【摘要】:数控机床伺服进给的控制除上述介绍的主回路外,还涉及机床操作面板上的按钮、各类开关、状态指示灯、I/O单元或模块及中间继电器等组成的辅助控制回路。表5-16所示为快速进给倍率旋钮信号的变换过程,图5-134所示为快速进给倍率控制的PMC梯形图。下面介绍HM1250卧式加工中心JOG进给速度的控制过程。
数控机床伺服进给的控制除上述介绍的主回路外,还涉及机床操作面板上的按钮、各类开关、状态指示灯、I/O单元或模块及中间继电器等组成的辅助控制回路。伺服进给的辅助控制主要包含快速进给倍率控制、JOG进给速度控制、程序进给速度倍率(F指令)控制、倍率取消(进给倍率固定在100%)控制、手摇脉冲发生器控制和轴互锁控制(禁止伺服轴移动)等环节。
1.快速进给倍率的控制及故障
数控机床无论自动运行快速进给速度还是手动运行快速进给速度,都是在CNC参数(如FANUC 18/18i/0i/30i系统的各轴快速进给速度参数#1420,通常设定为8000mm/min左右)中设定,即倍率100%时的快速进给速度,而不必在加工程序中指定。自动运行中的快速进给包括所有的快速进给,如固定循环定位和自动参考位置返回等,不只是程序指定的G00快速进给命令;手动快速进给包含了参考位置返回中的快速进给。通过机床操作面板上的快速进给倍率调节旋钮(见图5-133),可为数控机床的快速进给速度施加倍率控制,通常为F0、F25%、F50%和F100%四挡。其中,F0是由CNC参数(如FANUC 16/16i/18/18i/21/21i/0i/30i系统参数#1421)设定的各伺服轴快速进给倍率的固定进给速度。下面介绍HM1250卧式加工中心(FANUC 31iMA系统)快速进给倍率的控制过程。表5-16所示为快速进给倍率旋钮信号的变换过程,图5-134所示为快速进给倍率控制的PMC梯形图。
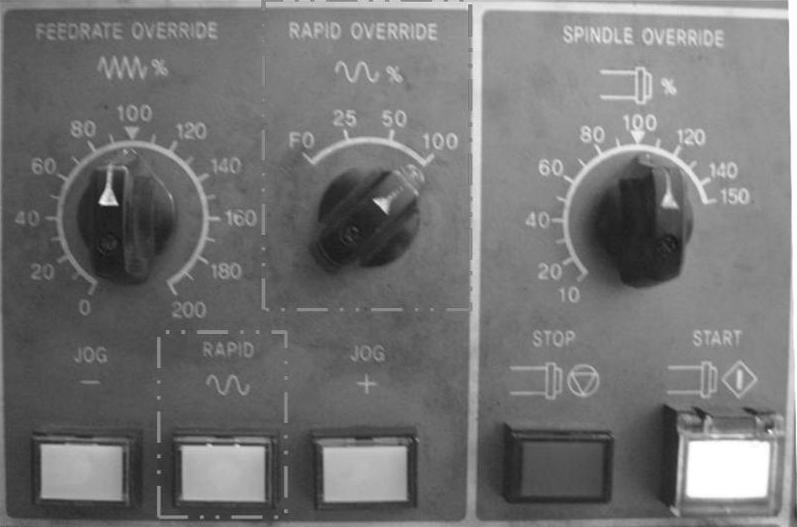
图5-133 HM1250卧式加工中心快速进给倍率旋钮
表5-16 快速进给倍率旋钮信号的变换过程
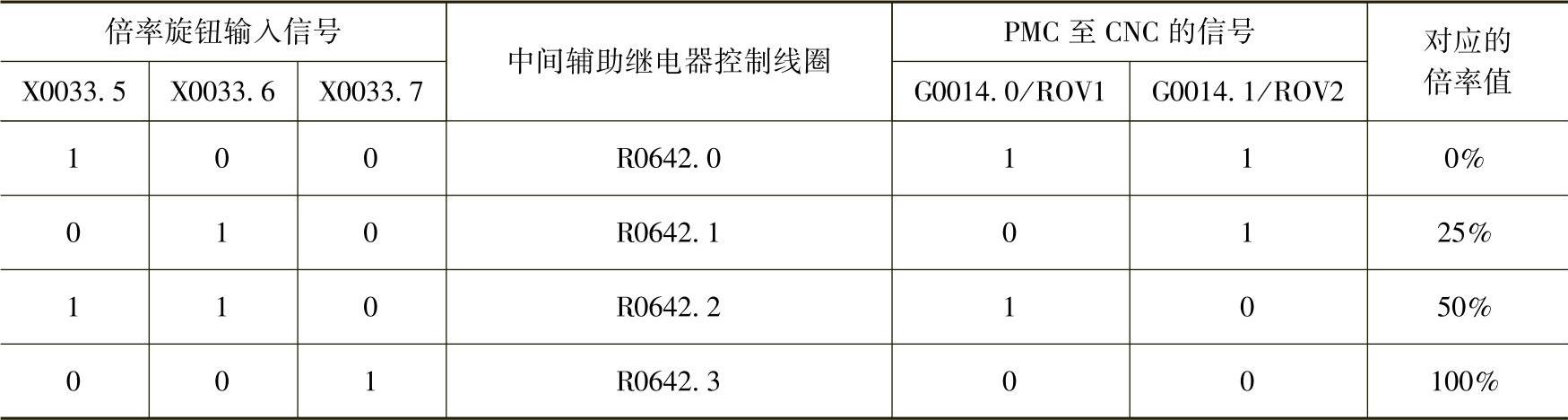
1)快速进给倍率调节旋钮的输入信号地址为X0033.5、X0033.6和X0033.7,进行“与”逻辑组成4种状态,并通过PMC内部线圈R0642.0、R0642.1、R0642.2和R0642.3输出。
2)R0642.0、R0642.1、R0642.2和R0642.3经PMC组合逻辑处理后,向CNC传送G0014.0/ROV1和G0014.1/ROV2两个信号地址。
3)G0014.0和G0014.1组合为4种状态,依次为11、01、10和00,分别对应倍率值的F0、F25%、F50%和F100%。
4)为提高操作过程中各伺服轴的JOG进给速度,特在面板上增加了手动快速进给按键SB23,前提条件为机床操作门关闭和无干涉区错误报警,并由PMC向CNC传送手动快速进给选择信号G0019.7/RT。
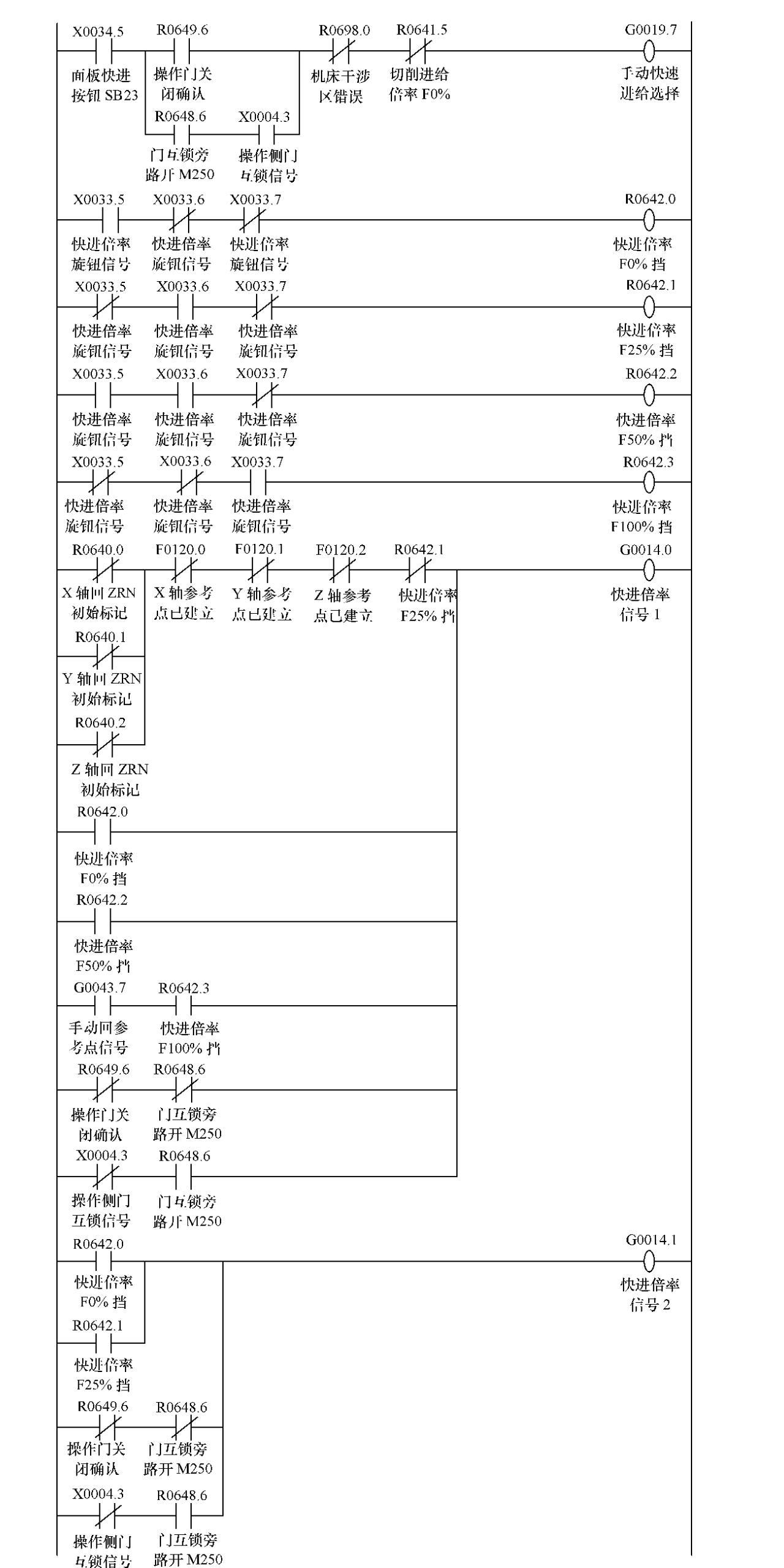
图5-134 HM1250卧式加工中心快速进给倍率控制的PMC梯形图
2.JOG进给速度的控制
当数控机床运行模式处于JOG进给方式,且伺服轴的方向选择信号设定为1时,即可通过面板上的伺服轴正方向按钮或负方向按钮,控制所选伺服轴连续移动,该功能称为机床的JOG进给(见图5-135)。伺服轴JOG进给的速度由CNC参数(如FANUC 18/18i/0i/30i系统参数#1423)设定,且同时移动的轴数由CNC参数来设定(如FANUC 18/18i/0i/30i系统参数#1002.0/JAX=0为JOG进给时仅单轴移动,#1002.0/JAX=1为同时移动3个轴);还有当伺服轴执行JOG进给时,机床操作面板上的进给倍率调节旋钮有效。另外,按下机床操作面板上的快速进给按钮,可使相应的伺服轴以CNC参数(如FANUC 18/18i/0i/30i系统中参数#1424)设定的手动快速移动速度进给,此时JOG进给速度倍率开关无效。下面介绍HM1250卧式加工中心(FANUC 31iMA系统)JOG进给速度的控制过程。表5-17所示为JOG进给速度控制的信号变换过程,图5-136所示为JOG进给速度控制的PMC梯形图。
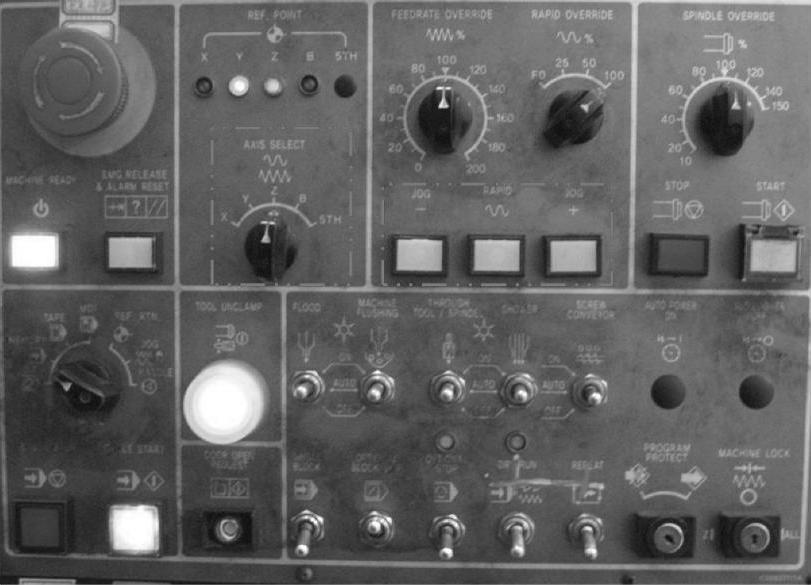
图5-135 HM1250卧式加工中心的JOG进给速度控制按键
表5-17 JOG进给速度控制的信号变换过程
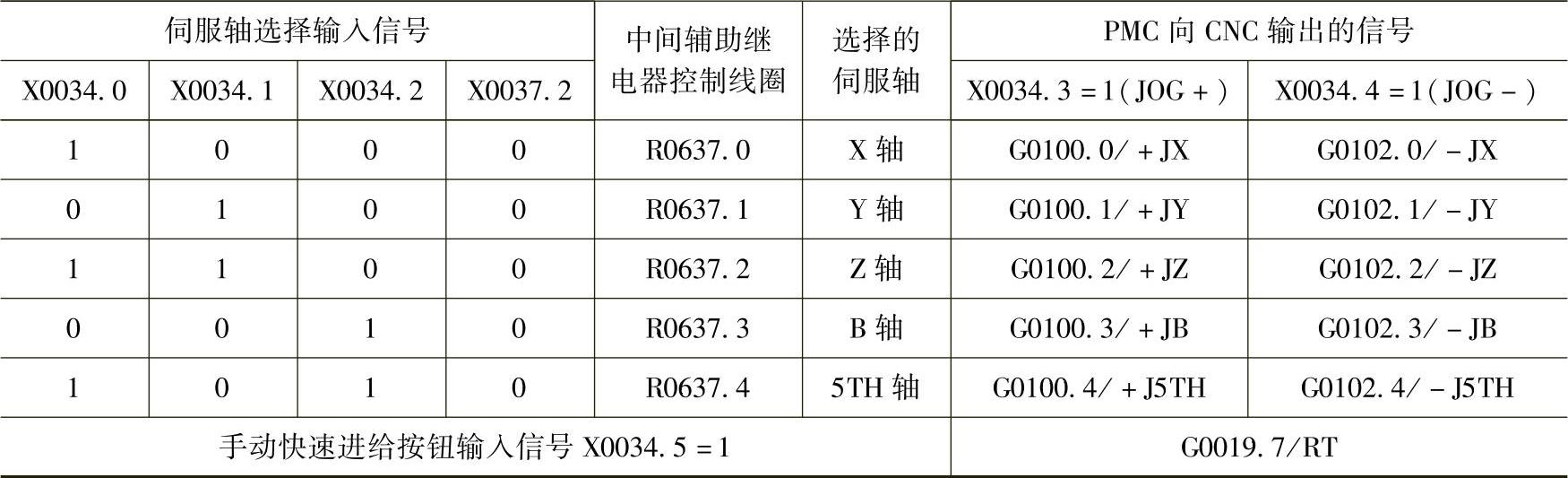
1)机床伺服轴选择的输入信号地址为X0034.0、X0034.1、X0034.2和X0037.2,进行“与”逻辑组成5种状态,并分别通过PMC内部线圈R0637.0、R0637.1、R0637.2、R0637.3和R0637.4输出。而伺服轴正方向按钮SB21、负方向按钮SB22和手动快速进给按钮SB23的输入信号地址分别为X0034.3、X0034.4和X0034.5。
2)伺服轴选择中间辅助控制信号R0637.0、R0637.1、R0637.2、R0637.3和R0637.4分别和伺服轴正方向按钮输入信号地址X0034.3进行与逻辑后,PMC向CNC传送进给轴正方向选择信号G0100.0/+JX、G0100.1/+JY、G0100.2/+JZ、G0100.3/+JB和G0100.4/+J5TH;同理,与X0034.4(负方向)进行“与”逻辑后,PMC向CNC传送进给轴负方向选择信号G0102.0/-JX、G0102.1/-JY、G0102.2/-JZ、G0102.3/-JB和G0102.4/-J5TH。
3)伺服轴JOG进给时,操作面板上的进给倍率调节旋钮有效;PMC向CNC传送手动进给速度倍率信号G10(见表5-18),
。其中,∗JVi=1时Vi=0;∗JVi=0时Vi=1。
表5-18 JOG进给倍率信号对应表(负逻辑信号即0有效)
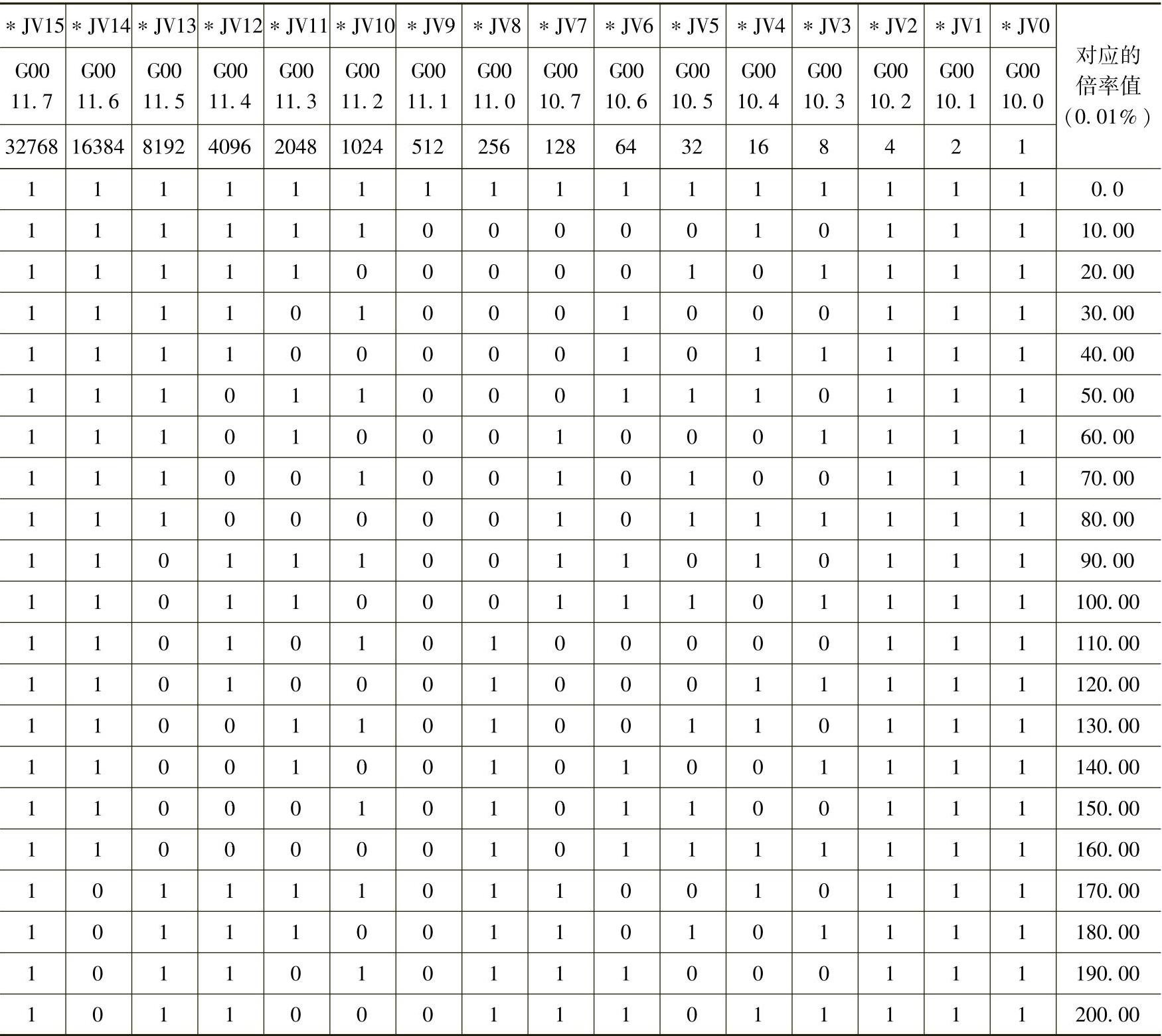
4)CNC装置对接收的G地址信号进行运算处理,由轴控制卡向伺服放大器发出伺服轴控制指令,驱动伺服电动机旋转;根据位置检测装置,经伺服放大器向CNC装置反馈的数据(机床工作台的位移,伺服电动机转子的角位移和速度),与预先给定的理论值相比较,以得到的差值控制机床实现精确定位,直至差值为零。
5)为提高操作过程中各伺服轴的JOG进给速度,特在面板上增加了手动快速进给按键SB23,前提条件为机床操作门关闭和无干涉区错误报警,并由PMC向CNC传送手动快速进给选择信号G0019.7/RT;手动快速进给速度由CNC参数#1424设定。
3.程序进给速度倍率(F指令)的控制
加工过程中,用户可通过机床操作面板上的进给倍率旋钮选择百分比(%)来增加或减少编程的进给速度。如程序中F代码指定的进给速度为100mm/min和进给倍率设定为50%时,机床实际切削进给速度为50mm/min。切削进给速度倍率信号共有8个二进制编码信号(倍率值在0%~254%内,以1%为单位倍率进行选择),进给倍率信号为负逻辑信号(即0)有效。FANUC 18/18i/0i/30i系统的进给倍率信号地址为G12,CNC参数#3002.4/IOV=0设定进给倍率信号和快速移动倍率信号使用负逻辑。下面介绍HM1250卧式加工中心(FANUC 31iMA系统)程序进给速度倍率(F指令,进给速度倍率旋钮见图5-137)的控制过程。
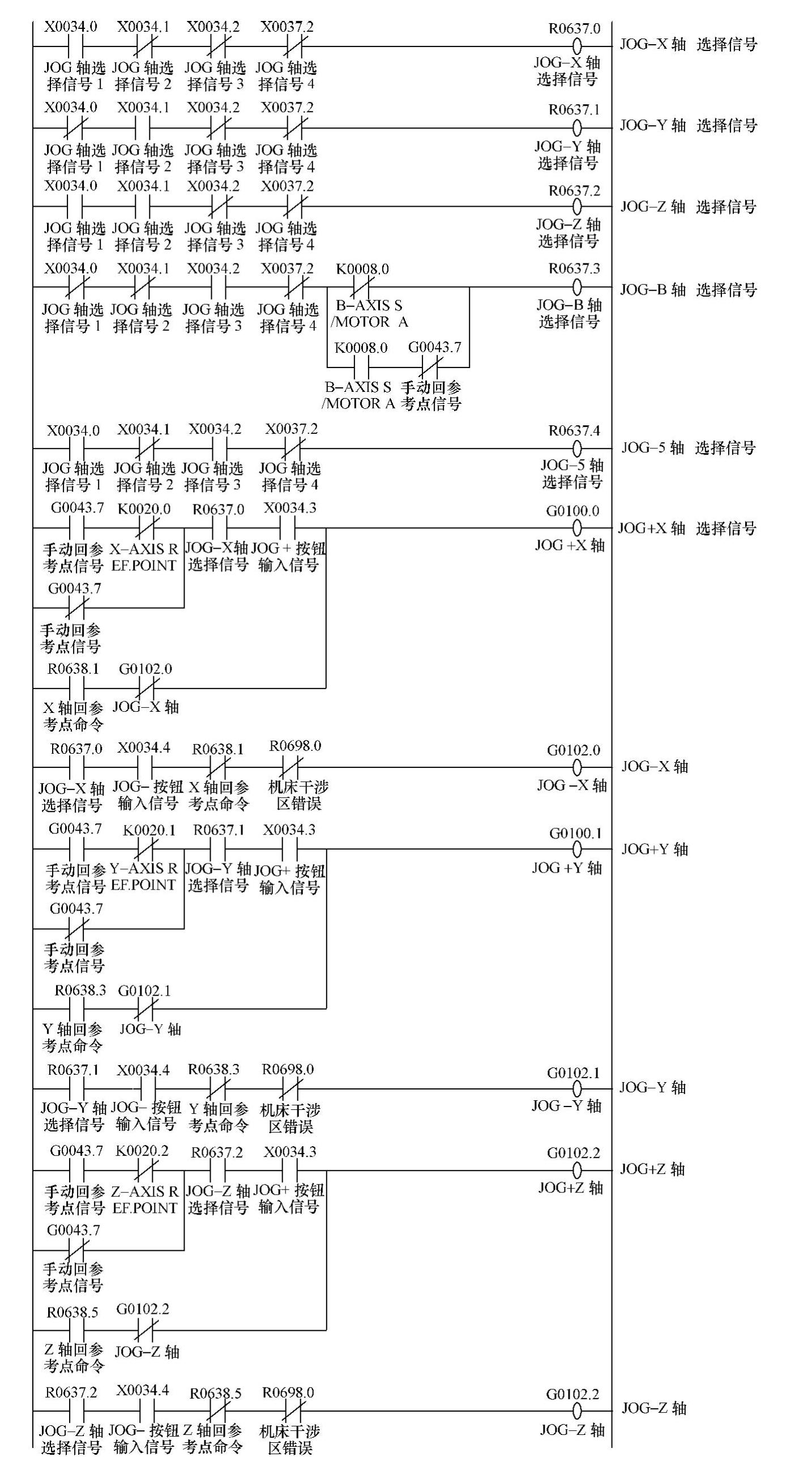
图5-136 HM1250卧式加工中心JOG进给速度控制的PMC梯形图
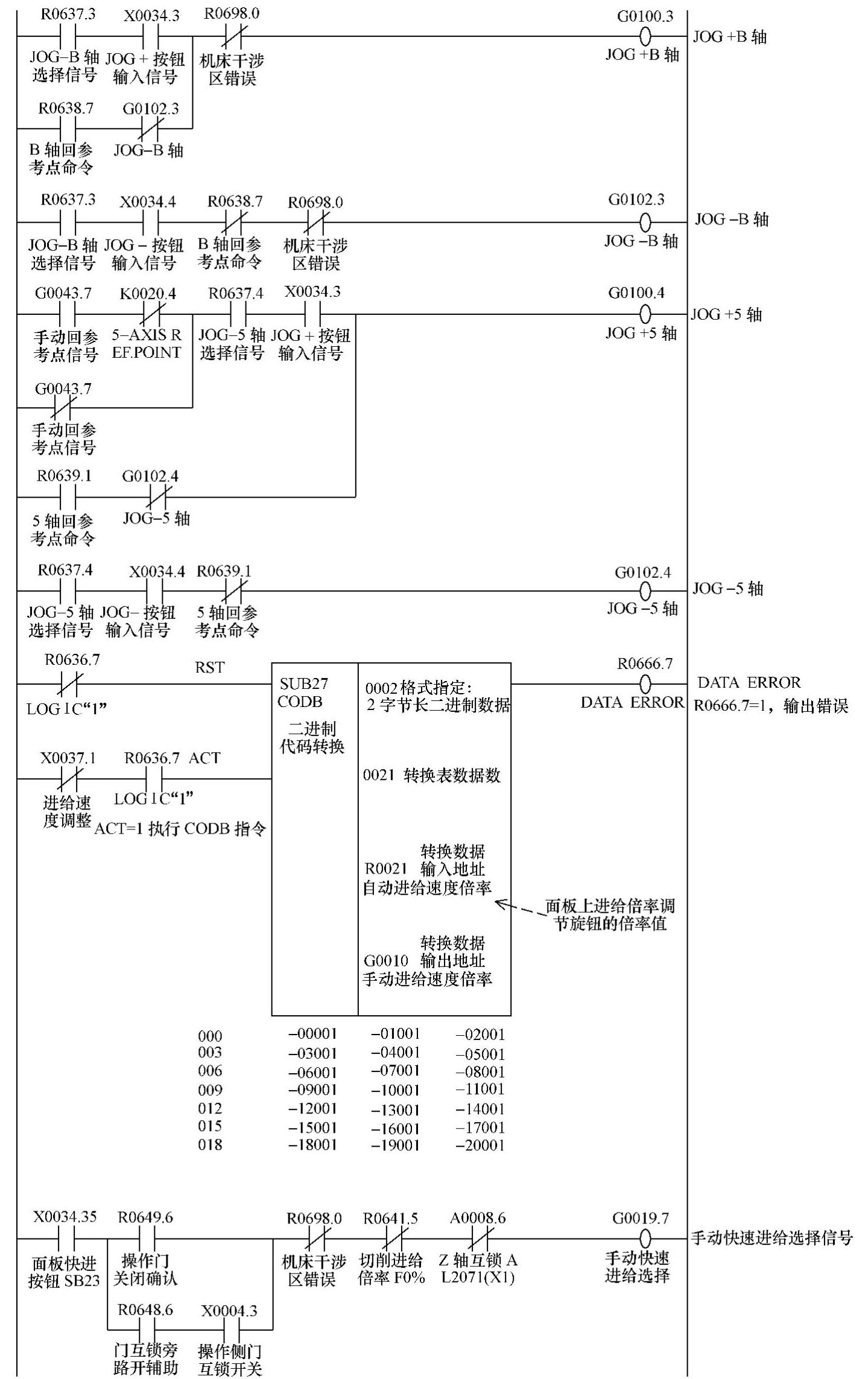
图5-136 HM1250卧式加工中心JOG进给速度控制的PMC梯形图(续)
1)机床进给倍率旋钮的输入信号地址为X0033.0、X0033.1、X0033.2、X0033.3和X0033.4,以二进制代码形式组成21种状态,并通过逻辑与传输指令MOVE发送至继电器R21中。
2)通过代码转换指令CODB把开关位置指定表格的数据转换成二进制数值,传送至数据表D660中。
3)由于CNC参数#3002.4/IOV=0使切削进给倍率为负逻辑控制,故通过指令MOVOR(逻辑或后的数据传送)将数据表D660中的数值进行逻辑加运算,并将运算结果输出至进给速度倍率信号G12中(见表5-19),从而完成PMC控制。
4)当倍率取消信号OVC/G0006.4=1时,切削进给倍率被固定为100%。
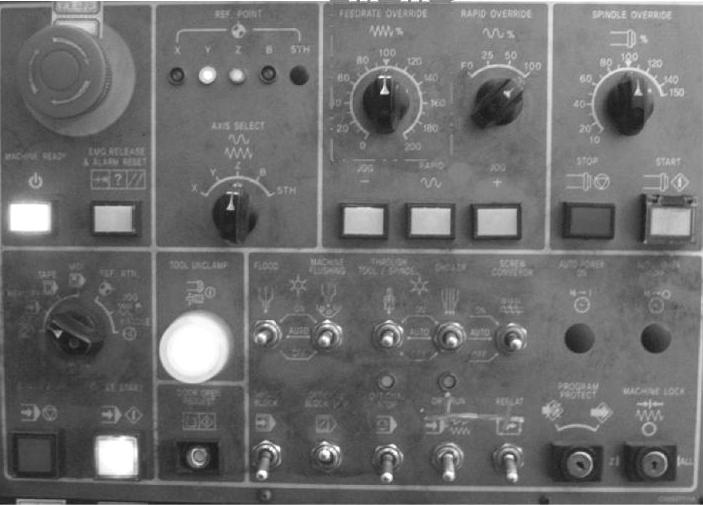
图5-137 HM1250卧式加工中心的程序进给速度倍率旋钮
HM1250卧式加工中心程序进给速度倍率控制梯形图见图5-138。
表5-19 程序进给速度倍率信号对应编码表(负逻辑信号即0有效)
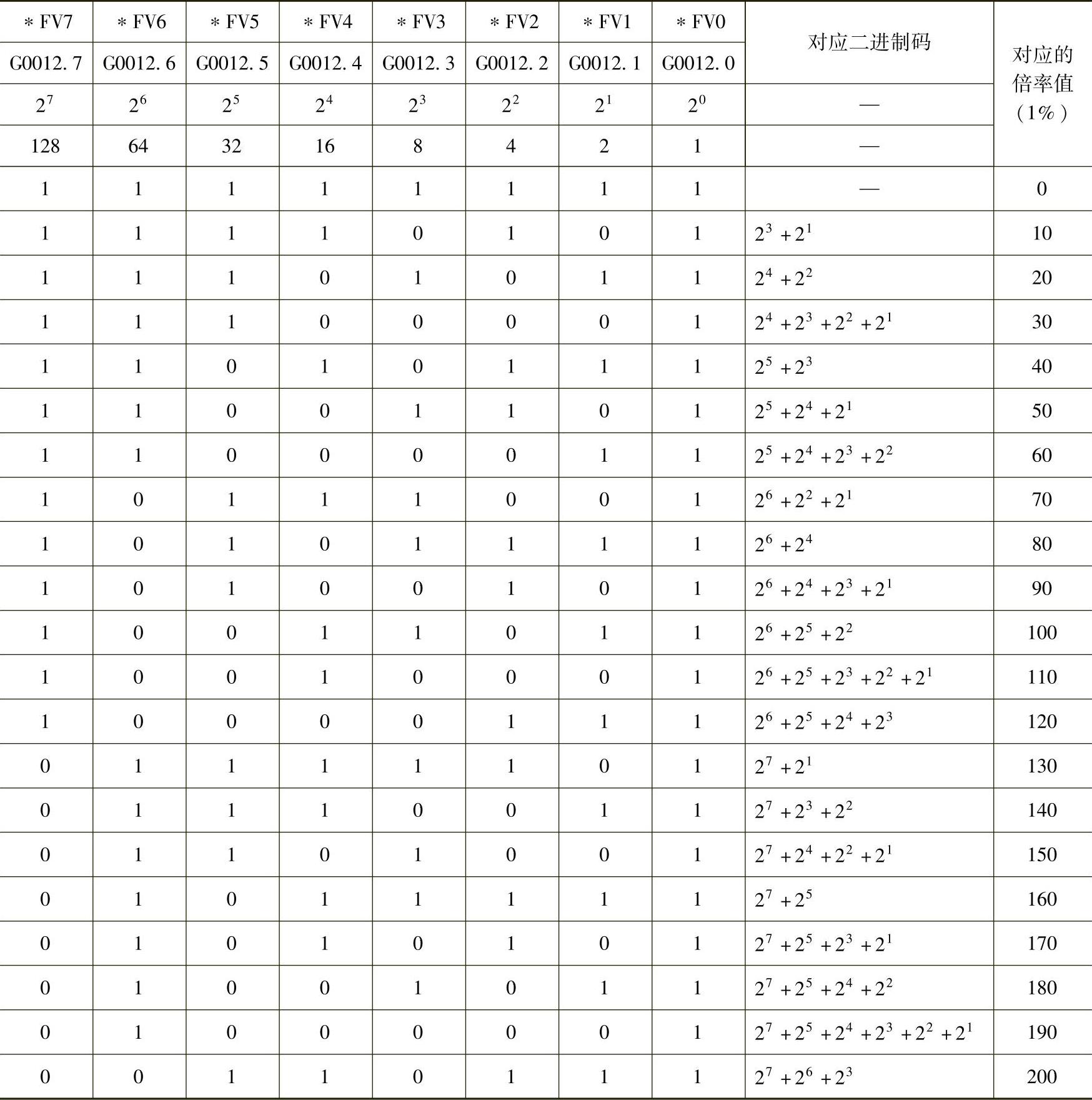
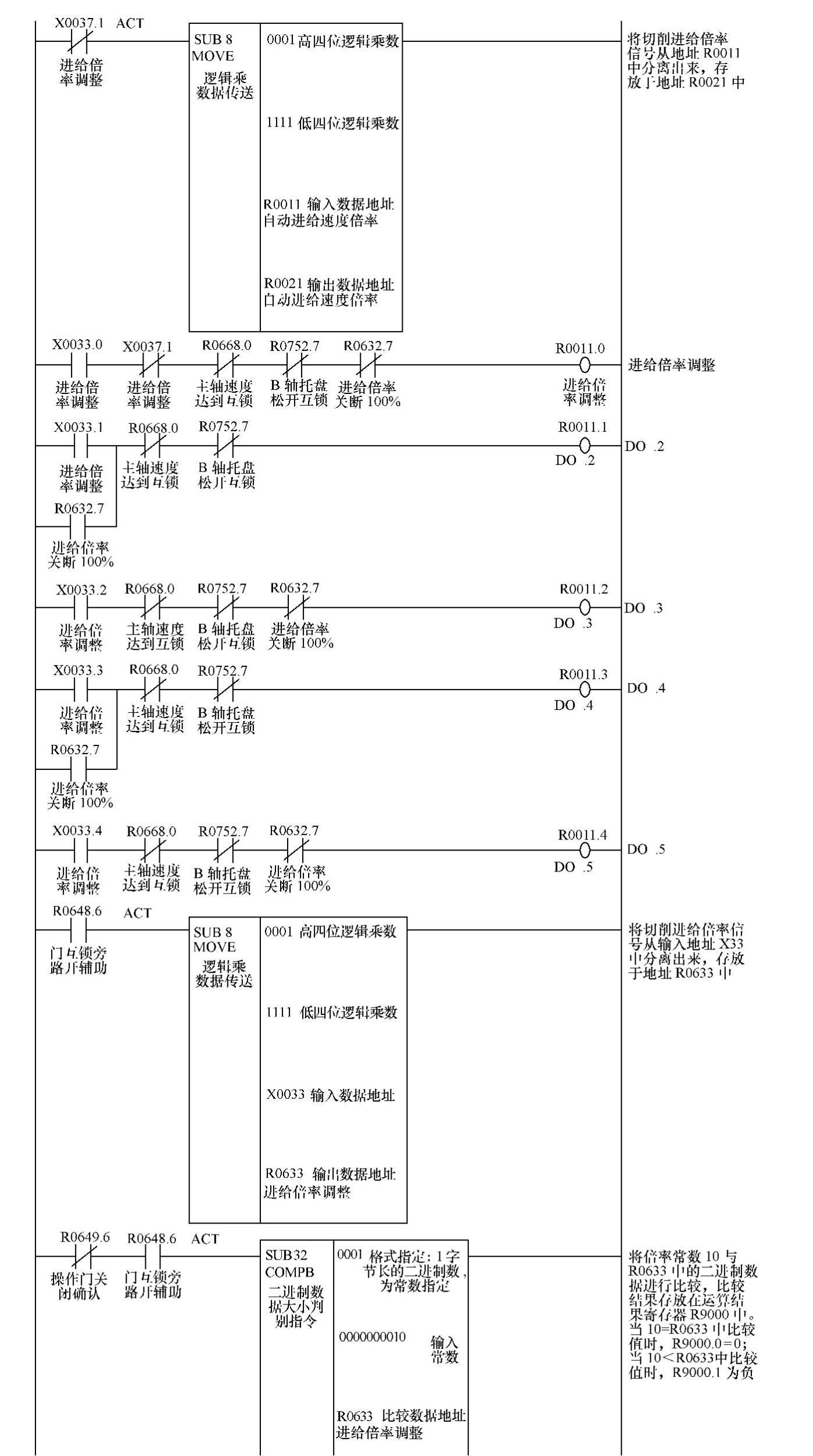
图5-138 HM1250卧式加工中心程序进给速度倍率控制梯形图
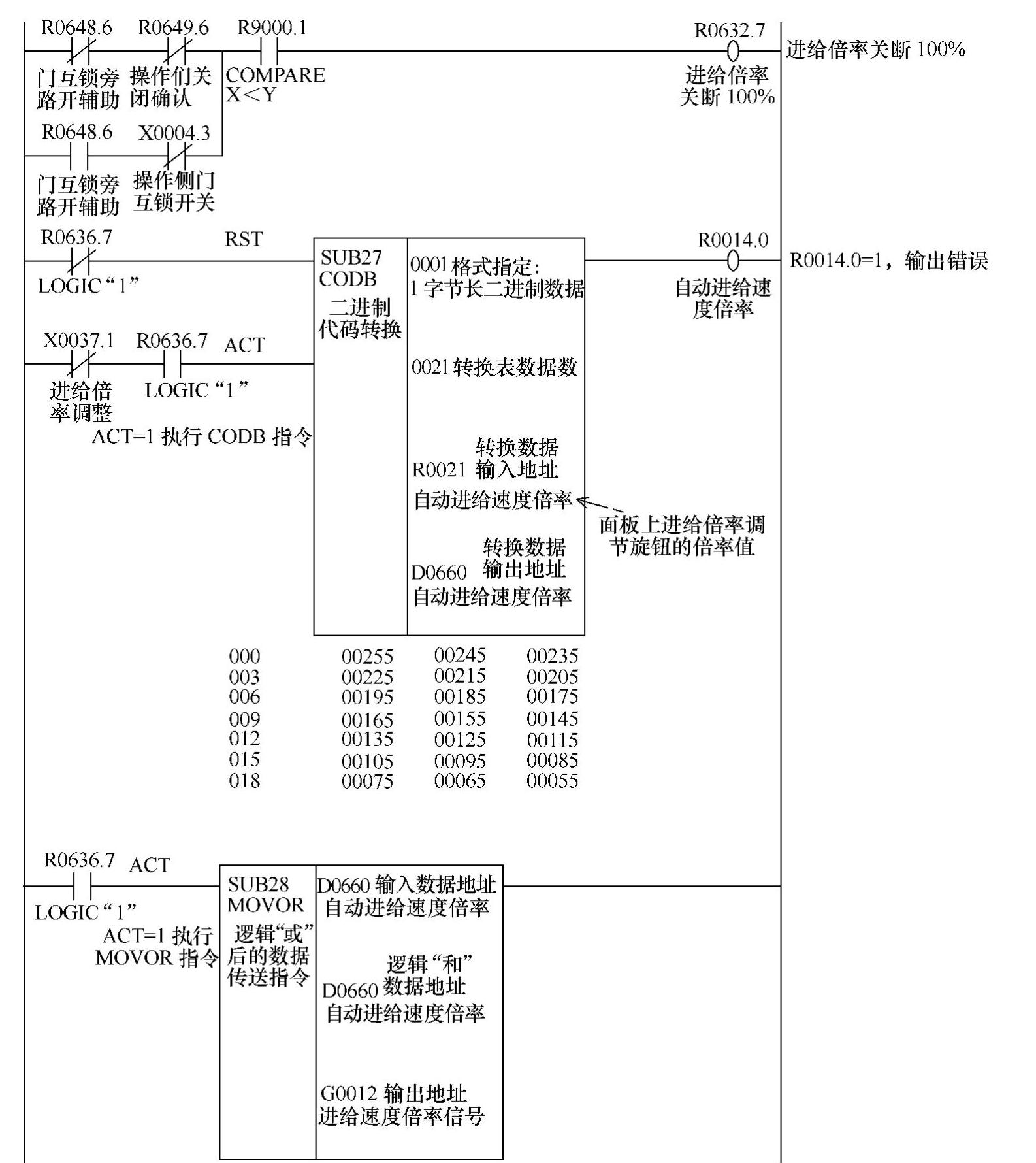
图5-138 HM1250卧式加工中心程序进给速度倍率控制梯形图(续)
4.倍率取消(进给倍率固定在100%)控制
倍率取消信号激活后,不论面板上的进给倍率旋钮置于何种位置,进给倍率均不起作用,即速度倍率固定在100%,但快速进给倍率和主轴速度倍率不受其影响。倍率取消信号主要用于攻螺纹中的螺纹加工以防止乱扣,FANUC 18/18i/0i/30i系统的倍率取消信号地址为G0006.4/OVC。HM1250卧式加工中心(FANUC 31iMA系统)的倍率取消分别由辅助功能代码M48和M49控制倍率取消功能打开、关闭。当CNC装置读取M指令时,对其进行二进制译码处理,结果分别存放于PMC内部继电器R0605.5(00110000)和R0605.6(00110001)中,通过PMC逻辑向CNC输出倍率取消信号OVC/G0006.4=1,从而完成PMC控制。图5-139所示为HM1250卧式加工中心的倍率取消控制梯形图。
5.手摇脉冲发生器的控制
当数控机床运行模式处于HANDLE/手轮状态时,用户可通过旋转机床操作面板上的手摇脉冲发生器MPG(简称手轮,见图5-140)而连续不断地移动所选伺服轴。利用手轮轴选择开关设定被移动的伺服轴,手轮旋转1个刻度时,机床移动的最小距离等于最小输入增量单位,即旋转手轮360°,机床移动的距离可被放大10倍或由CNC参数确定的任意倍率,如FANUC 18/18i/0i/30i系统的任意倍率参数#7113和#7114可设定2种倍率。除了所有伺服轴共用的任意倍率参数外,还可以在CNC参数中设定各伺服轴独立的任意倍率,如参数#12350和#12351。当手轮工作时,需要激活手轮进给选择信号、手轮轴选择信号、手轮倍率信号和手轮中断信号。
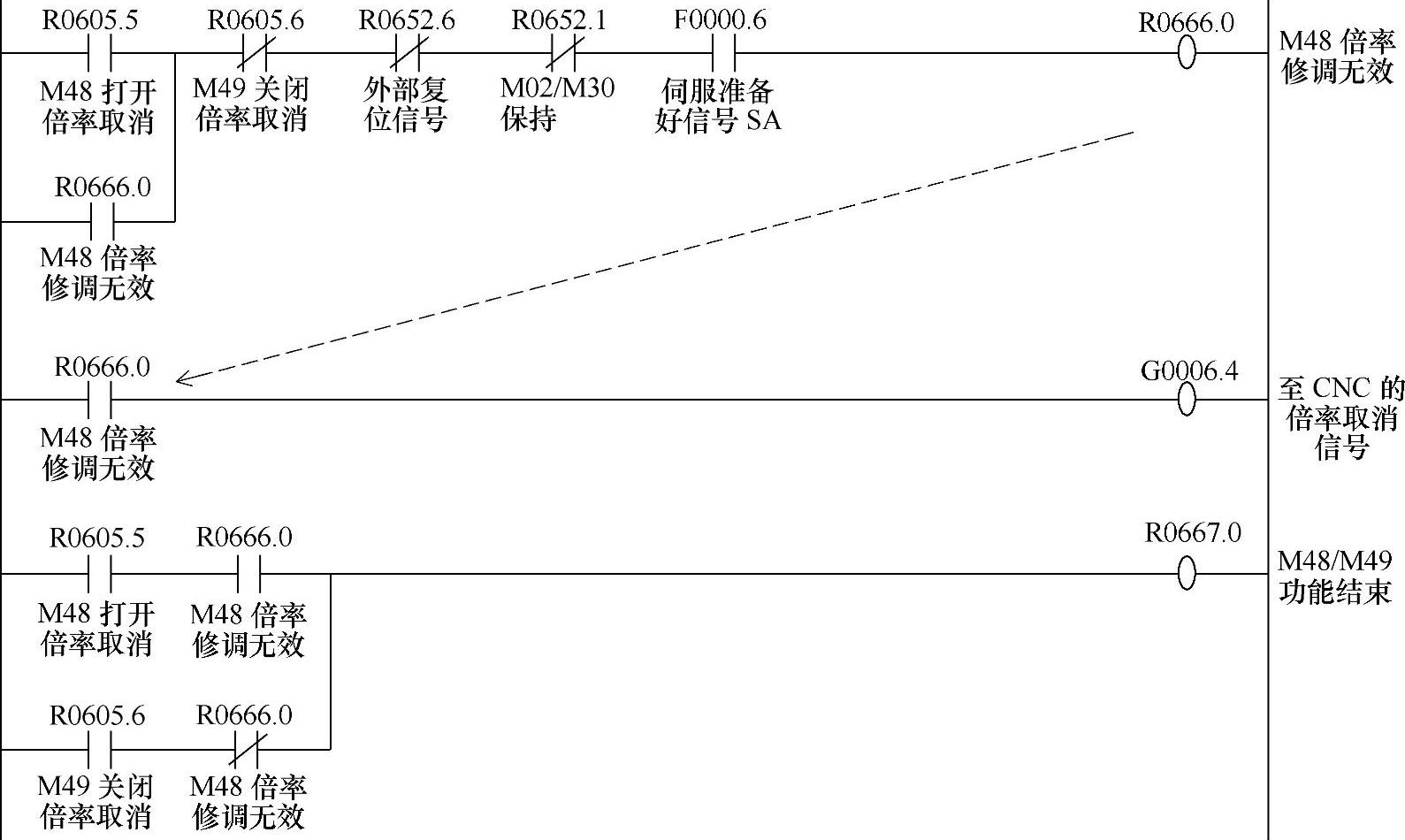
图5-139 HM1250卧式加工中心倍率取消控制梯形图
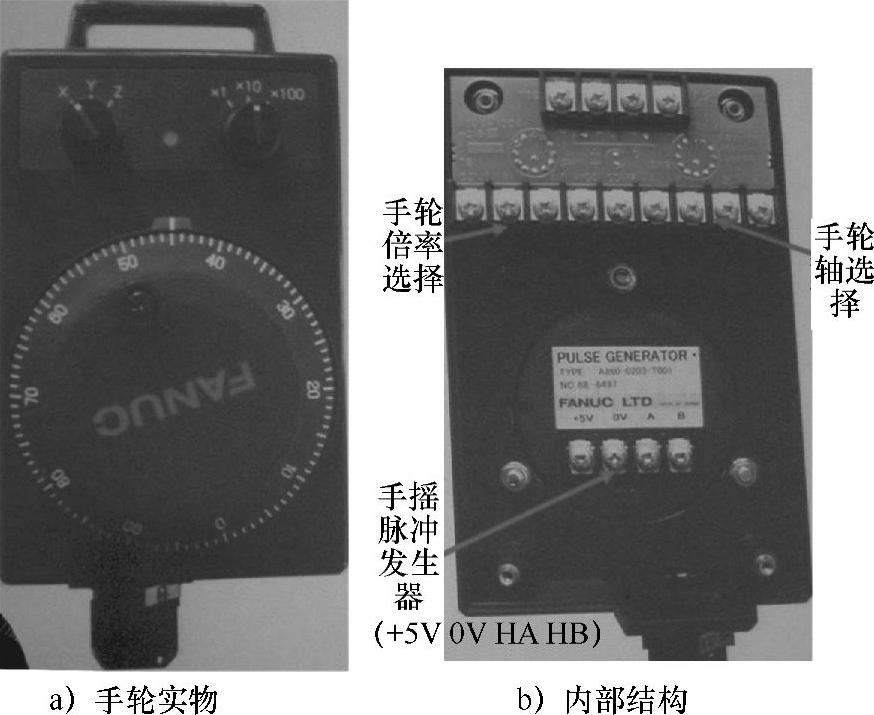
图5-140 FANUC公司的手摇脉冲发生器
FANUC公司的手轮经分布式I/O板连接至CNC装置中主CPU板的I/O Link接口。与脉冲编码器一样使用DC5V电源,其连接电缆电阻引起的电压降≤0.2V;连接电缆长度L可由以下公式计算得出

式中 0.1——MPG的电流;
R——每单位长度的电线阻值Ω/m;
m——0V或5V电线的数量。
通常,连接1个MPG时L≤50m,连接2个MPG时L≤38m,连接3个MPG时L≤25m。以HM1250卧式加工中心(FANUC 31iMA系统)为例,介绍手摇脉冲发生器的连接及PMC控制过程。
1)HM1250卧式加工中心手摇脉冲发生器的接线图见图5-141。
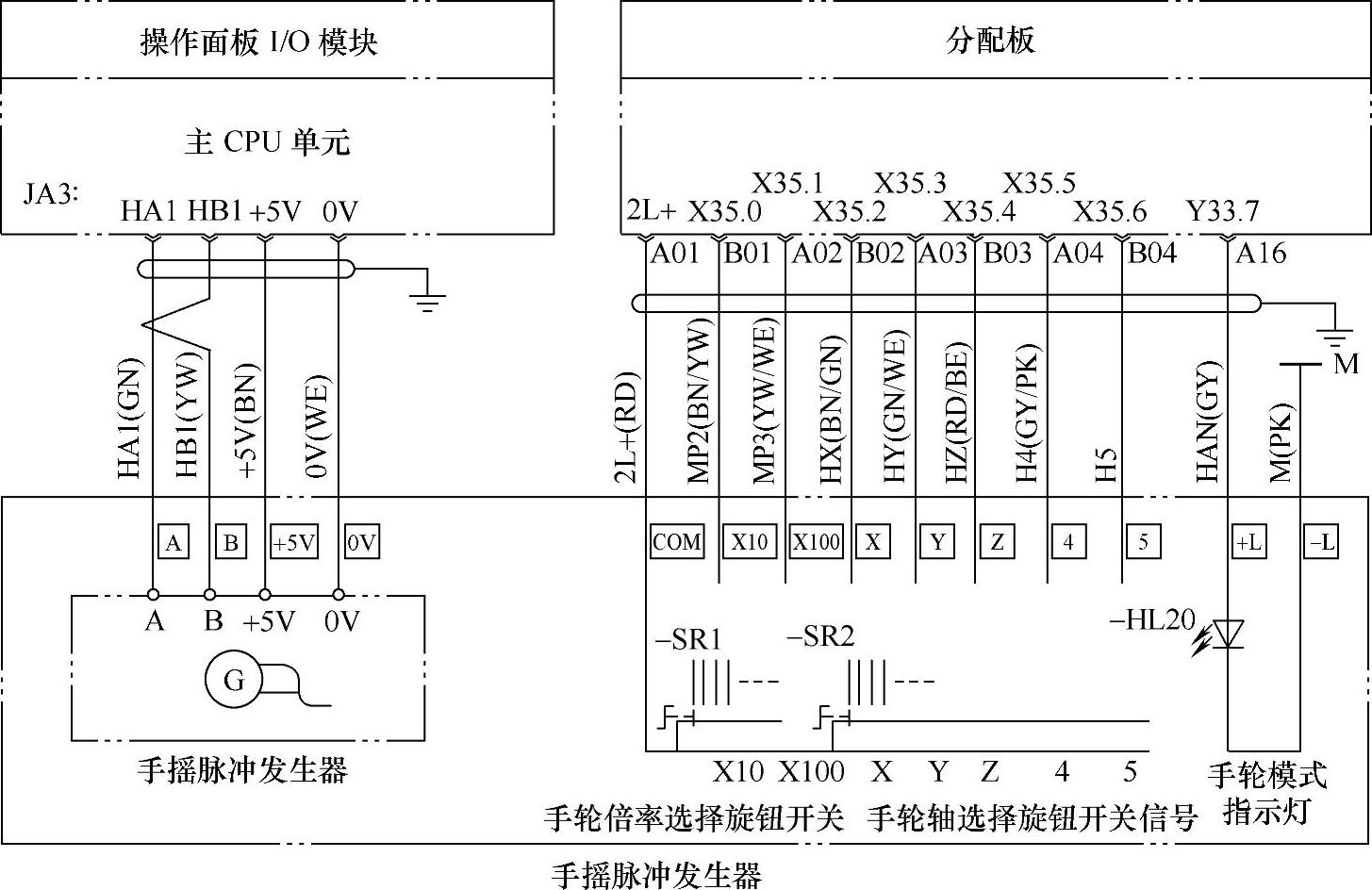
图5-141 HM1250卧式加工中心手摇脉冲发生器的接线图
2)对于FANUC 0iD/30i系统,设定CNC参数#8131.0/HPG=1以激活手轮进给功能;而FANUC 18/18i/0iA/0iB/0iC系统的CNC参数为#9920.2,FANUC 0C/0D系统的CNC参数为#900.2。当机床运行模式开关置于手轮状态时,屏幕的左下角显示HND,且模式选择信号为G0043.0~G0043.2(FANUC 18/18i/0i/30i系统)或G0122.0~G0122.2(FANUC 0C/0D系统)。
3)MPG的手轮轴选择输入信号分别为X0035.2、X0035.3、X0035.4、X0035.5和X0035.6,经PMC逻辑后向CNC输出手轮轴选择信号HS1A~HS1D/G0018.0~G0018.3(第2个MPG的手轮轴选择信号为HS2A~HS2D/G0018.4~G0018.7,第3个MPG的手轮轴选择信号HS3A~HS3D/G0019.0~G0019.3)。表5-20所示为手轮轴选通信号的对照。
表5-20 手轮轴选通信号的对照
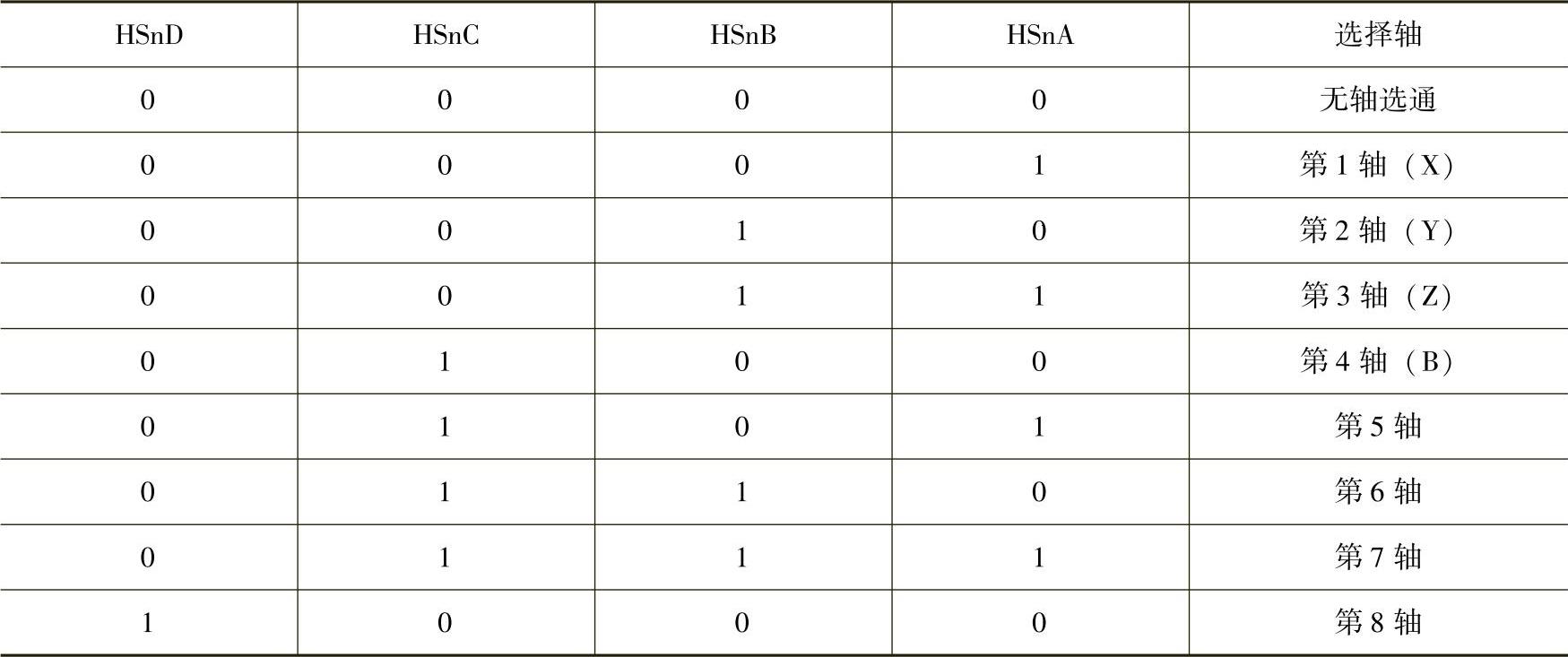
4)MPG的进给倍率输入信号为X0035.0和X0035.1,经PMC逻辑后向CNC输入手轮倍率信号MP1/G0019.4和MP2/G0019.5;同时设定手轮任意倍率的CNC参数#7113/Xm=100和#7114/Xn=1000;参数#7102.0/HNGx=0使MPG旋转方向与伺服轴进给方向一致,即顺时针旋转。表5-21所示为手轮倍率选通信号的对照。
HM1250卧式加工中心手摇脉冲发生器控制梯形图见图5-142。
表5-21 手轮倍率选通信号的对照
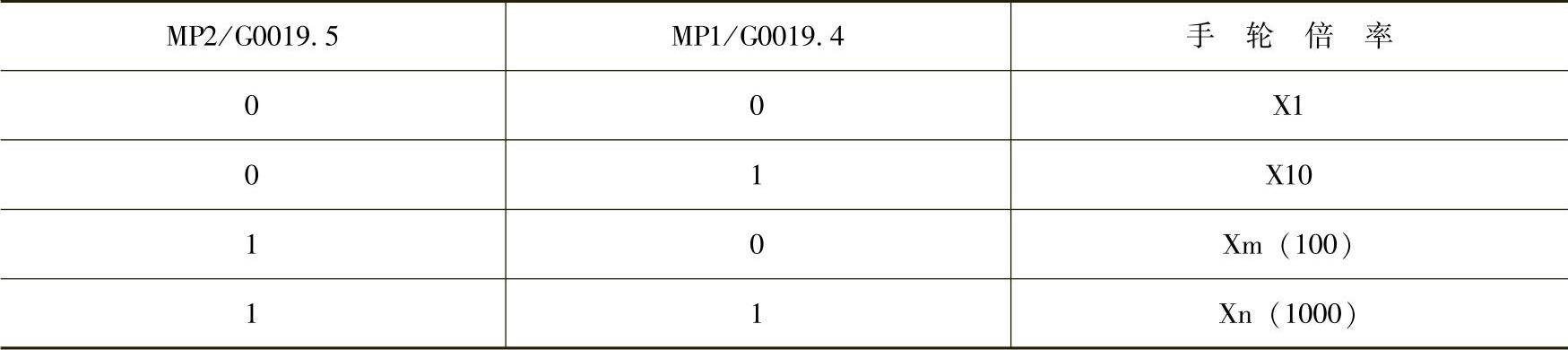
6.轴互锁控制
为避免操者误操作而使伺服轴和主轴、刀具、夹具之间的动作发生干涉等,导致工件自机床上掉下、刀具撞工作台等事故出现,特需要编写一些特殊情况下的互锁处理,并采用CNC系统专用的互锁信号控制。FANUC系统的互锁处理信号包含全轴互锁信号G008.0(当∗IT=0时PMC向CNC输入全轴互锁信号,禁止所有伺服轴移动)、各轴互锁信号G0130(当∗ITn=0时PMC向CNC输入第n伺服轴互锁信号,禁止其移动;通常1为X轴,2为Y轴,3为Z轴,4为B轴)、各轴正方向互锁信号G0132.0~G0132.3/+MIT1~+MIT4(当+MITn=1时第n伺服轴正方向被互锁,禁止其正方向移动但负方向可移动;T系列为X0004.2/+MIT1和X0004.4/+MIT2)、各轴负方向互锁信号G0134.0~G0134.3/-MIT1~-MIT4(当-MITn=1时第n伺服轴负方向被互锁,禁止其负方向移动但正方向可移动;T系列为X0004.3/-MIT1和X0004.5/-MIT2)、T系列的启动锁住信号G0007.1/STLK(为1时PMC相CNC发出启动锁住信号,禁止所有轴移动)等。以上互锁信号可由CNC参数#3003进行激活控制。

#5(DEC)0:参考点返回操作的减速信号(∗DEC1~∗DEC5)为0的情况下减速;
1:参考点返回操作的减速信号(∗DEC1~∗DEC5)为1的情况下减速。
#4(DAU)0:#3003.3/DIT=0时,各伺服轴方向互锁信号(±MITn)仅手动运行有效,自动运行无效;
1:#3003.3/DIT=0时,各伺服轴方向互锁信号(±MITn)在手动运行和自动运行情况下均有效。
#3(DIT)0:各伺服轴方向互锁信号(±MITn)有效;
1:各伺服轴方向互锁信号(±MITn)无效。
#2(ITX)0:各伺服轴互锁信号(∗ITn)有效;
1:各伺服轴互锁信号(∗ITn)无效。
#(ITL)0:全轴互锁信号(∗IT)有效;
1:全轴互锁信号(∗IT)无效。
除以上互锁信号外,数控机床还设有机床锁住信号(机床操作面板上增设机械锁住按钮)。当机床锁住信号有效后,CNC不再向伺服放大器发送移动指令脉冲,机床不再移动;同时CNC根据指令更新各伺服轴绝对坐标的显示(见图5-143),如同机床移动时的状态。使用机床锁住功能,可判断程序执行的轨迹是否正确;但机床锁住会使实际位置与当前绝对坐标显示值不相符,故恢复正常加工前应校准当前位置。FANUC系统的机床锁住信号包含全轴机床锁住信号G0044.1/MLK,各伺服轴机床锁住信号G0108.0~G0108.4/MLKn(n为伺服轴号,n=1~4),辅助功能锁住信号G0005.6(当AFL=1时,CNC不输出M、S、T代码信号,但不限制CNC专用M代码的输出)。
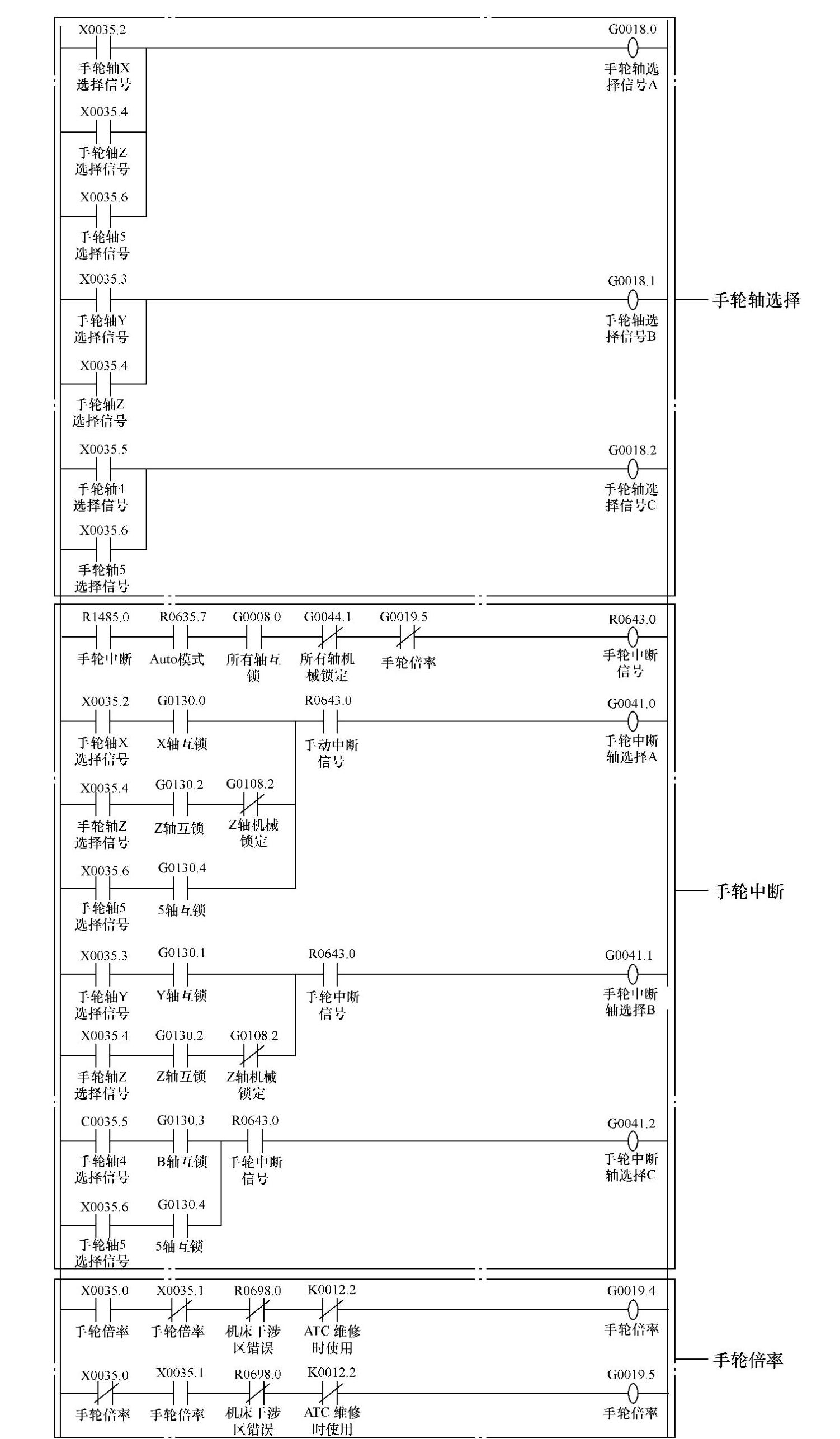
图5-142 HM1250卧式加工中心手摇脉冲发生器控制梯形图
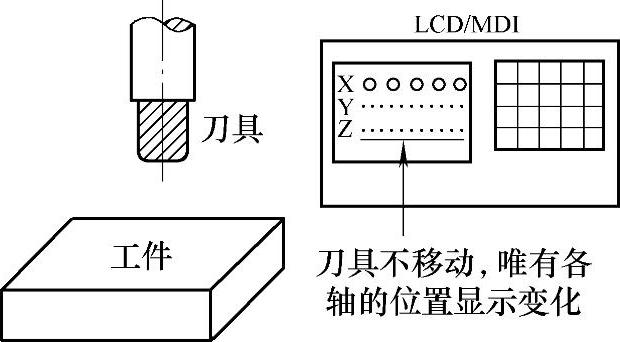
图5-143 机床锁住状态示意图
下面以TMV1100A立式加工中心(FANUC0iMC系统)为例,介绍其互锁信号和机械锁住信号的处理,该机床Z轴、B轴互锁控制框图见图5-144和图5-145。轴互锁控制梯形图中(见图5-146),保持型继电器K0002.6=1使刀具自动测量功能有效,K0005.5=0以实时显示轴互锁信息(1为启动后显示),K0015.7=1使刚性攻螺纹保持有效,K0023.0=0为执行M06自动换刀时X轴、Y轴和滑台进行互锁。
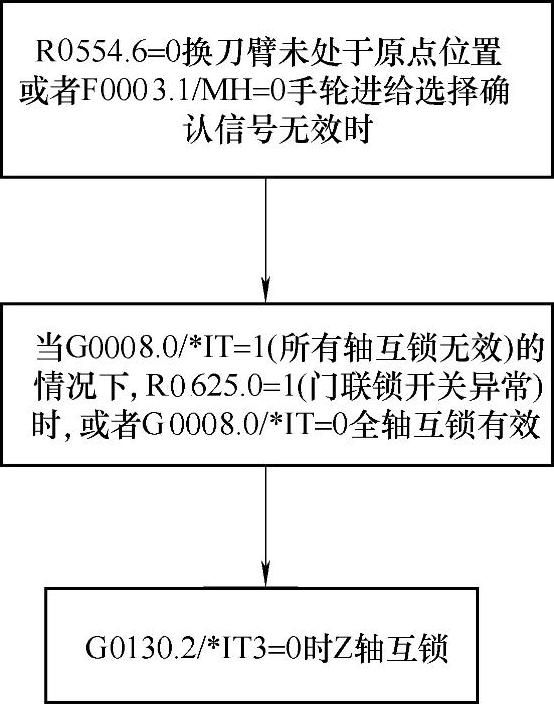
图5-144 Z轴互锁控制框图
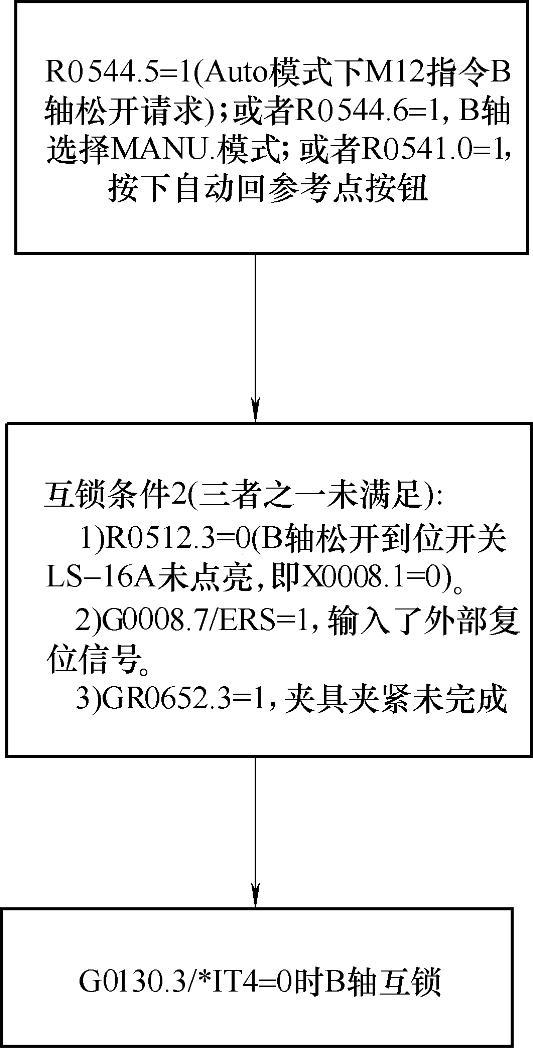
图5-145 B轴互锁控制框图
7.操作引起伺服轴不动作的常见故障分析
(1)机床手动(JOG)操作和自动(MEM)操作均无法执行当机床手动(JOG)操作和自动(MEM)操作均无法执行时,可通过查看CRT/LCD上的位置坐标是否变化来查找故障原因(见图5-147)。
1)位置坐标显示(相对、绝对、机械坐标)不变时的故障原因及处理方法。
①系统运行模式选择不对:可通过图5-147位置画面中运行模式选择状态查看是否显示JOG或MEM,也可通过PMCDGN诊断画面的STATUS状态子画面查看方式选择信号G0043.0/MD1、G0043.1/MD2和G0043.2/MD4的状态来判断。若状态信号不正确,则可能为运行模式开关不良或其断线故障。
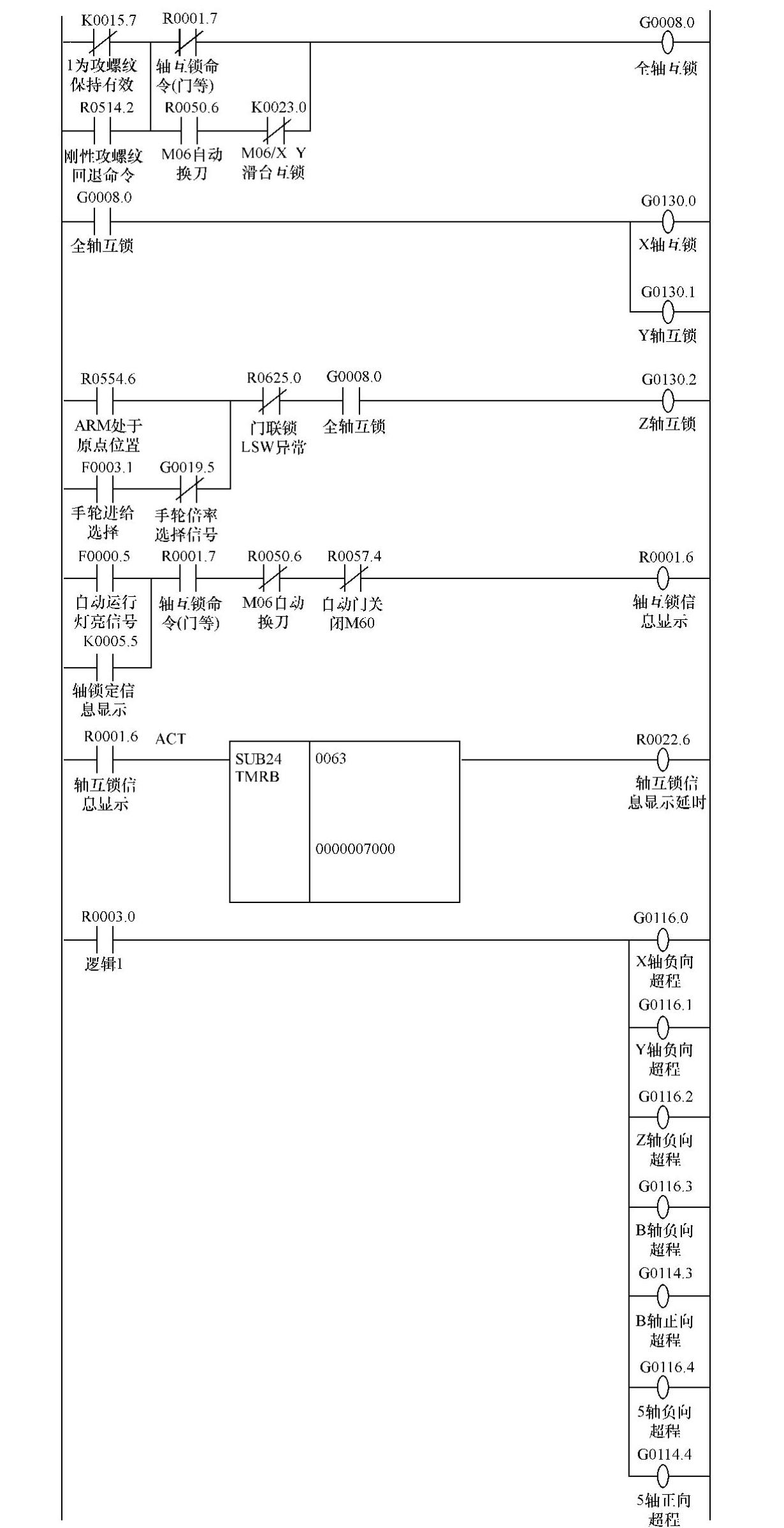
图5-146 TMV1100A立式加工中心轴互锁控制梯形图
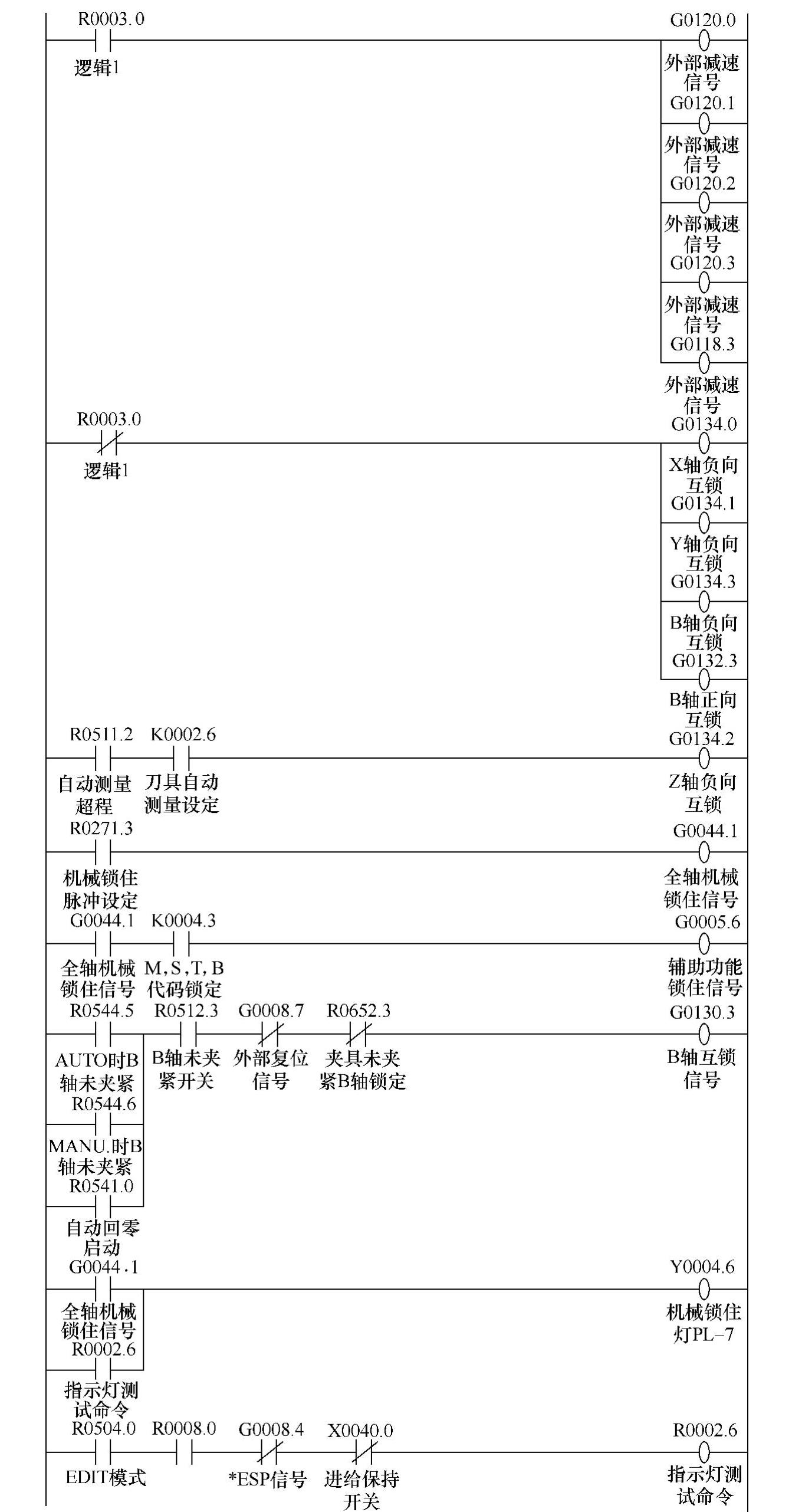
图5-146 TMV1100A立式加工中心轴互锁控制梯形图(续)
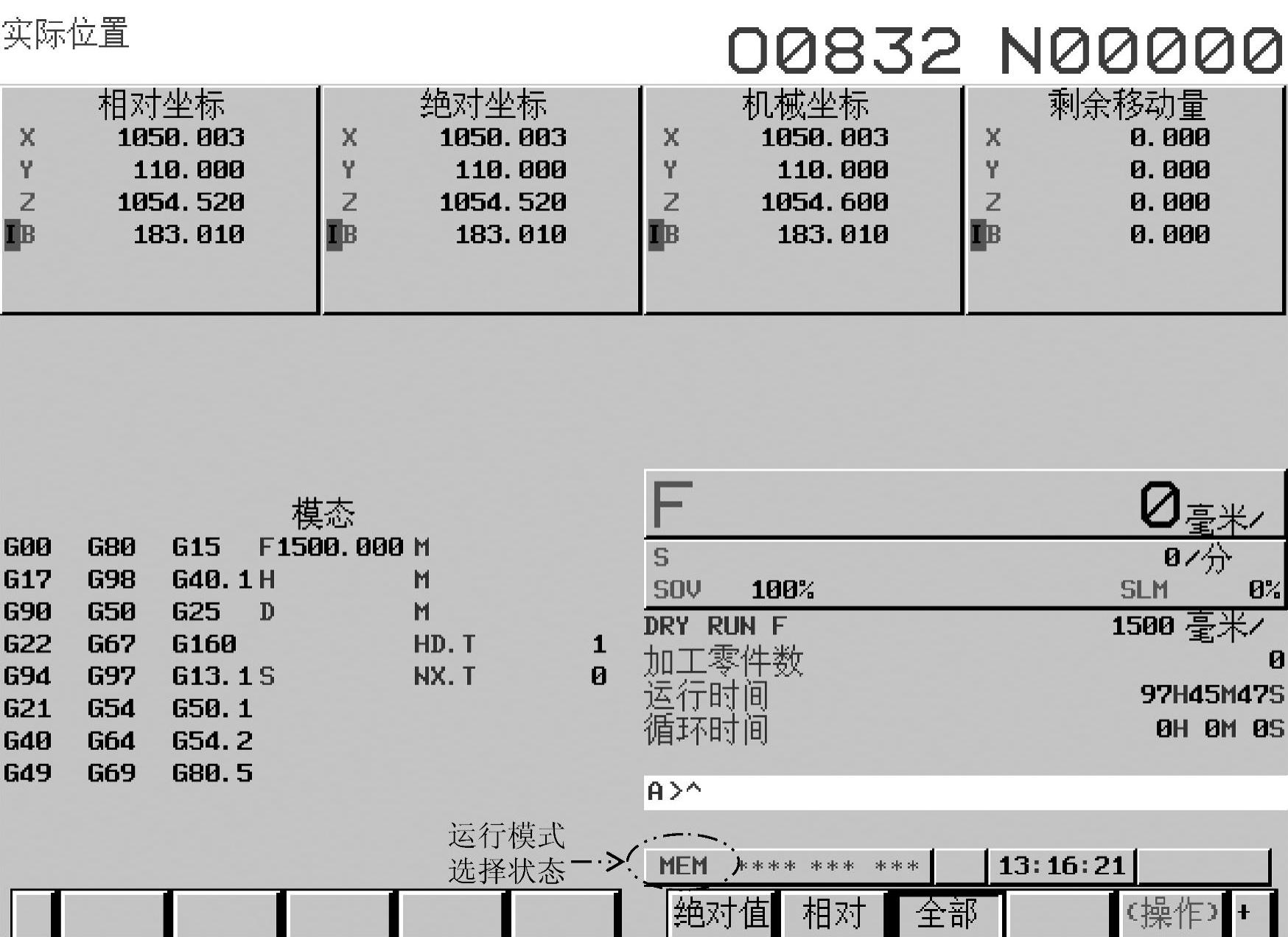
图5-147 HM1250卧式加工中心(FANUC31iMA系统)的位置画面
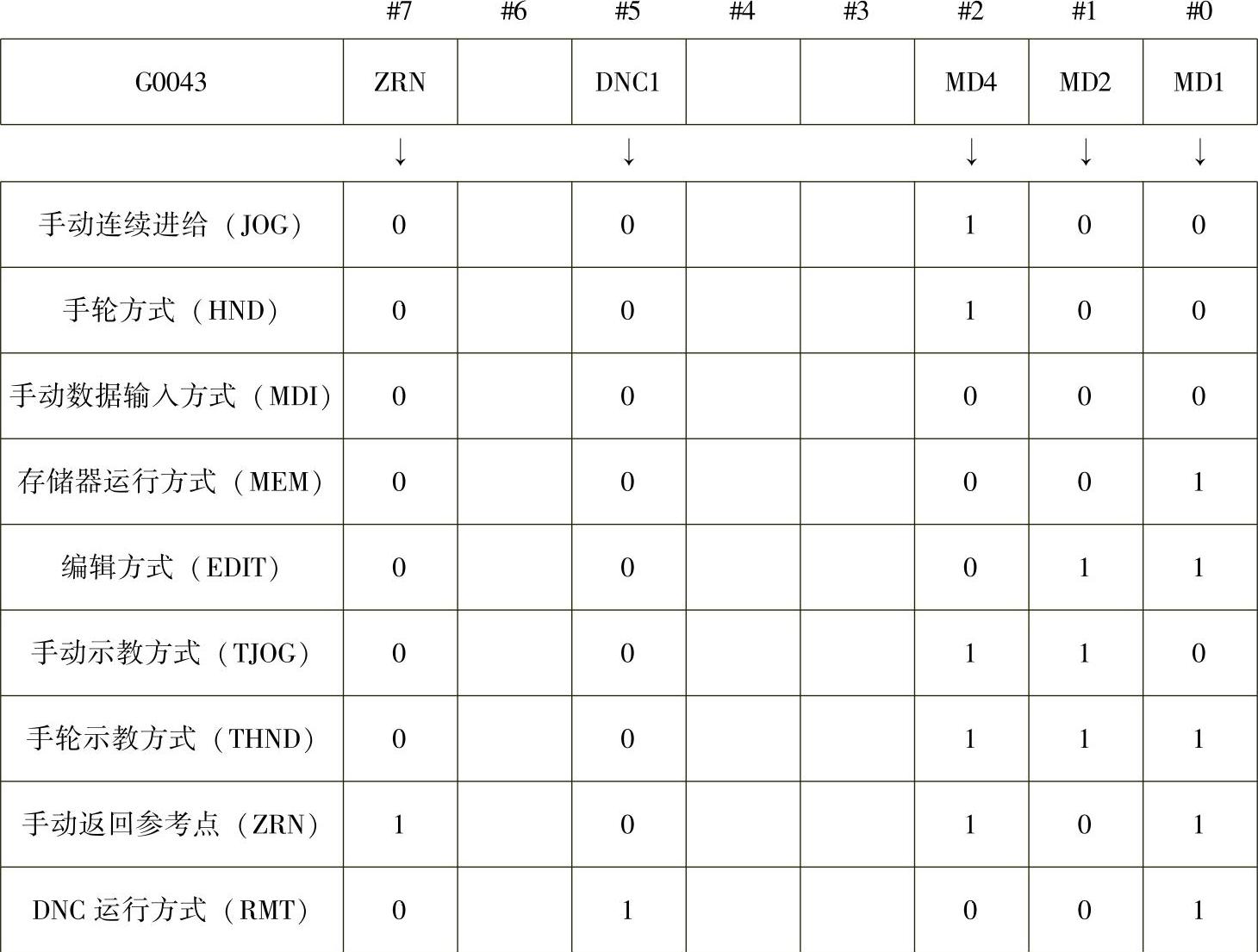
②系统处于急停状态(屏显EMG报警):通过PMCLAD梯形图显示画面查看G0008.4/∗ESP=0(机床正常时为1)的原因(G0008.4信号逻辑见图5-148)。
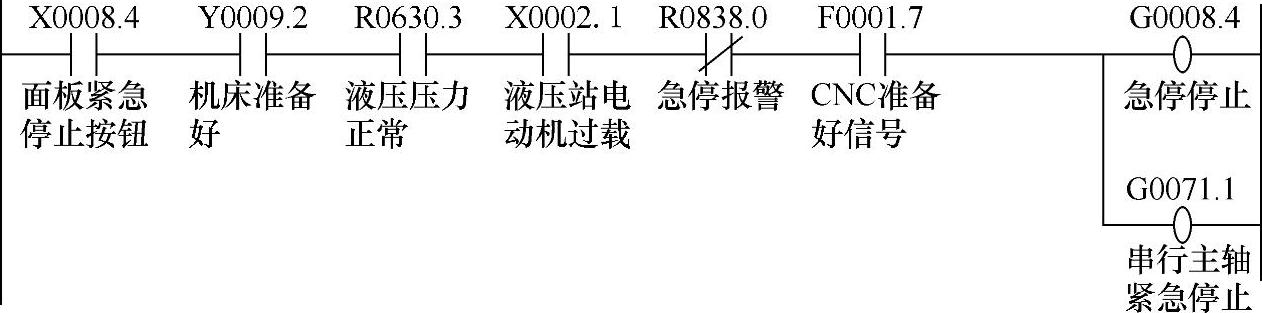
图5-148 HM1250卧式加工中心(FANUC 31iMA系统)的G0008.4信号逻辑
③机床复位信号被接通:外部复位信号G0008.7/ERS=1或MDI键盘的[RESET]键起作用,使F0001.1/RST=1。
④系统轴互锁信号被接通:可通过系统诊断画面(按面板[SYSTEM]功能键→[DGN]软键即可显示画面)的诊断号005 INTERLOCK/START LOCK是否置1进行判断,若诊断号005置1,则说明系统输入了轴互锁(禁止轴移动)启动信号。此时可借助PMCLAD梯形图显示画面查看全轴互锁信号G0008.0/∗IT=0和各伺服轴互锁信号G130/∗ITn=0(n为伺服轴号)的原因,详见第5.4.6节中的“轴互锁控制”。
⑤手动(JOG)进给速度倍率为0:可通过系统诊断画面的诊断号013 JOG FEEDRATE OVERRIDE0%是否置1来判断,若诊断号013置1,则说明JOG倍率为0。也可借助PMCDGN诊断画面下的STATUS状态子画面查看手动进给速度倍率信号G10(∗JV0~∗JV7)和G11(∗JV8~∗JV15)的状态,当倍率处于F0%挡时,G10、G11的全部位为1或0。大多数原因为进给倍率开关位置不对,详见第5.4.6节中的“手摇脉冲发生器的控制”。
2)位置坐标显示(相对、绝对、机械坐标)变化时的故障原因及处理方法。故障原因为机床输入了伺服轴的机床锁住信号,可借助PMCLAD梯形图显示画面查看全轴机床锁住信号G0044.1/MLK=1。各伺服轴机床锁住信号G0108.0~G0108.4/MLKn=1(n为伺服轴号,n=1~4)的原因详见第5.4.6节中的“轴互锁控制”。
(2)机床手动(JOG)操作不正常而自动(MEM)操作正常
1)系统运行模式选择不对:可通过图5-147位置画面中的运行模式选择状态查看是否显示JOG,也可PMCDGN诊断画面的STATUS状态子画面查看方式选择信号G0043.0/MD1、G0043.1/MD2和G0043.2/MD4的状态来判断。若状态信号不正确,则可能为运行模式开关不良或其断线故障。
2)进给轴方向选择信号未输入:借助PMCDGN诊断画面的STATUS状态子画面查看进给轴正向选择信号G0100.0/+JX、G0100.1/+JY、G0100.2/+JZ、G0100.3/+JB、G0100.4/+J5TH和轴负向选择信号G0102.0/-JX、G0102.1/-JY、G0102.2/-JZ、G0102.3/-JB、G0102.4/-J5TH的状态,当有一位为1时,相应进给轴方向选择被输入。
3)JOG进给速度参数设定不正确:FANUC 18/18i/0i/30i系统CNC参数#1423(伺服轴JOG进给速度)被设定为0。
4)系统轴互锁信号被接通:借助系统诊断画面的诊断号005 INTERLOCK/STARTLOCK是否置“1”判断,若诊断号005置1,则说明系统输入了轴互锁(禁止轴移动)启动信号。此时可借助PMCLAD梯形图显示画面查看全轴互锁信号G0008.0/∗IT=0和各伺服轴互锁信号G130/∗ITn=0(n为伺服轴号,n=1~8)的原因,详见第5.4.6节中的“轴互锁控制”。
(3)机床手轮(MPG)操作不正常而自动(MEM)操作正常
1)系统运行模式是否处于手轮(MPG)状态:可通过图5-147位置画面中的运行模式选择状态查看是否显示HND,也可通过PMCDGN诊断画面的STATUS状态子画面查看方式选择信号G0043.0/MD1、G0043.1/MD2和G0043.2/MD4的状态来判断。若状态信号不正确,则可能为运行模式开关不良或其断线故障。
2)手轮轴选择信号未输入:借助PMCDGN诊断画面的STATUS状态子画面查看手轮轴选择信号G0018.0~G0018.3/HS1A~HS1D(第2、3个MPG的手轮轴选择信号分别为G0018.4~G0018.7/HS2A~HS2D和G0019.0~G0019.3/HS3A~HS3D)的状态,若信号状态为0,则信号未接通。可能原因为手轮轴选择开关不良及断线故障。
3)手轮自身及接线故障:按图5-149所示的接线图检查手摇脉冲发生器连接电缆是否断线或短路,以及借助示波器检查手摇脉冲发生器输出信号的波形是否正常(见图5-150,ON与OFF的比例,HA与HB的相位差)。
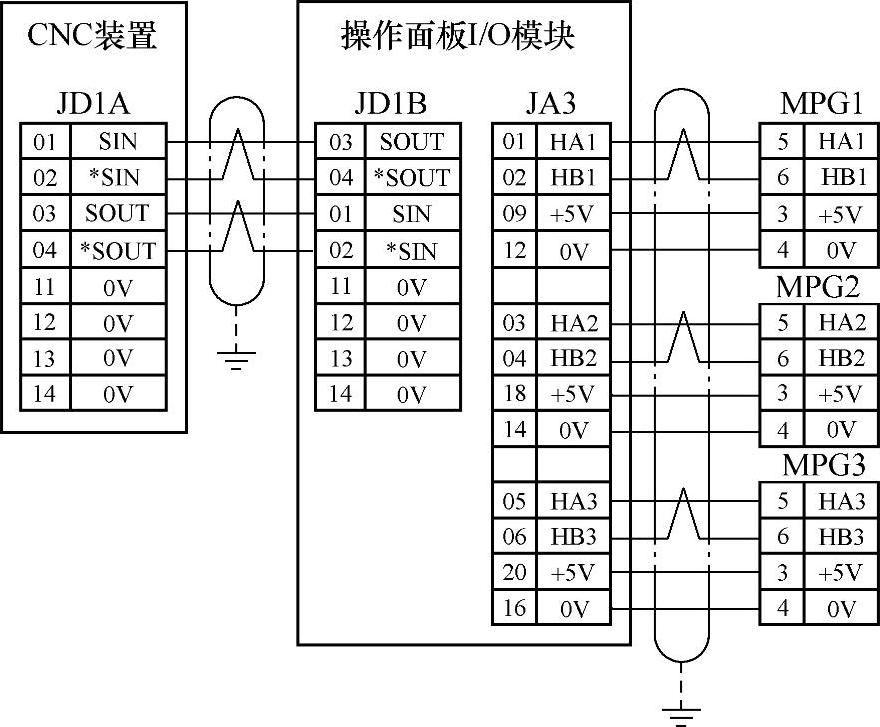
图5-149 手摇脉冲发生器的接线图
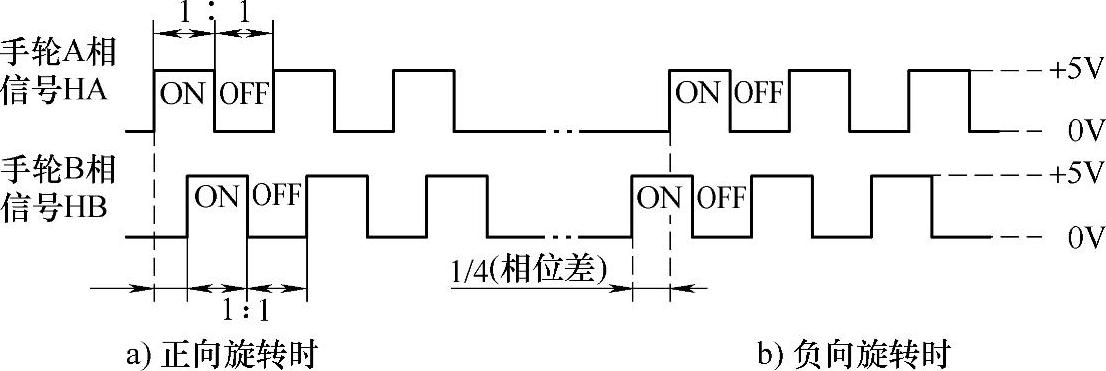
图5-150 手摇脉冲发生器输出信号的波形
4)系统功能包参数设定不正确:对于FANUC 0iD/30i系统,设定CNC参数#8131.0/HPG=1以激活手轮进给功能;而FANUC 18/18i/0iA/0iB/0iC系统的CNC参数为#9920.2,FANUC 0C/0D系统的CNC参数为#900.2。
(4)自动(MEM)操作无效而手动(JOG)操作正常
1)自动运行不能启动(循环启动灯不亮)。
①系统运行模式选择不对:可通过图5-147位置画面中的运行模式选择状态查看是否显示MEM存储器运行方式、RMT远程运行方式或MDI手动数据输入方式,也可通过PMCDGN诊断画面的STATUS状态子画面查看方式选择信号G0043.0/MD1、G0043.1/MD2和G0043.2/MD4的状态来判断。若状态信号不正确,则可能为运行模式开关不良或其断线故障。
②自动运行启动信号未输入:借助PMCLAD梯形图显示画面或PMCDGN诊断画面的STA-TUS状态子画面查看自动运行启动信号G0007.2/ST的状态。当按下操作面板的自动运行启动按钮时,G0007.2/ST=1;松开此按钮时,G0007.2/ST=0。若自动运行启动信号未输入,则可能为该按钮损坏及其接线不良、系统I/O接口或CNC主板不良等。
③自动运行暂停(进给暂停)信号被输入:借助PMCLAD梯形图显示画面或PMCDGN诊断画面的STATUS状态子画面查看自动运行暂停(进给暂停)信号G0008.5/∗SP的状态。若G0008.5/∗SP=0,说明系统输入了进给暂停信号。故障原因可能为机床进给暂停按钮自身损坏或其接线不良。
2)自动运行启动中(循环启动灯点亮)。
①机床进给速度倍率为0%:可通过系统诊断画面的诊断号004 FEEDRATE OVERRIDE0%是否置1判断,若该信号置1,则说明进给速度倍率为0;也可借助PMCDGN诊断画面下的STA-TUS状态子画面查看进给速度倍率信号G12(FV0~FV7)的状态,当倍率处于F0%挡时,G12的全部位为1或0。故障原因可能为进给倍率旋钮自身损坏及其接线不良、系统I/O接口或CNC主板不良等。
②系统轴互锁信号被接通:可通过系统诊断画面的诊断号005 INTERLOCK/START LOCK是否置1来判断,若诊断号005置1,则说明系统输入了轴互锁(禁止轴移动)启动信号。此时可借助PMCLAD梯形图显示画面查看全轴互锁信号G0008.0/∗IT=0和各伺服轴互锁信号G0130/∗ITn=0(n为伺服轴号)的原因,详见第5.4.6节中的“轴互锁控制”。
③CNC等待主轴速度达到信号(实际转速未达到程序中指令的主轴转速):可通过系统诊断画面的诊断号006 SPINDLE SPEED ARRIVAL CHECK是否置1来判断,若诊断号006置1,则说明CNC等待主轴速度信号G0029.4/SAR的输入。此时可借助PMCLAD梯形图显示画面查看主轴速度到达信号G0029.4/SAR是否被定义及逻辑条件是否满足,同时检查与主轴速度到达信号SAR对应的CNC参数#3708.0(1为检测SAR,0为不检测)。故障原因可能为主轴位置编码器不良、CNC参数设定错误等。
④正在执行程序中的辅助功能M/S/T/B指令(等待结束信号):先通过CNC参数#3001.7/MHI确定辅助功能接口的种类。若#3001.7=0,则M/S/T/B功能为普通接口,即M/S/T/B的选通脉冲信号和结束信号之间的交换为通常方式;若#3001.7=1,则M/S/T/B功能为高速接口,即M/S/T/B的选通脉冲信号和结束信号之间的交换为高速方式。
#3001.7=0选择普通接口时,若系统的辅助功能结束信号G0004.3/FIN由1变为0,则M/S/T/B辅助功能执行完毕,CNC读取下一个程序段;#3001.7=1选择高速接口时,需达到下述状态时辅助功能结束。
8.返回参考点的控制及故障
(1)数控机床返回参考点的必要性机床坐标系是数控机床固有的坐标系,该坐标系的原点称为机械参考点(或机床原点),它是机床制造和加工的基准点,属于1个固定不变的点。而电气参考点是以机床位置检测装置发出的栅点信号或零标志信号确立的参考点,为使其与机床原点重合,需将电气参考点到机床原点的距离用1个参考点偏移量参数进行设置,这个重合的点即为机床参考点(简称参考点)。数控机床通过返回参考点来确定机床原点的具体位置,从而建立1个正确的机床坐标系,这就是数控机床返回参考点的目的。

#3(TFIN) T功能结束信号
#2(SFIN) S功能结束信号
#O(MFIN) M功能结束信号
说明:
第2M功能结束信号为G004.4/MFIN2;
第3M功能结束信号为G004.5/MFIN3;
第2M、3M功能仅在CNC参数#3404.7/M3B=1时有效,即在1个程序段内最多指定3个M代码。
#7和#4(BFIN)第2辅助功能结束信号(未明确M系列或T系列的,表示共用参数]

#3(TF) T功能选通脉冲信号
#2(SF) S功能选通脉冲信号
#0(MF) M功能选通脉冲信号
说明:
第2M功能选通脉冲信号为F008.4/MF2;
第3M功能选通脉冲信号为F008.5/MF3;
第2M、3M功能仅在CNC参数#3404.7/M3B=1时有效,即在1个程序段内最多指定3个M代码。
#7和#4(BF) 第2辅助功能选通脉冲信号(未明确M系列或T系列的,表示共用参数)
数控机床位置检测装置为绝对式编码器时,系统断电后依靠记忆电池(见图5-151)提供电源来记忆机床断电后位置的变化,上电时系统与位置检测装置进行数据交换并刷新数据,使机床坐标系的坐标值与机床实际位置保持一致,所以绝对式编码器数控机床开机后可以不执行返回参考点操作;而位置检测装置为增量式编码器时,由于系统记忆的坐标值为机床断电前的位置,与机床实际位置有可能不一致,所以增量式编码器数控机床在首次开机时、按下急停按钮又解除急停后以及机床锁住进行程序校验后,必须执行返回参考点的操作。
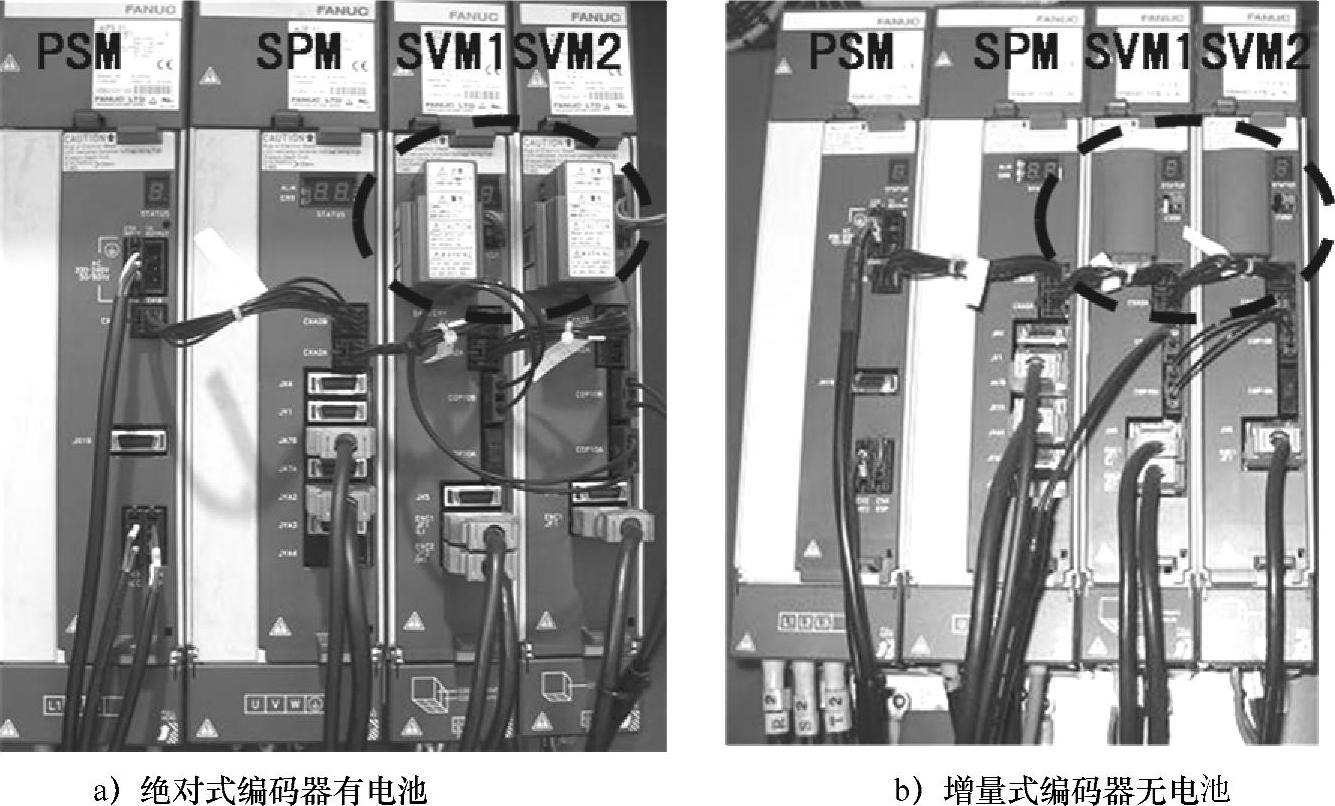
图5-151 数控机床位置检测装置的记忆电池
下面以LC34×3000卧式数控车床(FANUC 18TC系统)为例,说明数控机床执行返回参考点操作确立机床坐标系的过程(见图5-152)。该机床的原点设在主轴卡盘前端面的轴心上,机床第1参考点设在电动刀塔当前装有镗孔刀座端面的轴心上,它与机床原点的Z向距离为LZ=500mm、X向距离为2LX=260mm(采用直径编程)。执行手动返回或程序中G28指令自动返回参考点操作后的相对坐标为机床坐标系(以机床原点为基准建立的坐标系)下机床第1参考点到机床原点的增量坐标值(各轴坐标偏移值为0)。相对坐标仅用作各伺服轴当前位置的显示,将各轴的相对坐标复位为0或置为任意值,不影响数控机床的自动运行和加工程序的执行;绝对坐标为机床坐标系下机床第1参考点的绝对坐标值(各轴坐标偏移值为0),加工过程中显示程序绝对指令选定坐标系的坐标值;机械坐标为机床参考坐标系(以机床参考点为基准建立的坐标系)下机床第1参考点的绝对坐标值。

图5-152 LC34×3000卧式数控车床(FANUC 18TC系统)返回参考点的过程
当机床参考点用作自动换刀位置时,执行返回参考点操作可使刀具非常容易地移动至该位置。通过CNC参数#1240~#1243可在机床坐标系中分别设定4个参考点。当参数#1240=0时,机床第1参考点与机床原点重合。另外,在机床坐标系中通过CNC参数#1221~#1226可分别设定6个工件坐标系,对应的指令代码为G54~G59;同时这6个工件坐标系的工件零点可由CNC参数#1220或坐标系设定画面下00(EXT)组号(按[OFFSET/SETTING]功能键→[工件]软键便显示该画面)进行变更。
(2)数控机床返回参考点的控制方法按照位置检测装置检测参考点信号方式的不同,数控机床返回参考点的控制方法一般有磁开关法和栅格法两种。其中,磁开关法返回参考点是在开环伺服控制系统的机械本体上安装磁铁和磁感应参考点开关(或接近开关),当磁感应开关检测到参考点信号后,伺服电动机便立即停转,该停止点即为机床参考点。磁开关法的机床参考点位置会伴随着伺服电动机速度的变化而成比例的漂移,通常参考点偏离正确位置0.2~0.5mm。而栅格法返回参考点采用位置检测装置上每1转出现1次的栅格信号(又称1转信号PCZ)来确定机床参考点,只要接近参考点的速度小于某一固定值,伺服电动机便总是停止于同一点,也就是说,返回参考点后机床参考点的保持性好。因此,现代数控机床几乎全部采用栅格法返回机床参考点。目前,数控机床栅格法返回参考点的控制形式有增量编码器有挡块控制、绝对编码器有挡块控制和绝对编码器无挡块控制3种。下面分析FANUC 18/18i/0i/30i系统的增量编码器有挡块栅格法返回参考点的控制原理和绝对编码器无挡块栅格法返回参考点的控制原理。
1)增量编码器有挡块栅格法返回参考点的控制原理(见图5-153)。
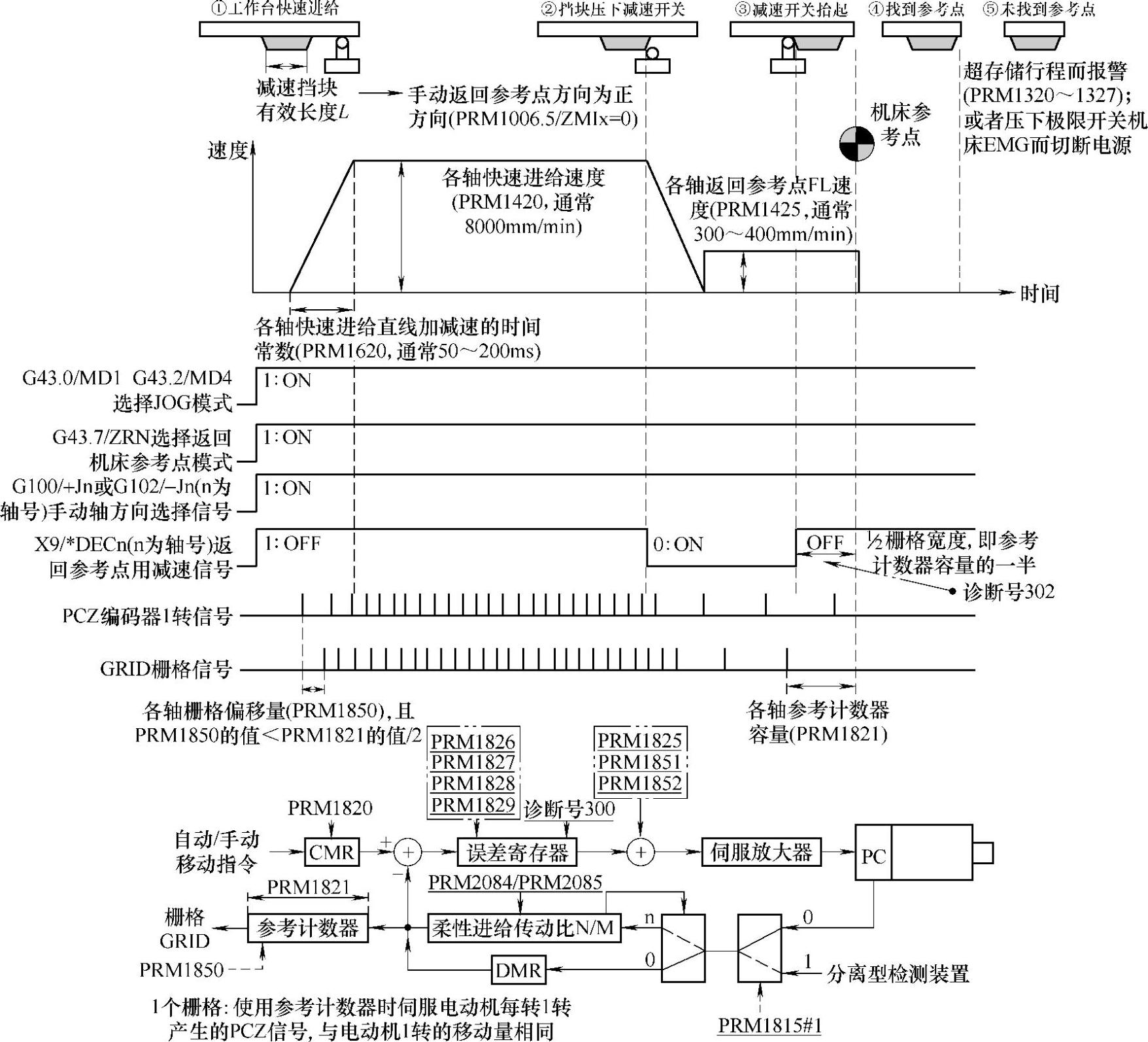
图5-153 FANUC 18/18i/0i/30i系统增量编码器有挡块栅格法返回参考点的控制原理图
①设定CNC参数#1002.1/DLZ=0,使机床所有轴采用有挡块式返回参考点;或设定参数#1005.1/DLZx=0(x表示可选轴),使机床被选轴为有挡块式返回参考点。

#3(AZR) 0:G28自动返回参考点与手动返回参考点相同,均为有挡块式;
1:未建立参考点之前执行G28自动返回参考点时,出现PS0304报警。
#1(DLZ) 0:所有轴采用有挡块式返回参考点(增量式);
1:所有轴使用无挡块式返回参考点,不能用于具有Cs轮廓控制或主轴准停功能的系统。
#0(JAX) 0:JOG进行、手动快进及手动返回参考点时,同时控制轴数为1轴;
1:JOG进行、手动快进及手动返回参考点时,同时控制轴数为3轴。
②设定CNC参数#1005.0/ZRNx=0,在未建立参考点时自动运行除G28(自动返回参考点)之外的轴移动指令时,系统发出PS0224返回参考点未结束报警,禁止伺服轴移动。

#3(HJZx) 0:已建立参考点后进行手动返回参考点时,继续有挡块式返回参考点控制
1:已建立参考点后进行手动返回参考点时,由参数#2.7/SJZ选择快速移动方式定位至参考点,而与减速挡块无关
#1(DLZx) 0:被设定伺服轴使用有挡块式返回参考点
1:被设定伺服轴使用无挡块式返回参考点,前提#1002.1/DLZ=0
#0(ZRNx) 0:未建立参考点时,自动运行除G28之外的轴移动指令时,系统发出PS0224报警(回参考点未结束),禁止伺服轴移动
1:不发出PS0224报警,允许伺服轴移动。
③设定CNC参数#1815.1/OPTx=0,采用内装型脉冲编码器进行位置检测;同时设定#1815.5/APCx=0,不使用绝对编码器作为位置检测装置。

#5(APCx) 0:不使用绝对位置编码器;
1:使用绝对位置编码器。
#4(APZx) 0:绝对位置编码器时,机械位置与绝对编码器的位置对应关系未建立;第1次调节或更换绝对位置编码器时,需将该参数设为0,机床断电重启,通过手动返回参考点等操作以设定绝对位置编码器的参考点,从而完成机械位置与绝对位置编码器之间的位置对应,此时该参数被自动置1。
1:绝对位置编码器时,机械位置与绝对编码器的位置对应关系已建立。
#2(DCLx) 0:分离型位置检测装置不使用带有参考标记或绝对地址原点的直线尺;
1:分离型位置检测装置使用带有参考标记或绝对地址原点的直线尺。
#1(OPTx) 0:采用内装式脉冲编码器作为位置检测装置;
1:采用分离型脉冲编码器或光栅尺作为位置检测装置。
④设定CNC参数#1240~#1243,依次为第1、2、3、4参考点在机床坐标系中的坐标值。参数#1240=0时,机床第1参考点与机床坐标系的原点重合。
⑤机床运行模式开关置JOG方式使G43(0,1,2)=(1,0,1)或TJOG方式使G43(0,1,2)=(0,1,1),同时将手动返回参考点选择信号G43.7/ZRN置1。

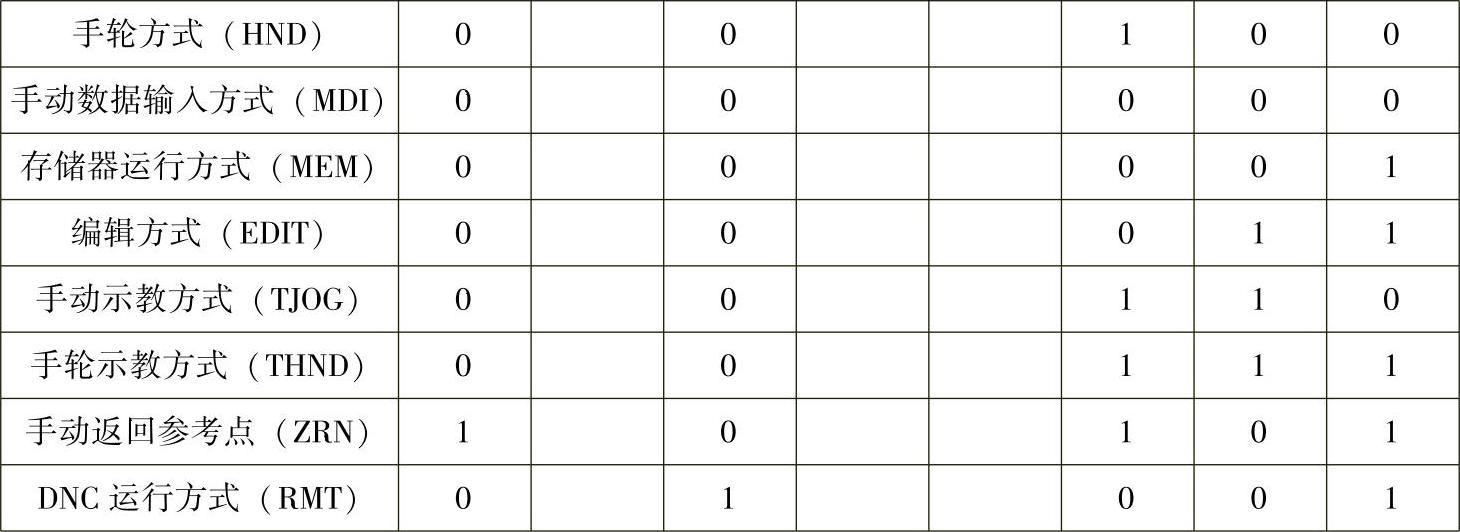
⑥在操作面板上选择待返回参考点的伺服轴方向键,使手动轴方向选择信号G100/+Jn=1或G102/-Jn=1(n为伺服轴号,n=1~8)。
⑦被选定的伺服轴带动工作台按既定方向快速进给移动,快速移动速度为CNC参数#1424的设定值;若被选定轴参数#1424=0,则快速移动速度为参数#1420的设定值与快速进给倍率F∗%挡的乘积。通常设定参数#1424=0mm/min、#1420=8000mm/min,返回参考点时的快速进给倍率置F100%挡(PMC地址G14.0/ROV1=0且G14.1/ROV2=0)。
⑧当接近参考点时,安装在机床上的减速开关被工作台上的减速挡块压下,使机床参考点减速信号X9/∗DECn(n为伺服轴号,n=1~8;参数#3006.0/GDC=0的前提下)由1变为0,此时该伺服轴的移动速度减为0mm/min;然后,机床便以固定的低速FL向参考点移动。通常,FL速度的设定参数#1425=300~400mm/min。

#0(GDC) 0:使用X9/∗DECn作为返回参考点的减速信号;
1:使用G0196外部减速开关信号。
⑨随着工作台向参考点方向移动,被压下的减速开关脱开,参考点减速信号X9/∗DECn再次变为1,机床以低速FL速度继续移动,直至到达第1个栅格点,再移动由参数#1850设定的栅格偏移量(又称参考点偏移量,且#1850中的数值不超过#1821设定值的一半)后便停止。此停止点就是机床的参考点。
⑩当确定坐标位置在参数#1826设定的到位宽度范围内时,也就是说,机械位置和指令位置的偏离(位置偏差量的绝对值)比参数#1826设定值还要小时,系统认为机械位置已到达指令位置,此时第1参考点返回结束信号F94/ZPn=1(第2、3、4参考点返回结束信号分别为F96/ZP2n、F98/ZP3n和F100/ZP4n)和参考点建立信号F120/ZRFn=1(n为伺服轴号,n=1~8),并由CNC传输至PMC。
(11)若CNC参数#1002.0/JAX=0(手动快速移动及手动返回参考点的同时控制轴数为单轴),则各轴需要分别执行返回参考点的操作;若参数#1002.0/JAX=1,则3个伺服轴(X/Y/Z)同时返回机床参考点。
(12)通常,利用CNC参数设定存储行程限位(软限位),监控参考点返回过程中各伺服轴是否出现超程报警(见表5-22);或者利用硬限位(极限开关)被压下使机床处于急停报警状态。
(13)借助系统诊断画面(按面板[SYSTEM]功能键→[DGN]软键即可显示画面)的诊断号302(自减速挡块脱离的位置至第1个栅格之间的距离)中的数值,进行减速挡块位置的微调。正常情况下,诊断号302显示的数值约等于1/2栅格宽度(参数#1821设定的参考计数器容量的一半),且多次重复返回参考点时诊断号302中的数值变化幅度不大,也就是说,机床参考点的位置稳定。当诊断号302显示的数值超过1/2个栅格时,得调整减速挡块的位置;当诊断号302显示的数值不超过1/2个栅格时,修改栅格偏移量参数#1850;当诊断号302中数值变化幅度大时,应考虑减速开关与减速挡块的接触太松或减速开关动作不良等故障因素。
表5-22 FANUC 18/18i/0i/30i系统与超程相关的报警
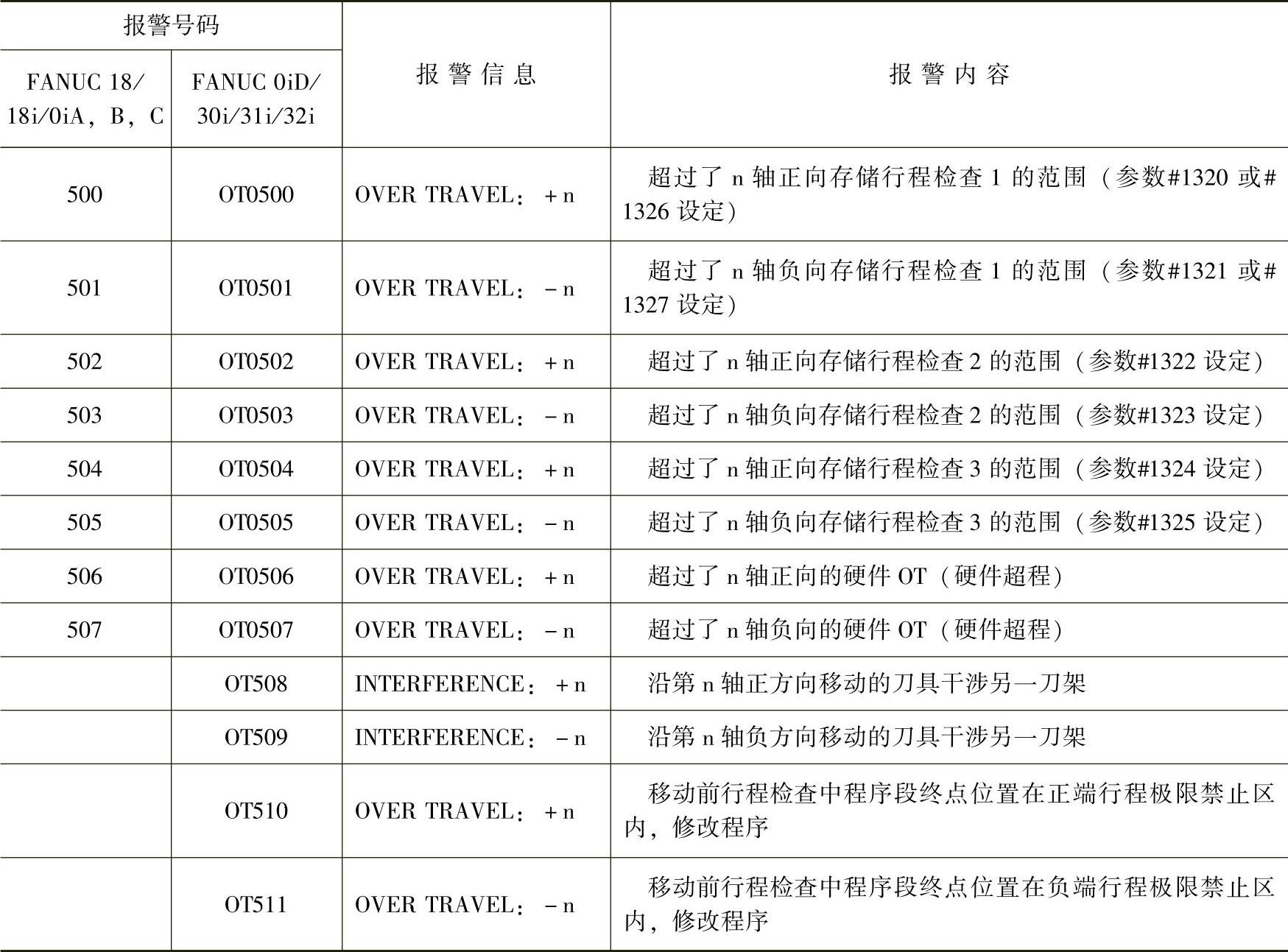
(14)减速挡块的有效长度L根据以下公式计算得出:

式中 V快——CNC参数#1420设定的快速进给速度(mm/min);
T1——参数#1620设定的快速进给直线加减速时间常数(ms);
T2——伺服加速时间(ms),且
;
30——经验得出的时间补偿量(ms);
1.2——计算值中包含20%的裕量。
若参数#1420=12000mm/min、#1620=100ms和
时,减速挡块的有效长度
,考虑日后可能会减小伺服的位置环增益,故确定减速挡块长度L=30~35mm。
(15)为方便读者更好地理解上述增量编码器有挡块栅格法返回参考点的控制原理,在此给出LC34×3100卧式数控车床(FANUC0iTC系统)返回参考点的辅助控制回路和I/O接口图(见图5-154)及PMC梯形图(见图5-155)。
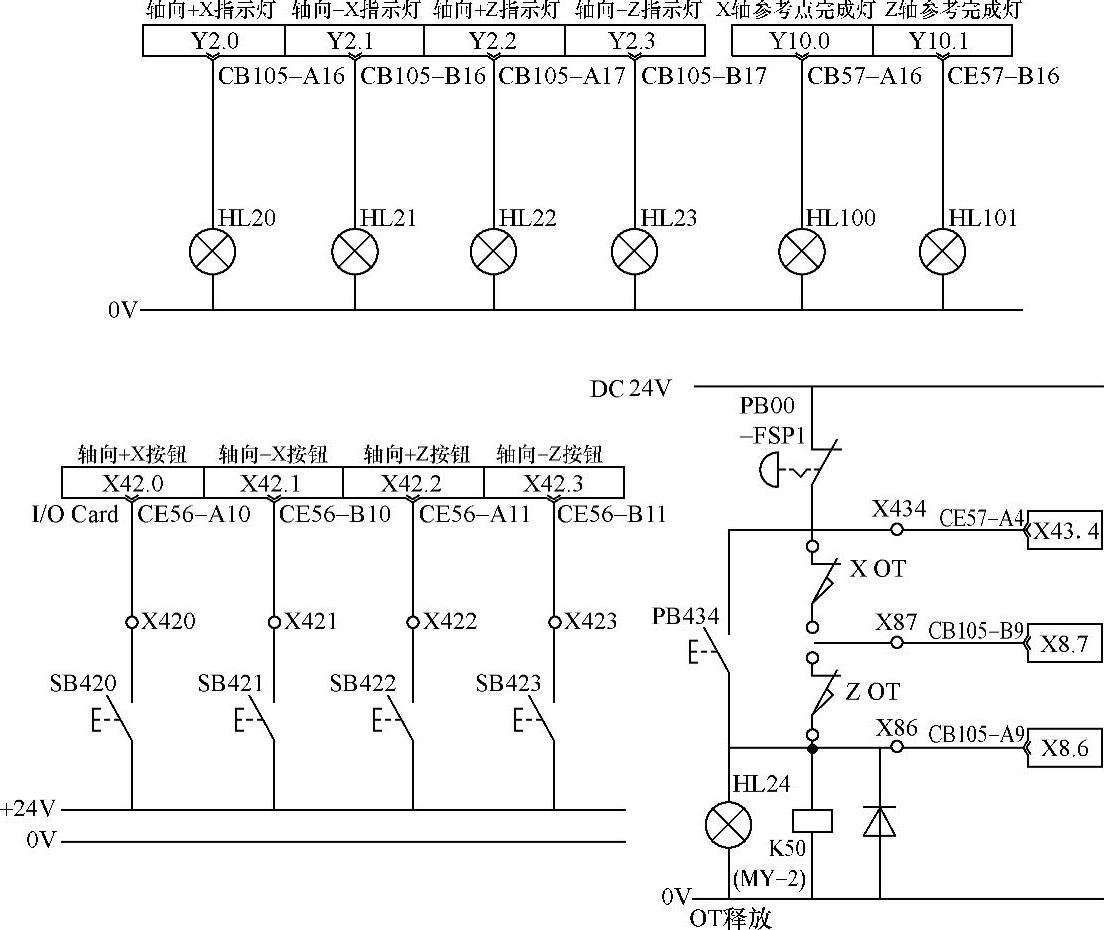
图5-154 LC34×3100卧式数控车床返回参考点的辅助控制回路和I/O接口图
2)绝对编码器无挡块栅格法返回参考点的控制原理(见图5-156)。
①设定CNC参数#1002.1/DLZ=1,使机床所有轴采用无挡块式返回参考点;或设定参数#1005.1/DLZx=1(x表示可选轴),使机床被选轴采用无挡块式返回参考点。
②设定CNC参数#1005.0/ZRNx=1,在未建立参考点时自动运行除G28(自动返回参考点)之外的轴移动指令时,系统不发出PS0224返回参考点未结束报警,允许伺服轴移动。
③设定CNC参数#1815.1/OPTx=1,采用内装型脉冲编码器进行位置检测;同时设定#1815.5/APCx=1,使用绝对编码器作为位置检测装置。
④设定CNC参数#1240~#1243,依次为第1、2、3、4参考点在机床坐标系中的坐标值;若设置为0,则机床第1参考点与机床坐标系的原点重合。
⑤机床运行模式开关置JOG方式,使G43(0,1,2)=(1,0,1);LCD上显示JOG。
⑥在操作面板上选择待返回参考点的伺服轴方向键,使手动轴方向选择信号G100/+Jn=1或G102/-Jn=1(n为伺服轴号,n=1~8);参数#1006.5/ZMIx=0时选择+Jn方向键,#1006.5/ZMIx=1时选择-Jn方向键。
⑦被选定的伺服轴带动工作台按既定方向手动进给至参考点附近(约数毫米前)停止,手动进给速度由CNC参数#1423设定(通常为4000mm/min)。
⑧更换运行模式开关为返回参考点方式,使G43.7/ZRN=1;LCD上显示REF。
⑨再次操作伺服轴的方向键,工作台以固定的低速FL向参考点位置移动(参数#1425设定FL速度通常为300~400mm/min)。
⑩当找到位置反馈装置上的第1栅格点后,再移动由该轴参数#1850设定的栅格偏移量(又称参考点偏移量,且#1850中的数值不超过#1821设定值的一半)后便停止。此停止点就是机床的参考点。
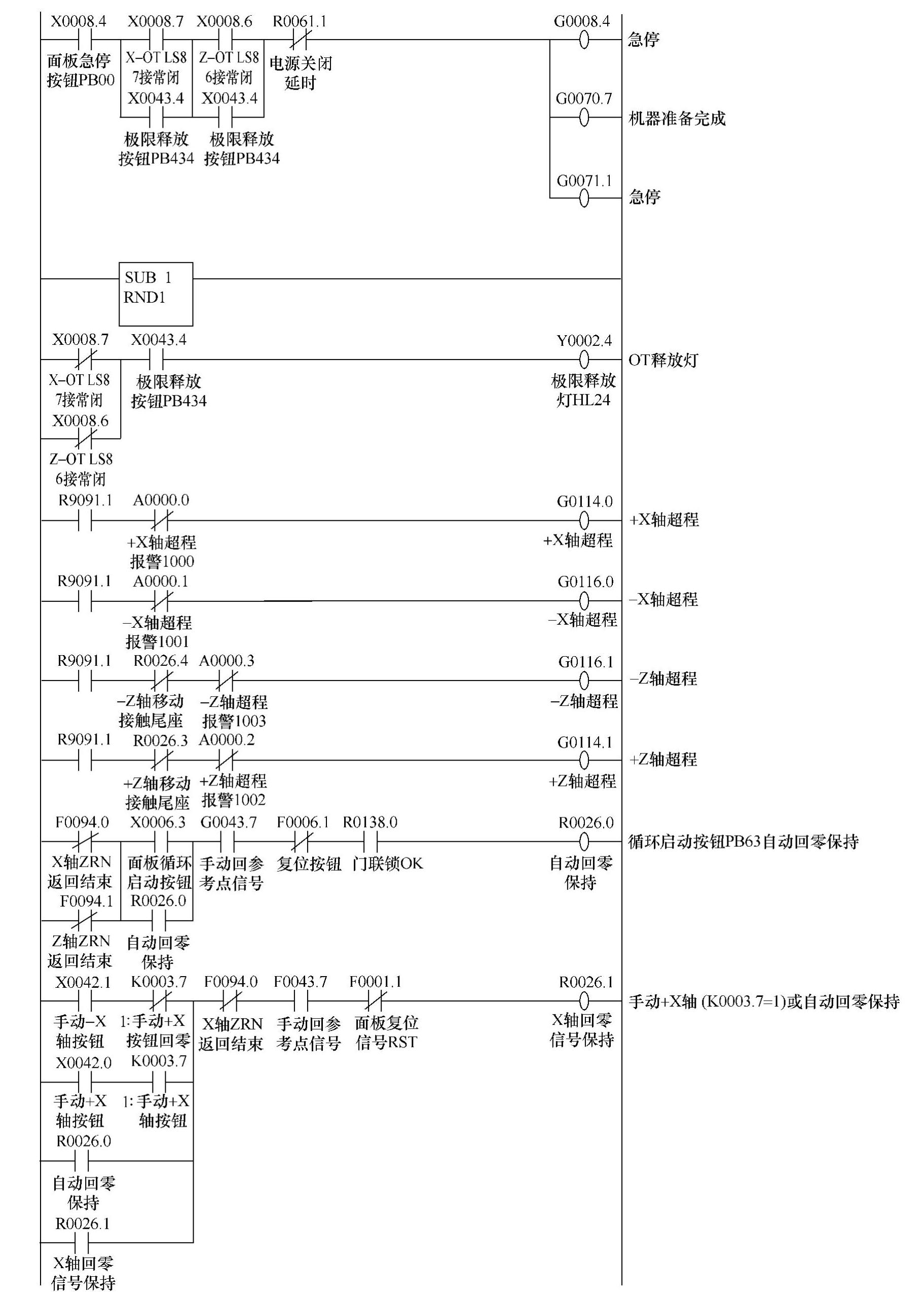
图5-155 LC34×3100卧式数控车床返回参考点的PMC梯形图
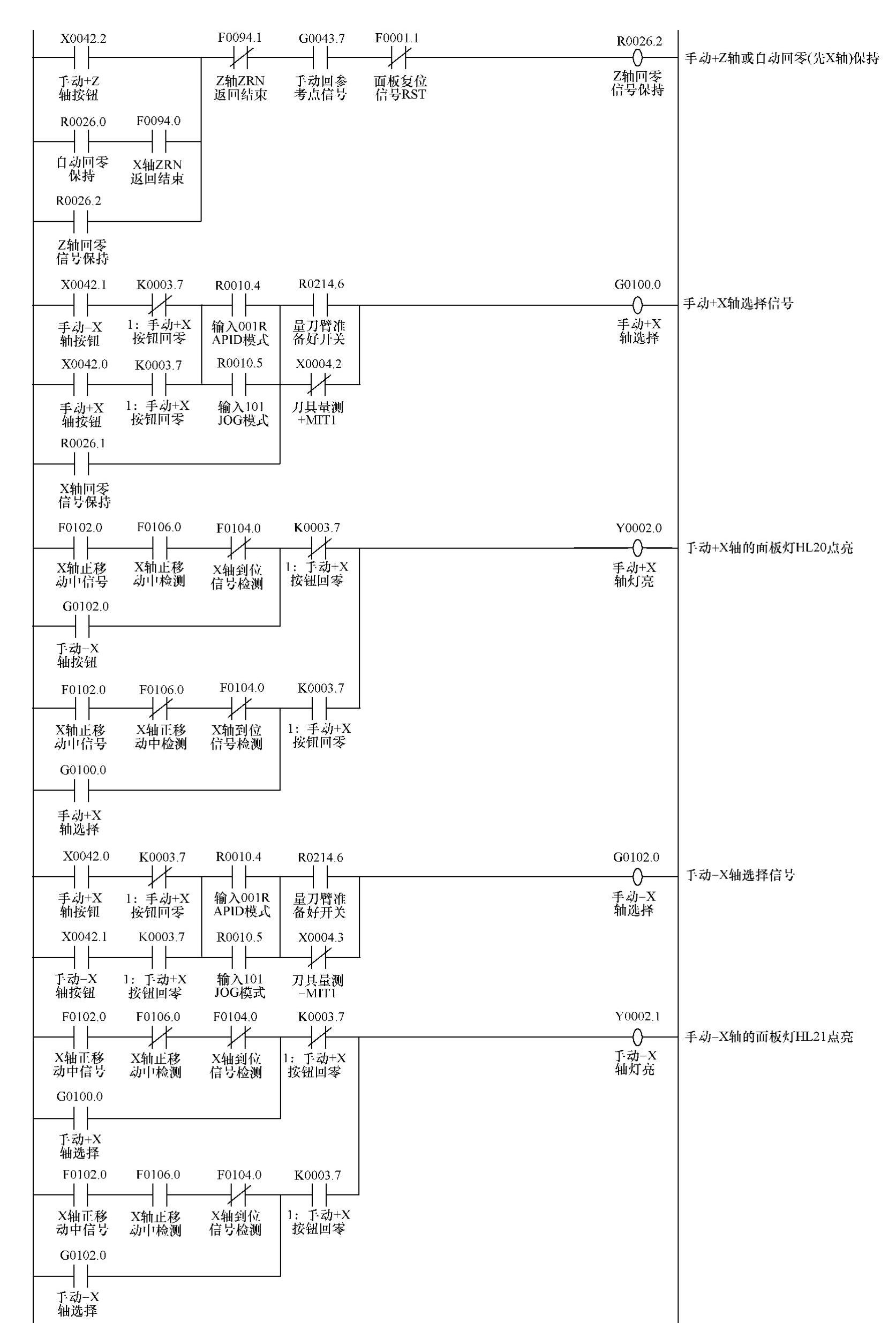
图5-155 LC34×3100卧式数控车床返回参考点的PMC梯形图(续)
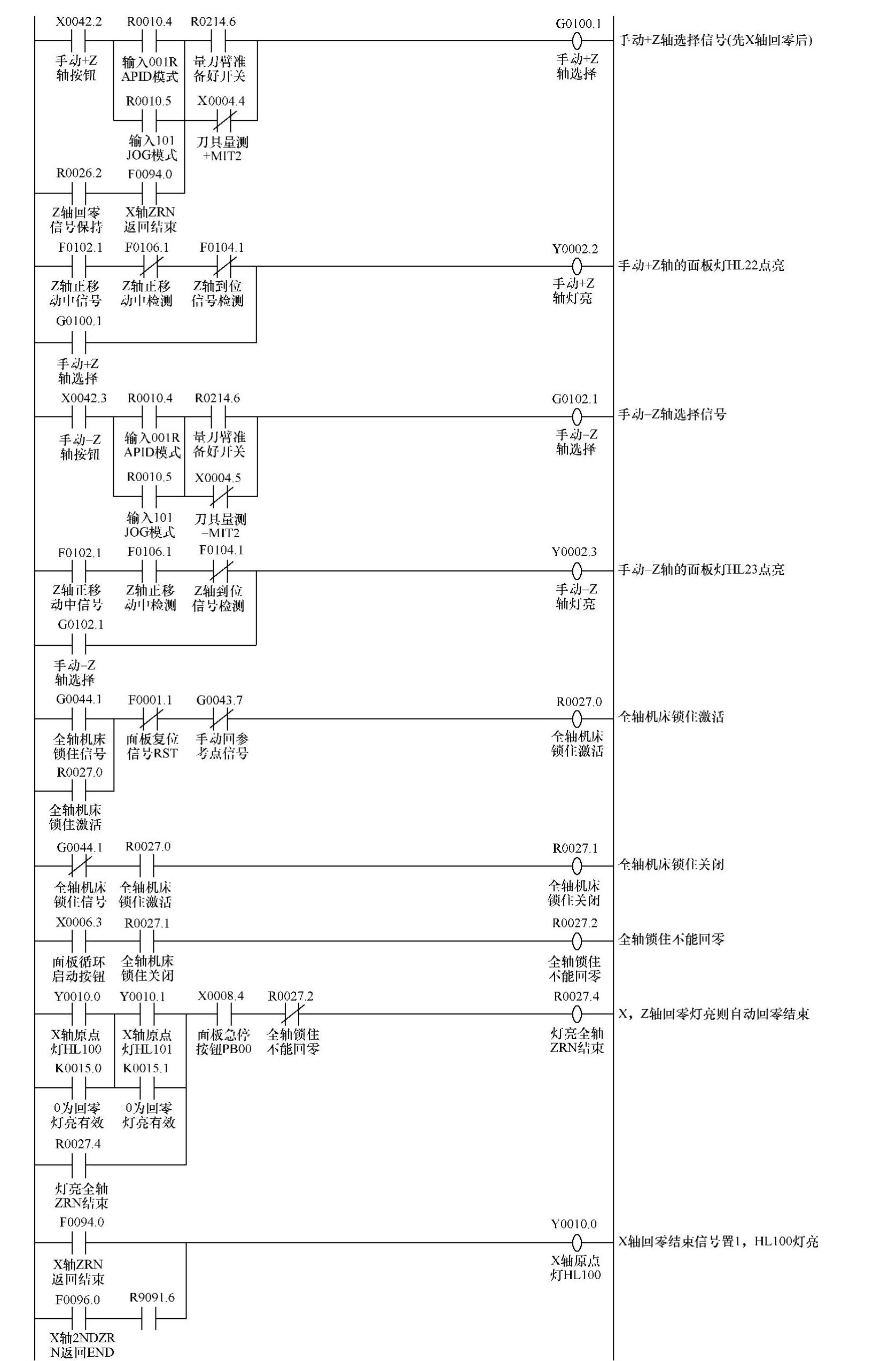
图5-155 LC34×3100卧式数控车床返回参考点的PMC梯形图(续)
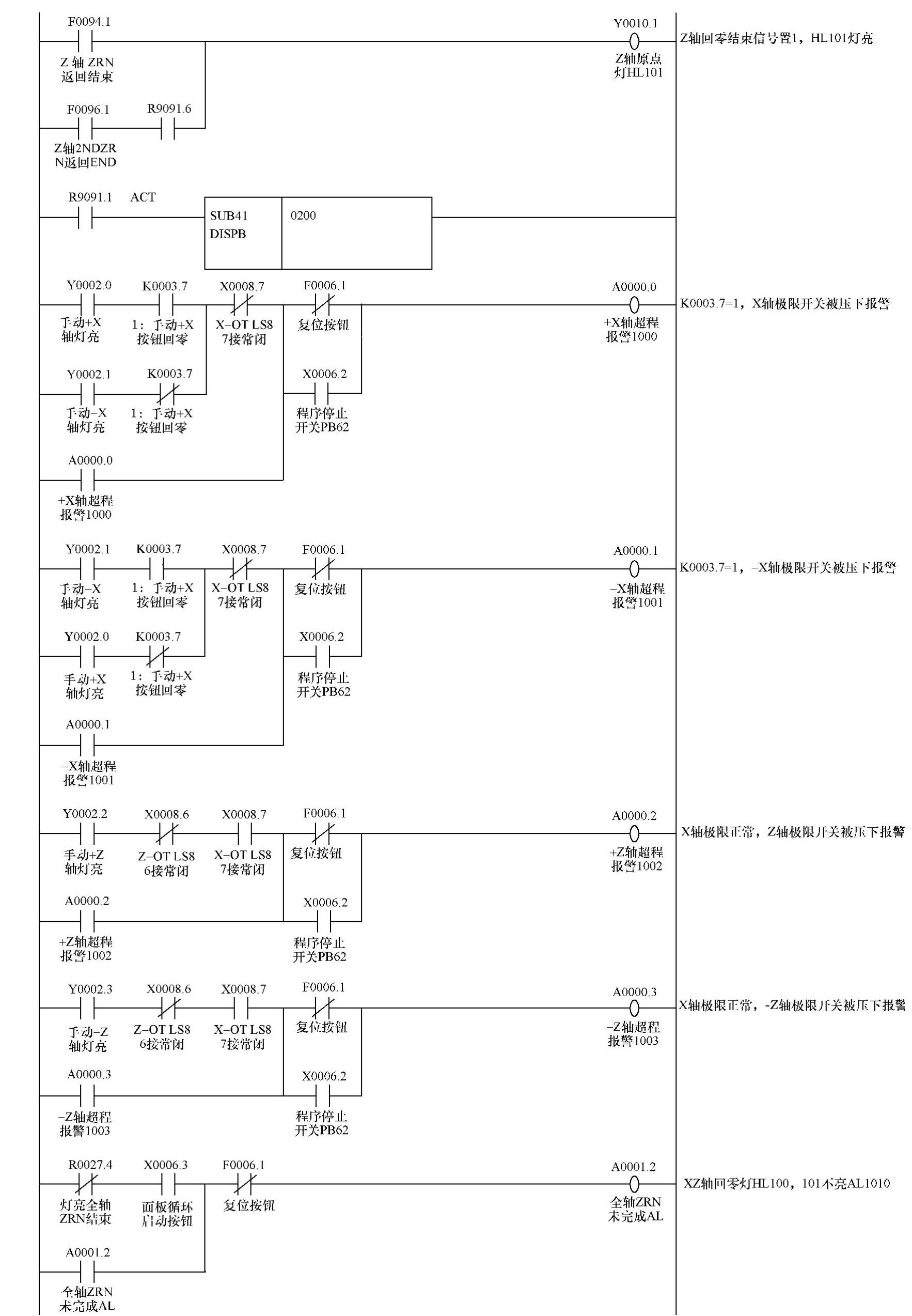
图5-155 LC34×3100卧式数控车床返回参考点的PMC梯形图(续)
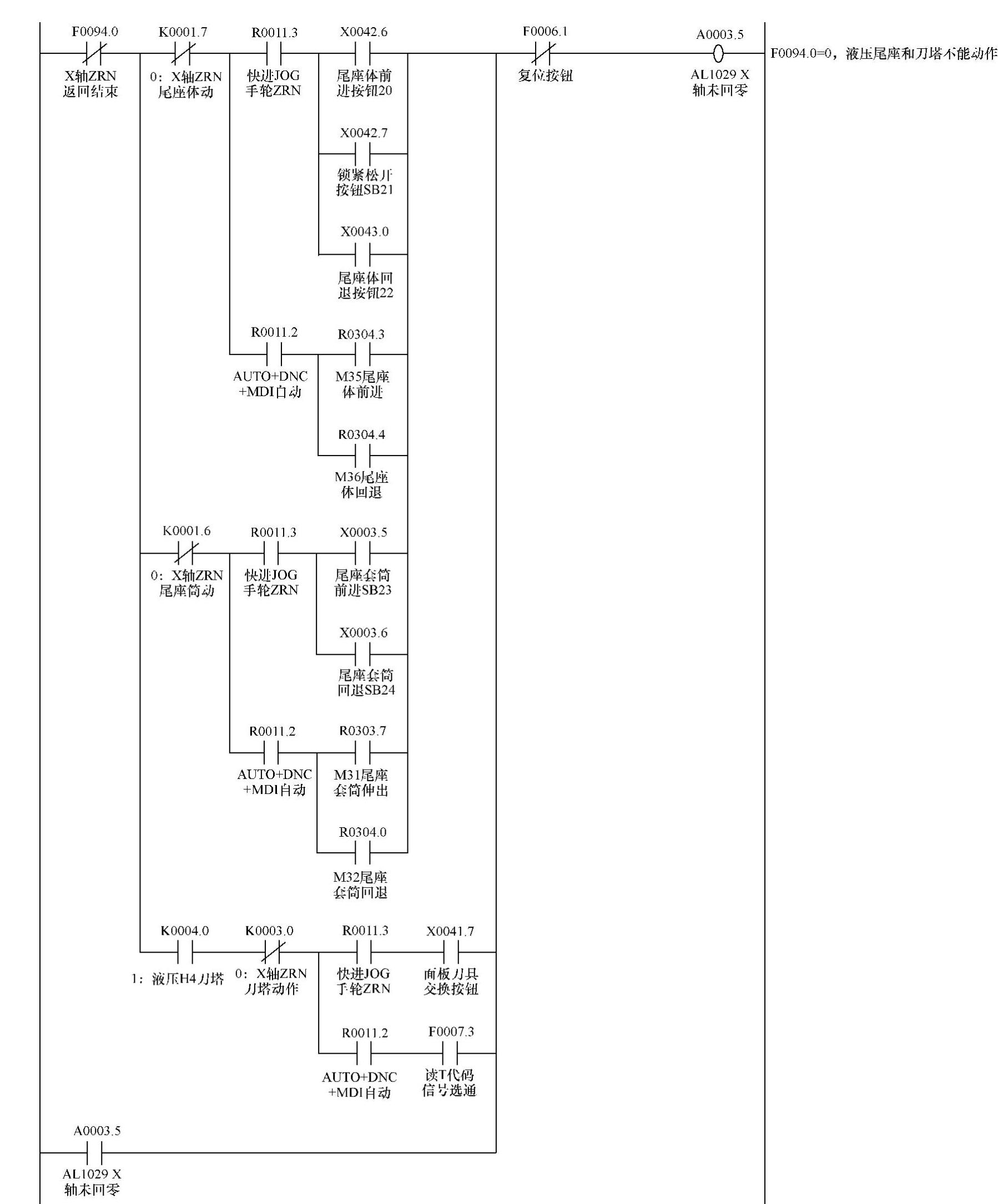
图5-155 LC34×3100卧式数控车床返回参考点的PMC梯形图(续)
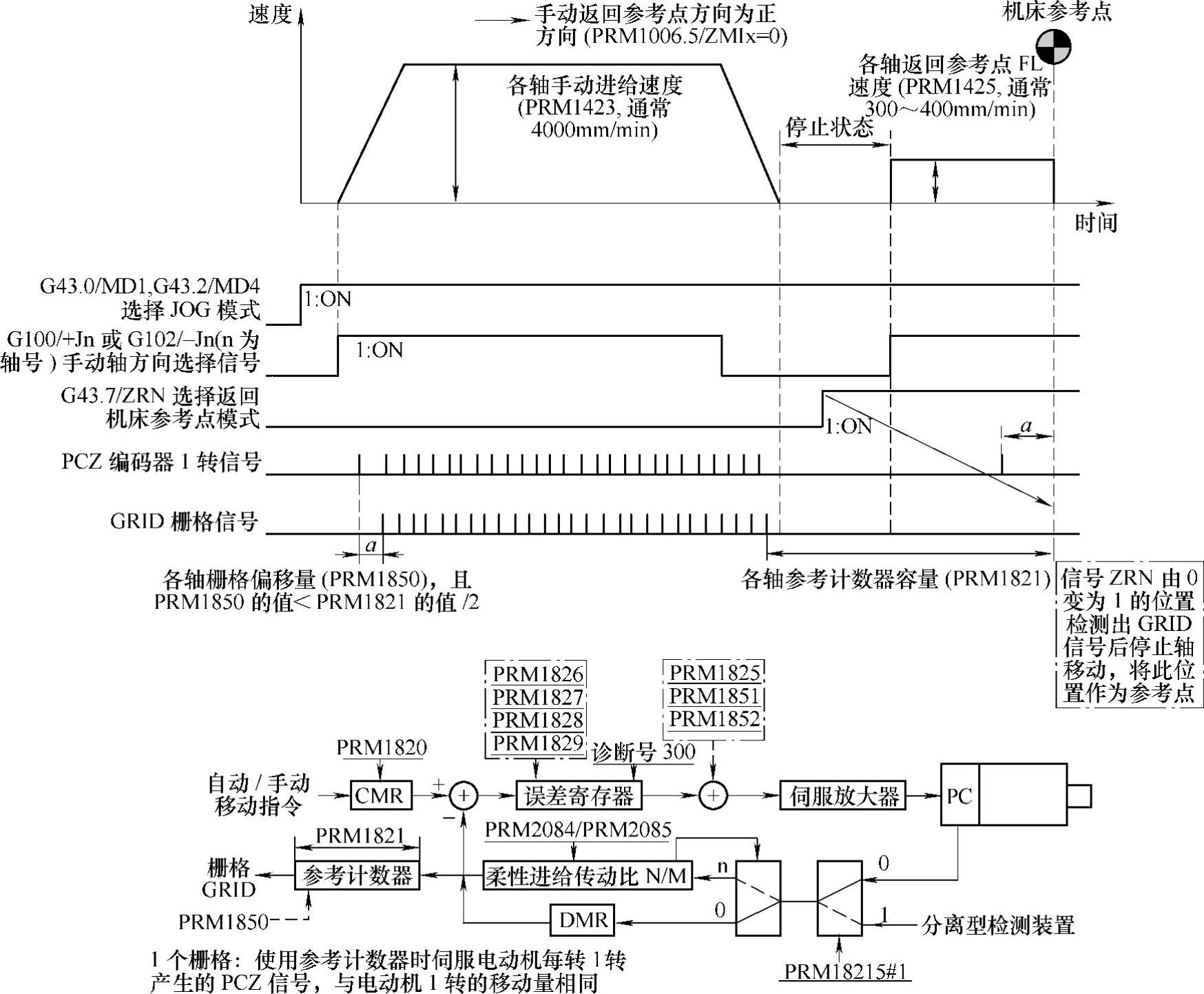
图5-156 FANUC 18/18i/0i/30i系统绝对编码器无挡块栅格法返回参考点的控制原理图
(11)采用绝对位置编码器的数控机床,其参考点一旦建立,就无需每次开机返回参考点操作;断电后的机床位置偏移(绝对位置编码器转角)被保存在电动机内装编码器的SRAM中,并通过伺服放大器上的存储电池(标准DC6V)支持电动机编码器SRAM中的数据。
(12)当更换伺服电动机或伺服放大器时,需将反馈线与电动机的插头脱开或者将电动机的反馈线与伺服放大器脱开,此操作使编码器SRAM电路与存储电池断开,进而SRAM中存储的位置信息随即丢失。当更换完毕机床再上电时,屏幕会出现#300(FANUC 16i/18i/21i/0iB/0iC系统)或DS0300(FANUC 0iD/30i/31i/32i系统)报警“n-AXIS ORIGIN RETURN”。此时需要调整参考点,具体操作方法见第5.4.2节位置检测装置及故障中的“绝对位置检测装置的报警及故障维修”内容。
(13)为方便读者更好地理解上述绝对编码器无挡块栅格法返回参考点的控制原理,在此给出QVM610A立式加工中心(FANUC 0iMC系统)返回参考点的PMC梯形图(见图5-157)。
3)数控机床返回参考点的常见故障分析数控机床返回参考点的常见故障主要有4方面:一是机床返回参考点过程中无减速动作且出现超程报警;二是机床返回参考点过程中有减速动作,但减速后轴运动不停止直至报警出现;三是手动返回参考点时伺服轴不移动;四是机床参考点位置因随机偏差而漂移不定。排查机床返回参考点的故障时,应从参考点返回的控制原理入手,借助PMCLAD梯形图显示画面或PMCDGN诊断画面的STATUS状态子画面,逐步分析参考点返回过程中PMC输入/输出信号的通与断,从而判定参考点减速挡块松动或有效长度异常、减速开关松动或损坏、减速挡块与减速开关之间的位置关系、CNC参数设置不当(如快速移动速度#1424/#1420、低速FL速度#1425、栅格偏移量#1850或参考计数器容量#1821)等故障因素。
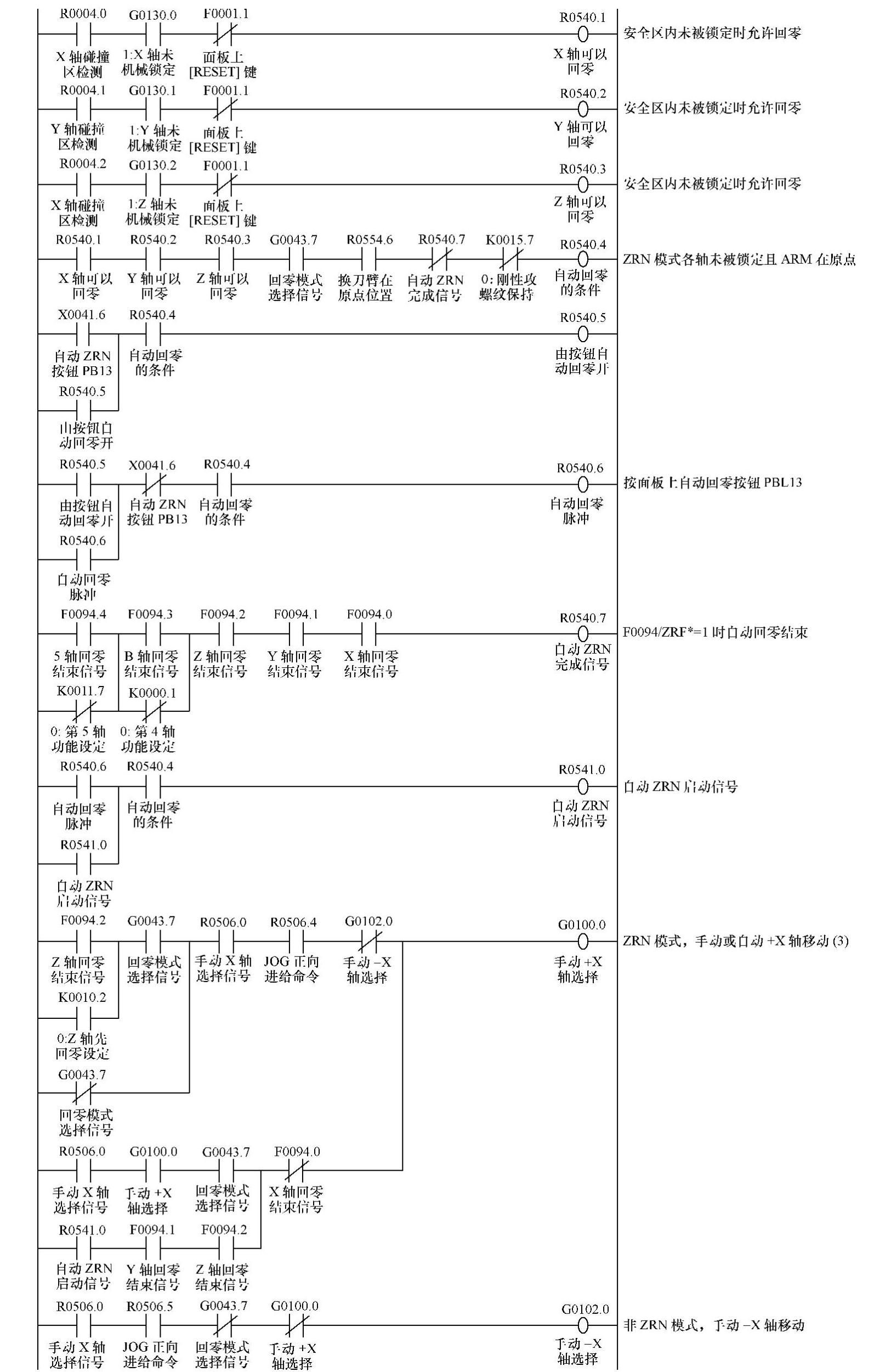
图5-157 QVM610A立式加工中心返回参考点的PMC梯形图
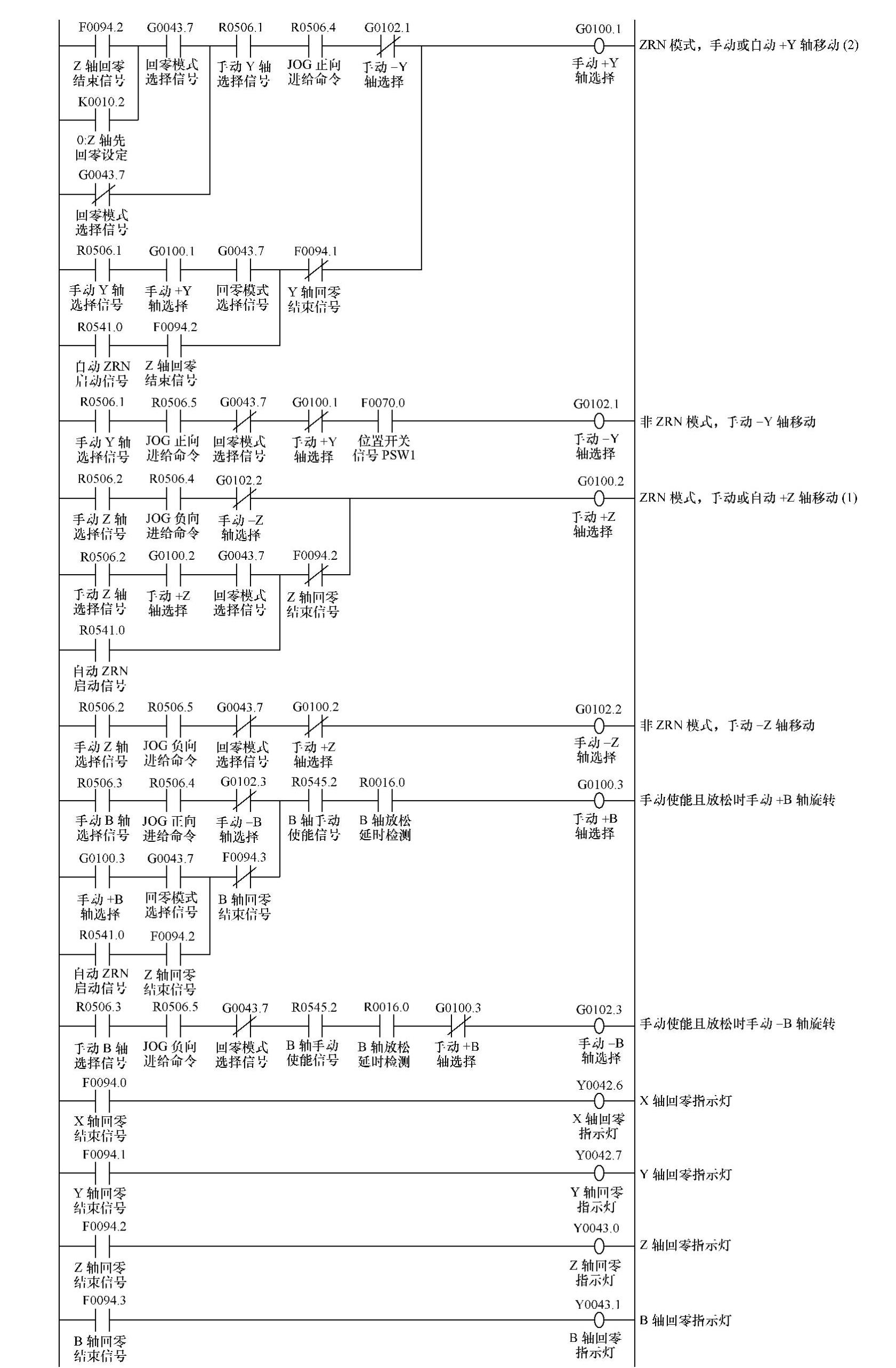
图5-157 QVM610A立式加工中心返回参考点的PMC梯形图(续)
1)机床返回参考点过程中无减速动作且出现超程报警。
①在参考点返回模式(REF),按伺服轴方向键按钮后,该轴能快速向参考点方向移动,说明模式选择开关信号(FANUC系统的G43.0,1,2,7)和伺服轴方向键信号(G100/+Jn或G102/-Jn)被接通且由PMC通知了CNC。
②当机床无减速动作且出现超程报警时,说明返回参考点的减速信号未通知到CNC。此时FANUC 18/18i/0i/30i系统中的负逻辑减速信号X9/∗DECn(n为轴号,n=1~8)或G196/∗DECn(参数#3006.0/GDC=1使用外部减速信号)为0,正常情况应为X9/∗DECn=1或G196/∗DECn=1。当减速挡块压下该开关后,信号由1变为0,工作台立即减速运行使减速开关释放,信号又恢复为1。
③造成减速开关信号失效的原因有减速开关损坏,因铁屑或严重油污使减速开关被压下后不能复位,减速挡块松动而随工作台移动时移位,减速开关信号线短路或断路,系统I/O接口板的减速信号接口因短路而烧毁等。
2)机床返回参考点过程中有减速动作,但减速后轴运动不停止直至报警出现。
①参考点返回过程中有减速动作且以低速FL速度减速运行,说明减速开关信号(FANUC 18/18i/0i/30i系统的X9/∗DECn=1或G196/∗DECn=1)已回馈至PMC中,且PMC并通知了CNC。
②当减速前行的伺服轴找到第1个栅格信号(伺服电动机编码器的一转信号PCZ或直线光栅尺的物理栅格)时,再移动由CNC参数设定的栅格偏移量(FANUC 18/18i/0i/30i系统为参数#1850且该值不超过#1821设定值的一半)后便停止,此停止点就是机床的参考点。当第1个栅格信号丢失时,减速后的伺服轴将持续前行而不停止。
③造成第1个栅格信号丢失的原因有伺服轴距离机床参考点太近、伺服轴存储行程设定值太小而使机床软超程(FANUC 18/18i/0i/30i系统为参数#1320~#1327)、电动机编码器或光栅尺因进水进油而被污染(窄脉冲PCZ信号门槛电压低或波形严重失真)、反馈信号线或光栅适配器受到外部干扰或反馈信号衰减、编码器或光栅尺的接口电路故障、伺服放大器接口电路故障、系统轴控制卡故障等。
④实例分析1:一台半闭环控制的龙门数控镗铣床(FANUC 16iMB系统)每次开机手动返回参考点时,X轴有减速动作但偶尔出现90号“未完成回参考点”报警;一旦手动回参考点(寻找第1个栅格信号PCZ)成功,重复用G28指令自动返回参考点(使用计数器清零方式)无任何问题。首先移动X轴远离机床参考点50mm左右,重复返回参考点,故障现象依旧,所以排除伺服轴距离参考点太近的原因。然后由于手动返回参考点是寻找第1个栅格信号,而G28自动返回参考点采用计数器清零方式,故用排除法重点检查X轴的1转信号PCZ是否正常(高速串行传送的数据无法用示波器检测),即先用万用表欧姆挡测量反馈电缆的通断,反馈线状态完好;再将未发现污染的X轴脉冲编码器与参考点返回正常的Z轴脉冲编码器(前提规格型号相同)互换,执行返回参考点操作后,X轴故障依旧、Z轴参考点正常,如此说明脉冲编码器状态完好;更换同规格型号的伺服放大器控制电路板后执行返回参考点,故障现象依旧,说明伺服放大器无异常;此时排查坦克链中的X轴反馈电缆过长(>50m)使1转信号PCZ衰减的可能性,将反馈电缆的DC5V和0V线脚与电缆中多余的备用线并联加粗,以降低线间电阻、提高信号幅值,执行返回参考点操作,故障排除。
⑤实例分析2:一台全闭环控制的KH50G立式加工中心(FANUC 0iMC系统)X轴手动返回参考点时无法找到第1个栅格信号(直线光栅尺为物理栅格)。由于全闭环控制的参考点返回采用直线光栅尺的物理栅格控制,故重点排查直线光栅尺的标尺光栅。首先屏蔽X轴光栅尺(方法详见第5.4.2节位置检测装置及故障中“屏蔽光栅尺的方法及注意事项”内容),执行X轴返回参考点操作正常,如此说明故障来自于直线光栅尺。然后将标尺光栅从光栅尺铝壳中水平抽出并用无水酒精或丙酮将其擦洗干净(见图5-158),发现参考点区域栅格有划伤无法修复。为了节省维修成本,基于满足工艺要求的前提下,将减速挡块前移n个栅格位置并重新固定,回装标尺光栅并测量安装精度符合要求后(读数头支架与光栅尺铝壳的间隙及读数头的位置度等),执行手动返回参考点操作成功。
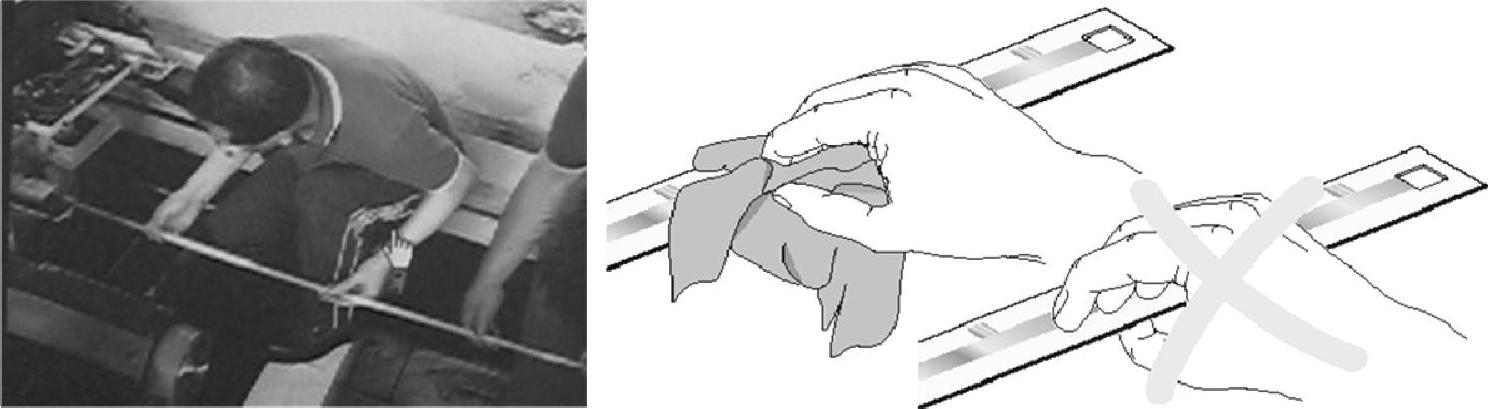
图5-158 KH50G立式加工中心X轴标尺光栅的维护
3)手动返回参考点时伺服轴不移动,故障原因及处理方法详见第5.4.6节操作引起伺服轴不动作的常见故障分析中的“机床手动(JOG)操作不正常而自动(MEM)操作正常”内容。
4)机床返回参考点的位置不准确(又称参考点漂移)
①若数控机床返回参考点的位置发生漂移(见图5-159),则将造成被加工件的尺寸大小不一而无法保证加工精度和满足工艺要求,还有可能发生干涉碰撞使机床、刀具或工件损坏。排查参考点漂移的原因时,应先测量进给传动部件的定位精度、重复定位精度及反向间隙是否超差,进而判别是机械方面故障还是电气系统方面故障。
②排查伺服电动机与滚珠丝杠副的连接是否松动:用白色铅油笔在伺服电动机轴、联轴器和滚珠丝杠轴上画一条线,JOG方式下前后移动伺服轴,观察电动机轴、联轴器和丝杠轴上的白线是否仍吻合,若吻合则连接正常,若不吻合则连接松动。
③排查滚珠丝杠副是否存在轴向窜动误差和反向间隙(见图5-160),处理方法详见第5.3.1节中的“滚珠丝杠副常见故障与排除”内容。
④排除减速挡块起始位置不正确致基准偏移N个栅格的因素:对于FANUC18/18i/0i/30i系统,读取系统诊断画面(按面板[SYSTEM]功能键→[DGN]软键即可显示画面)中诊断号302(自减速挡块脱离的位置至第1个栅格之间的距离)的数值,看其是否为CNC参数#1821设定的参考计数器容量的1/2,且多次重复返回参考点时诊断号302中的数值变化幅度不大(机床参考点位置稳定)。当诊断号302显示的数值超过1/2个栅格时,得调整减速挡块的位置;当诊断号302显示的数值不超过1/2个栅格时,修改栅格偏移量参数#1850;当诊断号302中数值变化幅度大时,应考虑减速开关与减速挡块的接触太松或减速开关动作不良等故障因素。对于减速挡块有效长度太短的情况,可根据以下公式计算得出:
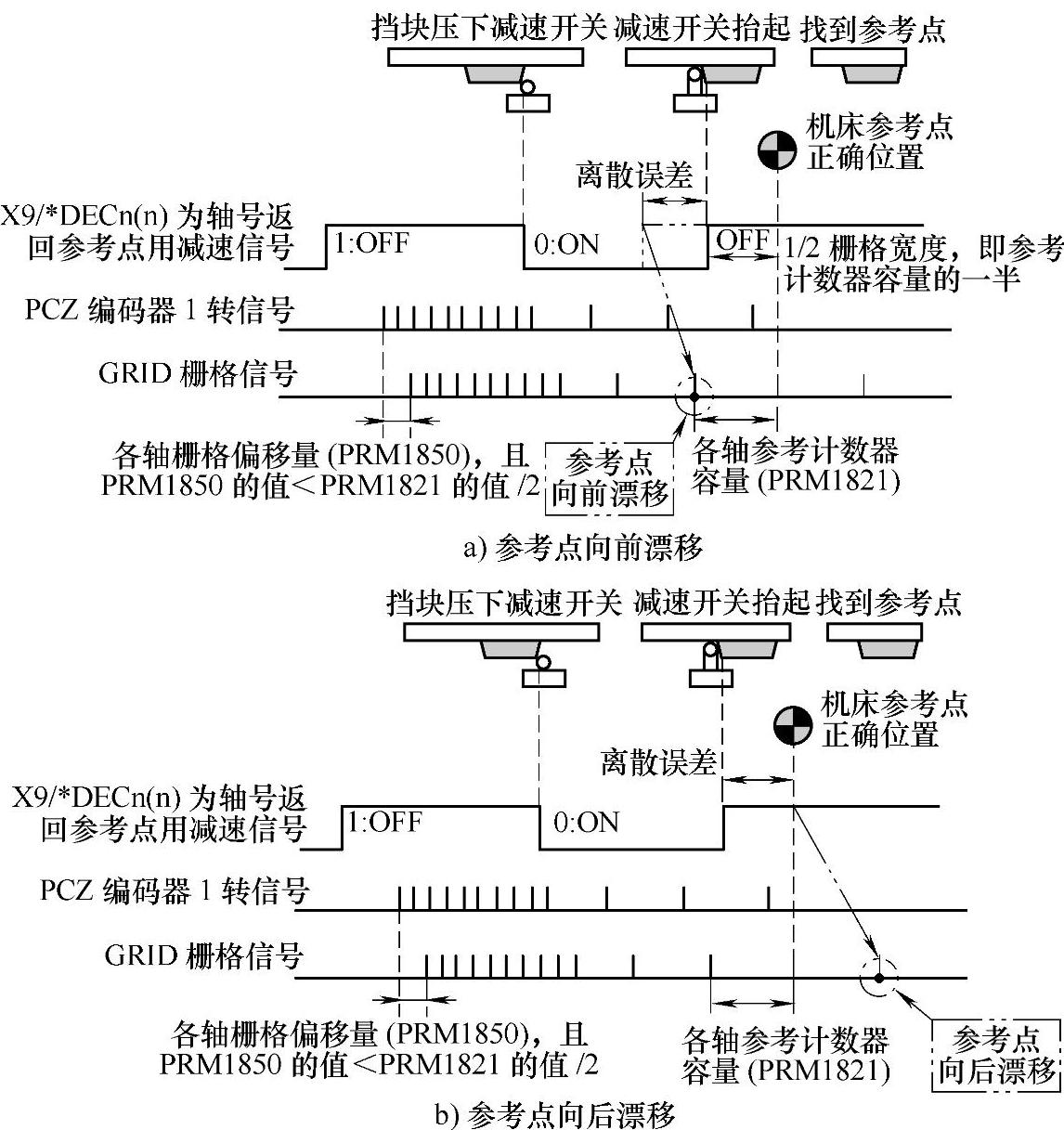
图5-159 离散误差造成机床参考点漂移
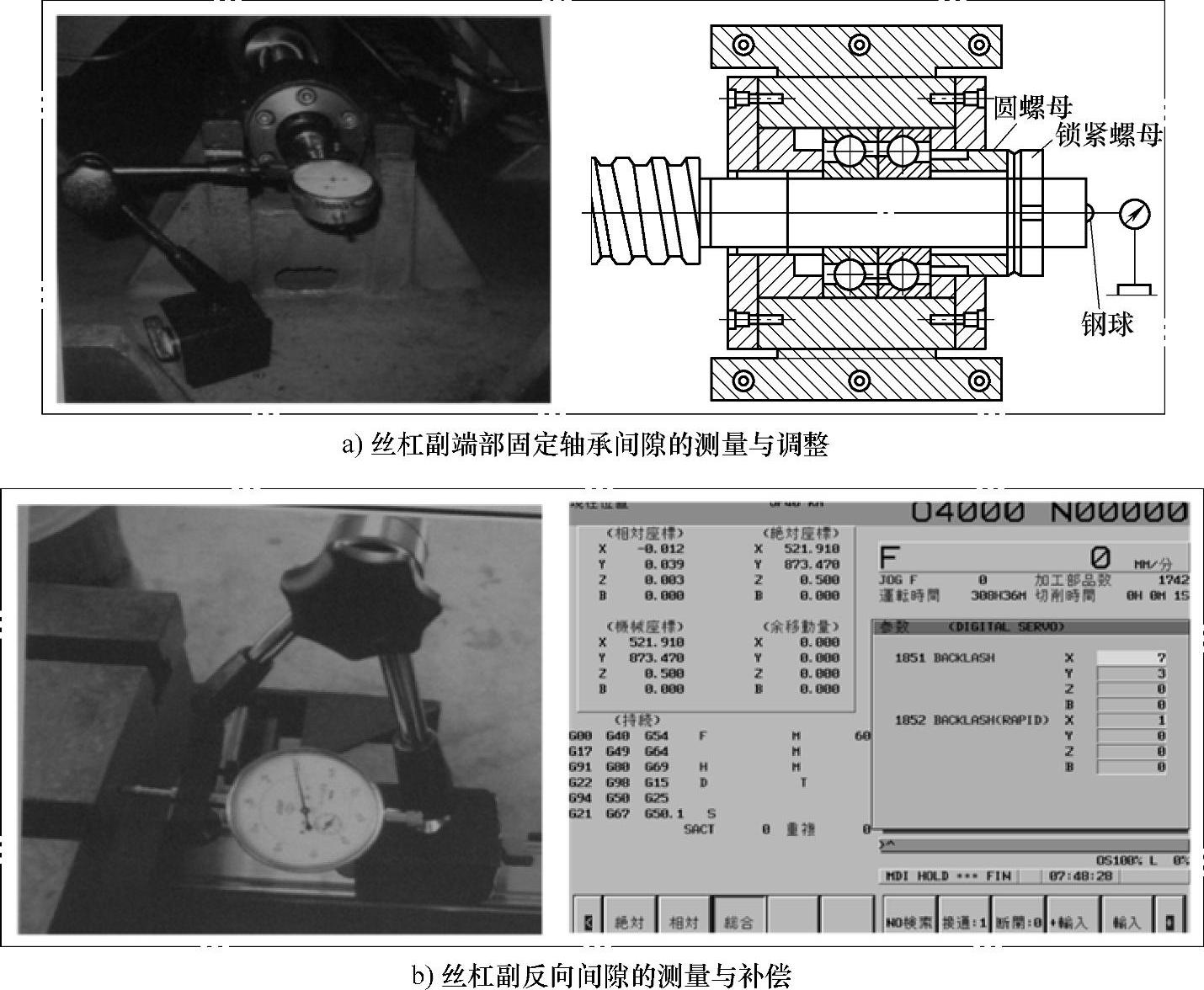
图5-160 滚珠丝杠副轴向窜动误差和反向间隙的测量与调整

式中 V快——参数#1420设定的快速进给速度(mm/min);
T1——参数#1620设定的快速进给直线加减速时间常数(ms);
T2——伺服加速时间(ms),且
;
30——经验得出的时间补偿量(ms);
1.2——计算值中包含20%的裕量。
排查参考点位置随机漂移的原因:检查位置检测装置反馈信号线的屏蔽是否有效或过于靠近强电电缆,位置检测装置的供电电压是否太低(不足DC5V±5%),脉冲编码器或伺服放大器是否不良(对调伺服放大器侧电动机的动力线和位置反馈线,故障转移则放大器不良,否则脉冲编码器不良),伺服位置环增益(参数#1825)设定是否过低或进给伺服轴快速移动速度(参数#1420)是否过高,返回参考点的低速FL速度(参数#1425)设定是否过低,参考计数器容量(
)是否设置错误等。
相关推荐