【摘要】:手动脱模是在开模后,由人工操作的方式推出机构取出塑件。上述脱模机构中,手动脱模的动作平稳,对塑件无撞击,操作安全,但劳动强度大,生产效率低。一次推出机构是最常用的脱模方式,塑件只经过推出机构的一次动作就能脱模,故又称简单脱模机构。3)脱模板脱模。
在塑件注射成型的每一个工作循环中,都必须让塑件从模具型腔中或型芯上脱出,模具中这种脱出塑件的机构称为脱模机构(或称推出机构、顶出机构)。脱模机构的作用是完成塑件脱出、取出两个动作,即首先将塑件和浇注系统凝料与模具型腔或型芯松动分离,称为脱出,然后使塑件与模具完全分离。
1.脱模机构的分类
脱模机构可按驱动方式、脱模动作或推出零件的形式等进行分类。
(1)按驱动方式分类
1)手动脱模。手动脱模是在开模后,由人工操作的方式推出机构取出塑件。
2)机动脱模。机动脱模是利用注射机的开模动作使塑件脱离型腔。开模时塑件先随动模一起移动,达到一定位置时,脱模机构被注射机上固定不动的推杆(或顶杆)顶住而不能随动模继续移动,从而使塑件脱离型腔。
3)液压脱模。注射机上设置有专用的液压顶出装置(即液压缸),当开模到一定距离后,通过液压缸活塞驱动而实现脱模动作。
4)气动脱模。利用压缩空气,通过型腔里微小的顶出气孔或受气阀将塑件吹出。
上述脱模机构中,手动脱模的动作平稳,对塑件无撞击,操作安全,但劳动强度大,生产效率低。机动式生产效率高,推出力大,生产中被广泛采用。液压式的顶出力、速度和时间可通过液压系统调节,但需要专用液压装置。气动式可以直接吹出塑件,并且制件表面无任何痕迹,但是需要专用装置。
(2)按脱模机构的动作分类
1)一次推出机构。一次推出机构是最常用的脱模方式,塑件只经过推出机构的一次动作就能脱模,故又称简单脱模机构。
2)二次推出机构。塑件经过两次不同的动作才能脱模的机构,称为二次推出机构。
3)延迟动作推出机构。在某些情况下,当塑件被推出后还需延迟动作再推出浇注系凝料等的机构,称为延迟动作推出机构,该机构尤其适用于潜伏式浇注系统注射模具。
(3)按模具中的推出零件分类
1)推杆式脱模。应用广泛,常用圆形截面推杆。
2)推管式脱模。适用于薄壁圆桶形塑件。
3)脱模板脱模。脱模板也称推件板,常用于薄壁容器、壳体,以及不允许存在推出痕迹的塑件。
4)推块式脱模。适用于齿轮类或一些带有凸缘的制件,可防止塑件变形。
5)利用成型零件推出制件的脱模。适用于螺纹型环一类的制件,利用模具中某些成型零件推出塑件。
6)多元联合式脱模。对于某些深腔壳体、薄壁制品及带有环状凸起、凸肋或金属嵌件的复杂制件,为防止其出现缺陷,常采用两种或两种以上的推出机构联合动作以完成脱模过程。
(4)混合分类 随着塑件品种及尺寸大小、形状的不同,脱模机构的种类很多,不便统一标准而划分,在生产实践中用混合法较为实用和直观,如图5⁃55所示。
2.脱模机构的设计要求
1)尽量使塑件留在动模上。这是因为要利用注射机推出装置来推出塑件,必须在开模过程中保证塑件留在动模上,这样模具结构较为简单。
2)保证塑件不变形、不损坏。为此,必须正确分析塑件与型腔各部位的附着力的大小,选择合理的推出方式和推出部位,使脱模力合理分布。由于塑件收缩时包紧型芯,因此脱模力作用位置应尽量靠近型芯,同时亦应布置在塑件刚度、强度最大的部位(如凸缘、加强筋等处),作用面积也应尽可能大些,以免损坏塑件。
3)保证塑件外观良好。也就是说,推出塑件的位置应尽量选在塑件的内部或对塑件外观影响不大的部位。
4)结构可靠。推出机构应工作可靠,运动灵活,具有足够的强度和刚度。
3.脱模力的计算
脱模力是指将塑件从型芯上脱出时所需克服的阻力。它是设计脱模机构的重要依据之一。
当塑件收缩包紧型芯时,受力情况如图5⁃56所示。未脱模时,正压力(F正)就是对型芯的包紧力,此时的摩擦力为F阻=fF正。然而,由于型芯有锥度,故在脱模力(F脱)的作用下,塑件对型芯的正压力降低了F脱sinα,即变成了(F正-F脱sinα),所以此时的摩擦力为
F阻=f(F正-F脱sinα)=fF正-fF脱sinα (5⁃12)
式中 F阻——摩擦力(N);
f——摩擦因数,一般取f=0.15~1.0;
F正——因塑件收缩对型芯产生的正压力(即包紧力)(N);
F脱——脱模力(N);
α——脱模斜率,一般为1°~2°。
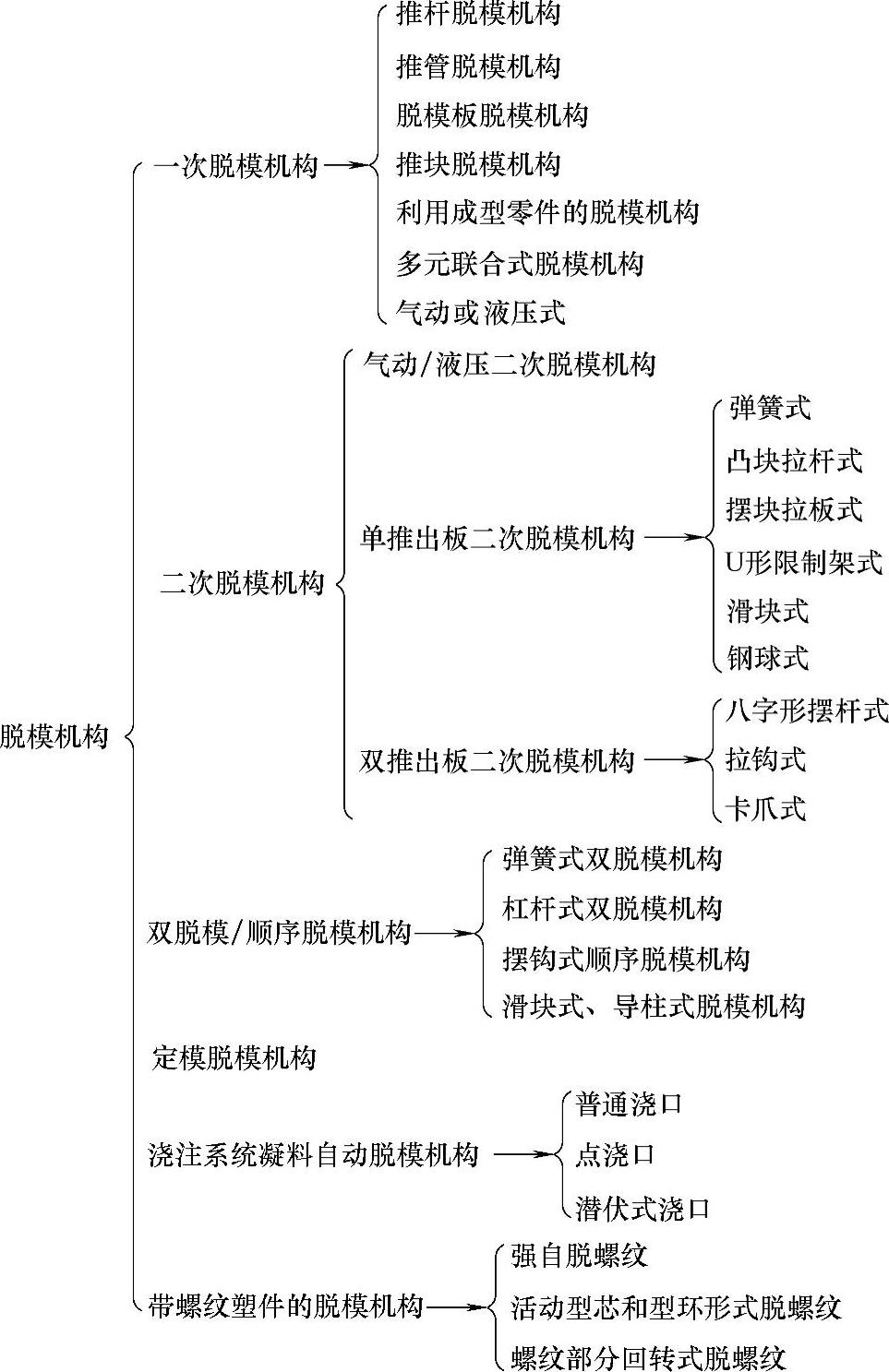
图5⁃55 脱模机构的分类
根据受力图可列出平衡方程式
ΣFx=0 (5⁃13)
即
F脱+F正sinα=F阻cosα
F脱=F阻cosα-F正sinα (5⁃14)
F脱+F正sinα=F阻cosα
即
F脱+F正sinα=(fF正-fF脱sinα)cosα
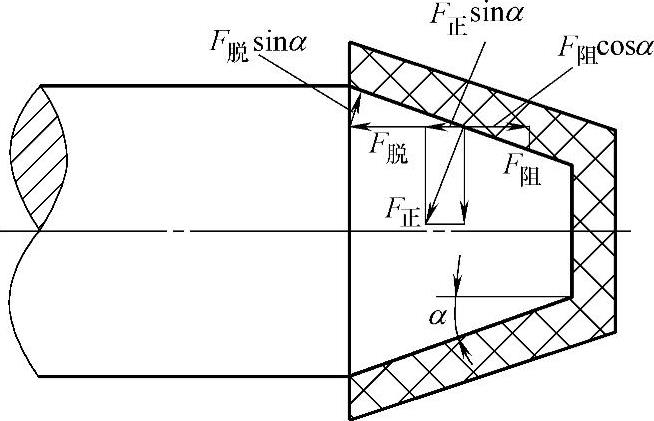
图5⁃56 塑件脱模力分析图
即

由于α一般很小,故fF脱sinα之值可以忽略不计。
忽略fF脱sinα后,F阻=fF正,上式为
F脱=F阻cosα-F正sinα
=fF正cosα-F正sinα
=F正(fcosα-sinα) (5⁃16)
F正=pA (5⁃17)
式中 p——塑件对型芯产生的单位正压力(包紧力)(MPa);
A——塑件包紧型芯的侧面积(mm2)。
一般p=8~12MPa,薄件取小值,厚件取大值。
对于不通孔的壳形塑件脱模时,还需要克服大气压力造成的阻力F阻′,其值为
F阻′=0.1A′ (5⁃18)
式中 A′——型芯断面面积(mm2)。
故不通孔的壳形塑件脱模时的总脱模力应为
F脱′=F脱+F阻+F阻′
或
F脱′=F脱+0.1A′ (5⁃19)
对于一般模具,可按F脱=F正(fcosα-sinα)计算。
对于要求严格的模具,最好是按
计算。
4.一次脱模机构(简单脱模机构)
凡在动模一边施加一次推出力,就可实现塑件脱模的机构称为一次脱模机构,也称简单脱模机构。一次脱模机构通常包括推杆脱模机构、推管脱模机构、脱模板脱模机构、推块脱模机构、多元联合脱模机构和气动脱模机构等。
(1)推杆脱模机构 推杆(顶杆)脱模机构是最简单、最常用的一种形式,具有制造简单、更换方便、推出效果好等特点,其典型结构如图5⁃57所示。它是由推杆1、推板5、推杆固定板2和挡销8等组成。推杆直接与塑件接触,开模后将塑件推出。
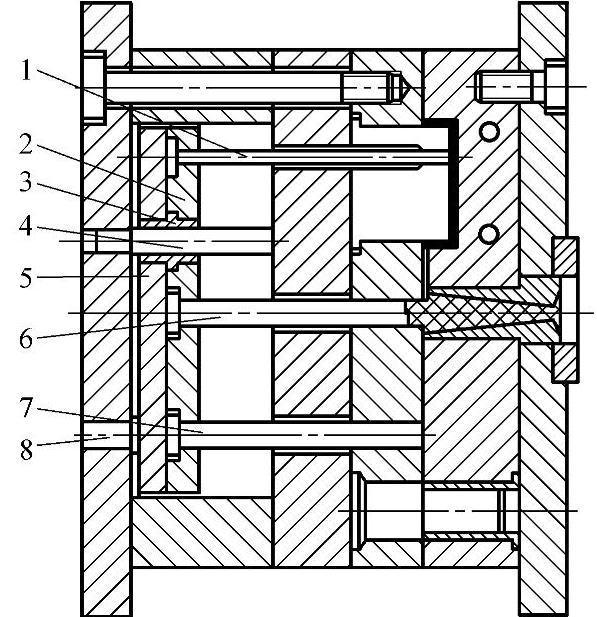
图5⁃57 推杆脱模机构
1—推杆(顶杆) 2—推杆固定板 3—推板导套 4—推板导柱 5—推板 6—拉料杆 7—回程杆(复位杆) 8—挡销(支承钉)
常用推杆推出机构的结构型式见表5⁃8。
表5⁃8 推杆推出机构的结构型式
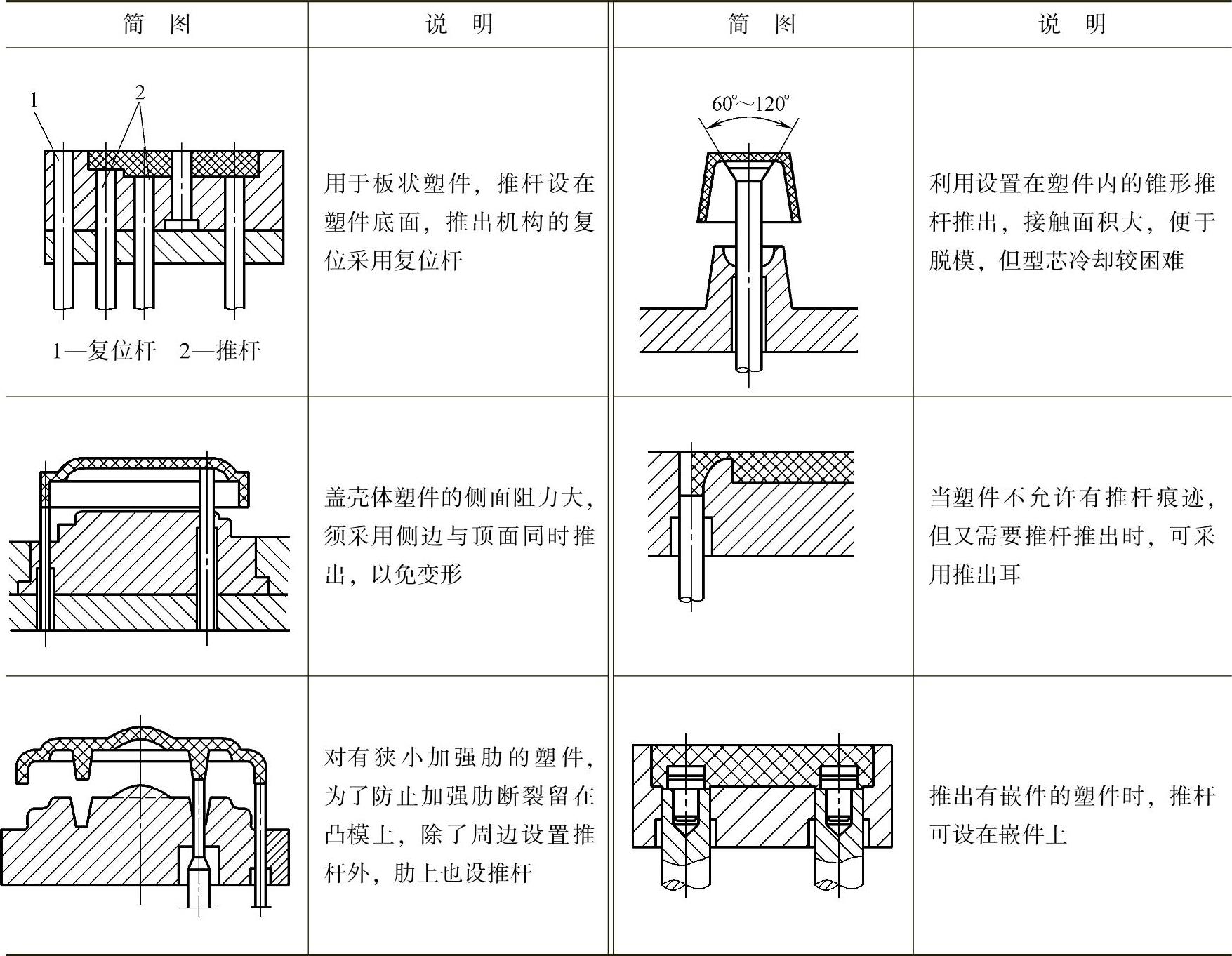
1)推杆的截面形状。推杆分为普通推杆与成型推杆两种。普通推杆只是推出塑件之用,其截面形状有圆形、方形及其他各种类型。成型推杆者除了推出塑件之外,还参与塑件局部成型,可做成塑件某一部分的形状,或作为型芯。
2)推杆的尺寸计算。圆形推杆的直径,可按欧拉公式简化计算,即

式中 d——推杆直径(mm);
L——推杆长度(mm);
F脱——塑件的脱模力(N);
E——推杆材料的弹性模量(MPa);
n——推杆数量;
k——安全系数,一般取k=1.5。
推杆直径确定后,还应进行强度校核,其计算式为

式中 [σ压]——推杆材料的许用压应力(MPa)。
3)推杆的固定形式。推杆与推杆孔的配合可采用H8/f8或H7/e7。配合表面的表面粗糙度一般为Ra0.8~Ra0.4μm。推杆在固定板中的形式如图5⁃58所示。图5⁃58a所示为一种常用形式,适用于各种形式的推杆。图5⁃58b是采用垫块或垫圈代替固定板上的沉孔,使之加固简便。图5⁃58c中,推杆的高度可以调节,螺母起固定锁紧作用。图5⁃58d所示是利用螺母顶紧推杆,适用于推杆直径较大及固定板较厚的情况。图5⁃58e所示是铆钉的形式,适用于直径小的推杆或推杆之间距离较近的情况。图5⁃58f所示是用螺钉紧固,适用于粗大的推杆。
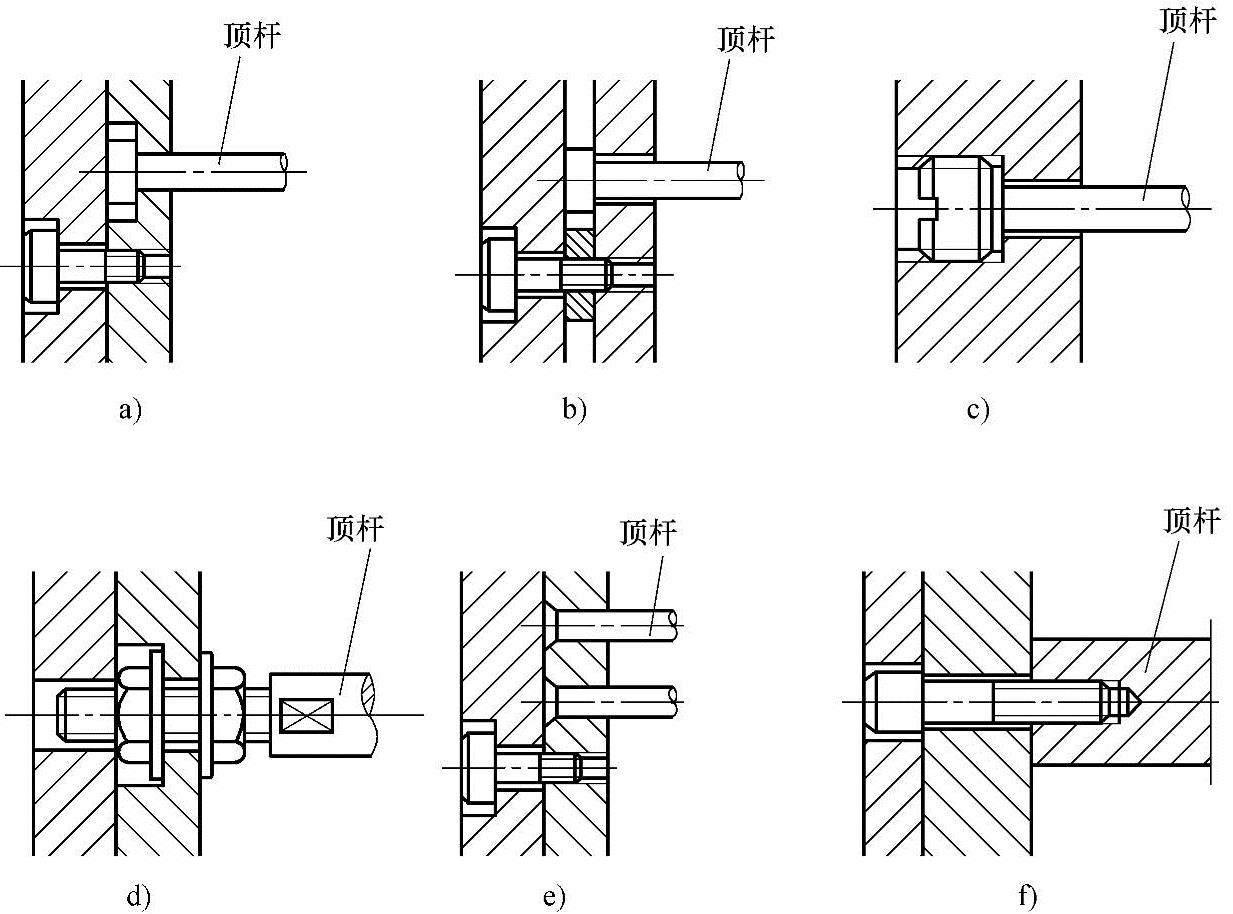
图5⁃58 推杆的固定形式
4)推出机构的导向。当推杆较细或推杆数量较多时,为了防止因塑件反阻力不均而导致推杆固定板扭曲或倾斜、折断推杆或发生运动卡滞现象,常在推出机构中设导向零件,一般包括导柱和导套。导柱一般不少于两个,大型模具要四个。图5⁃59所示为导柱的三种安装形式。其中,图5⁃59a、b所示的导柱除定位作用外,还能起到支撑柱的作用,以减少注射成型时动模支承板的弯曲。
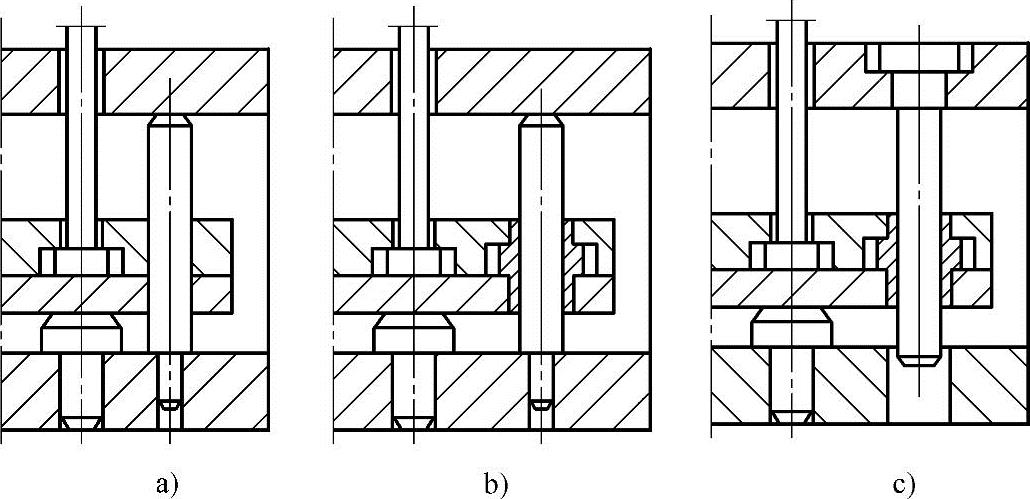
图5⁃59 推出机构的导向装置
5)推出机构的复位。脱模机构完成塑件顶出后,为进行下一个工作循环必须回复到初始位置。目前,常用的复位形式主要有复位杆复位和弹簧复位。
复位杆又称回程杆或反推杆。复位杆通常装在与固定推杆的同一固定板上,且各个复位杆的长度必须一致。复位杆一般设2~4根,为避免长期对定模板的撞击,可采取两种防止措施,其一是使复位杆端面低于定模板平面0.02~0.05mm,其二是在复位杆底部增设弹簧缓冲装置,如图5⁃60d所示。
弹簧复位是一种最简单的复位方式。推出塑件时弹簧被压缩,而合模时弹簧的回力就将推出机构复位。此外,弹簧还有使推杆预先复位的作用,尤其适用于带侧抽芯机构的模具。
图5⁃60~图5⁃62所示为几种复位形式。图5⁃60所示是用复位杆的形式,其中,图5⁃60a所示为开模时推杆推出塑件状态,图5⁃60b所示为合模时推出机构回位状态,图5⁃60c所示为在模具上装有反向销的复位杆,由于反向销作为磨损件容易替换,所以建议在使用复位杆时采用反向销,图5⁃60d所示是在复位杆底部装有弹簧缓冲装置。图5⁃61所示是推杆(或推管)兼作复位杆的形式。图5⁃62所示是弹簧式预复位形式。
此外,有时推杆也兼作复位杆用,如图5⁃63所示。
有时,复位杆也兼作导柱用,此时就可省去推出机构的导向元件,如图5⁃60b所示。
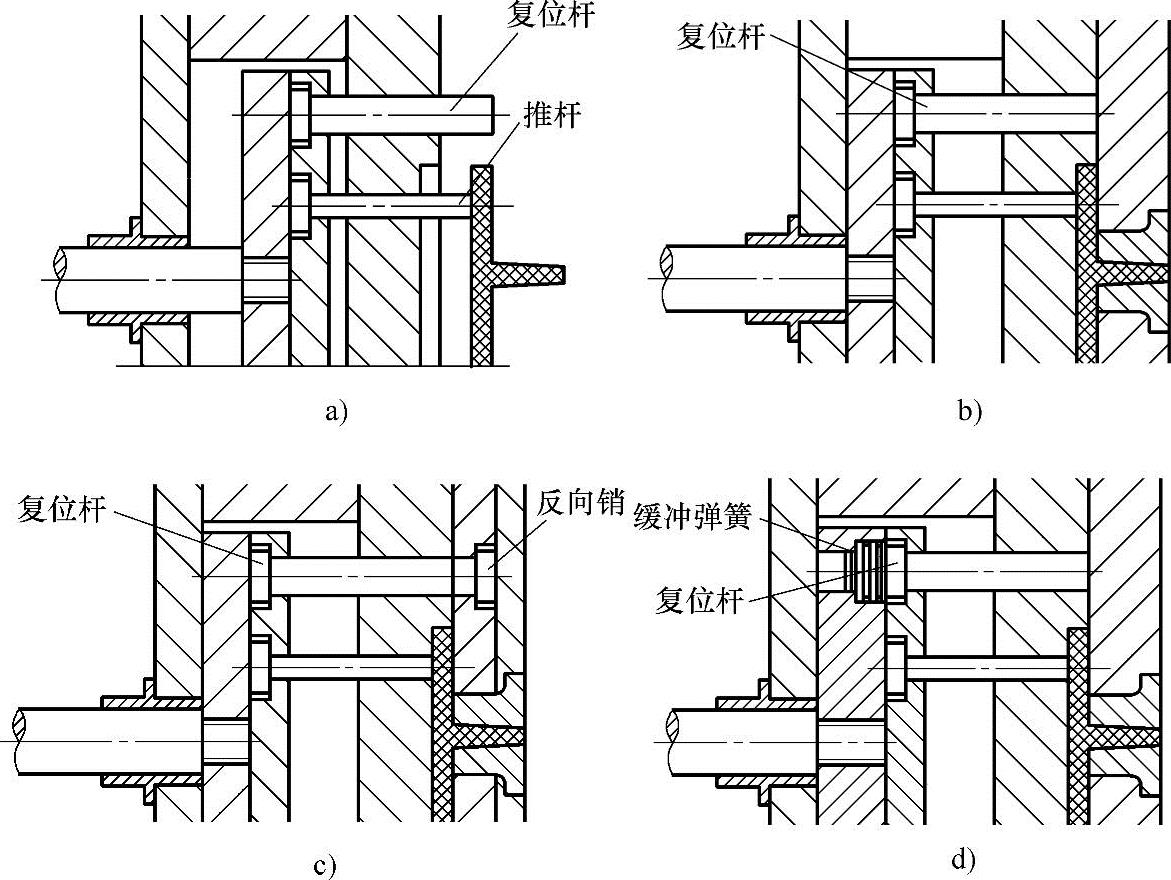
图5⁃60 复位杆的形式
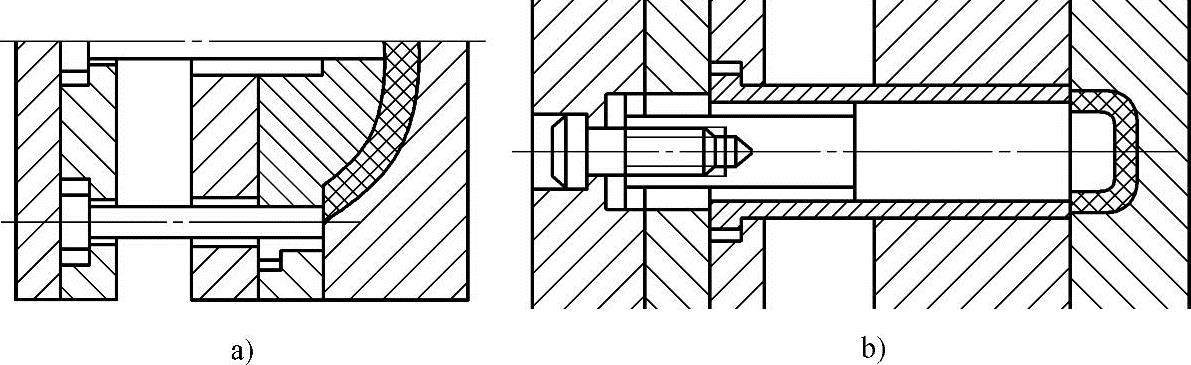
图5⁃61 推杆(或推管)兼作复位杆
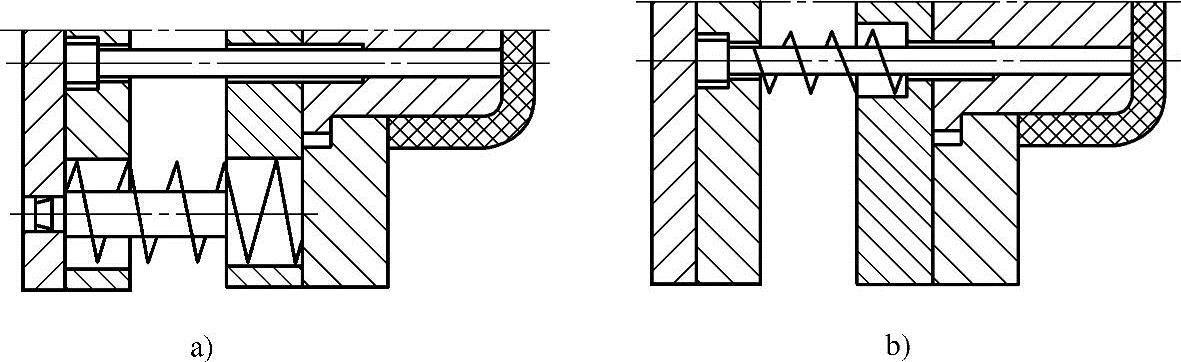
图5⁃62 弹簧先复位形式
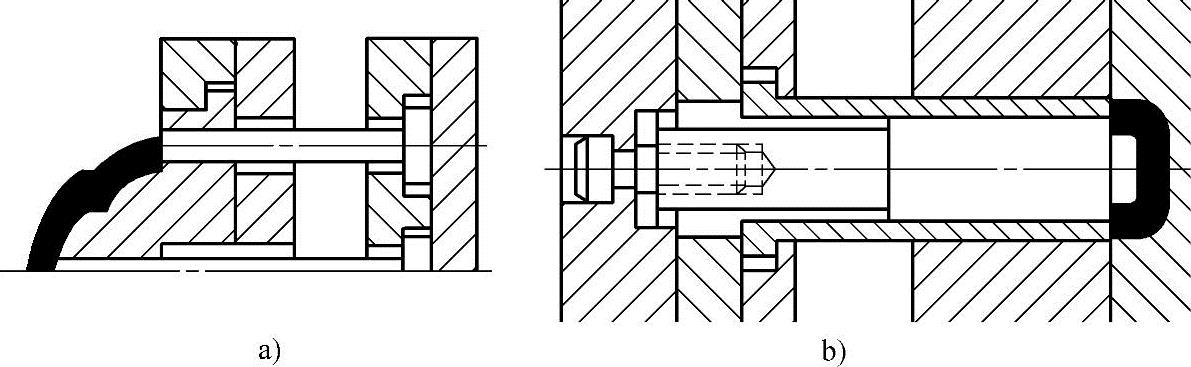
图5⁃63 推杆兼作复位杆
(2)推管脱模机构 推管又称空心推杆或顶管,特别适用于圆环形、圆筒形等中心带孔的塑件脱模。推管整个周边推顶塑件,使塑件受力均匀,无变形、无推出痕迹等优点。推管推出机构的常用方式是将主型芯固定于动模座板的推管脱模机构,如图5⁃64a所示。型芯穿过推板固定于动模座板上。此种结构型芯较长,型芯可兼作脱模机构的导向柱,多用于脱模距离不大的情况下。图5⁃64b所示为其配合形式。推管的内径与型芯配合,外径与模板配合,其配合精度一般为间隙配合,对于小直径推管取H8/f8或H7/f7,对于大直径推管取F8/f7。推管与型芯的配合长度为推出距离S加3~5mm,推管与模板的配合长度一般为推管外径的1.5~2倍,其余部分均为扩孔,推管扩孔为d+0.5(mm),模板扩孔为D+1(mm)。另外,为了不擦伤型腔,推管外径要略小于塑件相应部位的外径。
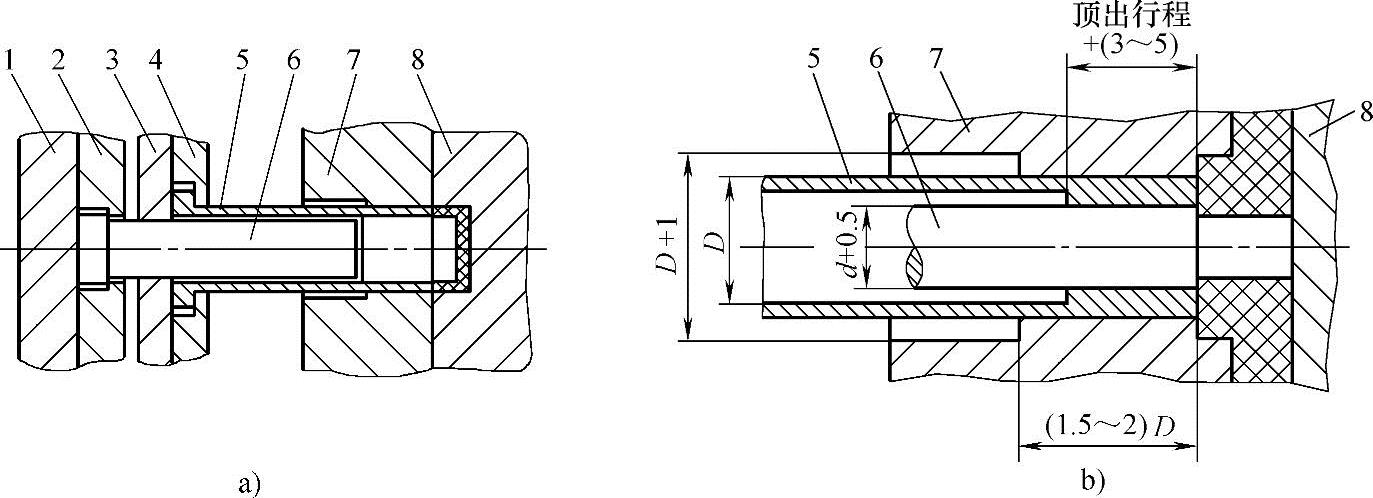
图5⁃64 主型芯固定于动模座板的推管脱模机构
1—动模座板 2—型芯固定板 3—推板 4—推管固定板 5—推管 6—主型芯 7—动模板 8—定模板
主型芯固定于动模型芯固定板的推管结构如图5⁃65所示。采用这种结构,型芯的长度可大为缩短,但推出行程包含在动模板内,致使动模的厚度增加,推出距离受限。型芯的固定方法如图5⁃65所示。
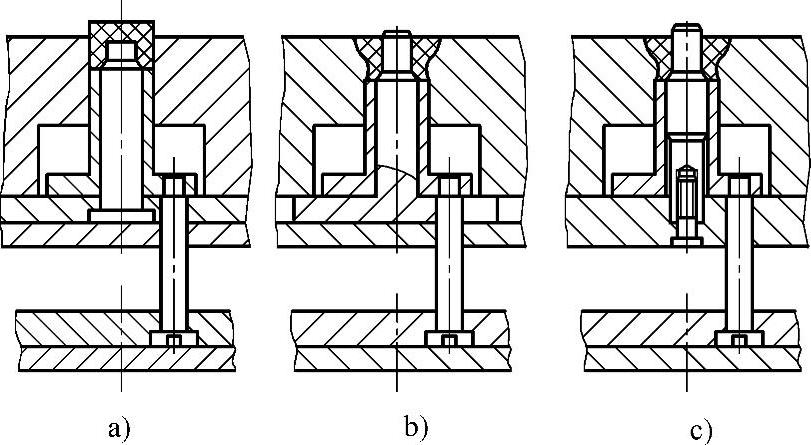
图5⁃65 主型芯固定于动模型芯固定板的推管结构
图5⁃66所示为推管中部开有长槽,型芯用圆销或扁销固定于动模支承板上,槽在圆销以下的长度L应大于推出距离。这种结构型芯较短,模具结构紧凑,但型芯的紧固力较小,要求推管和型芯及型腔的配合精度较高,适用于型芯直径较大的模具。

图5⁃66 推管中部开有长槽的推管结构
(3)脱模板脱模机构 脱模板又称卸料板或刮板。其特点是推出面积大、推力均匀,塑件不易变形,表面无推出痕迹,结构简单,模具不需要设置复位杆,适用于大筒形塑件或薄壁容器及各种罩壳形塑件。
1)脱模板的结构形式。脱模板的结构形式如图5⁃67所示。其中,图5⁃67a、b所示的脱模板与推杆固定连接,以防止脱模板在推出过程中脱落;其余几种为无固定连接形式,但必须严格控制推出距离,并要求导柱有足够长度保证脱模板不脱落。另外,图5⁃67a是应用最广的形式;图5⁃67b所示的脱模板镶入模板中,又称环状脱模板,结构紧凑;图5⁃67c适用于两侧带有顶出杆的注塑机;图5⁃67d用定距螺钉的头部顶脱模板,另一端与推出板直接相连,省去推杆固定板;图5⁃67e所示的推出机构的导向借助动模、定模的导柱。脱模板与型芯之间的配合为间隙配合,如H7/f6。
2)脱模板厚度的计算。
①对圆筒形塑件,其脱模板一般采用同心圆周分布的数根推杆推动,如图5⁃68a所示,若按刚度计算,则为

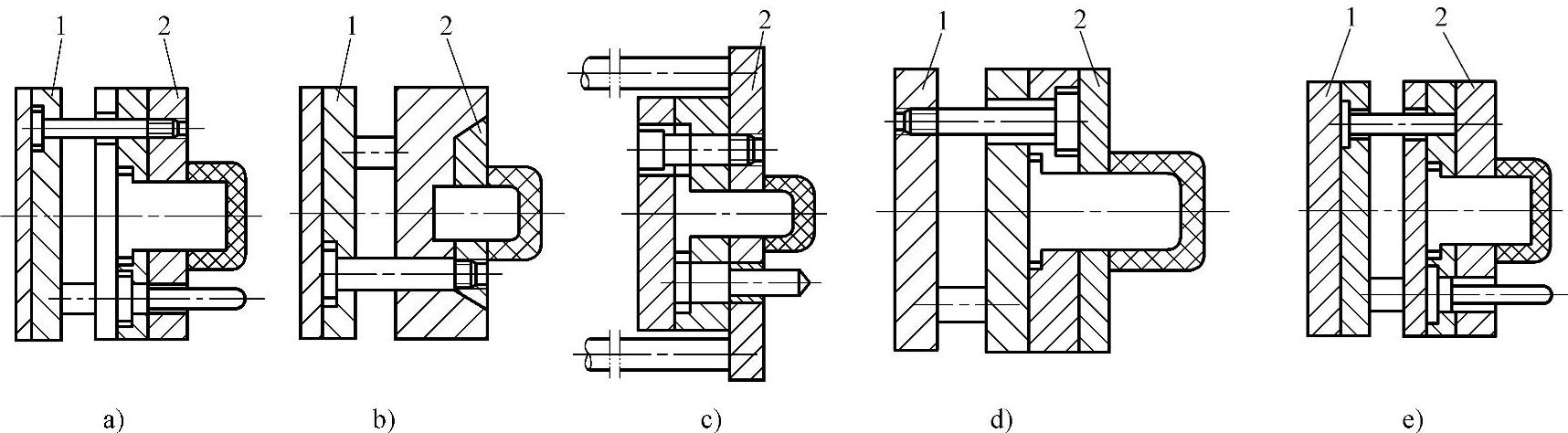
图5⁃67 脱模板脱模结构形式
1—顶出板(推板) 2—脱模板
若按强度计算,则为

式中 H——脱模板厚度(mm);
F脱——脱模力(N);
R——推杆轴线到脱模板中心距离(mm);
k1、k2——与R/r相关的系数,按表5⁃9选取,其中r为脱模板环形内孔(或型芯)半径;
E——钢材的弹性模量(MPa);
[δ]——脱模板中心允许的最大变形量(mm),一般取塑件在推出方向上尺寸公差的1/10~1/5;
[σ]——钢材的许用应力(MPa)。
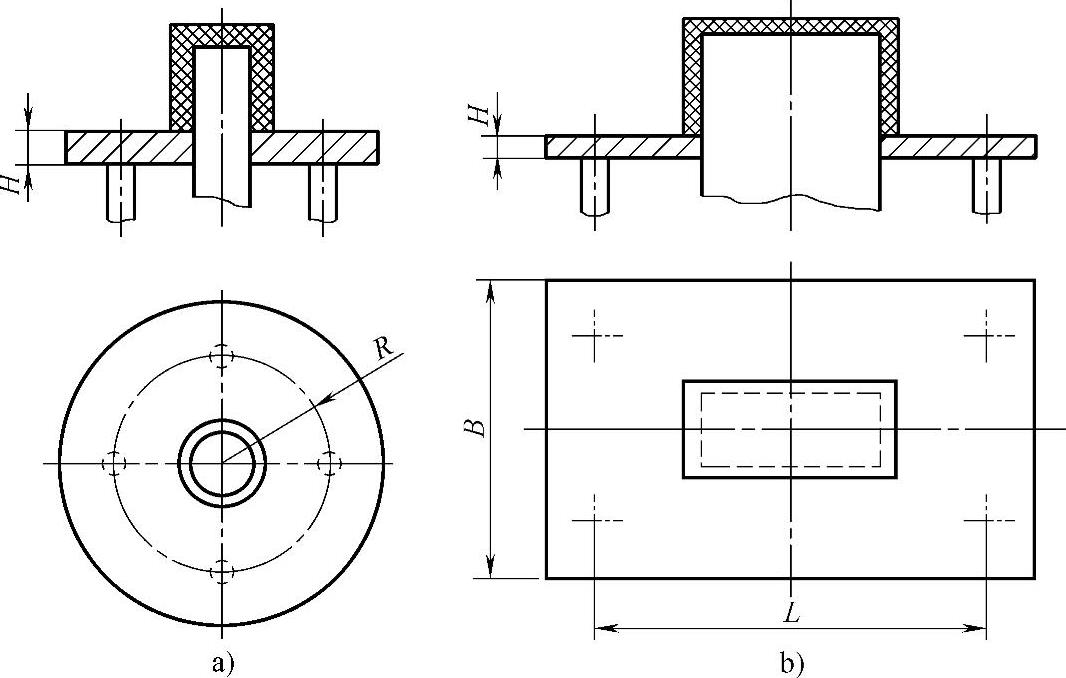
图5⁃68 脱模板厚度计算关系图
1—圆筒形盆件 2—矩形塑件
表5⁃9 圆环形平板系数k1、k2推荐值

②对矩形或异环形截面塑件,其脱模板所用推杆分布如图5⁃68b所示,若按刚度计算,则

式中 B——脱模板的宽度(mm)。
(4)推块脱模机构 推块是推管的一种特殊形式,用于推出非圆形的大面积塑件,其结构如图5⁃69所示。图5⁃69a所示为无复位杆,推块的复位靠主流道中的熔体压力来实现。图5⁃69b所示为中复位杆在推块的台肩上,结构简单紧凑,但与图5⁃69a一样,在推出塑件时,型腔3与推块1的移动空间应足以使推块推出塑件。图5⁃69c所示为采用非台阶推块推出塑件时,推块1不得脱离型腔3的配合面,复位杆2带动推杆4使推块1复位。
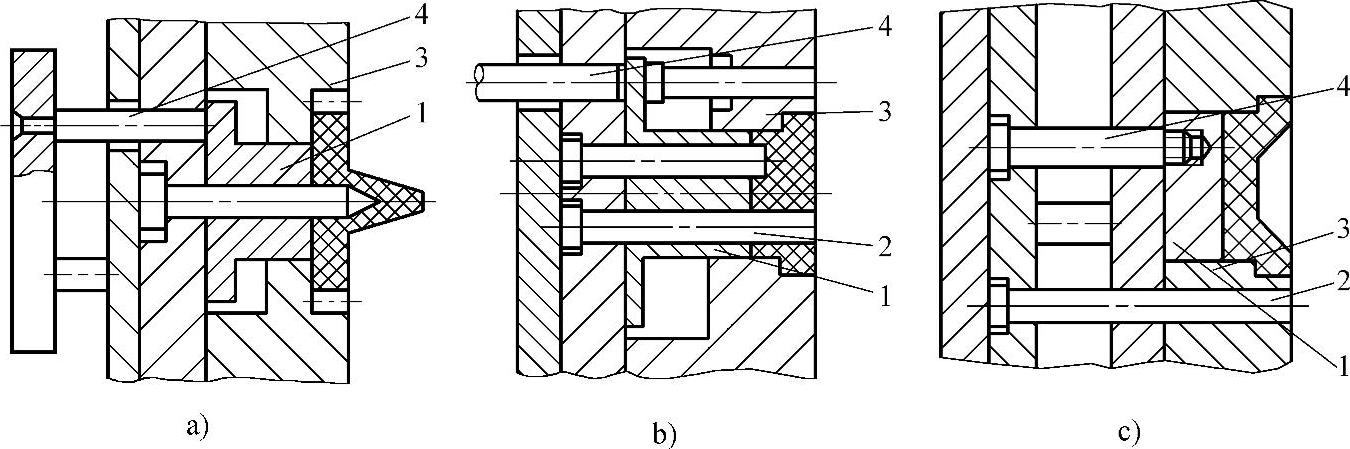
图5⁃69 推块脱模机构
1—推块 2—复位杆 3—型腔 4—推杆
推块与型腔间的间隙配合为H7/f6,推块材料用T8,并经淬火后硬度为53~55HRC或45钢经调质后硬度为235HBW。
(5)利用成型零件的脱模机构 有些塑件由于结构形状和所用塑料的缘故,不能采用上述各种脱模机构。这时,可利用成型镶件或型腔作为推出零件来脱模,如图5⁃70所示。图5⁃70a所示是利用推杆推出螺纹型芯。图5⁃70b推杆推出的是螺纹型环,经人工取塑件后将型环放入模内,为便于型环安放,推杆采用弹簧复位。图5⁃70c所示是利用活动镶块将塑件推出,然后人工取塑件。图5⁃70d将镶块固定于推杆上,脱模时,镶块不与模体分离,用人工取出塑件后由推杆带动镶件复位。图5⁃70e所示是利用型腔带出塑件的推出机构,开模时,型腔将塑件脱离型芯后,用人工将塑件从型腔中取出。这种结构适用于软质塑件,但型腔数目不宜过多,否则取件困难。
(6)多元联合脱模机构 对于深腔壳体、薄壁、局部有管状、凸肋、凸台及金属嵌件的复杂塑件,多采用两种或两种以上的简单脱模机构联合推出,以防止塑件脱模时变形。图5⁃71所示为二元联合脱模机构,图5⁃72所示为四元联合脱模机构,即推杆、推管、脱模板和活动镶块并用的形式。
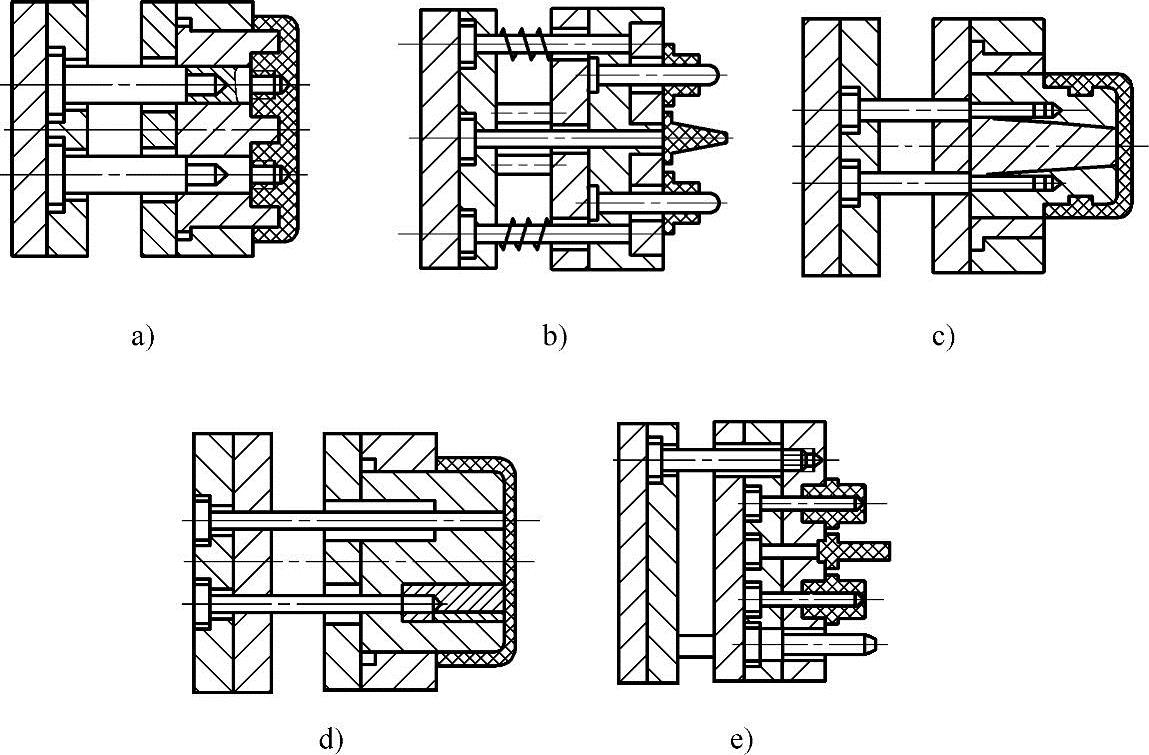
图5⁃70 利用成型零件推出的脱模机构
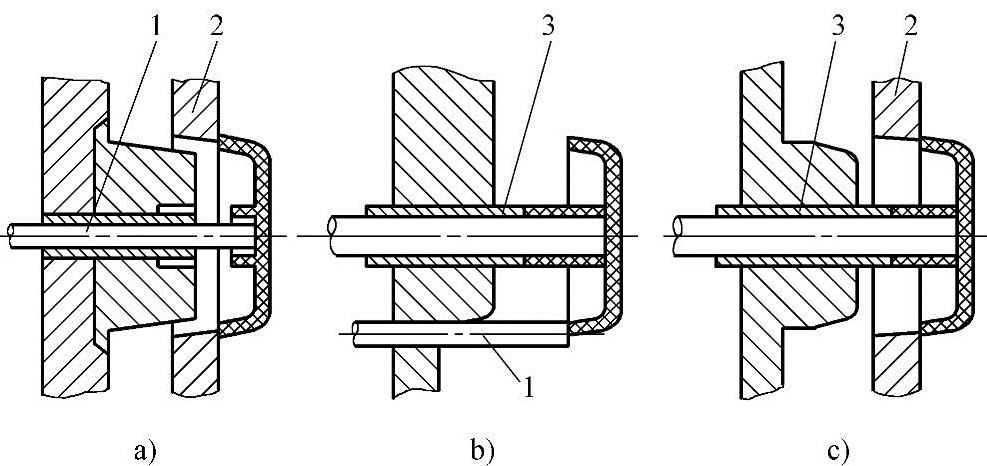
图5⁃71 二元联合脱模机构
1—推杆 2—脱模板 3—推管
(7)气动脱模机构 气动脱模机构是在凸模(型芯)上设置压缩空气推出阀门,在型芯与塑件之间通入0.5~0.6MPa的压缩空气使塑件脱模。它特别适用于深腔薄壁类容器,尤其是软质塑料的脱模。其结构形式如图5⁃73所示。
5.二次脱模机构
一般的塑件,其推出动作都是一次完成的。但某些特殊形状的制件,一次推出动作难以将制件从型腔中推出或者制件不能自动脱落,这时就必须再增加一次推出动作才能使制件脱落。例如,采用脱模板推出制件时,若在脱模板上加工有制件的成型部分,制件会附着在脱模板上,仍难以脱出,这时必须采用推杆作第二次推出,使其完全脱离脱模板。
二次脱模机构的种类很多,运动形式也很巧妙,但都应该遵循一个共同点,即两次推出的行程一般都有一定的差值,行程大与行程小者既可以同时动作也可以滞后动作。同时动作时,要求行程小者提前停止动作。若不同时动作时,要求行程大者的零件滞后运动。下面介绍几种实现二次脱模的推出机构。
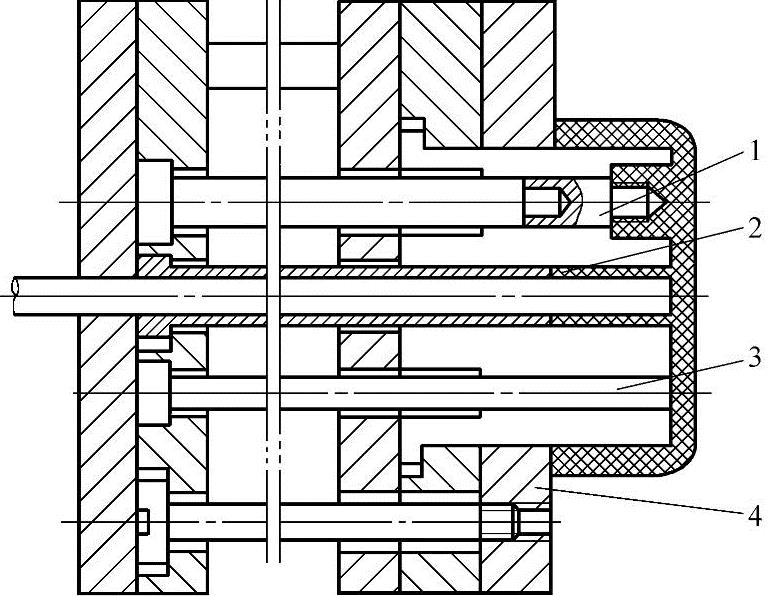
图5⁃72 四元件联合脱模机构
1—螺纹型芯 2—推管 3—推杆 4—脱模板
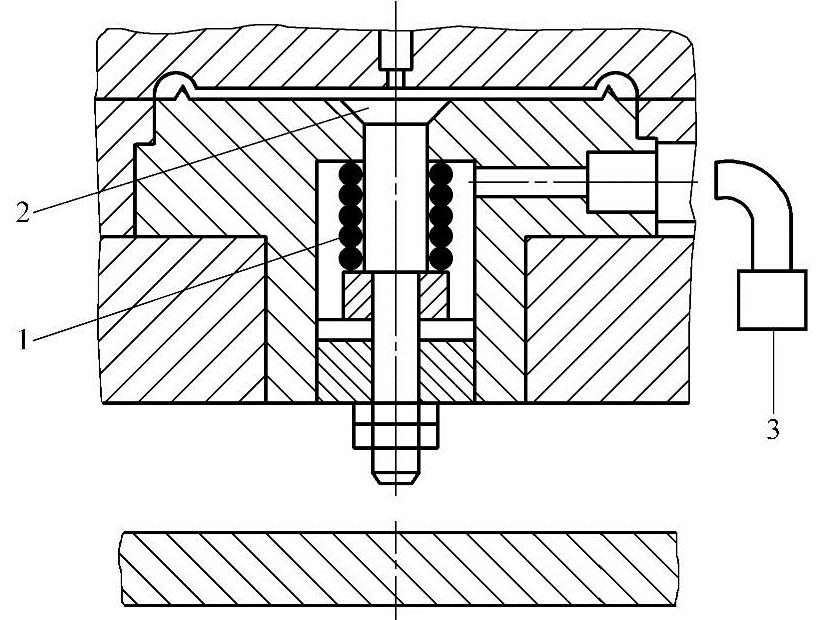
图5⁃73 气动脱模装置
1—弹簧 2—阀杆 3—压缩空气
(1)气动或液压二次脱模机构 图5⁃74a所示是气动二次脱模机构示意图。该机构的动作原理是,先由推杆推动脱模板(即型腔板)完成第一次脱模动作,使塑件脱离型芯。此后打开气阀,压缩空气从喷嘴喷出,将塑件从型腔板(即脱模板)中吹出,完成第二次脱模。图5⁃74b所示是液压式脱模机构示意图,第一次推出动作由液压缸完成,第二次推出动作依靠机械推出系统完成。
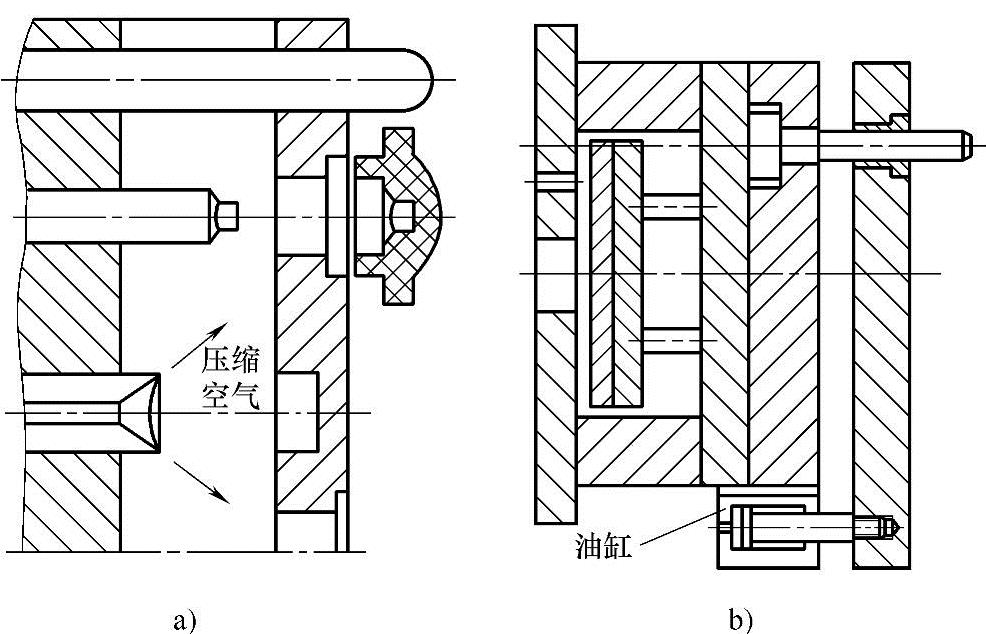
图5⁃74 气动、液压式二次脱模机构
(2)单推板二次脱模机构 单推板二次脱模机构的特点是仅有一套推出装置,但需完成两次脱模动作。第一次推出往往由开模动作带动拉杆、摆杆、滑块或弹簧等零件实现。这里只介绍常用的几种形式。
1)弹簧式单推板二次脱模机构。如图5⁃75所示,由弹簧4推动型腔板(或脱模板)2,使塑件离开型芯1一段距离l1,完成第一次脱模。再由推杆3前进一段距离l2,使塑件脱离型腔板(即脱模板)2和型芯,完成塑件自动脱落的第二次脱模动作。
2)拉杆式二次脱模机构。如图5⁃76所示,当模具从A—A打开一段距离后,拉杆3拉住脱模板(即型腔板)4,开始一次顶出。当动模继续移动时,模具从B—B分开,使塑件开始脱离型芯。当固定在型芯固定板上的凸块1接触凸轮拉杆上的长销2时,随拉杆的转动而脱离脱模板4,完成了一次脱模动作,即使塑件脱去型芯,但仍留在脱模板(型腔板)上。动模继续移动时,由推出机构(推杆)完成第二次脱模动作,即将塑件与型腔板(脱模板)分离。弹簧6的作用是使拉杆复位。
3)摆块拉板式二次脱模机构。如图5⁃77所示为摆块拉板式二次脱模机构。其中,图5⁃77a所示为合模状态,摆块5固定在动模固定板上。图5⁃77b所示为当开模到一定距离时,固定在定模板上的拉板7迫使摆块5推动型腔板1前进,完成第一次顶出。图5⁃77c所示为继续开模时,由于限位螺钉2的作用,阻止了型腔板1继续向前移动,当推出系统与注射机顶杆4相碰时,通过推杆3将塑件从型腔中推出,完成第二次推出。弹簧6的作用是使摆块会始终靠紧型腔。
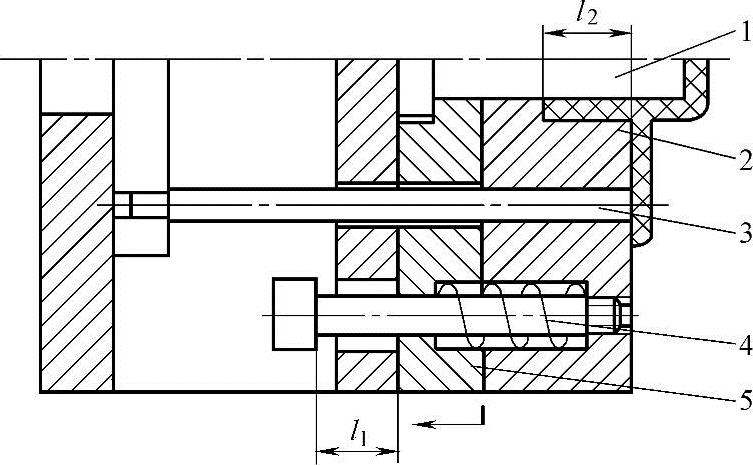
图5⁃75 弹簧式二次脱模机构
1—型芯 2—型腔板(脱模板) 3—推杆 4—弹簧 5—型芯固定板
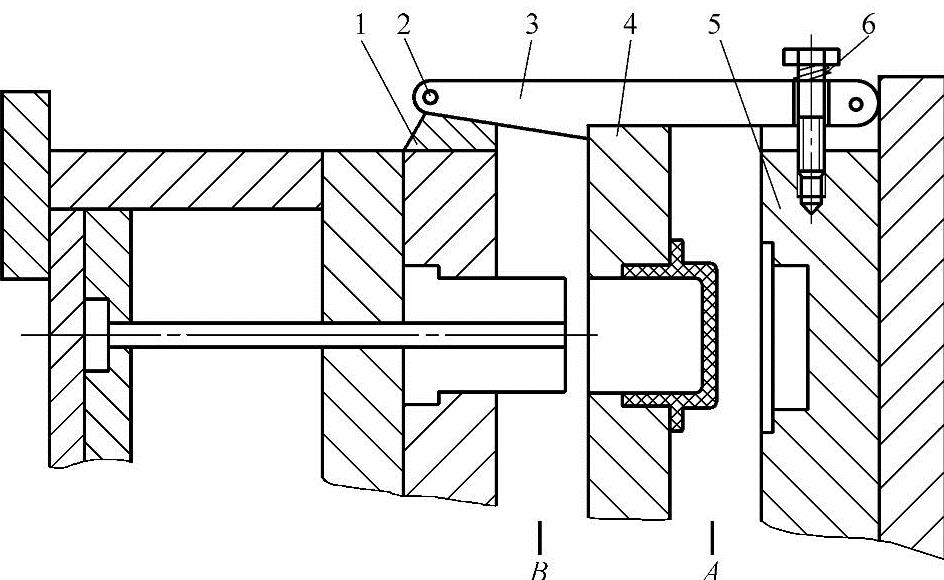
图5⁃76 拉杆式二次脱模机构
1—凸块 2—长销 3—凸轮拉杆 4—型腔板(脱模板) 5—凹模板 6—弹簧
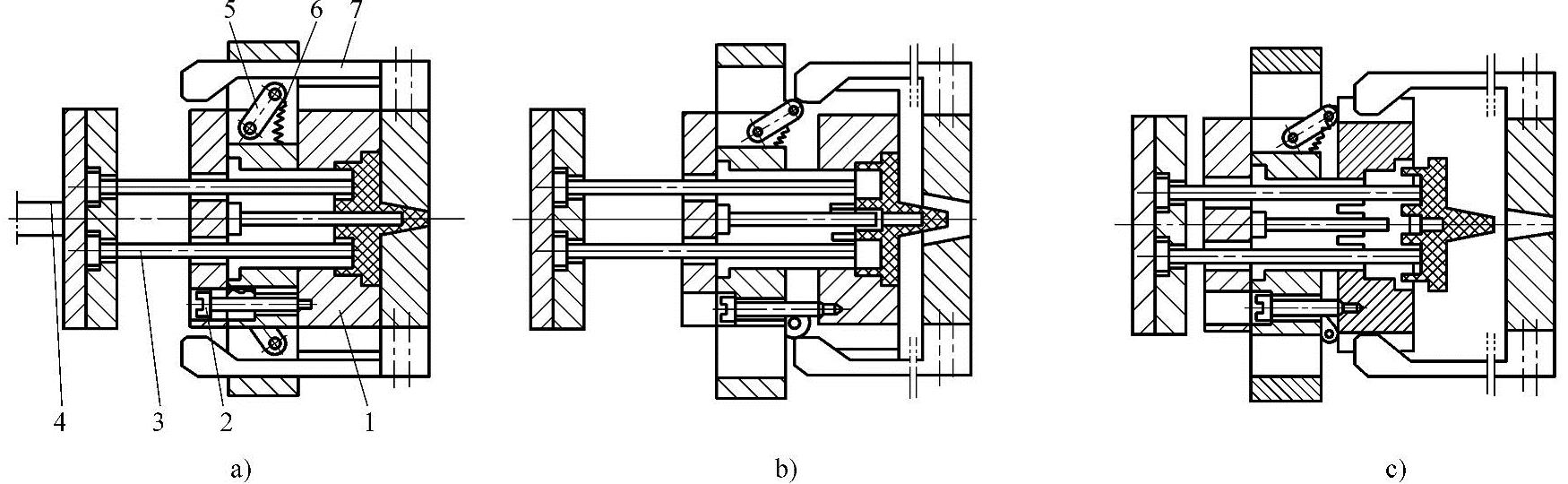
图5⁃77 摆块拉板式二次脱模机构
1—型腔板 2—限位钉 3—推杆 4—注射机顶杆 5—摆块 6—弹簧 7—拉板
4)U形限制架式二次脱模机构。图5⁃78所示为U形限制架式二次脱模机构。其中,图5⁃78a所示为闭模状态,U形限制架4固定在动模座板上,摆杆3固定在推出板上,可由转动销6转动,圆柱销1装在型腔板10上。图5⁃78b所示为当注射机顶杆5推动推板时,摆杆受U形架的限制只能向前运动,推动圆柱销1,使型腔板10和推杆7同时作用,使塑件脱离型芯8,完成第一次推出动作。图5⁃78c所示为摆杆3脱离限制架,限位螺钉9阻止型腔板10继续向前运动,此时圆柱销1将两个摆杆分开,弹簧2拉住摆杆紧靠在圆柱销1上,当注射机顶杆继续顶出时,推杆7则推动塑件脱离型腔板10,完成第二次动作。
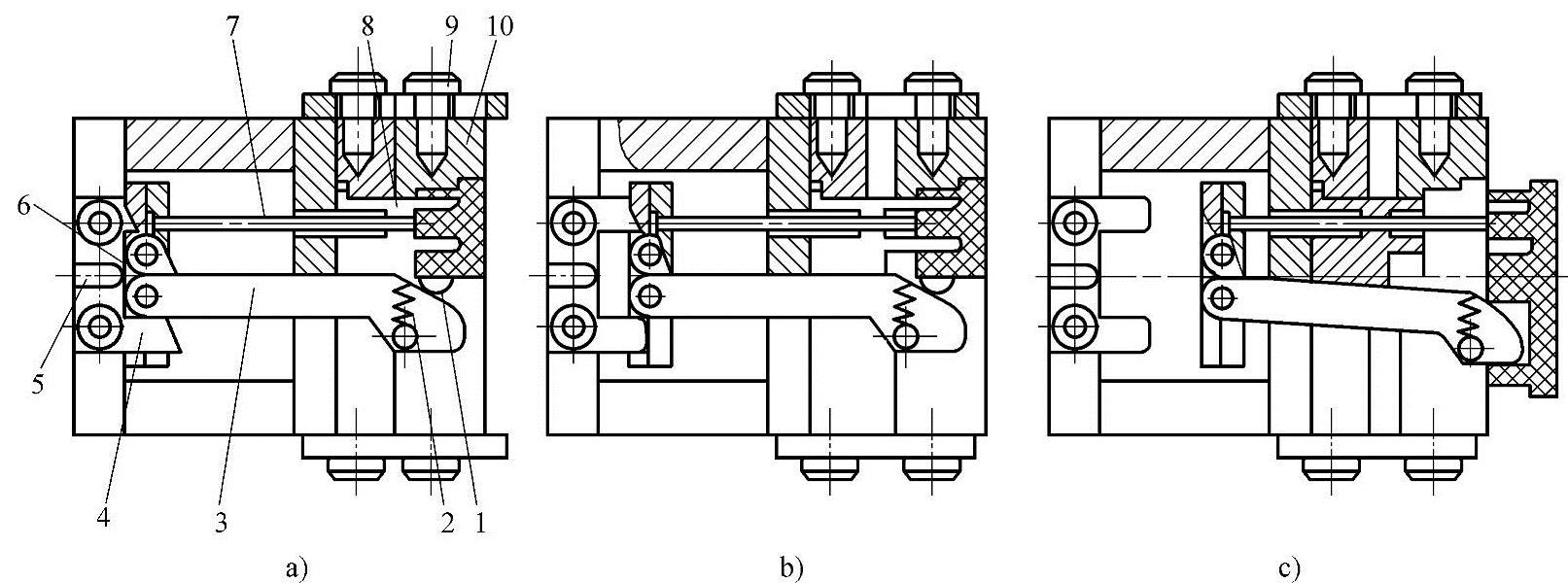
图5⁃78 U形限制架式二次脱模机构
1—圆柱销 2—弹簧 3—摆杆 4—U形限制架 5—注射机顶杆 6—转动销 7—推杆 8—型芯 9—限位螺钉 10—型腔板
5)滑块式二次脱模机构。图5⁃79所示为通过斜导柱和滑块实现二次脱模。其中,图5⁃79a所示为闭模状态,当注射机顶杆推动推出板时,中心推杆2与脱模板3一起运动,使塑件脱离型芯1。与此同时,滑块7在斜导柱6的作用下向中心方向移动,图5⁃79b所示。再继续运动时,迫使中心推杆2沿滑块的斜面上升的高度大于脱模板的移动高度,塑件则脱离脱模板,如图5⁃79c所示,完成第二次脱模。
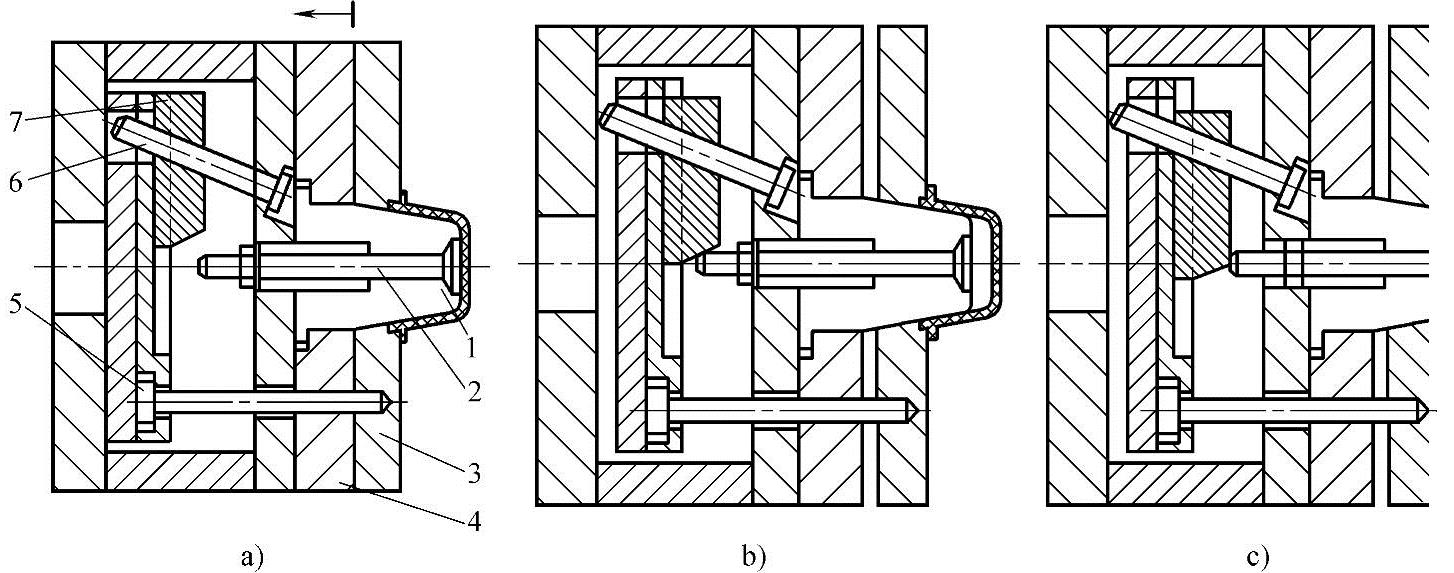
图5⁃79 斜导柱⁃滑块二次脱模机构
1—型芯 2—中心推杆 3—脱模板(型腔板) 4—动模板 5—推杆 6—斜导柱 7—滑块
图5⁃80所示是通过滑块实现二次脱模的另一种结构形式,滑块9的移动是靠固定在支承板上的楔形块10实现的。开模时,推杆11带动脱模板1和中心推杆6一起运动,使塑件脱去型芯2,这时滑块9与斜楔10接触,斜楔的斜面迫使滑块9向中心移动,直至脱模板上的推杆11落入滑块9的孔中,因此脱模板1停止运动,而中心推杆6仍继续向前,将塑件从脱模板(型腔板)1中推出。合模时,复位杆5使推出板8后退,当推杆11离开滑块孔时,弹簧将滑块9推回原位。
6)摆块式二次脱模机构。摆块式二次脱模机构如图5⁃81所示,推出时,推杆4、推杆2推动型腔板1和制件一起移动,使制件脱离型芯3,完成第一次顶出。此时压杆5与支承板7接触。继续顶出时,推杆4推动型腔板1继续移动,同时由于压杆5迫使摆块6摆动,推杆2则超前于型腔板1的运动,将制件从型腔板1中顶出。
7)钢球式二次脱模机构。图5⁃82所示为钢球式二次脱模机构,一次脱模靠推出系统推动脱模板3,使塑件脱离型芯,此时塑件仍有一部分留在脱模板3内,因此设置特殊结构的推杆5实现第二次脱模。内套筒9与脱模板用卡紧圈连在一起,一次脱模时,钢球卧在内套筒与推杆5之间,推杆一运动,则带动内套筒与脱模板3,实现一次脱模,使塑件脱离型芯2。当钢球移到外套筒的凹槽时,钢球被挤到内外套筒之间,使内套筒不随推杆5运动,即脱模板停止运动,这时推杆1将塑件推出脱模板。
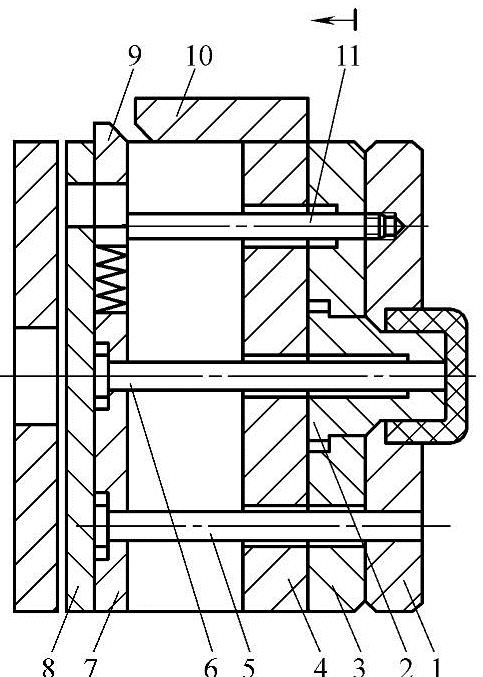
图5⁃80 滑块式二次脱模机构
1—脱模板(型腔板) 2—型芯 3—型芯固定板 4—支承板 5—复位杆 6—中心推杆 7—推杆固定板 8—推板 9—滑块 10—斜楔 11—推杆
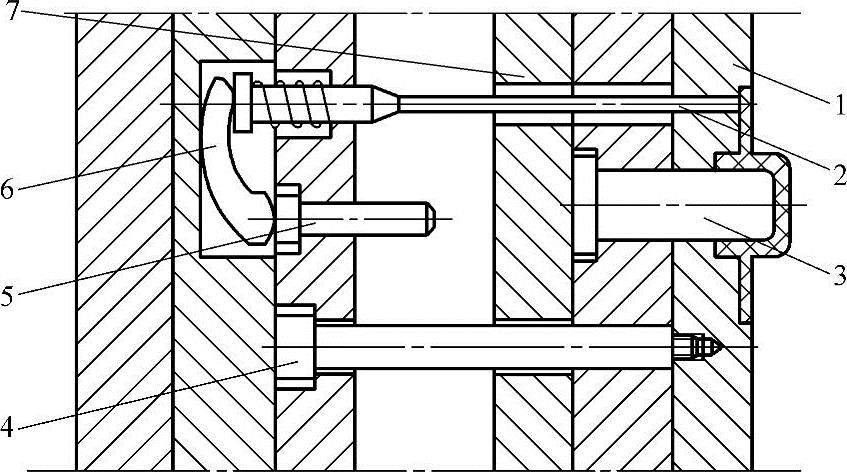
图5⁃81 摆块式二次脱模机构
1—脱模板(型腔板) 2—推杆 3—型芯 4—推杆 5—压杆 6—摆块 7—支承板
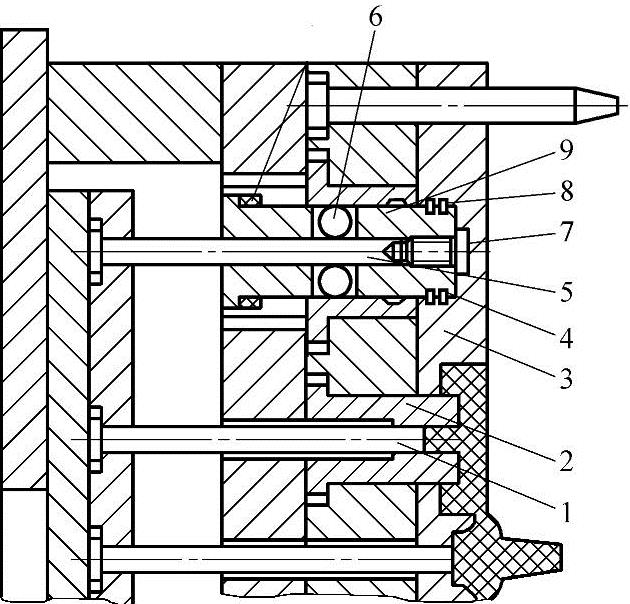
图5⁃82 钢球式二次脱模机构
1—推杆 2—型芯 3—脱模板 4—卡紧圈 5—推杆 6—钢球 7—盖子 8—聚氨酯垫圈 9—内套筒
(3)双推板二次脱模机构 此类脱模机构具有两套推出装置,并利用其先后动作完成二次脱模,常见的有以下三种形式。
1)八字形摆杆式二次脱模机构。图5⁃83所示八字形摆杆式二次脱模机构,型腔推杆2固定在一次推板上,推动塑件用的中心推杆3固定在二次推板上,在一次推板与二次推板之间有定距块5,它固定在一次推板上。开模时,注射机顶杆6推动一次推板,通过定距块使二次推板以同样的速度推动塑件和型腔1脱离动模型芯10,完成第一次推出动作。当运动到图5⁃83b所示位置时,一次推板接触到八字形摆杆4,由于摆杆与一次推出板接触点比二次推板接触点距支点的距离小,使二次推板向前移动的距离大于一次推板向前移动的距离,因而将塑件从型腔1中脱去,完成第二次脱模动作,如图5⁃83c所示。
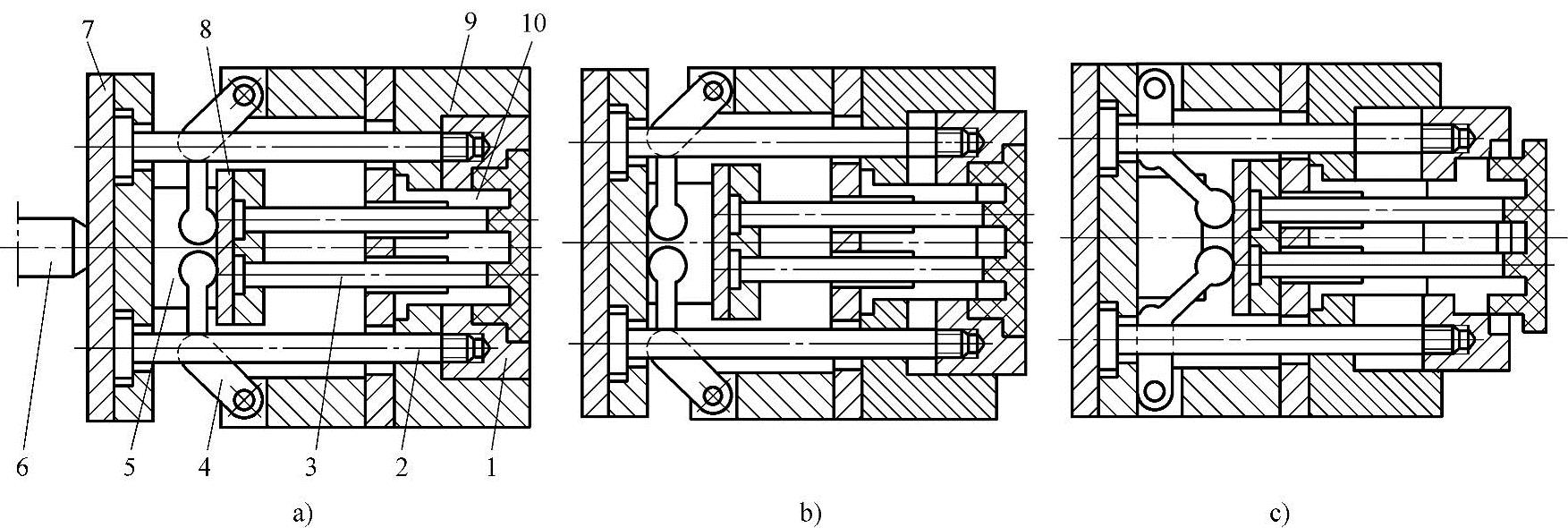
图5⁃83 八字形摆杆式二次脱模机构
1—型腔 2—型腔推杆 3—中心推杆 4—八字形摆杆 5—定距块 6—注射机顶杆 7—一次推板 8—二次推板 9—动模固定板 10—型芯
2)楔块摆钩式二次脱模机构。图5⁃84所示楔块摆钩式二次脱模机构,塑件为薄壁且内腔有台阶和孔。该机构的特点是兼作型芯的成型推杆7固定在一次推板9上,中心推杆6固定在二次推板10上,同时在二次推板10上还固定有摆钩1,一次推板9上固定有被摆钩拉住的圆柱销5,在合模状态下由于拉簧2的作用,摆钩始终钩住圆柱销,如图5⁃84a所示。开模时,注射机顶杆8推动二次推板,由于摆钩1的作用,一次推板、二次推板同时推动塑件使其脱离型芯,完成第一次推出动作。继续运动时由于斜楔3的作用伸长拉簧2,使摆钩脱离圆柱销,此时固定在一次推板9上的限距柱4与动模固定板接触而使一次推板9停止前进,如图5⁃84b所示。当注射机顶杆8继续推动二次推板10时,中心推杆6则推动塑件脱离成型推杆7,完成第二次推出,如图5⁃84c所示。
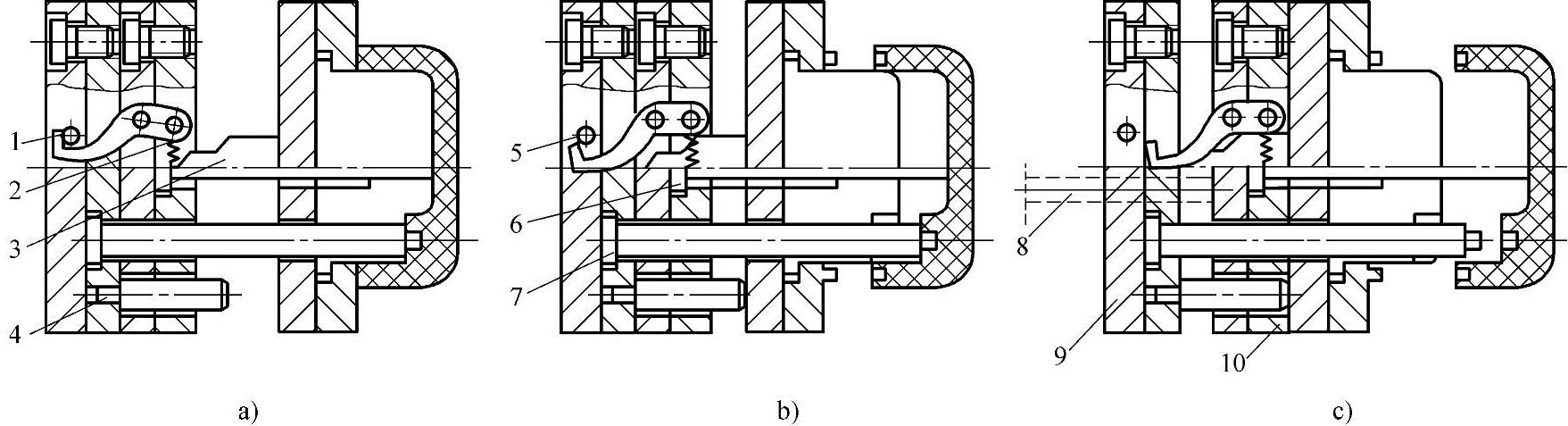
图5⁃84 楔块摆钩式二次脱模机构(一)
1—摆钩 2—拉簧 3—斜楔 4—限距柱 5—圆柱销 6—中心推杆 7—成型推杆 8—注射机顶杆 9—一次推板 10—二次推板
图5⁃85是楔块摆钩式的另一种形式。推动型腔板(脱模板)1的推杆2固定在一次推板4上,中心推杆8固定在二次推板3上,摆钩6连接在一次推板上,可以绕轴转动。开模时注射机顶杆推动二次推板,由于弹簧5拉住摆钩使一次推板随之运动,使塑件脱离型芯,完成一次脱出动作。再继续运动时,摆钩6接触到动模固定板7的斜面,迫使摆钩转动而脱离二次推板,因此一次推板停止运动,在中心推杆8的作用下,塑件脱离型腔板1,完成第二次脱出动作。
6.双脱模机构
由于塑件结构或形状特殊,开模时塑件滞留于动模、定模不确定的情况下,应考虑动模和定模两侧都设置脱模机构,故称为双(向)脱模机构。图5⁃86所示为常见的双脱模机构。图5⁃86a所示的定模采用弹簧推出,动模采用脱模板推出。这种形式结构紧凑、简单,适用于在定模上所需推出力不大,推出距离不长的塑件,但弹簧容易失效。图5⁃86b所示是杠杆式双脱模机构,利用杠杆的作用实现定模的脱模,开模时固定于动模上的滚轮压动杠杆,使定模推出装置动作,迫使塑件留在动模上,然后利用动模上的推出机构将塑件推出。
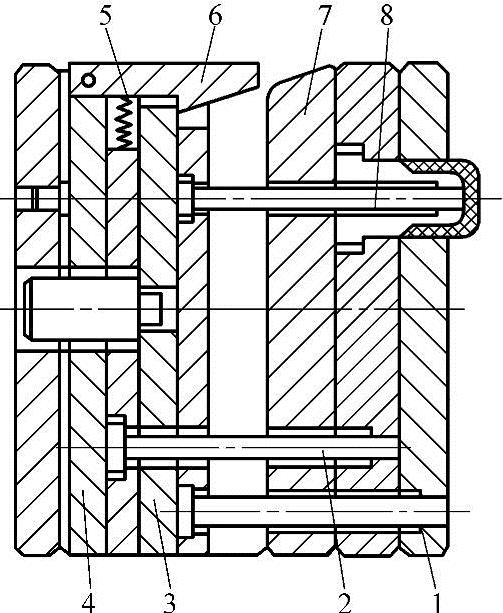
图5⁃85 楔块摆钩式二次脱模机构(二)
1—型腔板(脱模板) 2—推杆 3—二次推板 4—一次推板 5—弹簧 6—摆钩 7—动模固定板 8—中心推杆
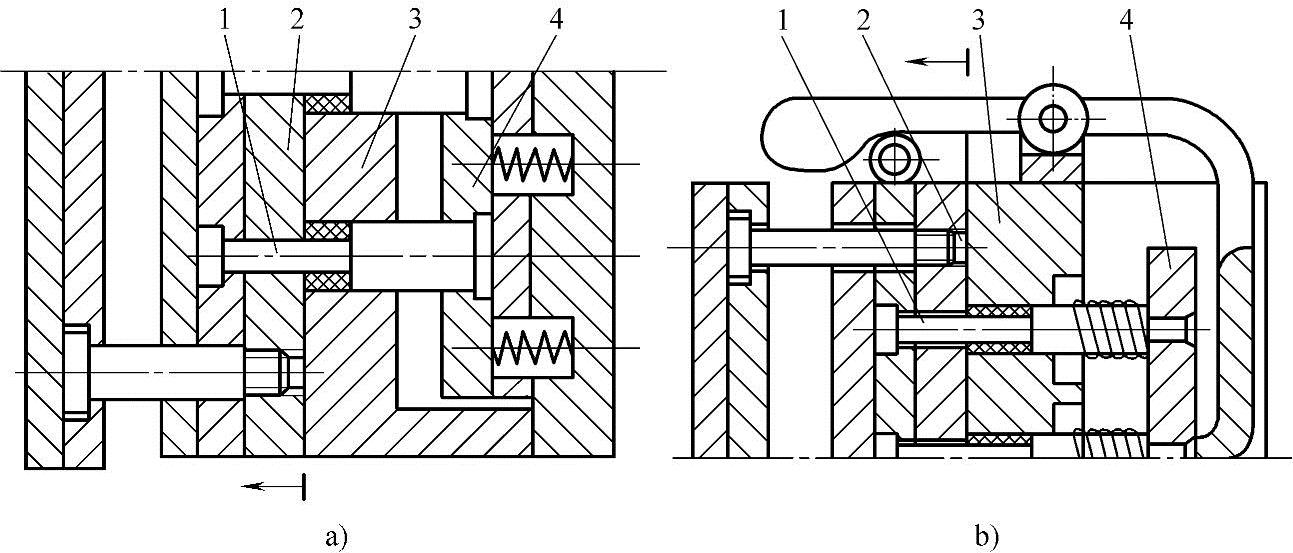
图5⁃86 动、定模双向脱模机构
a)弹簧式双脱模机构 b)杠杆式双脱模机构
1—型芯 2—脱模板 3—型腔板 4—定模推出板
图5⁃87所示是气动双脱模机构。在动模、定模两侧均有进气口与气阀,开模时,首先定模的电磁阀开启,使塑件脱离定模而留在动模型芯上,然后关闭定模电磁阀。开模终止时,打开动模电磁阀,将塑件吹离型芯。
7.顺序脱模机构
顺序脱模机构又称顺序分型机构,有该机构的模具又称双分型面模具,如图5⁃78~图5⁃81所示。由于塑件与模具结构的需要,首先需将定模型腔板与定模分开一定距离(即A—A分型)后,再使动模与定模型腔板分开(即B—B分型)取出塑件。
8.浇注系统凝料的脱出机构
一般来说,普通浇注系统多数是单分型面的二板模具,而点浇口、潜伏式浇口多是双分型面的三板模具。
(1)普通浇注系统凝料的脱出机构 通常采用侧浇口、直接浇口及盘环形浇口类型的模具,其浇注系统凝料一般与塑件连在一起。塑件脱出时,先用拉料杆拉住冷料穴,使浇注系统留在动模一侧,然后用推杆或拉料杆推出,靠其自重而脱落,如图5⁃75所示。
(2)点浇口式浇注系统凝料的脱出机构 点浇口浇注系统凝料,一般可用人工、机械手取出,但生产效率低,劳动强度大,为适应自动化生产的需要,可采取以下几种依靠模具结构而自动使浇注系统凝料脱落的方法。
1)利用推杆拉断点浇口凝料的脱出机构。如图5⁃88所示,开模时模具首先沿A—A面分开,流道凝料被带出定模座板8,当限位钉1对推板2限位后,推杆4及推杆5共同将浇注系统凝料推出。
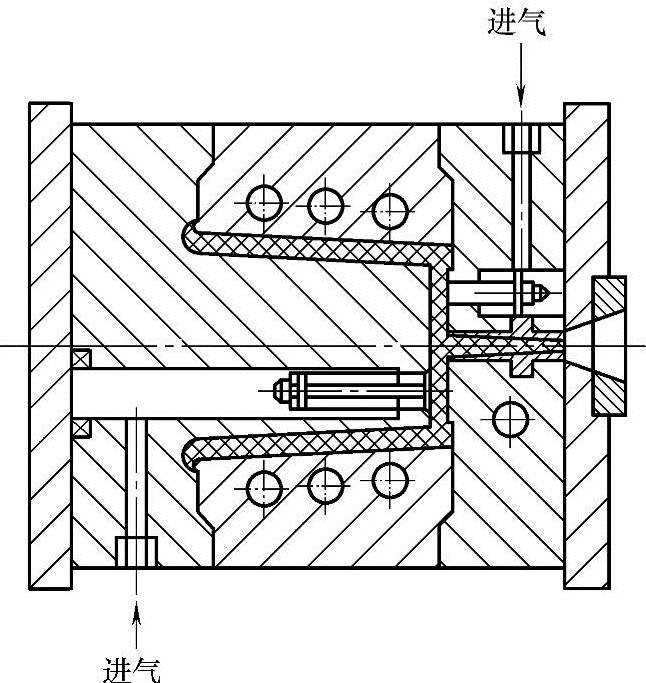
图5⁃87 气动双脱模机构
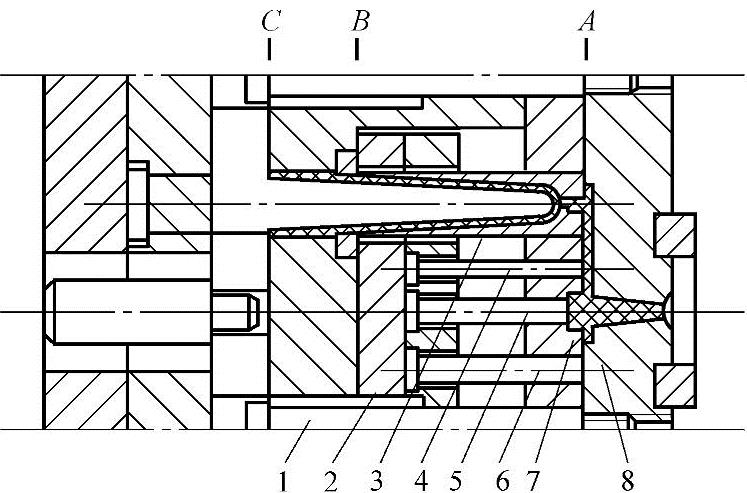
图5⁃88 利用推杆拉断点浇口的脱出机构
1—限位钉 2—推板 3—镶件 4、5—推杆 6—复位杆 7—流道板 8—定模座板
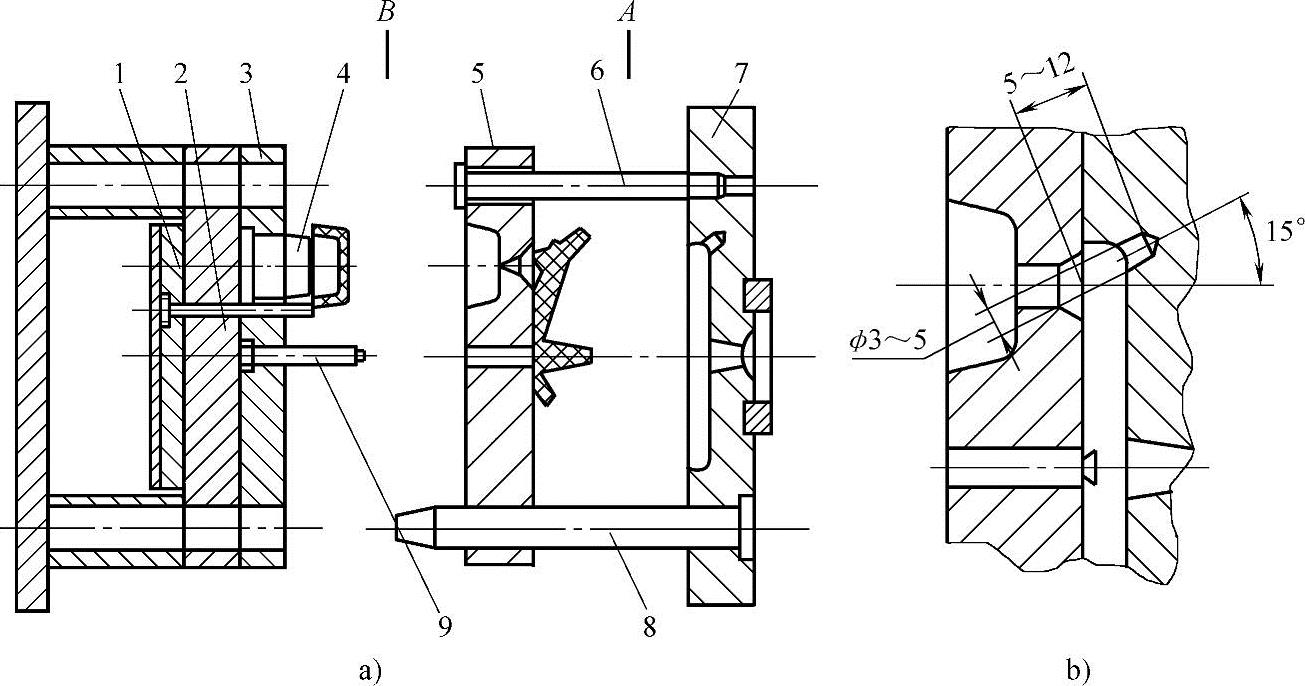
图5⁃89 利用侧凹拉断点浇口凝料的脱模机构(一)
1—顶出板 2—顶杆 3—动模固定板 4—型芯 5—型腔板 6—限位钉 7—定模板 8—导柱 9—拉料杆
2)利用侧凹拉断点浇口凝料的脱出机构。分流道末端钻一小斜孔,开模时确保模具先由A—A面分开,点浇口被拉断,流道凝料被中心拉料杆9拉向型腔板一侧。当限位钉6起作用后,动模与定模型腔板5分开,即B—B分型,中心拉料杆随之失去作用,流道凝料便自动脱落,如图5⁃89所示,侧凹部分的形状与尺寸如图5⁃89b所示。
图5⁃90所示为侧凹拉断点浇口的另一种形式,分流道末端做成斜面。开模时,由于弹簧6的作用,模具首先从A—A面分型,点浇口被拉断,同时拉料杆相对于型芯固定板1移动l距离。继续开模时,型芯固定板1碰到拉料杆2的台阶,拉料杆2则将主流道凝料脱出,随后型腔板(中间板)3将流道凝料从拉料杆2上推出并自动脱落。
3)利用拉料杆拉断点浇口凝料的脱出机构。图5⁃91所示为利用拉料杆拉断点浇口凝料的脱出机构。图5⁃91a所示为闭模状态,图5⁃91b所示为开模状态。开模时,首先从A—A面分型,由于流道拉料杆3的作用,浇口凝料断开后并留在定模一边。待分开一定距离后,限位钉2带动流道推板1沿B—B分开,并将浇注系统凝料脱掉。继续开模时,型腔板(中间板)5受到限位拉杆4的阻碍不能移动,即实现C—C分型,塑件随型芯移动而脱离型腔板5,最后在推杆7的作用下脱模板将塑件脱离型芯即D—D分开。
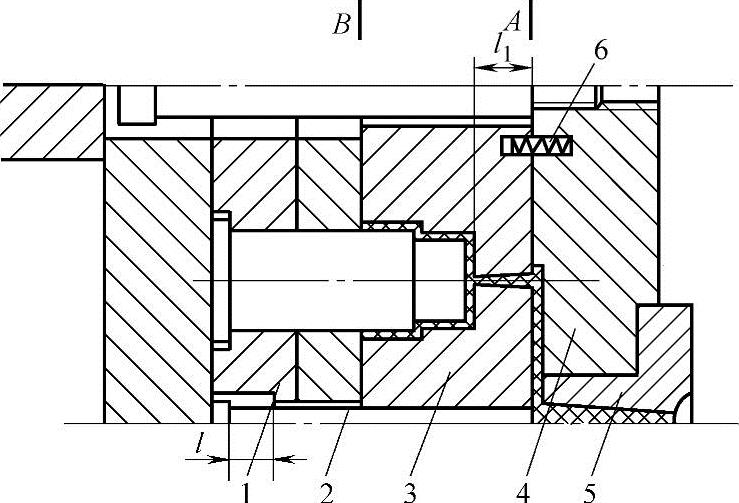
图5⁃90 利用侧凹拉断点浇口凝料的脱模机构(二)
1—型芯固定板 2—拉料杆 3—型腔板(中间板) 4—定模座板 5—浇口套 6—弹簧
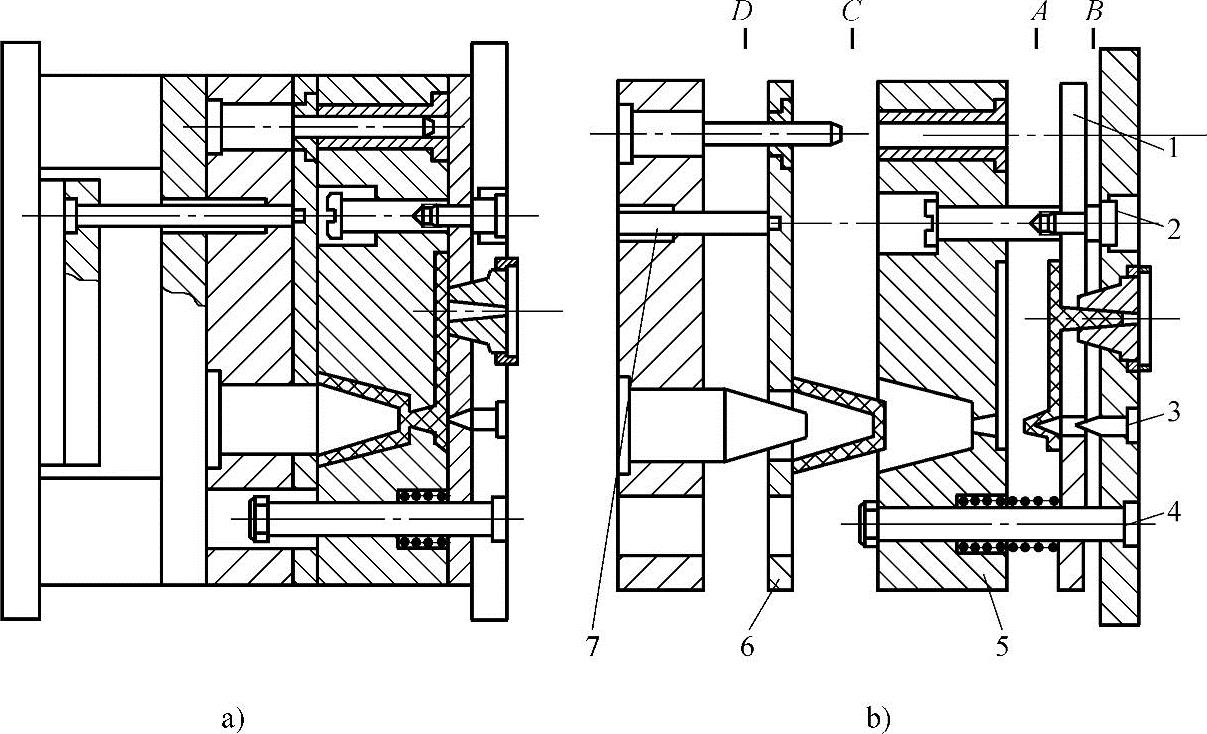
图5⁃91 利用拉料杆拉断点浇口凝料的脱出机构
a)闭模状态 b)开模状态
1—流道推板 2—限位钉 3—流道拉料杆 4—限位拉杆 5—型腔板(中间板) 6—脱模板 7—推杆
4)利用定模推板拉断点浇口凝料的脱出机构。图5⁃92所示为利用定模推板拉断点浇口凝料的脱出机构,在定模型腔板3内镶一个定模推板5,开模时由定距分型机构保证定模型腔板3与定模座板4首先沿A—A而分型,拉料杆2将主流道凝料从浇口套中拉出。当开模到l距离时,限位钉(拉杆)1带动定模推板5使主流道凝料与拉料杆脱离,即实现B—B分型,同时拉断点浇口,浇注系统凝料便自动脱落。最后沿C—C分型时,利用脱模板将塑件与型芯分离。
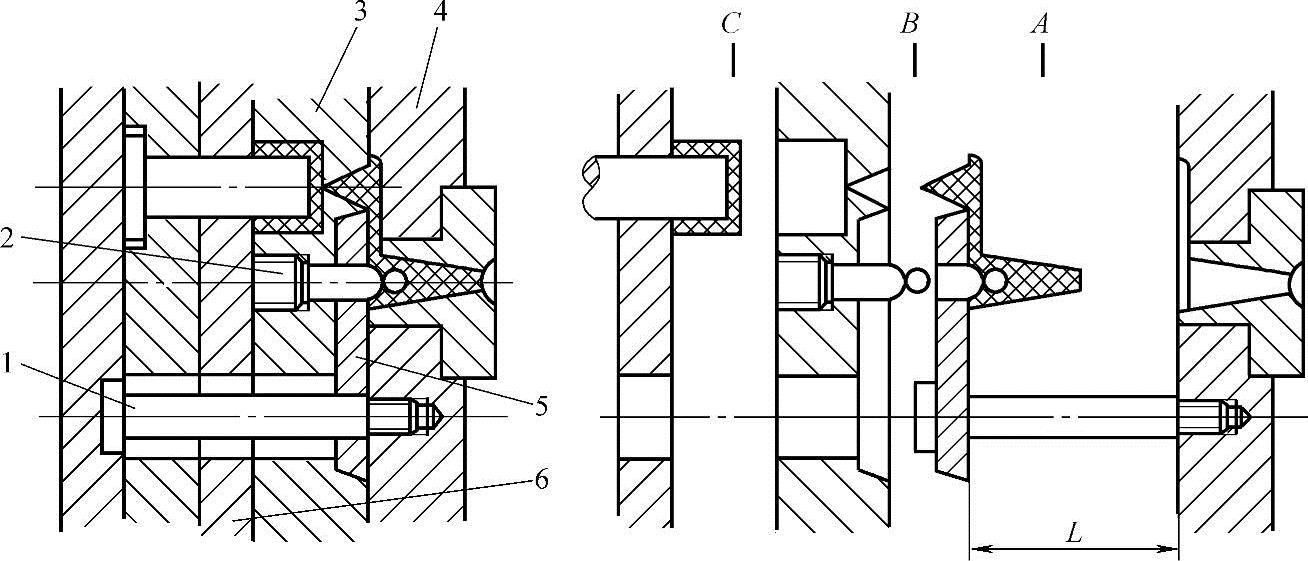
图5⁃92 利用定模推板拉断点浇口凝料的脱出机构
1—限位钉 2—拉料杆 3—定模型腔板(中间板) 4—定模座板 5—定模推板 6—脱模板
5)浮动拉杆式脱点浇口凝料的脱出机构。如图5⁃93所示,开模时,模具首先从A面分型,拉料杆3将主流道拉出浇口套,浮动拉杆4随之向左移动。随后,当拉料杆3的台阶与定模座板6相碰时,将点浇口拉断,并拉出型腔板(中间板)2。当限位钉1起作用后,模具沿B面分开,定模型腔板2将浇注系统凝料从拉料杆3上刮落,流道凝料便自动脱落。
6)杠杆式推料板拉断点浇口凝料的脱出机构。图5⁃94所示为杠杆式推料板拉断点浇口凝料的脱出机构,开模时,模具首先沿A—A面分型,将主流道凝料拉出定模座板3。继续开模,当拉钩9和杠杆7接触时,迫使推料板5拉断点浇口,并将流道凝料推离型腔板1,使之自动脱落。
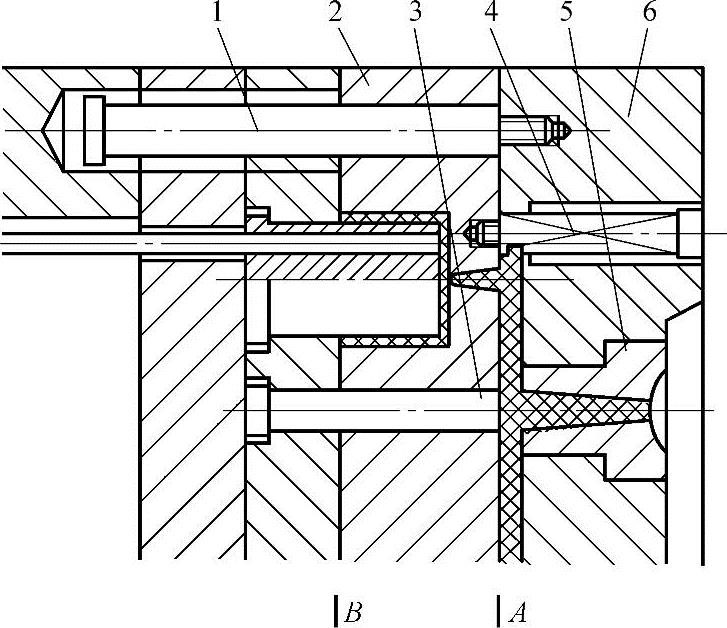
图5⁃93 浮动拉杆式脱点浇口凝料的脱出机构
1—限位钉 2—型腔板(中间板) 3—拉料杆 4—浮动拉杆 5—浇口套 6—定模座板
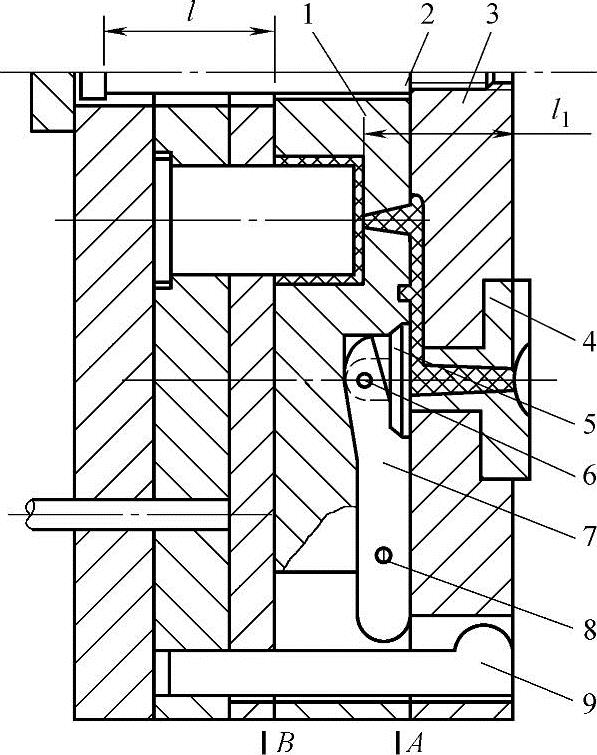
图5⁃94 杠杆式推料板拉断点浇口凝料的脱出机构(一)
1—型腔板(中间板) 2限位钉 3—定模座板 4—浇口套 5—推料板 6、8—轴 7—杠杆 9—拉钩
图5⁃95所示为推料板拉断点浇口的另一种形式。开模时,模具首先沿A—A面分开,主流道脱出浇口套。当限位钉4起限位作用时,模具沿B—B面分开,推料板3将浇点口拉断,并将凝料从型腔板1中拉出自动脱落。
(3)潜伏式浇口凝料的脱出机构 采用潜伏式浇口的模具,其脱模装置必须分别设置塑件和流道凝料的推出机构。在推出过程中,浇口被拉断,塑件与浇注系统凝料各自自动脱落。
1)利用推件板(脱模板)切断浇口凝料的脱出机构。图5⁃96所示为利用脱模板切断浇口凝料的脱出机构。其中,图5⁃96a所示为闭模状态,图5⁃96b所示为开模状态。浇口设在塑件内侧。开模时,定模座板1与脱模板3首先分开,塑件留在型芯2上。推出时,脱模板3首先移动并与型芯共同把浇口切断,然后推杆5将流道凝料推出而自动落下。
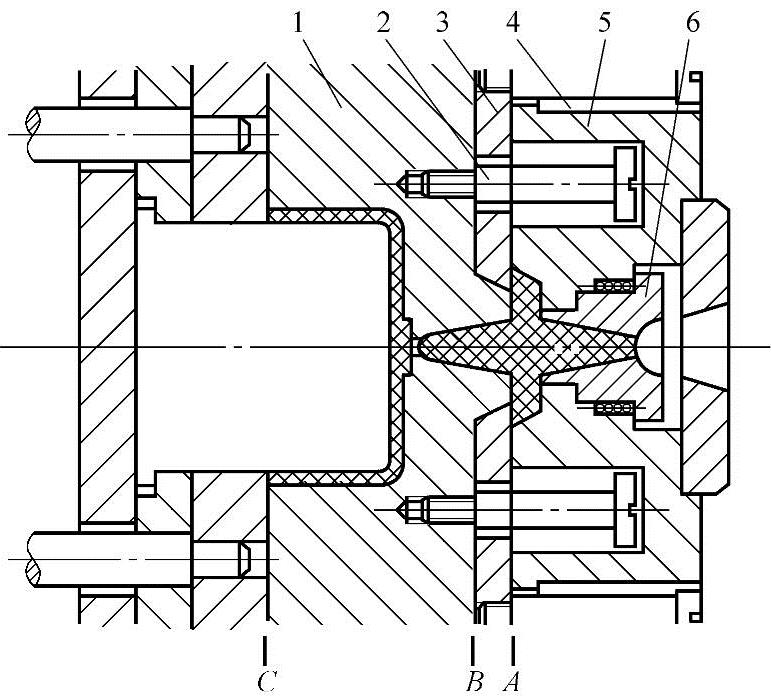
图5⁃95 杠杆式推料板拉断点浇口凝料的脱出机构(二)
1—型腔板(中间板) 2—限位钉 3—推料板 4—限位钉 5—定模座板 6—浇口套
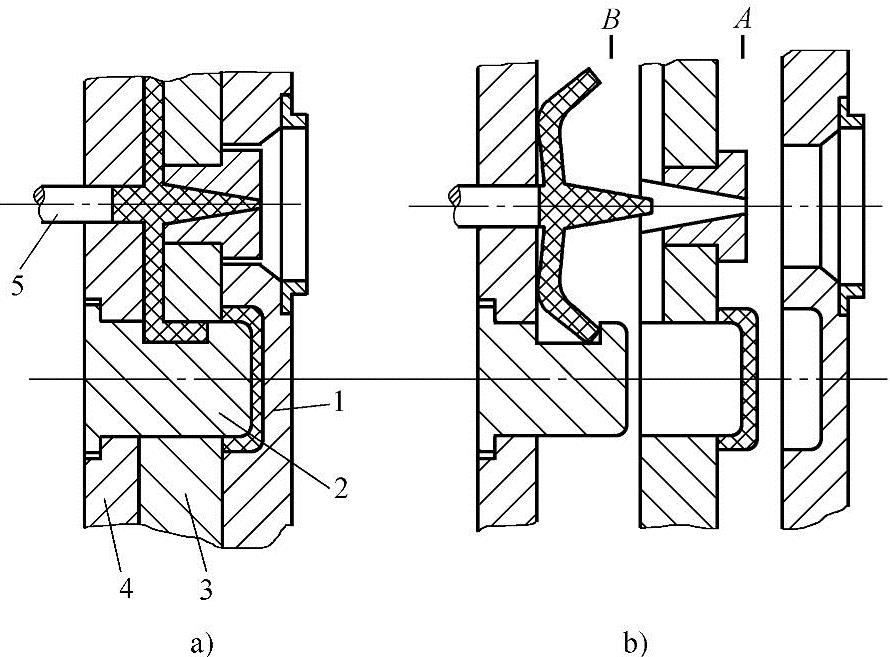
图5⁃96 内侧进料及脱模板切断浇口凝料的脱出机构
a)闭模状态 b)开模状态
1—定模座板 2—型芯 3—脱模板 4—型芯固定板 5—推杆
2)利用差动式推杆切断浇口凝料的脱出机构。图5⁃97所示为利用差动式推杆切断浇口凝料的脱出机构。其中,图5⁃97a所示为闭模状态,在脱模过程中,先由塑件推杆2推动塑件,将浇口切断而与塑件分离,如图5⁃97b所示。当推板移动l距离后,限位圈4即开始被推动,从而由流道推杆3推动流道凝料,最终塑件和流道凝料都被推出型腔,如图5⁃97c所示。
3)其他形式切断浇口凝料的脱出机构。图5⁃98和图5⁃99为其他类型脱潜伏式浇口凝料的脱出机构。推出过程中,流道推杆与塑件推杆分别推动浇口和制件,并使它们分离。最后,浇注系统凝料与制件分别被推出。
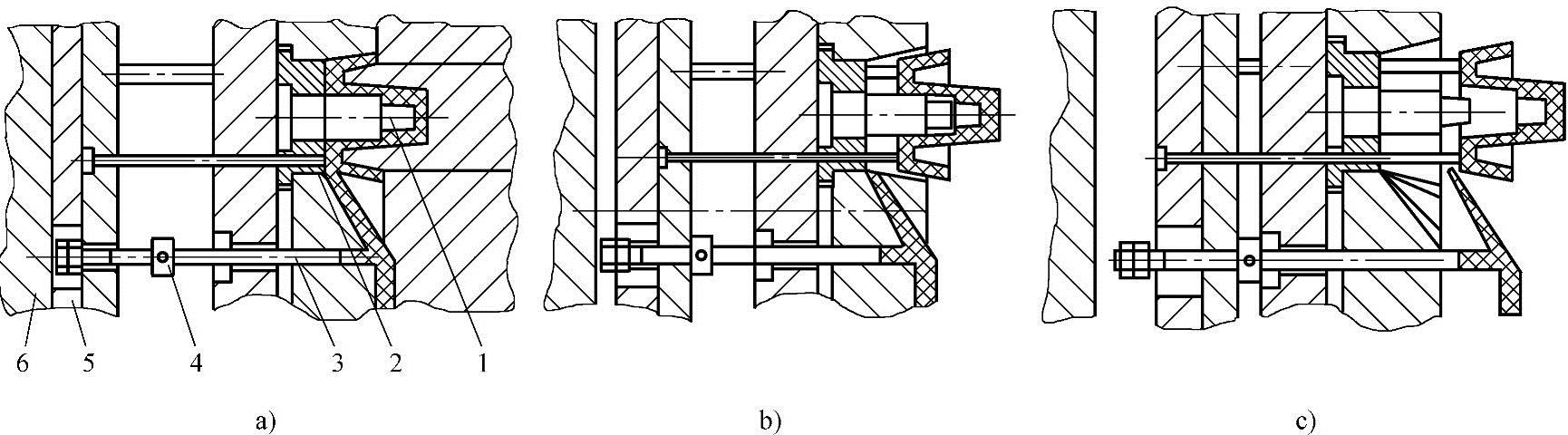
图5⁃97 利用差动式推杆切断浇口凝料的脱出机构
1—型芯 2—塑件推杆 3—流道推杆 4—限位圈 5—推板 6—动模座板
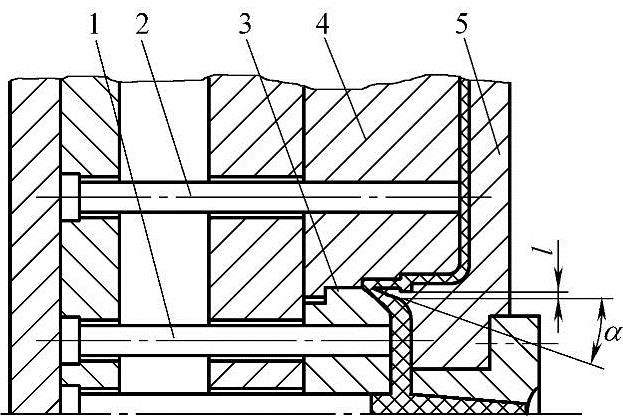
图5⁃98 潜伏式浇口凝料的自动脱出
1—流道推杆 2—制件推杆 3—动模 4—型芯 5—定模
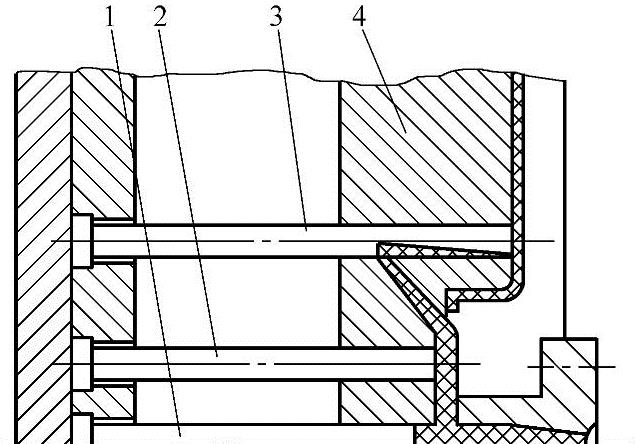
图5⁃99 推杆上开设潜伏式浇口凝料的脱出
1、2—流道推杆 3—制件推杆 4—动模
9.带螺纹塑件的脱模机构
塑件的内螺纹由螺纹型芯成型,外螺纹由螺纹型环成型,所以带螺纹塑件的脱出可分为强制脱螺纹、活动螺纹型芯或螺纹型环和旋转脱螺纹等三大类。
(1)强制脱螺纹 这种模具结构简单,通常用于精度要求不高的塑件。
1)利用塑件的弹性脱螺纹。对于聚乙烯、聚丙烯等具有弹性的塑料件,可以采用脱模板将塑件从螺纹型芯上强制脱出,如图5⁃100所示。
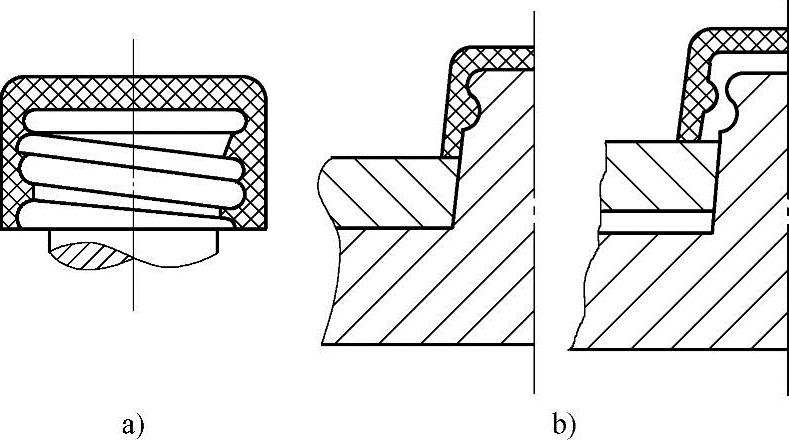
图5⁃100 利用塑件的弹性脱螺纹
2)利用硅橡胶螺纹型芯脱螺纹。图5⁃101所示为硅橡胶螺纹型芯脱螺纹。开模时,由于弹簧6的作用,模具从A—A分型,芯杆5首先从橡胶螺纹型芯4中脱出,使橡胶螺纹型芯产生收缩,再由推杆1将塑件强迫脱出。
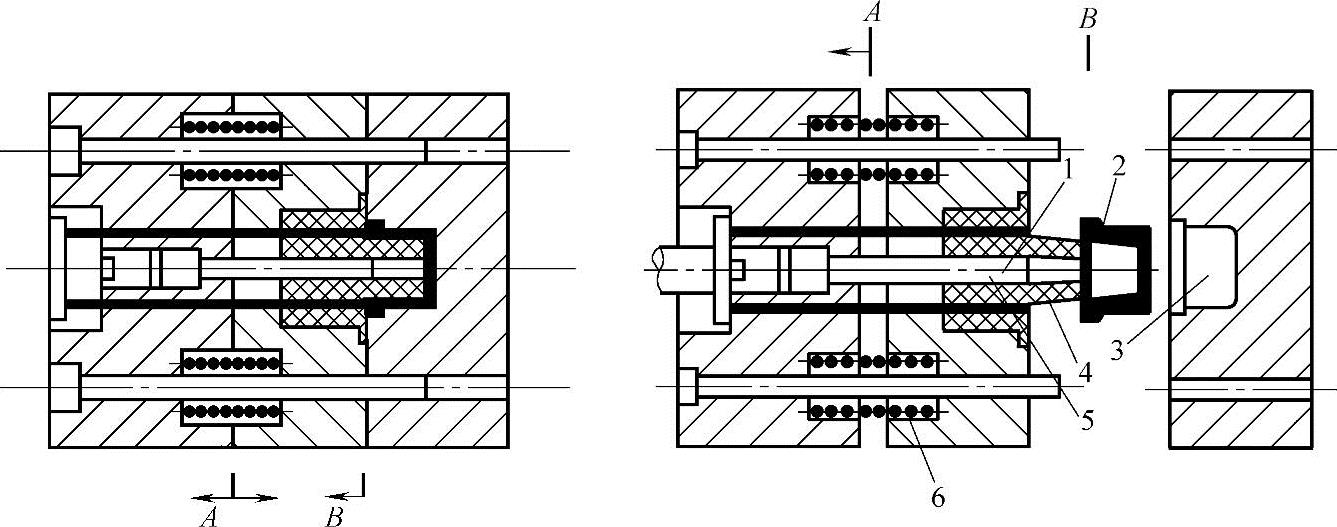
图5⁃101 硅橡胶螺纹型芯脱螺纹
1—推杆 2—塑件 3—型腔 4—橡胶螺纹型芯 5—芯杆 6—弹簧
(2)活动螺纹型芯或型环脱螺纹 这种模具是将螺纹部分做成活动型芯或型环,开模时随塑件一起脱模,最后在模外用手工将其与塑件脱离。这种模具结构简单,但需要数个螺纹型芯或型环,还需要模外取芯装置。
图5⁃102a所示为螺纹型芯随塑件推出后,用专用夹具夹住型芯尾部使其脱出塑件。图5⁃102b所示为手工脱螺纹型环的形式,开模后螺纹型环随塑件推出,再用专用工具使螺纹型环脱出塑件。
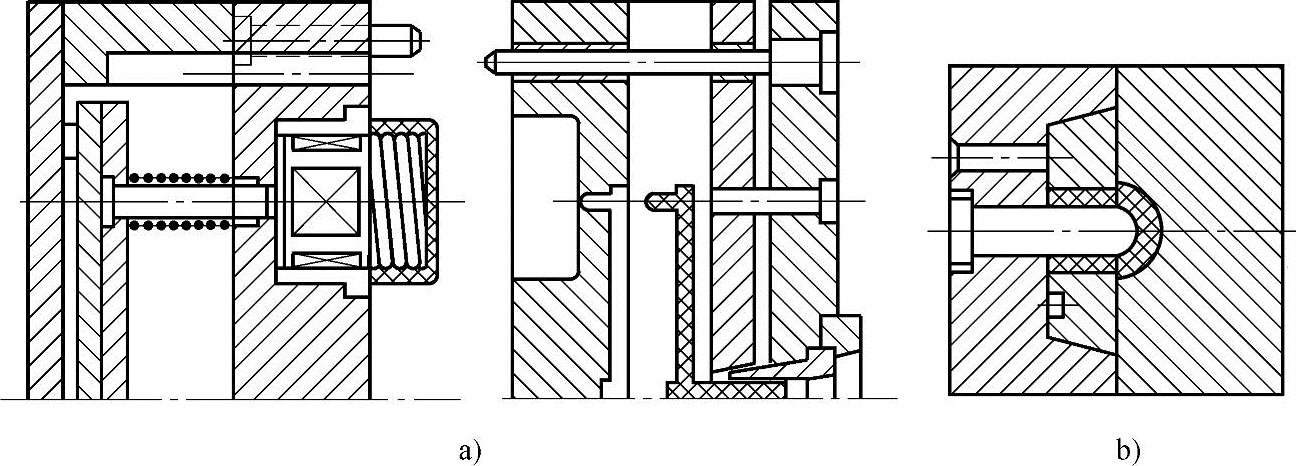
图5⁃102 螺纹部分做成活动型芯或型环
对于精度要求不高的外螺纹塑件,可采用两块拼合式螺纹型环成型,如图5⁃103所示。开模时,在斜导柱的作用下,型环上下分开,再由脱模板推出塑件。
对于精度要求不高的内螺纹塑件,可设计成间断内螺纹,由拼合的螺纹型芯成型,如图5⁃104所示。开模后塑件留在动模,推出时推杆1带动推板2,推板2带动螺纹型芯5和脱模板3一起向前运动,同时螺纹型芯5向内收缩,使塑件脱模。
(3)旋转脱螺纹
1)手动旋转脱螺纹。图5⁃105所示为手动旋转脱螺纹机构。开模后,用手轮转动轴1,通过齿轮2和齿轮3的传动,使螺纹型芯7按旋出塑件方向转动。弹簧4在脱出塑件的过程中,始终顶住活动型芯6,使其随塑件一起向脱出方向移动,其顶端与塑件始终相接触,防止塑件随螺纹型芯转动,从而使塑件顺利脱模。
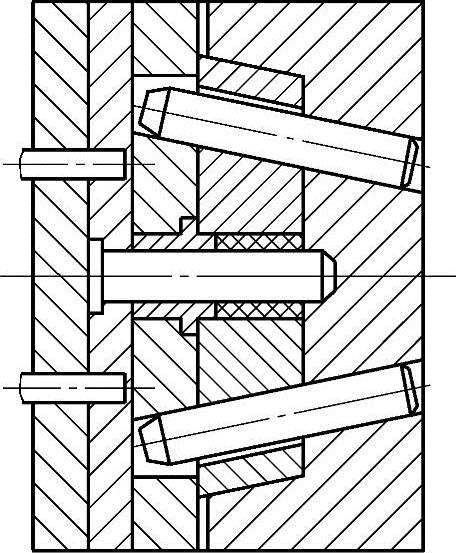
图5⁃103 拼合式螺纹型环
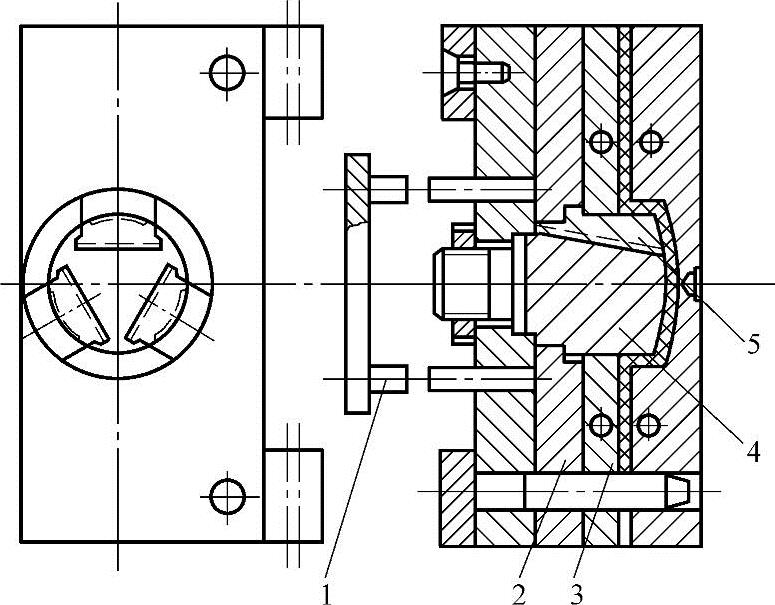
图5⁃104 拼合式螺纹型芯
1—推杆 2—推板 3—脱模板 4—型芯 5—螺纹型芯
2)机动旋转脱螺纹。这种机构是利用开模时的直线运动,通过齿条、齿轮或螺杆的传动,带动螺纹型芯或型环作旋转运动而脱出塑件。图5⁃106所示为齿轮、齿条脱螺纹机构。开模时,装在定模座板上的齿条1带动小齿轮3,并通过齿条2带动螺纹型芯5随之转动,从而将带螺纹的塑件及浇注系统凝料同时脱出。
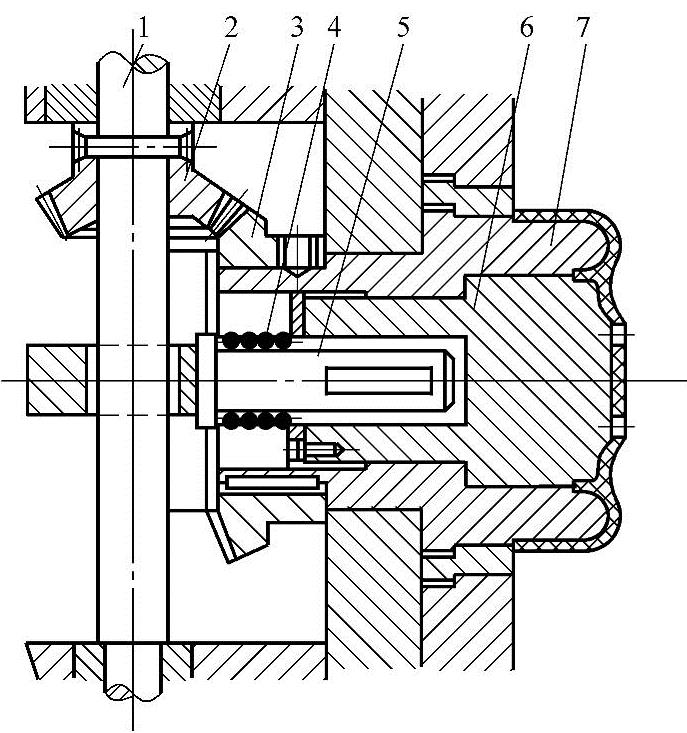
图5⁃105 手动旋转脱螺纹
1—轴 2、3—齿轮 4—弹簧 5—花键轴 6—活动型芯 7—螺纹型芯
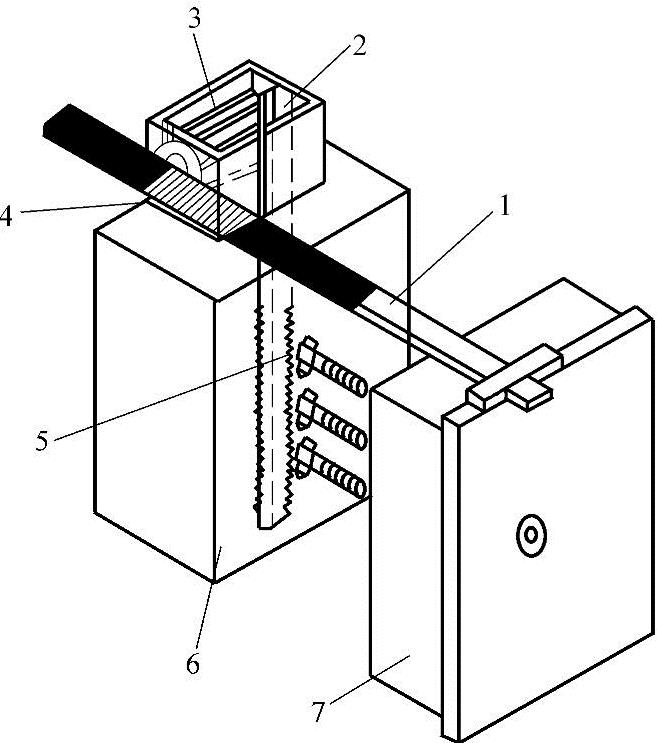
图5⁃106 齿轮、齿条脱螺纹机构
1、2—齿条 3—齿轮 4—驱动箱 5—型芯 6—动模 7—定模
图5⁃107所示为螺旋杆、齿轮脱螺纹机构。开模时,在二次分型机构的作用下,首先脱掉点,浇口。当限位钉10与型腔板8接触时,模具从C—C分型面分开,此时,螺旋杆1与螺旋套2作相对直线运动,因螺旋杆1的一端由定位键固定,因此迫使螺旋套2转动,从而带动齿轮3及螺纹型芯4转动。同时弹簧5推动推管6及推板7,使其始终顶牢制件,防止制件随螺纹型芯转动,从而顺利脱模。
图5⁃108为斜导柱、螺旋杆脱螺纹机构。开模时,斜导柱1抽动螺旋杆2,由于滚珠3的作用使齿轮5转动,通过齿轮5使带有小齿轮4的螺纹型芯6按旋出方向转动,而从制件中脱出。螺旋杆2带有大导程螺旋槽,其螺旋方向由成型螺纹的螺旋方向及传动级数而定。
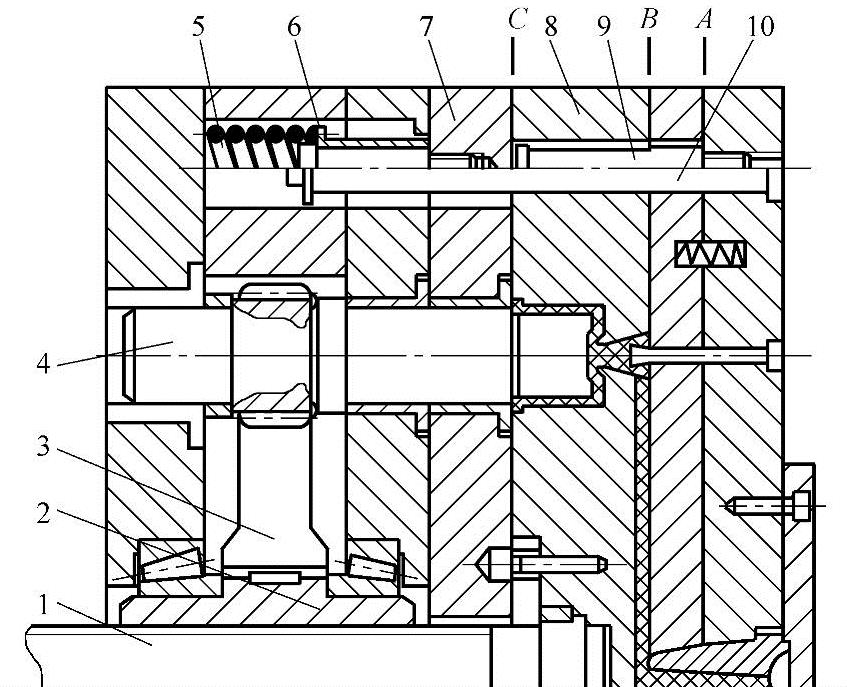
图5⁃107 螺旋杆、齿轮脱螺纹机构
1—螺旋杆 2—螺旋套 3—齿轮 4—螺纹型芯 5—弹簧 6—推管 7一推板 8一型腔板(中间板) 9、10—限位钉
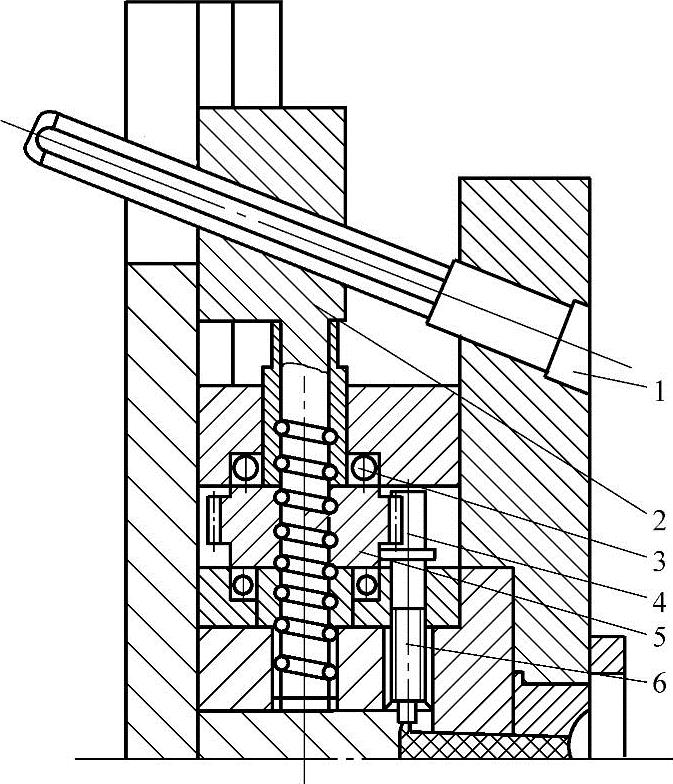
图5⁃108 斜导柱、螺旋杆脱螺纹机构
1—斜导柱 2—螺旋杆 3—滚珠 4、5—齿轮 6—螺纹型芯
3)其他动力源旋转脱螺纹机构。图5⁃109所示为靠液压缸或气缸给齿条以往复运动,再通过齿轮使螺纹型芯回转。图5⁃110是靠电动机和蜗轮蜗杆使螺纹型芯回转的脱螺纹机构。
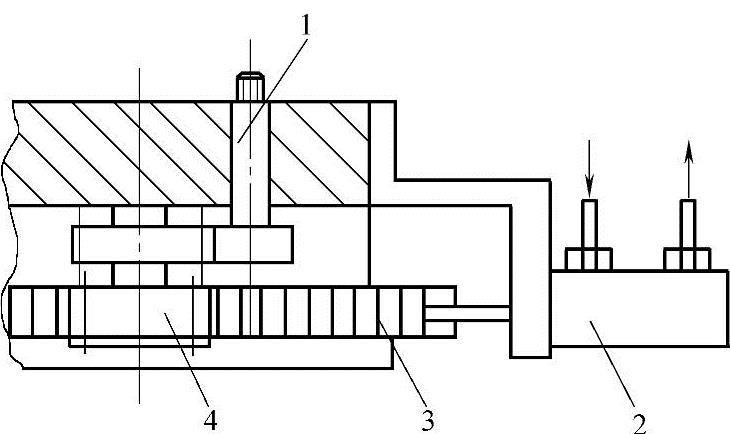
图5⁃109 气(液)驱动形式
1—螺纹型芯 2—液压缸 3—齿条 4—齿轮
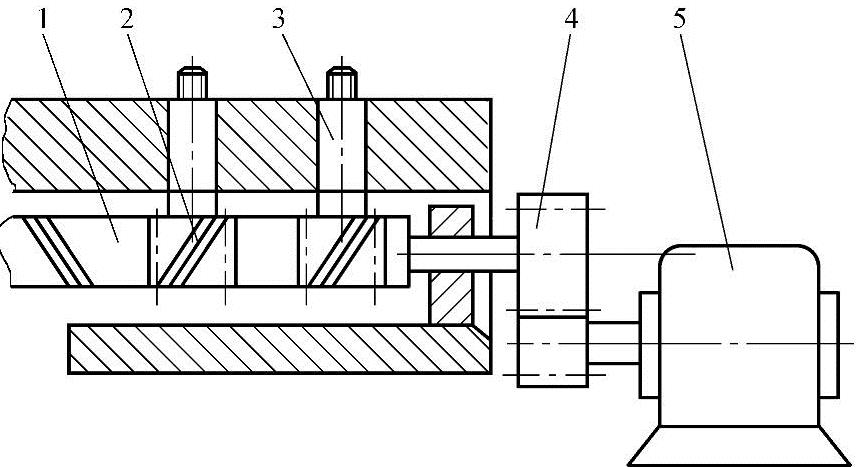
图5⁃110 电动机驱动形式
1—蜗杆 2—蜗轮 3—螺纹型芯 4—齿轮 5—电动机
相关推荐