀(pulsed laser ablation)两种方法。
1)等离子体蚀刻。等离子体是固态、液态、气态以外物质的第四态,是正离子和电子的密度大致相等的电离气体,通过激光、微波、电晕放电、热电离、弧光放电等方式可将气体激发到等离子态。用于PCB板表面处理的常见气体是氧气(O2)、氮气(N2)、氢气(H2)、四氟化碳(CF4)和氩气(Ar)。
等离子体蚀刻系统如图3-29所示,在其等离子发生器中设置两个电极形成电场,用真空泵实现一定的真空度,随着发生器中气体越来越稀薄,分子间距及分子或离子的自由运动距离越来越长,受电场作用,它们发生碰撞而形成等离子体,这些离子的活性很高,其能量足以破坏几乎所有的化学键,在PCB板表面引起化学反应,使PCB板表面分子片段和原子从表面溅射出来,改变表面的微观形态,在分子级范围内增加表面粗糙度,从而改善表面的粘结性能。
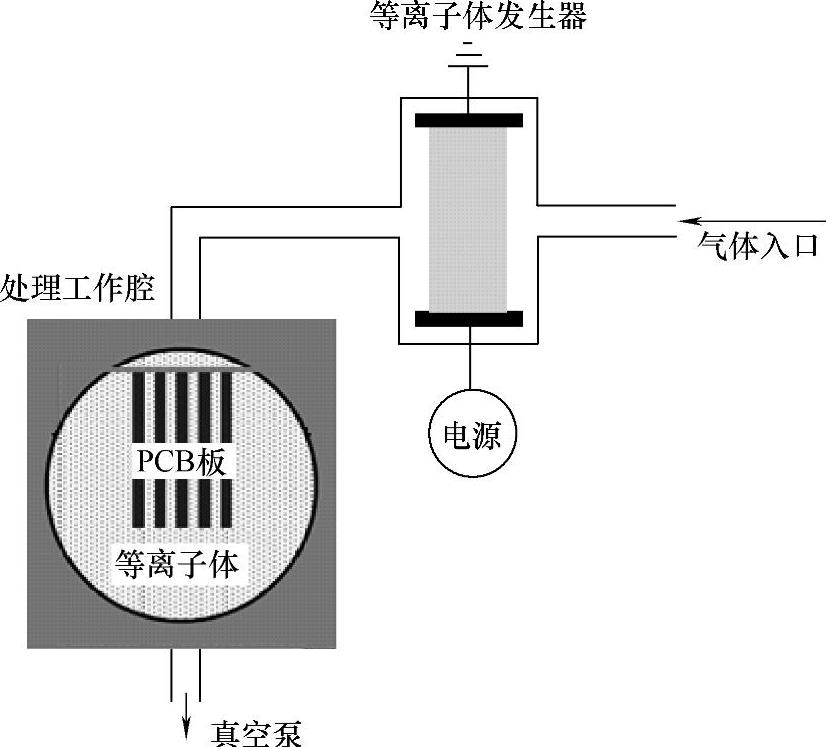
图3-29 等离子体蚀刻系统原理图
2)脉冲激光烧蚀。它是用激光在基板表面烧蚀孔、直线、影格线(见图3-30),形成烧蚀图案,以便使表面改性。烧蚀时,激光束的光能传递至基板,同时通过诱导光解工艺(photolytic process)使材料的键断裂(bond scission)和热解工艺(pyrolytic process)使材料热降解(thermal degradation),去除基板上的部分材料。
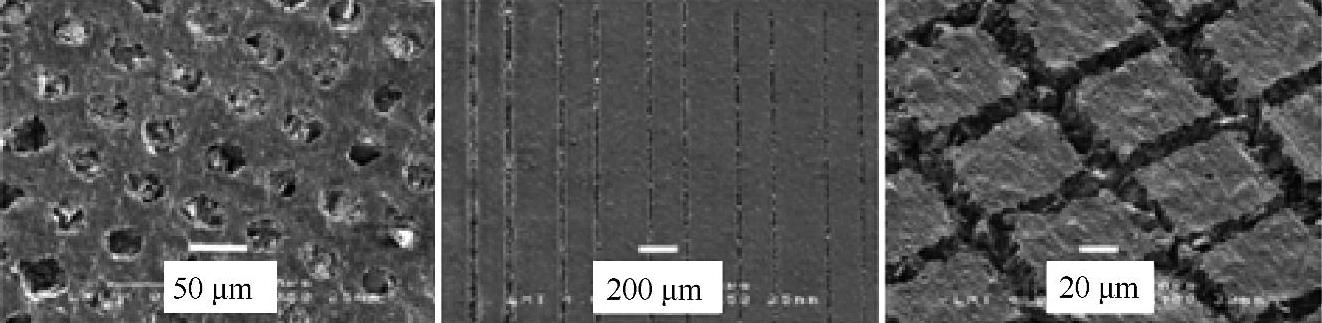
图3-30 在聚合基板上用激光烧蚀的孔、直线和影格线图案
烧蚀材料时,材料的烧蚀阈值(ablation threshold)必须低于材料可吸收的激光能,此能量足够使材料的分子键裂开。聚合物的烧蚀阈值较低(通常低于200mJ·cm-2),因此非常适合用激光进行大面积预处理。
采用脉冲激光(例如微秒紫外激光)烧蚀基板时,脉冲的持续时间非常短,瞬时密度非常高,从而限制了照射区域,因此与连续激光烧蚀聚合基板相比,脉冲激光烧蚀的优点是基板中的热扩散较小,有助于用最小的热量在基板上构成精密图案。
(2)后处理
用金属墨水进行喷印之后,喷印的结构还需进行两种后处理:烧结(sinte-ring)与无电镀(electroless plating,化学镀)。
烧结的目的是去除沉积墨水中的非金属成分,并提高喷印金属结构的连续一致性。无电镀是一种可选后处理工艺,目的是增加喷印金属结构的厚度。
1)烧结。在PCB板上喷印导电结构时,一般采用纳米金属墨水,因其表面/体积比较高,与块状金属相比有较低的熔点,而且在印制电子工艺中,所谓“烧结”并非指熔化纳米颗粒,而是指颗粒生长(particle growth)和晶界迁移(grain-boundary migration)的组合,因此所需烧结温度很低(又称为固化,cure),例如美国UT Dots公司纳米银导电墨水的烧结温度为90~200℃。
常用的烧结方法有以下几种:
①热烧结。将喷印结构置于对流恒温烤箱中烧结固化,其过程如下(见图3-31a)。a)热解:通过加热从沉积的墨水中去除溶剂和分散剂,纳米颗粒仍然呈离散状(见图3-31b)。b)烧结开始:继续加热,颗粒开始接合,晶粒尺寸增大(见图3-31c)。c)烧结结束:晶粒之间有保证结构连续性的足够接触(见图3-31d),然而最终结构很少能达到100%的密度,杂质和针孔常常会妨害烧结金属的连续性。热烧结所需时间较长,能量消耗较多,基板需承受热应力,热影响区大。
不同品牌的纳米银导电墨水有不同的烧结温度与时间,例如Cabot Conductive Ink CCI-300的烧结时间、温度与电阻率的关系见图3-32。由此图可见,电阻率随着烧结温度提高、烧结时间延长而降低。
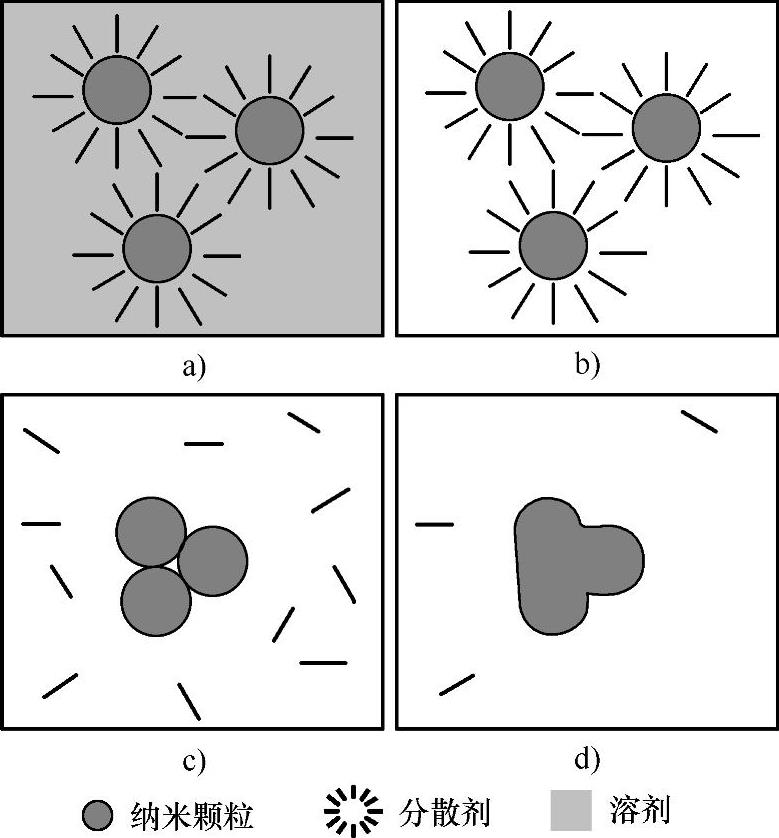
图3-31 纳米颗粒的热烧结过程
a)加热前 b)热解开始 c)烧结开始 d)烧结结束
从图3-33可见,随着温度升高,颗粒之间的间隙和电阻率缩小。
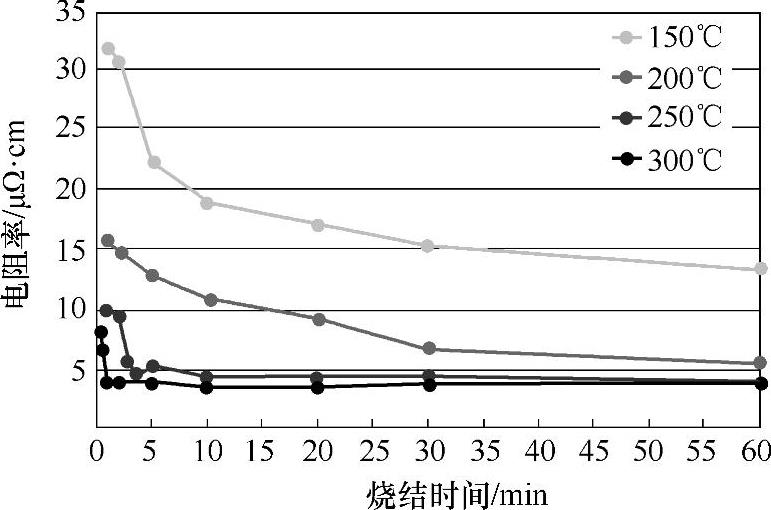
图3-32 烧结时间、温度与电阻率的关系

图3-33 温度升高使颗粒之间的间隙和电阻率缩小
②激光束烧结。也可在喷印纳米金属墨水之后,随即用激光束进行烧结处理(见图3-34),特别是当基板的材料为挠性聚合物时[84],这种方法的优点是曝光时间短,热影响区较小,有更高的有效沉积能。
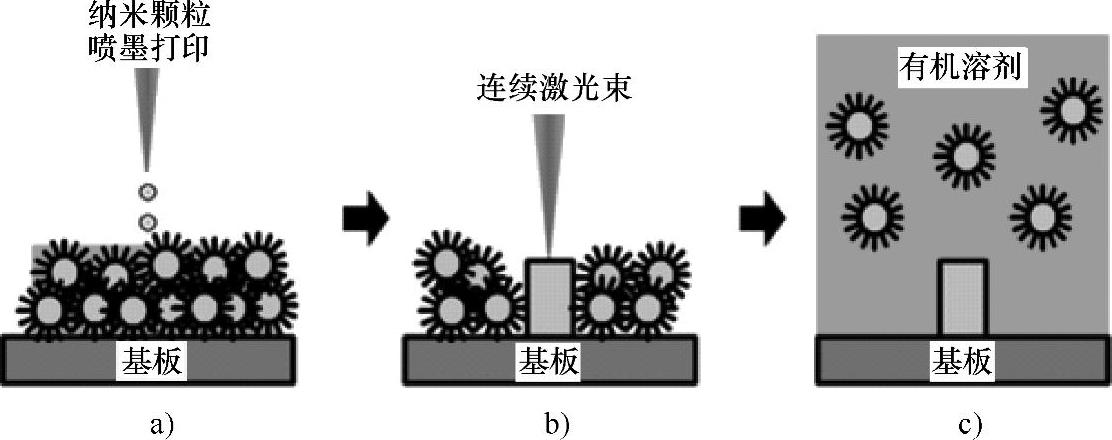
图3-34 用激光束进行烧结后处理
a)喷印 b)烧结 c)烧结后
③微波烧结。将喷印结构置于微波炉中烧结固化,这种方法的加热速度快。
2)无电镀。无电镀是无需电流的一种利用氧化还原反应的自催化镀(auto-catalytic plating)工艺,非常适用于不同基板(包括非导电基板)的金属沉积均质化,广泛用于PCB板的制作。但是与电镀相比,无电镀的金属沉积率较低(取决于镀液成分与温度),对于镀铜而言一般低于5μm/h。
无电镀铜时,碱性溶液中的铜离子因还原反应而沉积于目标材料上。当目标材料为聚合物基板并在其上已喷印银种子层时,银种子层作为还原反应的催化剂。开始沉积之后,随着反应继续,更多的铜自催化地沉积在已沉积的铜层上。无电镀铜可表示为以下两种电化学反应的耦合:

反应①是阴极还原反应,其中L是有机配位体(organic ligand,化学螯合剂),它形成稳定的Cu(Ⅱ)螯合物。反应②是阳极甲醛氧化(anodic formaldehyde oxi-dation)。
相关推荐