【摘要】:图10-15双刃扁钻图10-16四直槽钻铰复合钻2.制孔工艺复合材料制孔指钻孔钦孔及他窝3 个加工工序。由于不同纤维增强的复合材料性能差录较大,相应的制孔工艺也不尽相同。凯芙拉纤维复合材料钻孔钻头,应以能否迅速沿孔周切断凯芙拉纤维来衡量其优劣。图10-17三尖两刃钻头图10-18双刃定心钻对于由凯芙拉纤维与碳纤维组成的混杂复合材料,由于这两种纤维的加工特性不一样,将其混杂制成构件后,孔加工的难度更大。
1.制孔刀具
(1)刀具材料
碳纤维硬度较高,为HRC53~65,而高速钢钻头常温硬度仅为HRC62~65,两者极为接近。因而用高速钢刀具加工碳纤维复合材料时,材料中的纤维硬质点使刀具表面产生严重的磨料磨损。为此,必须采用高硬度刀具材料,如硬质合金和金刚石等,或者在钻头表面镀耐磨镀层。
①硬质合金。在国产硬质合金中,目前材质为Y330的φ3~φ8 mm的整体式硬质合金麻花钻、硬质合金锪窝钻、硬质合金铰刀,已可满足碳纤维复合材料制孔要求,如图10-10~图10-12所示。

图10-10 硬质合金麻花钻
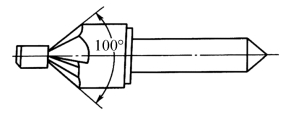
图10-11 硬质合金锪窝钻

图10-12 硬质合金铰刀
②人造金刚石。硬质合金刀具虽能满足碳纤维复合材料制孔要求,但在实际生产中也存在一些问题:一是加工大孔时,若仍用大直径硬质合金钻头,不仅成本高,且钻削时的轴向力会随钻头直径加大而急剧增大,易引起碳纤维复合材料分层;二是硬质合金锪窝钻在台钻上至多锪190 个窝后即磨钝,且不能重新修磨,故使用寿命较短。加之这种整体式硬质合金锪窝钻制造工艺复杂,目前尚不能进行工业化生产,所以成本高,经济效益低。
随后研制开发的人造金刚石套料钻(见图10-13)和锪窝钻弥补了上述不足。这种金刚石刀具的基体是用经调质的45 号钢或工具钢制成的,其切削部分用电镀法均匀镀上一层人造金刚石。金刚石粒度可根据加工需要进行选择,一般来说,加工件表面粗糙度和精度要求不高的可选粗粒度的金刚石刀具。粗粒度刀具切削轻快,工作效率高,刀具寿命长。如果加工件有精度和表面粗糙度要求应选用较细粒度的金刚石刀具。这种用电镀法将两种材料组合在一起的刀具,具有内韧外刚的特点,不仅耐用度高,而且克服了整体式硬质合金刀具的脆性,可满足实际装配条件下的使用要求。这类刀具的实际成本优于硬质合金刀具,具有发展潜力,在国内外越来越受重视。
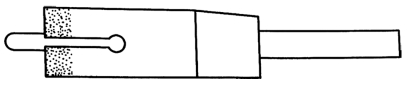
图10-13 人造金刚石套料钻
③聚晶金刚石(PCD)。聚晶金刚石(PCD)钻头是目前在高速下切屑碳纤复合材料最理想的刀具,PCD 材料很硬,但同时也很脆,因此做成整体式钻头是不适宜的。通常是将聚晶金刚石刀片钎焊在硬质合金钻头的钻尖上,或是用粉末冶金方法烧结在钻尖上。如图10-14所示为我国研制的银片式直槽PCD 钻头。
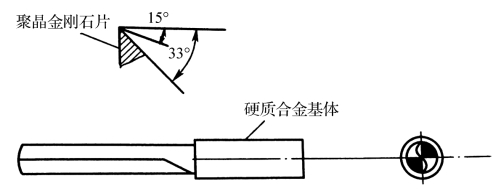
图10-14 银片式直槽聚晶金刚石钻头
(2)钻尖几何参数
提高刀具寿命,除选用高硬度耐磨材料外,钻尖几何参数及钻型选择也是一个重要方面。研究结果表明,对常用的麻花钻(见图10-6),如顶角(2φ)在100°~120°、后角在15°~25°、螺旋角在25°~30°、钻芯厚度在0.9~1.3 mm(对直径4.85 mm 钻头),进给轴向力较小,钻头耐用度较高。
为解决用整体式硬质合金麻花钻在复合材料上钻孔必须加衬垫的问题,改进钻头形状是可行的途径。如图10-15所示的双刃扁钻,用台钻或自动进给钻钻孔,可不加衬垫。如图10-16所示是由双刃扁钻改进而成的四直槽钻铰复合钻,只要进给不要太快,不加衬垫,可获得满意的质量。
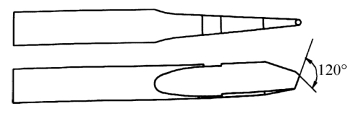
图10-15 双刃扁钻
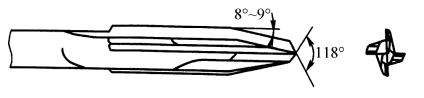
图10-16 四直槽钻铰复合钻
2.制孔工艺
复合材料制孔指钻孔钦孔及他窝3 个加工工序。由于不同纤维增强的复合材料性能差录较大,相应的制孔工艺也不尽相同。
(1)钻削工艺
对碳纤维复合材料,当孔径在8mm 以下时,通常使用整体式硬质合金麻花钻钻孔,孔的出口面必须加衬垫,一般选用低进给(0.02~0.06 mm/r)和较大转速(1400~2400 r/min)为好。当孔径大于8 mm 时,先用硬质合金钻头钻一小孔,然后再用如图10-13所示的电镀金刚石套料钻制出大孔。
对凯芙拉纤维复合材料,由于该纤维具有良好的韧性,且基体树脂的黏性较差,加工碳纤维复合材料的刀具和工艺方法完全不适用于凯芙拉纤维复合材料。凯芙拉纤维复合材料钻孔钻头,应以能否迅速沿孔周切断凯芙拉纤维来衡量其优劣。如图10-17所示是适于钻削这种复合材料的Y330 硬质合金三尖两刃钻头,具有两个锋利外刃尖和一个起定心作用的中心尖。为获得两个关键的外尖,主刃磨成了圆弧形,钻孔时中心尖先切入复合材料定位中心,然后依靠两锋利的外刃尖在复合材料上画圆进行切削,并迅速沿孔边切断凯芙拉纤维,从而得到无毛边的孔。对于大孔(如孔径在12 mm 以上的孔),先用三尖两刃钻头钻一小孔,然后用如图10-18所示的双刃定心钻可钻出无毛边的大孔。为防出口面分层,第一次钻先不钻通,约钻入一半后将钻退出,然后再从背面钻通另一半,这样可不用加衬垫支撑。用三尖两刃钻钻小孔,速度以110 m/min 左右为最佳,钻大孔孔径为12~20 mm,速度以25~90 m/min 为宜,进给量以较小为好。
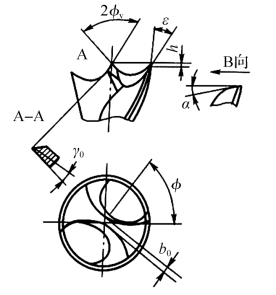
图10-17 三尖两刃钻头
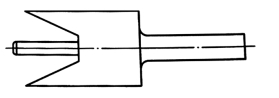
图10-18 双刃定心钻
对于由凯芙拉纤维与碳纤维组成的混杂复合材料,由于这两种纤维的加工特性不一样,将其混杂制成构件后,孔加工的难度更大。现以混杂复合材料面板(外表层为凯芙拉纤维、内层为碳纤维)、Nomax 蜂窝芯子的夹层结构为例,来说明其钻孔工艺。
对小孔,可直接用三尖两刃硬质合金一次钻出,转速可用2440~4100 r/min。
对大孔,先用三尖留钻小孔(孔径比双刃定心钻的导柱大0.1 mm),然后用双刃定心钻将表层凯芙拉纤维切断,再换上同样直径的金刚石套料钻,钻削碳纤维和Nomax 蜂窝。钻削速度:双刃定必钻用800~4100 r/min,金刚石钻头用1400~4100 r/min。
(2)锪窝工艺
对碳纤维复合材料,既可用普通三刃式Y30 硬质合金德窝钻以500~800 r/min 转速进行,也可用人造金刚石锪窝钻,以1400~2400 r/min 转速进行。后者锪窝质量及使用寿命均远高于前者。
对凯芙拉纤维复合材料,锪窝非常困难,这是因为钻孔时已将纤维切断,当用锪钻锪窝时,因为凯芙拉的柔韧性,被锪钻刀刃切削的纤维往往产生退让,绝大部分难被切断,易被挤压在窝边,刀刃仅刮去复合材料中的树脂,从而造成极其粗粒的锪窝表面和大量纤维毛边。针对这一情况,可用三种刀具锪窝。
①在凯芙拉复合材料板上加一块铝板,用普通电窝刀具锪窝。铝板将限制凯芙拉纤维滑移,选用80~160 r/min 的锪窝速度,锪出来的窝面较光滑,入口处仅有一圈很小的毛边。
②用四刃细锯齿锪窝钻锪窝(见图10-19)。
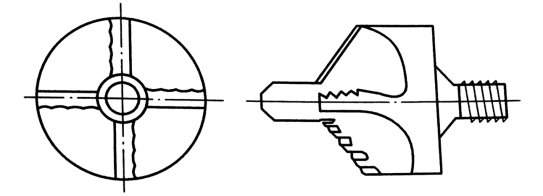
图10-19 四刃细锯齿锪窝钻
这种饱窝钻是美国生产的,4 个切削刃上开有一些锯齿状小槽。在锪窝过程中,随着刀具的旋转,切削刃利用小齿绞住凯芙拉纤维,在60~110 r/min 转速下,能获得较好切削效果。
上述两种锪钻加垫板锪窝时,应采用专用锪窝限位器(见图10-20)先将铝板钻一小孔,使锪钻导柱能插入,然后通过限位器的弹簧压紧铝垫板进行锪窝,锪窝深度可以通过限位器调整。
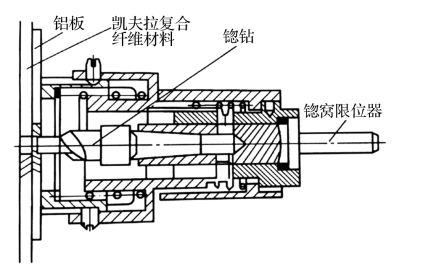
图10-20 专用锪窝限位器
③用C 形锪窝钻锪窝(见图10-21)。这种锪钻有两个C 形刃,锪窝时能将凯芙拉纤维引向中心切断。在较低速度下,不用垫铝板,即可加工出高质量的窝。

图10-21 C形锪窝钻
凯芙拉—碳纤维混杂复合材料层压板的锪窝,可采用加工凯芙拉纤维材料的刀具C 型锪窝钻进行。
(3)铰孔工艺
碳纤惟复合材料的铰孔,可采用与普通直槽刀相同的Y330 硬质合金短铰刀以500 r/min 的速度进行。而凯芙拉纤维复合材料,由于通常均用于非主要受力部位,一般钻孔后即直装配。
3.叠层材料的钻孔
叠层材料是指纤维复合材料与金属板叠合在一起的结构。由于叠合材料的性能相差很大,给钻孔带来相当大的困难。以碳纤维复合材料和钛合金叠层材料为例,通常,钻削碳纤维复合材料需用高速和聚晶金刚石刀具,而钻削铁合金的切削温度高,聚晶金刚石(PCD)中的碳原子容易扩散到钛合金中,造成刀具的扩散磨损,故应选用硬质合金钻头以低速加工。所以叠层材料钻孔的传统方法是采用分步钻孔,即钻不同材料时采用不同钻头和速度,但这样极大地影响了加工效率和质量。为此,人们对钻孔进行了大量研究,探索出以下几种有效钻削方法。
①自适应钻孔:钻头针对不同材料层自动改变转速和进给量。
②啄式进给钻孔:用不连续的啄式(啄木鸟式)方式进行钻孔。避免连续钻孔引起的切屑长、热量大等问题,提高钻孔质量。
③复合金刚石钻:这种钻头的PCD 刀头不是钎焊到刀尖上,而是采用粉末冶金的方法压在硬质合金钻头的钻尖上。这种钻头在钻碳纤复合材料/钛合金叠层材料时,比钎焊PCD钻头提高耐用度50 倍以上。如图10-22所示就是波音公司用来钻削碳纤维复合材料和钛合金的粉末冶金烧结的PCD 钻头。
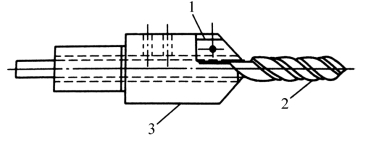
图10-22 粉末冶金烧结的PCD 钻头
1—沉头钻刀片(PCD);2—PCD 钻头;3—沉头钻钻夹头
相关推荐