【摘要】:因此60Si2MnA材料适宜制作汽车钢板弹簧。回火工艺参数 汽车钢板弹簧的回火应在460~540℃的温度下进行,以获得回火托氏体组织。
1.工作条件和技术要求
汽车钢板弹簧是一种弹性元件,其作用是承受车厢以及载物(静载荷),可传递垂直载荷,缓和及抑制不平路面所引起的冲击,限制车身和车轮的振动。作为弹性元件它既有缓冲、减振、储能的功能,又起到传递力和导向的作用,在工作过程中,钢板弹簧承受道路不平所引起的冲击载荷以及由此引起的单向循环弯曲应力和振动的作用,同时也要受到泥水和泥沙等的侵蚀。由于其结构简单、使用可靠、维修方便,因而被一般载货汽车广泛采用。
汽车钢板弹簧采用合金钢制造,硬度为380~460HBW,板簧具有优异的强度特性,即高的弹性极限,经过抛丸后处于表面压应力状态,然后进入机械加工阶段。
资料介绍,重型汽车的几率-应力曲线表明,钢板弹簧所受应力为900~1000MPa。汽车钢板弹簧的主要失效形式有腐蚀疲劳断裂、应力腐蚀断裂、脆性断裂、磨损和应力松弛以及永久性塑性变形等,其危害有停车待修、板簧耗损量大、降低行车舒适性等,因此应认真对待,降低出现失效的几率,在弹簧制造和热处理等各个环节确保产品质量合格。钢板弹簧应具有高的弹性极限、良好的淬透度、低的脱碳敏感性、较高的硬度和强度、一定的冲击韧度、良好的疲劳强度以及最大比弹性功,破断部位一般在卷耳与中间固定处。
钢板弹簧一般由多片曲率半径不同、长度不等、宽度一样的钢板等组成,如图5-10所示。
钢板弹簧在载荷作用下变形时,各片之间因相对滑动而产生的摩擦以及两端支承处的摩擦,可以促进车架振动的衰减。但各片间的干摩擦将使车轮所受的冲击在很大程度上传给车架,降低了悬架缓和冲击的能力,并使钢板弹簧各片加速磨损。因此各片之间应涂上较稠的石墨润滑脂,也有的在钢板弹簧片之间夹入塑料垫片。
汽车钢板弹簧在工作状态下要吸收大量的弹性功,又要求本身不发生永久变形,因此其具有高屈强比和尽可能大的弹性比功,为了得到强度高、疲劳极限大的钢板弹簧,板簧用弹簧钢应选用碳质量分数为0.45%~0.65%的合金钢,如60Si2Mn材料,其中各元素的质量分数为:碳0.54%~0.64%,硅0.50%~2.00%,锰0.60%~0.90%,铬和镍小于0.35%。硅在钢中形不成碳化物而是固溶在铁素体中,产生固溶强化作用,显著提高钢的硬度和整体强度,它的存在提高了钢的弹性极限、屈服强度和屈强比以及疲劳强度和疲强比,回火后的疲强比为0.8~0.9。因此60Si2MnA材料适宜制作汽车钢板弹簧。材料的选择应从钢材的工艺性能和力学性能方面进行考虑,前者影响零件制造的难易程度,后者必须满足零件的设计和使用要求,且能提高零件的使用寿命。
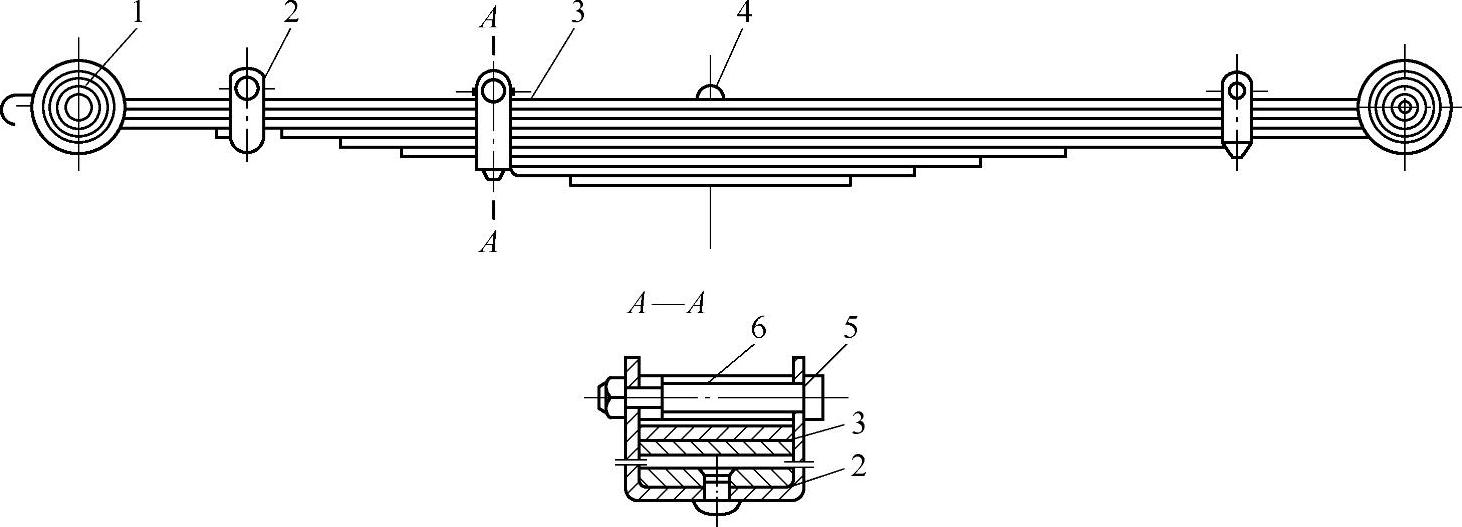
图5-10 汽车钢板弹簧
1—卷耳 2—钢板夹子 3—钢板 4—中心螺栓 5—螺栓 6—套管
2.汽车钢板弹簧的机械加工流程
一般汽车弹簧钢板的加工流程为:剪切下料→机械加工(钻孔、切角等)→校直→卷耳→淬火→中温回火→喷丸→质量检查。
考虑到弹簧的工作条件,为确保获得理想的技术指标,对原材料的要求比较严格,一般供货状态为热轧状态。通常技术要求为钢材的化学成分、表面脱碳层的深度及游离态的石墨等夹杂物符合规定,表面不允许有麻点、裂纹、锈蚀、折叠、斑疤、气泡及压入的氧化皮和棱边碎裂等致命缺陷,并进行表面抛丸或抛光处理,从而大大提高其疲劳寿命。
3.汽车钢板弹簧的热处理工艺规范
汽车钢板弹簧选用的材料为60Si2MnA,其热处理工艺流程为:预热→加热→冷却→中温回火→喷丸,要求硬度为42~45HRC,板簧淬火后必须及时进行回火处理,回火温度一般为440~520℃,金相组织为回火托氏体+碳化物。
(1)加热工艺参数 为实现汽车弹簧钢板的热处理,应将其加热到奥氏体化温度,最佳的加热温度为860~880℃,奥氏体化温度的高低对钢板的淬火马氏体(金相组织)有重要的影响,低于860℃淬火后获得了片状马氏体,高于880℃时为板条马氏体,温度越高板条马氏体的数量越多,且尺寸逐渐长大,同时残留奥氏体的数量增多,低于900℃时残留奥氏体呈块状分布在板条马氏体之间,当达到920℃时则明显形成条状残留奥氏体,并沿板条马氏体分布。
采用的热处理加热设备有燃油炉、可控气氛网带炉和燃煤反射炉,从生产的流程来分单板弹簧可在连续式加热炉(液压步进式)、周期性作业炉内完成加热过程,连续式加热炉具有炉温均匀、成分稳定、热效率高等特点,采用运输带将钢板从一端送入炉内,从另一端出炉冷却,资料介绍,钢板在加热炉内的保温时间不得低于表5-5中的规定。
表5-5汽车板簧厚度与加热保温时间的关系

(2)冷却工艺要求 弹簧钢板在加热炉内的保温结束后,采用链板式输送链将弹簧钢板在淬火机上自动夹紧成形,或经机械手将加热的钢板移动到液压自动弯曲淬火机内喷油冷却,或入油左右摇摆进行冷却,自动卸片,再经输送带传递出淬火油池。淬火油池内的淬火冷却介质为5号机械油,油温为20~80℃,淬火后的马氏体级别在5级左右,淬火后基体硬度≥63HRC。连续式加热炉处理的弹簧钢板的质量稳定,表面基本无氧化和脱碳,是目前国内外热处理企业普遍应用的热处理设备。
(3)回火工艺参数 汽车钢板弹簧的回火应在460~540℃的温度下进行,以获得回火托氏体组织。需要注意此时碳化物未明显长大,具有应力分布特征,基体α相仅发生回复过程,保持马氏体针状态和一定的强化效果,使回火托氏体有较高的弹性极限。回火后水冷可以防止第二类回火脆性的出现,使钢板表面产生了残留压应力,提高了疲劳强度,硬度为42~45HRC。推荐的在油炉中的保温时间见表5-6。
表5-6汽车板簧厚度与回火保温时间的关系

回火温度同样会影响汽车钢板弹簧的力学性能,试验表明在910℃加热淬火,分别在420℃、460℃和500℃回火处理,回火后的组织回火托氏体具有不同的形态。提高回火温度到一定程度后,获得的板条马氏体的断裂韧度随温度的升高而急剧下降。其原因在于板条马氏体断裂韧度很高,随着回火过程的进行,逐渐有针状碳化物析出和长大,从而使钢的断裂韧度降低。只有碳化物团聚才能使钢的断裂韧度再次提高。而片状马氏体由于其本身的断裂韧度较低,必须提高淬火温度,使碳化物析出并聚集,故870℃加热淬火和520℃以上回火对韧性是有利的。
(4)注意事项 由于汽车钢板弹簧为长条状结构,在炉内为连续加热,自炉
内传出到进入液压淬火机需要一定的时间,因此其工艺加热温度为940~950℃,保温12~18min,在液压淬火机内进行油冷前,板簧的温度为860~880℃,符合加
热温度的要求,回火温度为500~540℃,保温60~90min后水冷。
合金弹簧钢的临界冷却速度较低,为防止淬火开裂,在油中冷却是可行的,可
获得细致的马氏体组织,但应防止淬火油中混进水,否则将会在板簧表面生成一层
导热不良的蒸汽膜,使冷却能力下降,并导致淬透性不良。
60Si2MnA汽车钢板弹簧也可采用硝盐冷却,具体工艺为860~880℃加热,淬入硝盐水溶液中(淬火冷却介质中各成分的质量分数为31%NaNO3、21%NaNO2、48%H2 O,密度为1.44~1.46g/cm3,使用温度在20℃以上),450~470℃回火
1.5h后出炉水冷,硬度为43~46HRC。此种方法具有无污染、介质不易老化、工
件变形小和不易开裂的特点,同时改善了作业环境,适合于批量生产。
4.汽车钢板弹簧热处理工艺分析与操作要点
1)上述成熟工艺已经普遍使用,目前少数弹簧厂采用了高温快速回火工艺,
即在650~700℃送入炉内,加热5~15min,此时钢板表面在600℃左右。这种方法缩短了回火时间,马氏体分解速度加快,消除了淬火应力,马氏体分解析出
的碳化物来不及长大,故弥散度大,性能稳定。需要注意的是汽车钢板弹簧失效
的原因除了设计、安装和使用方面的以外,更为重要的是热处理质量和表面质量,前者是指硬度、组织和内应力,后者取决于表面脱碳层的深度、喷丸工艺,
与热处理密切相关,因此如何实现钢板的无氧化加热是热处理工艺人员首先考虑
的问题。
2)在淬火过程中,加热温度、保温时间和冷却速度是十分重要的工艺参数,若温度过高,则奥氏体晶粒粗大,氧化脱碳严重,将会降低其强度和疲劳极限;而
温度过低,则会造成组织转变的不均匀,出现未溶解的铁素体,同样会降低其强度
和使用寿命,因此要严格控制淬火温度。
汽车弹簧钢板所受负荷属于小能量多次冲击和疲劳载荷,提高淬火温度获得板
条马氏体即可提高其抗拉强度和提高疲劳寿命,淬火温度为850~900℃时获得的抗拉强度、冲击韧度以及断裂韧度等最佳。但为确保抗弯强度和冲击韧度,淬火温度应在880℃以下,事实证明淬火温度为860~880℃是最佳的。另外根据服役条件
的具体要求,材料应满足强韧性的要求,因此应采用较低的回火温度,回火温度以460℃为佳。钢板在870℃左右淬火成形+回火+喷丸(或抛丸)后,疲劳寿命明显提高。
3)目前国内外对汽车板簧进行热处理方法,除了常规的整体淬火外,已经发展了整体感应加热强化工艺,使表层具有0.1~0.2mm的马氏体组织,表面存在较
大的残留压应力,可提高承载能力,延长使用寿命。另外还采用了形变热处理工艺,在钢板加热后,在辊压机上进行热变形压轧,利用余热进行淬火处理,使金属细化、马氏体的长度和宽度减小,加上采用了保护气体,减少了钢板的表面脱碳,提高了表面质量,从而提高了疲劳寿命。
4)为减少板簧表面的脱碳层,推荐选用盐浴炉或可控气氛炉,也可进行高频感应淬火,从而提高弹簧的弯曲疲劳强度和使用寿命。氧化会降低表面质量和疲劳强度,脱碳则强烈降低疲劳强度,导致出现早期断裂。事实上钢板弹簧在热处理过程中如果出现表面脱碳将显著降低弹簧的抗疲劳性能,这是因为一方面脱碳层的存在降低了表面硬度,另一方面有软点或铁素体存在,成为疲劳裂纹源。
对脱碳层深度不同的钢板弹簧进行弯曲疲劳试验,结果表明,钢板表面脱碳层越深,则疲劳强度越低(当脱碳层深0.141mm时,疲劳极限只有350MPa),而无脱碳层则明显提高(570MPa),具体见表5-7。脱碳层的存在对弹簧的使用寿命有重要的影响,材料热处理前后的表面状态不允许改变。
表5-7脱碳层深度对钢板弹簧疲劳寿命的影响
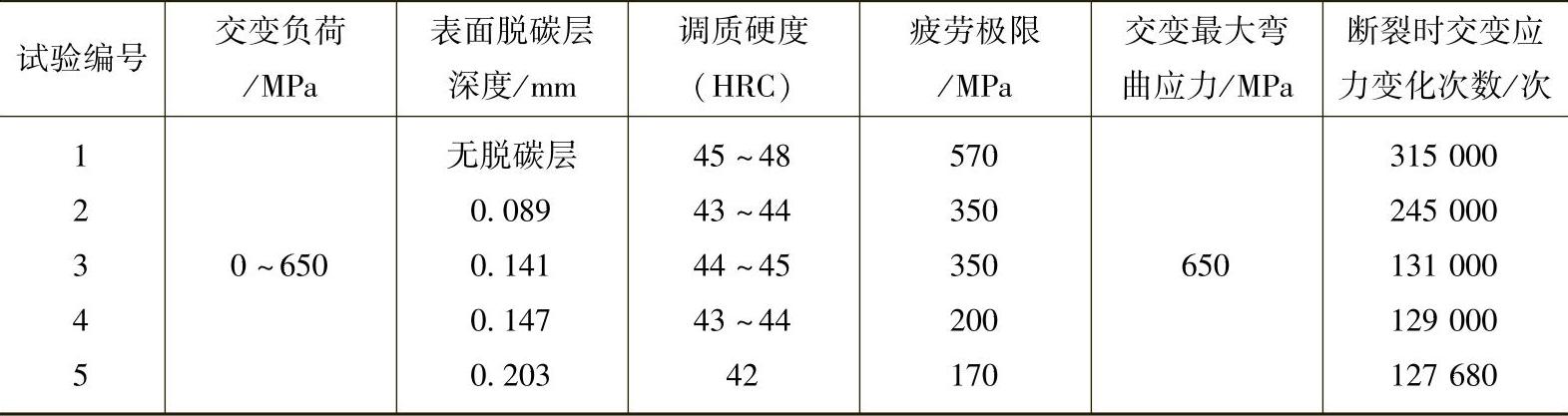
资料介绍,通过分析55SiMnVB脱碳对疲劳极限的影响可见,脱碳与未脱碳材料的疲劳强度相差59%,由此可知,严重脱碳的钢板弹簧(图5-11)的疲劳寿命的显著降低。

图5-11 严重脱碳的钢板弹簧(×100)
5)为了提高钢板弹簧的使用寿命,可进行形变热处理,利用马氏体相变强化和形变强化提高了抗拉强度和韧性。
6)为了提高弹簧的疲劳强度,可进行应力抛丸和弹簧棱边喷丸。喷丸后钢板表面发生塑性变形,抵消了工作过程中承受的弯曲压应力,抗拉强度提高25%以上。通常抛丸是对板簧的凹面进行喷射,抛丸或喷丸可除掉弹簧钢板上粘附的残盐或油垢及氧化皮等,使表面清洁呈银灰色,砂粒直径为0.5~1mm,压力为0.3~0.66MPa,喷射角度为30°~40°。喷丸强化处理可明显提高疲劳寿命、耐蚀性和耐热性,采取强压(弯、扭、拉)也是改善弹簧拉应力松弛的有效方法。该方法主要用于承受循环载荷、容易发生疲劳损坏的各种压缩弹簧、板簧和扭杆弹簧等,在其成形及热处理后进行。研究发现喷丸强化处理减轻或消除了弹簧表面缺陷(如小裂纹、凹凸、缺口以及表面脱碳等)的有害作用,表层产生循环的塑性变形、加工硬化和有利的残留压应力,可有效提高疲劳寿命。
喷丸机由弹丸加速装置(如离心式及气喷式弹丸循环装置)弹丸分离装置、弹丸补充装置和操纵被加工零件的运动装置等组成,目前在国内有滚筒式、履带式、吊链式、轨道通过式、转台式、台车式、钢板预处理式等抛丸机或喷丸机,另外还出现了吊挂式喷丸机,可满足不同的工作需要。
汽车板簧的断裂源萌生于其侧面(厚度弯曲表面),喷丸对钢板弹簧的影响很大。板簧损坏的主要原因是板簧之间接触面上的微动引起微粒的磨损(垫板边缘或其他弹簧板的过渡区),为了抑制在微动磨损过程中发展的摩擦表面上的粘着、疲劳氧化磨损、疲劳腐蚀磨损和磨粒磨损,可以采取以下两种措施:消除(或减小)相对位移和缩短损坏过程,即用正常的磨损过程(最低磨损速度)来代替现有的急剧磨损方式;将相对位移运动传给中间介质,消除微动,通常在低弹性模量的金属基体上采用阻尼材料、聚合物、涂料等来实现,这种方法在国外得到了极为广泛的应用。资料介绍喷丸对55SiMnVB平板试样及弹簧使用寿命的影响为:喷丸后的平板试样比未喷丸的疲劳强度提高90%,货车用钢板弹簧平均寿命提高6倍以上。60Si2MnA弹簧(尺寸为7mm×65mm×560mm)经920℃淬火+480℃回火后,硬度为42~47HRC,然后进行喷丸处理,用0.8~1.2mm的钢丸,新旧钢丸各占50%,采用离心式喷丸机,叶片速度为2500r/min,喷射速度为70m/min,叶轮中心至工件表面的距离为0.5m,角度为45°,喷射时间为24s,放入Al menC片,强化喷丸强度,其结果见表5-8。
表5-8喷丸强度对60Si2MnA汽车钢板弹簧疲劳寿命的影响

注:C为弧高;疲劳试验频率为15000次/h。
从表中可知强度为0.18C时,疲劳寿命最高。事实上除了对钢板正面喷丸外,棱边喷丸对60Si2Mn钢板弹簧疲劳寿命的影响也是较大的,见表5-9,试验压力为1029MPa。
表5-9钢板棱边喷丸对60Si2MnA钢板弹簧疲劳寿命的影响
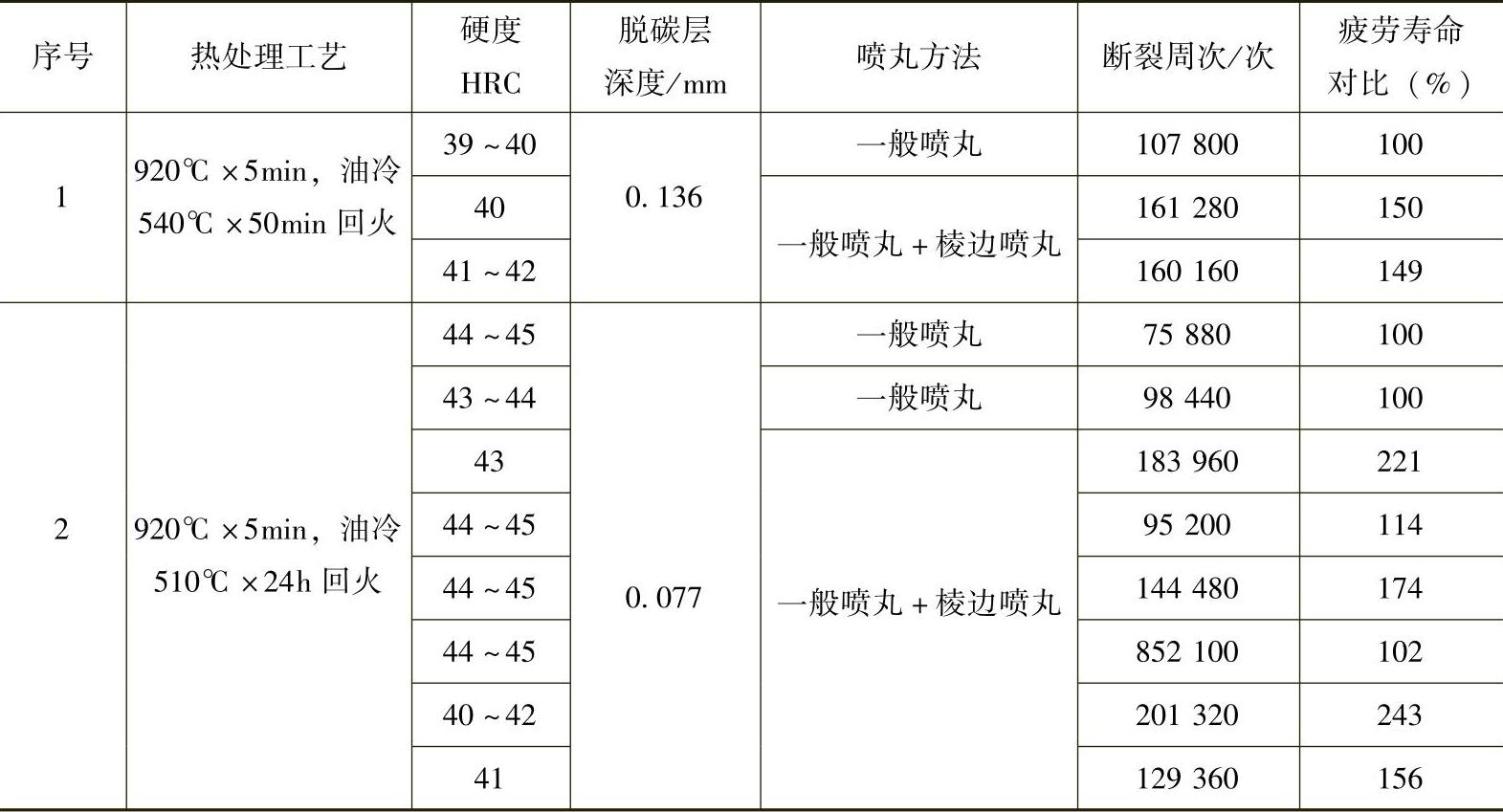
5.汽车钢板弹簧的热处理质量检验
关于钢板弹簧的工作过程,前面已经作了部分介绍,它的受力状况比较复杂,通常受到弯曲应力、压应力和剪切应力的共同作用,因此整个截面必须淬透,回火后获得回火托氏体组织,具有高的屈强比和优良的疲劳强度等,能满足弹簧的工作要求。如果淬火后出现铁素体、珠光体或贝氏体组织,则将使弹簧回火后的力学性能严重恶化。调质处理后的显微组织一般按回火后回火托氏体和铁素体的形态、数量以及分布分为8级,见表5-10,1~4级为合格组织。
表5-10汽车钢板弹簧热处理后金相组织的分级
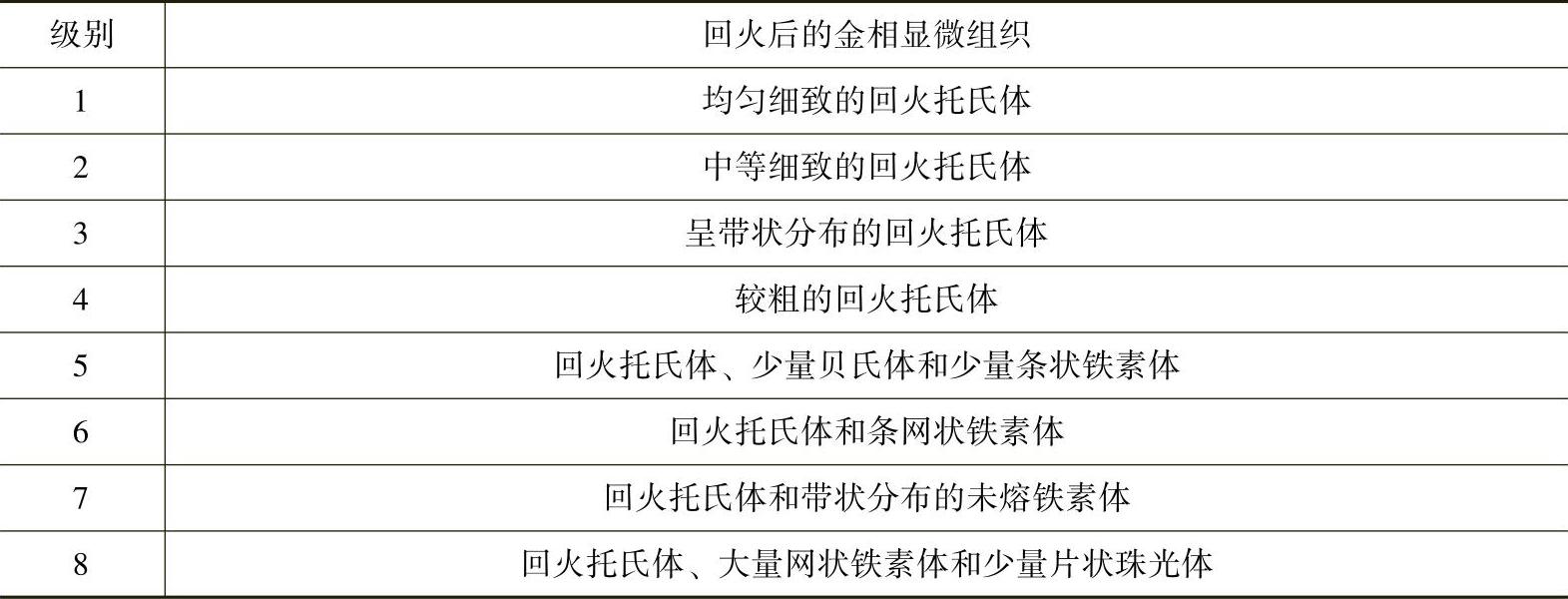
试验表明调质处理后的钢板弹簧如果有贝氏体和铁素体,则抗拉强度和冲击韧度将明显降低,对弯曲疲劳寿命的影响尤为显著,见表5-11。
表5-1160Si2MnA钢板金相组织与力学性能的关系
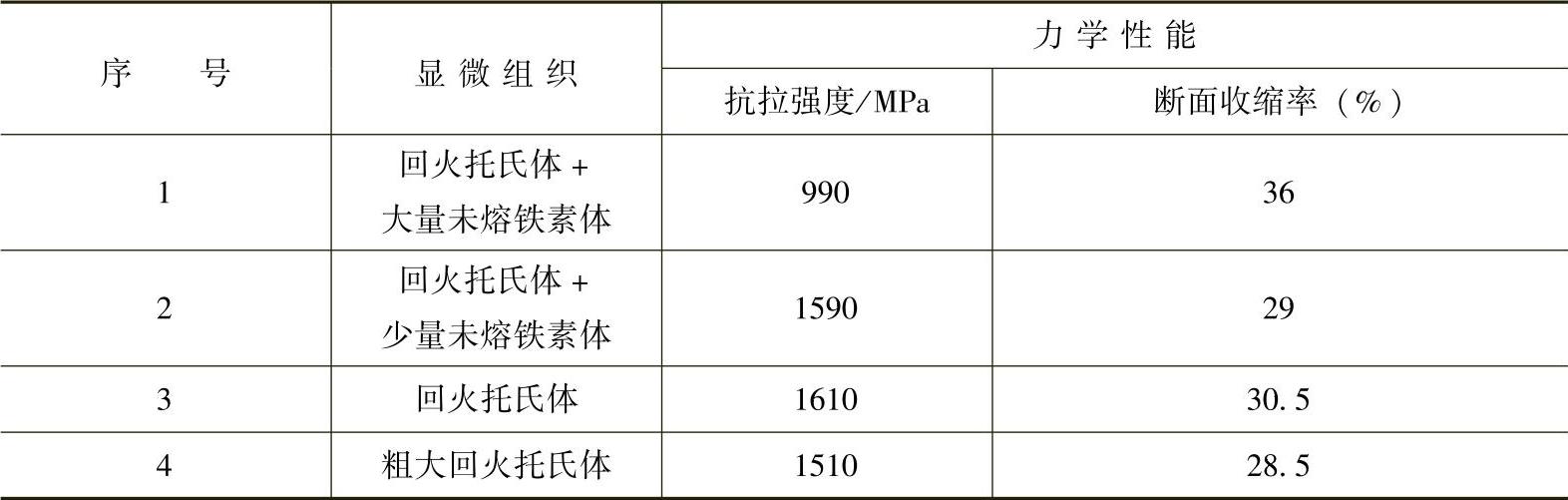
从表中可知,严格控制钢板弹簧热处理后的金相组织,选择合理的热处理加热、冷却工艺参数是保证钢板弹簧质量的前提,也是提高其使用寿命的有效措施。
钢板弹簧抛丸校直后,进行磁粉无损检测和石墨化检查。抛丸或喷丸可使表面0.25mm内存在压应力层,提高了疲劳强度,疲劳寿命可达到50万次以上。
6.汽车钢板弹簧的常见热处理缺陷分析与对策
从众多失效板簧的断口分析可知,钢板弹簧的棱边是疲劳断裂源,为应力最集中的部位,是热轧和热处理过程中出现缺陷的位置,检查发现棱边的脱碳程度比其他位置严重,脱碳层比其他位置深。一般弹簧出现的质量问题是表面脱碳、脆性的马氏体组织、组织粗大、非马氏体组织过多、回火不足等,因此在实际的热处理过程中,应严格执行工艺要求,并注重减少导致上述缺陷的根源,从而使弹簧的疲劳强度和使用寿命会得到大幅度的提高。表5-12为汽车钢板弹簧的常见热处理缺陷分析与对策。
表5-12汽车钢板弹簧的常见热处理缺陷分析与对策
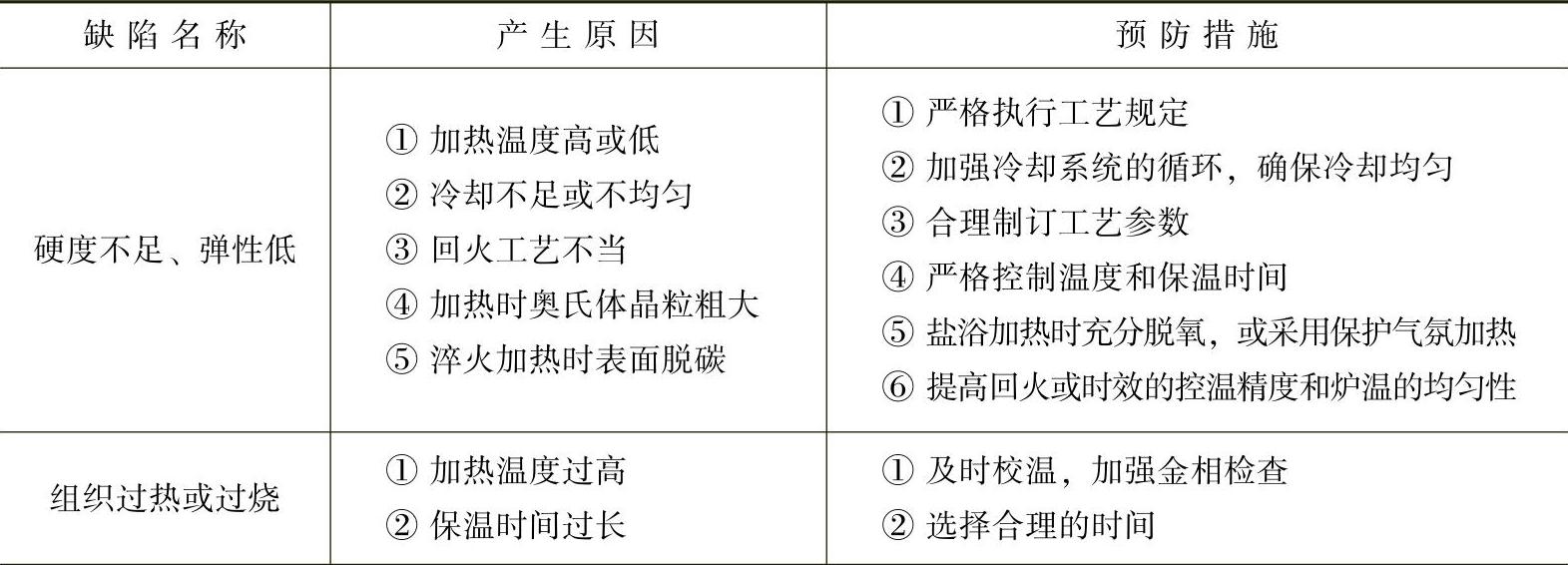
(续)
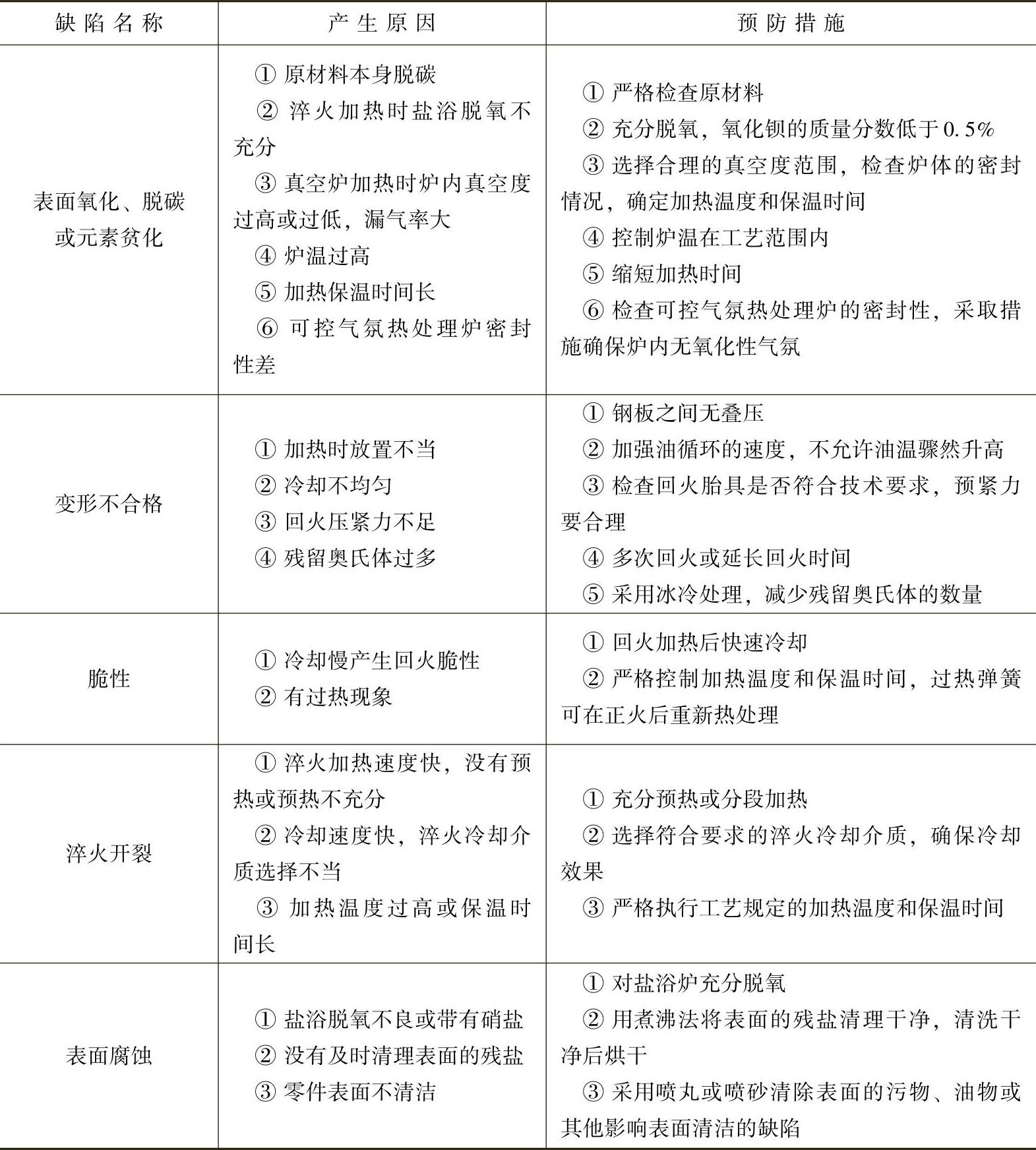
相关推荐