【摘要】:3D打印技术是一项多学科交叉、具有绿色智能特征的前沿先进制造技术,实现了设计图形数据直接生产实物的快速制造。焊接的堆焊工艺应被认为是3D打印的前驱。日、美一些公司已经将精密铣削技术和金属部件3D打印技术融合,实现复杂零部件的快速制造。
3D打印技术是一项多学科交叉、具有绿色智能特征的前沿先进制造技术,实现了设计图形数据直接生产实物的快速制造。在航空航天、国防军工、生物医学等众多领域有广泛的应用前景,成为国内外科研机构和制造企业的发展热点。其概念是从20世纪80年代的快速成形增材制造发展而来的,即采用增材堆积的技术思路,根据最终尺寸要求进行材料的堆积,堆积成形的零件直接使用,或者对成形零件的表面进行微量加工,降低表面粗糙度后即可使用。相比传统制造工艺,3D打印具有很多优势:①材料总体利用率高;②无需开模,制造工序少,周期短;③可制造复杂结构的零件;④根据力学性能要求自由设计,较少考虑制造工艺;⑤更好地实现CAD与CAM一体化的融合,实现自由成形制造。图12-35是分别采用电子束铺粉和激光铺粉熔融快速直接成形制造的金属结构件。
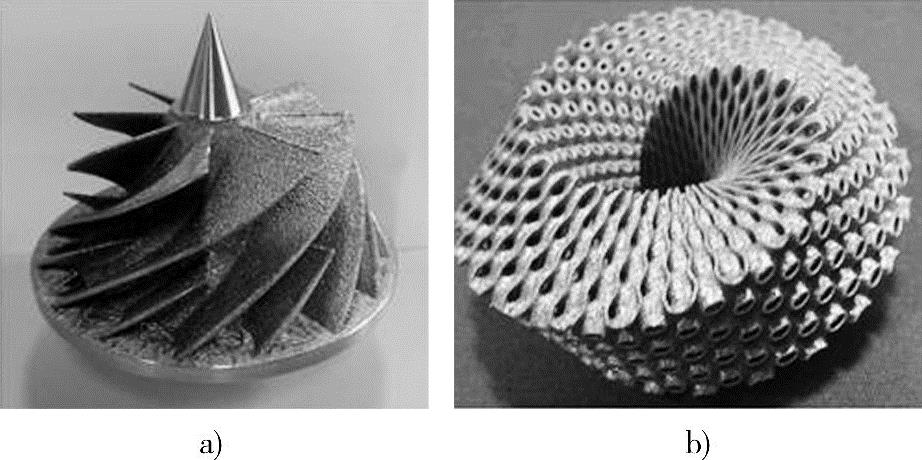
图12-35 快速直接成形制造的复杂结构件
a)电子束铺粉 b)激光铺粉
在3D打印技术的工程化应用中,对大型金属零部件3D打印日趋关注,当前的热点表现在:①从技术难度上分析,一是功能性的实物制造比模型制造难度大;二是金属等材料的成形温度更高且凝固时产生较大的内应力,容易出现开裂、变形、气孔等现象,成形工艺比较复杂。对打印零部件的内部质量、机械强度、成形速度、尺寸精度均有较高要求;②从热源应用角度,金属零件的3D打印除了采用电子束与激光作为热源外,还可以采用高能量密度电弧和等离子电弧,填充的材料从粉末到丝材;③从提高成形效率、降低成本的角度,将增材制造与以往的切削减材制造技术相结合,采用电弧填丝等低成本、低分辨率的打印工艺,同时用在线切削加工等措施来保证成形精度,使最终成形零件达到技术标准。
焊接的堆焊工艺应被认为是3D打印的前驱。当前CAD/CAM以及视觉传感等新技术能使机器人在工作坐标系下自动生成轨迹,实现零件的直接成形(见图12-36),或对待修复的工件进行三维重构。图12-37是用熔化极气体保护焊方法完成的冲击式水轮机水斗的再制造。
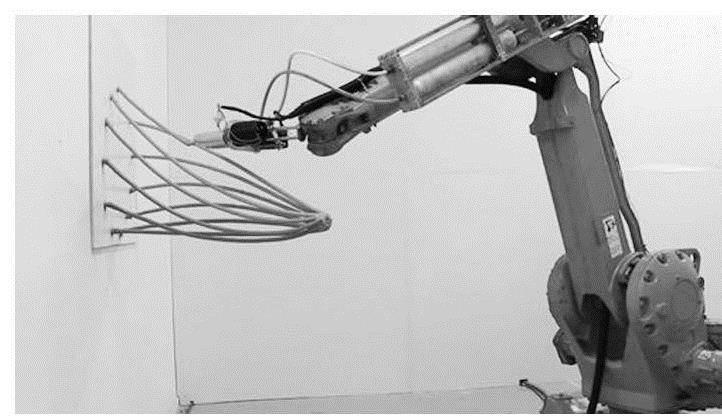
图12-36 零件的直接成形
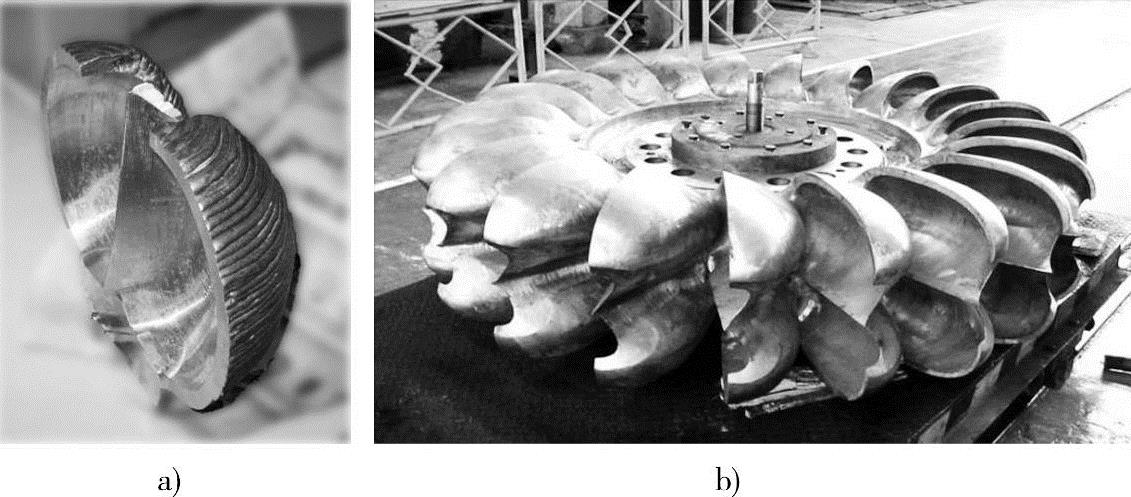
图12-37 机器视觉传感加三维重构的堆焊工件
a)焊接后 b)加工组装后
金属部件直接自由成形的“3D打印技术”仍在迅速发展中,要解决的问题有以下几个方面:
1)目前大部分金属零部件3D都采用盲打工艺,对每一种形状零件、每一种材料都需要做大量试验,几乎每一层都需要设定工艺参数,而且当成形过程中出现异常时,系统无法识别,也不能自动调整,如果不去人工干预,将造成无法继续成形或将缺陷留在工件里,必须由经验丰富的专业技术人员操作机器,并随时观察成形状态才能做出较合格的零件,影响了金属3D打印的工业化应用。
2)为了提高3D打印零件的成形精度,常规的方法是减小3D打印点的尺寸,提高分辨率,比如提高激光束的汇聚性,让熔化区域变得更小,单个熔化区域尺寸达到微米级,但同时给超细材料的供给带来很大难度,另外熔化区的变小会带来成形速度及效率大幅降低而不适于工业领域应用。而采用目前的电弧焊接方式,虽具有填丝或送丝方便、熔覆率高等优势,但熔化区域及热影响区较大,对工件的成形与控性均提出了较高的要求。
3)多机器人、多功能的技术协同为解决大尺寸金属部件的自由成形提供了一种可行的条件。日、美一些公司已经将精密铣削技术和金属部件3D打印技术融合,实现复杂零部件的快速制造。
包括焊接应用在内的工业机器人制造系统是对资金、技术、人才需求“三高”的产品,需要持续不断的创新。以大数据、云计算、移动互联网为代表的新一代信息技术与机器人技术的融合促进了创新的加速,不仅将会开发出更具自主学习能力和自主解决问题能力的新型智能焊接机器人,还将为各焊接机器人系统建立起相应的互联网和知识库的“云空间”,使其通过互联网进行交互、通过云计算提升焊接机器人的智能化水平。
相关推荐