【摘要】:外圆表面的精车一般作为最终工序或光整加工的预加工工序。用研磨工具和研磨剂,通过研具与工件在一定压力下做相对滑动,从工件表面上磨掉一层极薄的金属,以提高工件尺寸、形状精度和降低表面粗糙度的精整加工方法。
外圆表面是构成机器零件的基本表面,如轴类、套类和盘类零件是具有外圆表面的典型零件。外圆表面的加工在机器零件制造中是很常见的,根据外圆表面的尺寸、材料及加工要求不同,可选择不同的加工方法。常见的外圆表面的加工方法及特点如下。
1.外圆表面的车削加工
(1)粗车。外圆表面的粗车是最经济、最有效的方法,粗车在车床工艺系统允许的前提下,尽可能地采用大的背吃刀量和进给量,以提高生产率,但为了保证刀具耐用度,切削速度通常选为低速。粗车所能达到的加工精度为IT11~IT12,表面粗糙度Ra 为12.5~50 μm。
(2)精车。外圆表面的精车一般作为最终工序或光整加工的预加工工序。精车后工件尺寸精度可达IT7~IT8,表面粗糙度Ra 为0.8~1.6 μm。
(3)高速细精车。高速细精车是采用硬质合金、立式氮化硼或金刚石刀具,用高切削速度(160 mm/min 以上)、小的背吃刀量 (0.03~0.05 mm)和小的进给量 (0.02~0.2 mm/r),对工件进行精细加工的方法。对于硬度较低的有色金属(如铜、铝),如果采用磨削加工,磨屑容易糊住砂轮,一般在高精度的车床上,采用金刚石刀具进行高速细精车,工件尺寸精度可达IT5~IT6,表面粗糙度Ra 为0.1~1.0 μm,甚至可达镜面效果。
2.外圆表面的磨削加工
外圆表面的磨削加工是主要精加工方法,能经济地获得高的加工精度和小的表面粗糙度值。加工精度通常可达IT5~IT7,表面粗糙度Ra 值可达0.2~0.8 μm。采用高精度的磨削方法,表面粗糙度Ra 值可达0.006~0.1 μm。磨削加工不但可进行精加工,而且可进行粗磨、荒磨、重负荷磨削,特别适合于各种高硬度和淬火后的零件的精加工。
3.外圆表面的精整、光整加工
外圆表面的精整、光整加工是精加工以后进行的超精密加工方法,适用于某些精度和表面质量要求很高的零件。
(1)研磨。用研磨工具和研磨剂,通过研具与工件在一定压力下做相对滑动,从工件表面上磨掉一层极薄的金属,以提高工件尺寸、形状精度和降低表面粗糙度的精整加工方法。研磨精度可达0.025 μm,圆柱度可达0.1 μm,表面粗糙度可达Ra0.01 μm。研磨主要用于精密的零件,如量规、精密配合件、光学零件等。
(2)抛光。抛光能降低表面粗糙度,但不能提高工件的尺寸精度和形状精度。普通抛光工件表面粗糙度可达Ra0.4 μm。
由于各种加工方法所能达到的经济加工精度、表面粗糙度、生产率和生产成本各不相同,因此必须根据具体情况,选择合理的加工方法。表3-1所示为外圆表面各种加工方案和经济加工精度。
表3-1 外圆表面加工方案
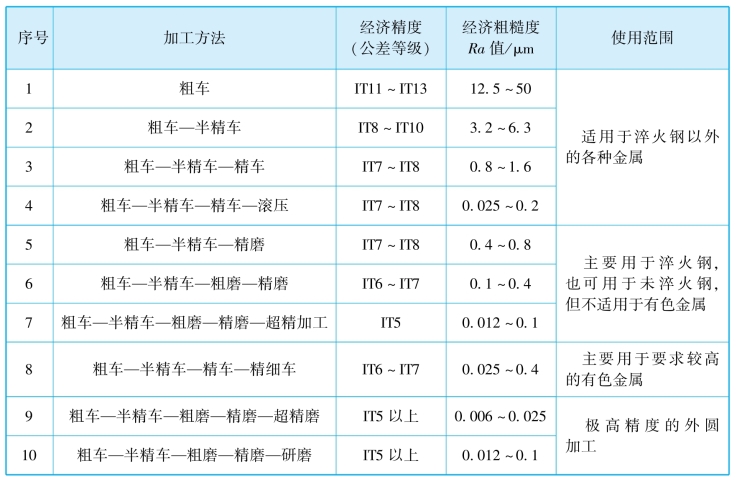
相关推荐