【摘要】:数控机床伺服进给的控制可分为主回路和辅助控制回路两部分。其中,主回路包括电源模块、伺服放大器、伺服电动机和位置检测装置等部分,辅助控制回路则由机床操作面板上按钮、各类开关、状态指示灯、I/O单元或模块及中间继电器等组成。TH1、TH2:过热报警输入端子,可用于伺服变压器及制动电阻的过热信号的输入。CX3:伺服装置内MCC动作确认接口,一般可用于SVU主电路接触器的控制。
数控机床伺服进给的控制可分为主回路和辅助控制回路两部分。其中,主回路包括电源模块(第4.4.2节已介绍)、伺服放大器、伺服电动机和位置检测装置等部分(见图5-83),辅助控制回路则由机床操作面板上按钮、各类开关、状态指示灯、I/O单元或模块及中间继电器等组成。对于伺服进给的控制,因数控系统和用户要求的不同而不同,其硬件连接和参数设定就有所不同,具体需根据数控系统厂家提供的《硬件连接手册》、《功能说明书》和《参数说明书》等资料进行安装和配置。
1.伺服放大器及故障
伺服放大器负责接收通过FSSB输入的CNC轴控制指令,驱动伺服电动机按照指令运转,同时放大器上的JFn接口接收伺服电动机编码器的反馈信号并将位置信息通过FSSB光缆再传输到CNC中,从而实现伺服电动机闭环电流的矢量控制及进给执行部件的速度和位置控制。
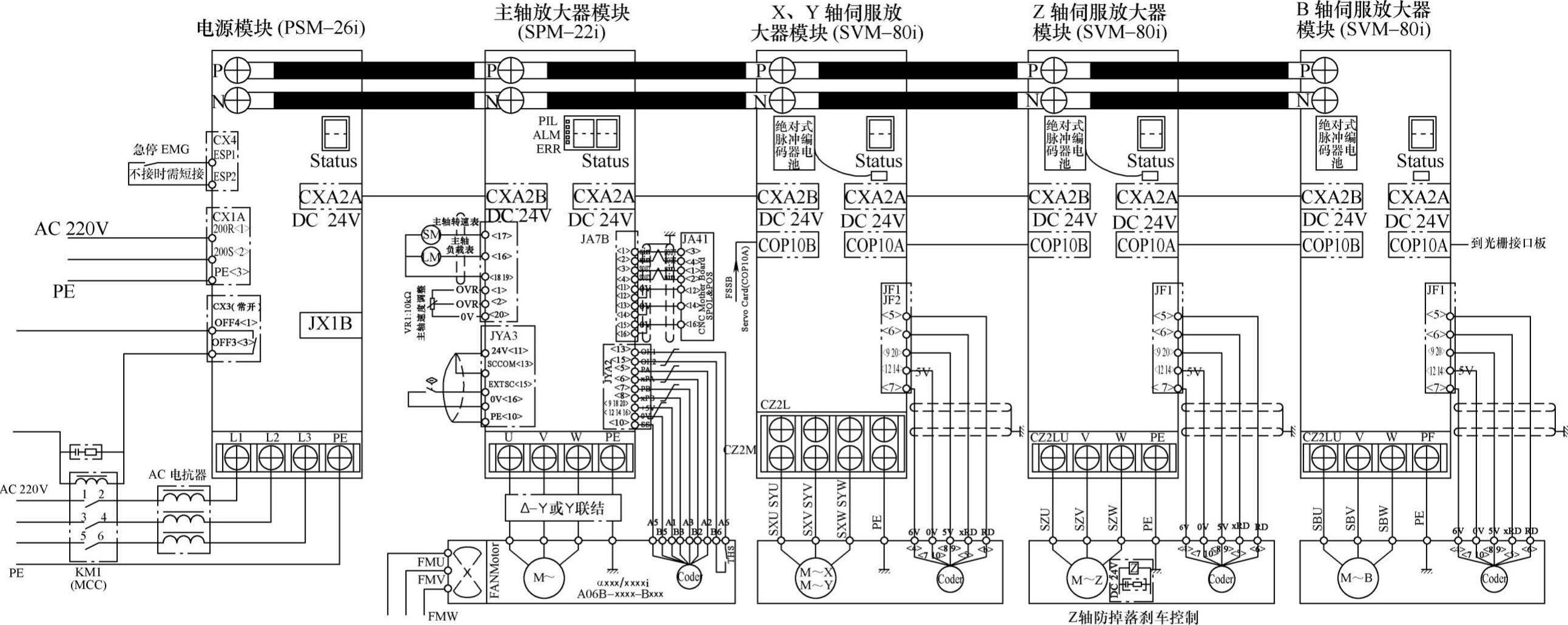
图5-83 TMV1100A立式加工中心主回路连接图
按伺服装置主电路电源输入是交流伺服驱动装置还是直流伺服驱动装置分类,可分为伺服单元(SVU)和伺服模块(SVM)两种。伺服单元的输入电源通常为AC200V、50Hz的三相交流电,电动机的再生能量通过伺服单元的再生放电单元中的制动电阻消耗掉;伺服模块的输入电源为直流电源(标准型为DC300V,高压型为DC600V),电动机的再生能量通过电源模块反馈到电网中。FANUC系统的伺服单元有α系列、β系列、βi系列和一体型SVPM四种(见图5-84),FANUC系统的伺服模块有α系列和αi系列两种(见图5-85)。通常当主轴为模拟量控制驱动时,采用伺服单元驱动进给轴电动机;当主轴为串行数字控制驱动时,采用伺服模块驱动进给轴电动机。
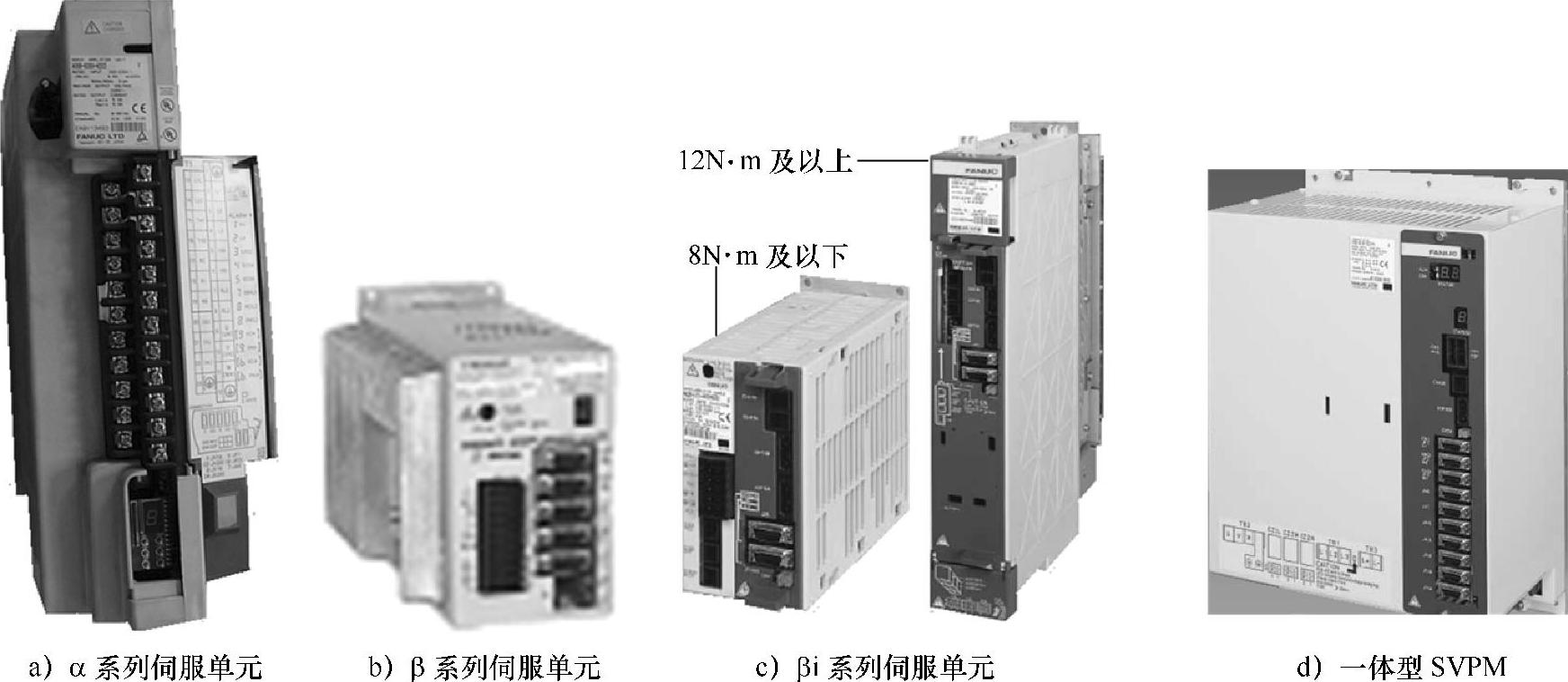
图5-84 FANUC系统伺服单元SVU
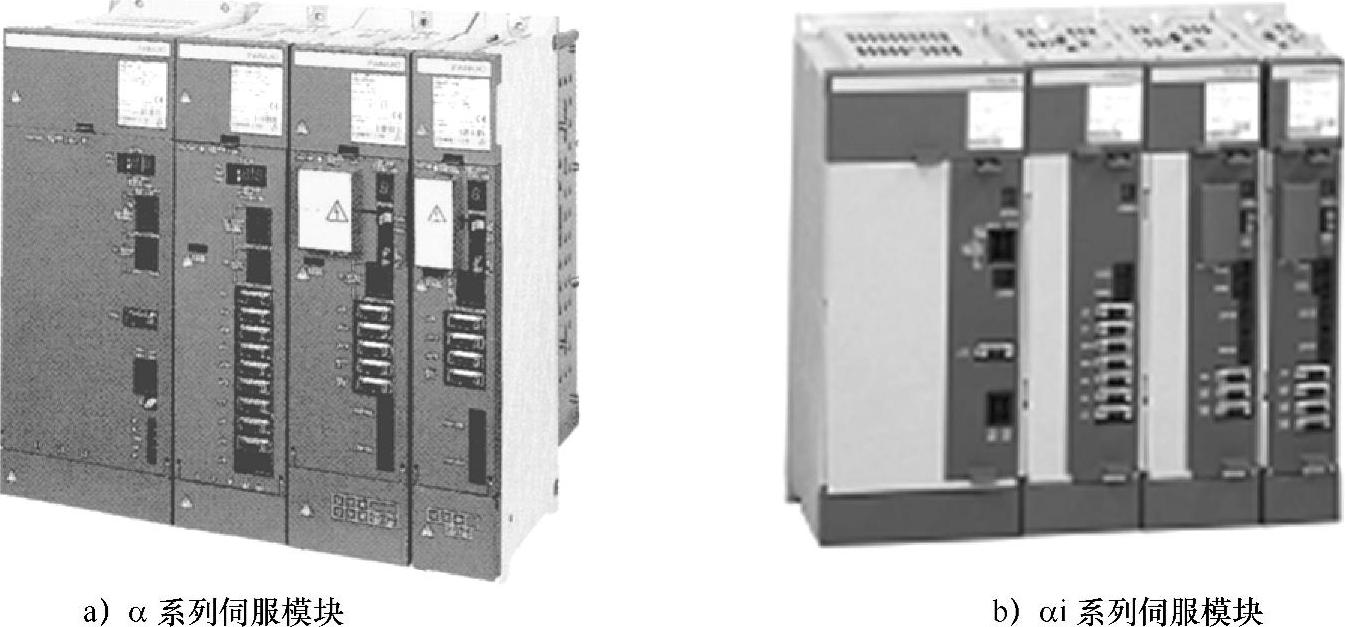
图5-85 FANUC系统伺服模块SVM
(1)α系列伺服单元SVU的实物连接及接口布置(见图5-86)
1)接线端子说明。
L1、L2、L3:三相输入动力电源端子,交流200V。
L1C、L2C:单相输入控制电路电源端子,交流200V(出厂时与L1、L2短接)。
TH1、TH2:过热报警输入端子(出厂时TH1-TH2已短接),可用于伺服变压器及制动电阻的过热信号的输入。

图5-86 α系列伺服单元的实物连接及接口布置
RC、RI、RE:外接或内装制动电阻选择端子。
RL2、RL3:MCC接触器动作确认输出端子(MCC的常闭点)。
100A、100B:C型放大器内部交流继电器的线圈外部输入电源(α型放大器已为内部直流24V电源)。
UL、VL、WL:第一轴伺服电动机动力线。
UM、VM、WM:第二轴伺服电动机动力线。
2)电缆接口说明。
JV1B、JV2B:A型接口的伺服控制信号输入接口。
JS1B、JS2B:B型接口的伺服控制信号输入接口。
JF1、JF2:B型接口的伺服位置反馈信号输入接口。
JA4:伺服电动机内装绝对编码器电池电源接口,DC6V。
CX3:伺服装置内MCC动作确认接口,一般可用于SVU主电路接触器的控制。
CX4:伺服紧急停止信号输入端,用于机床面板的急停开关(常闭触点)。
3)α系列伺服单元SVU的连接(见图5-87)。
4)开关的设定。
开关1的设定:CNC与伺服放大器之间的接口类型不同,其设定也不同。A型接口为OFF,B型接口为ON。设定不对时,将出现401号伺服报警(SVU状态LED显示“-”)。
开关2的设定:选择C型或α型放大器,C型放大器设定为ON,α型放大器设定为OFF。设定不对时,将出现401伺服报警(SVU状态LED显示“-”)。
开关3、4的设定:根据使用的再生放电电阻不同,设定也不同。开关3、4均置ON时为内装型(800W),开关3置ON、开关4置OFF时为分离型(800W),开关3、4均置OFF时为分离型(1200W)。
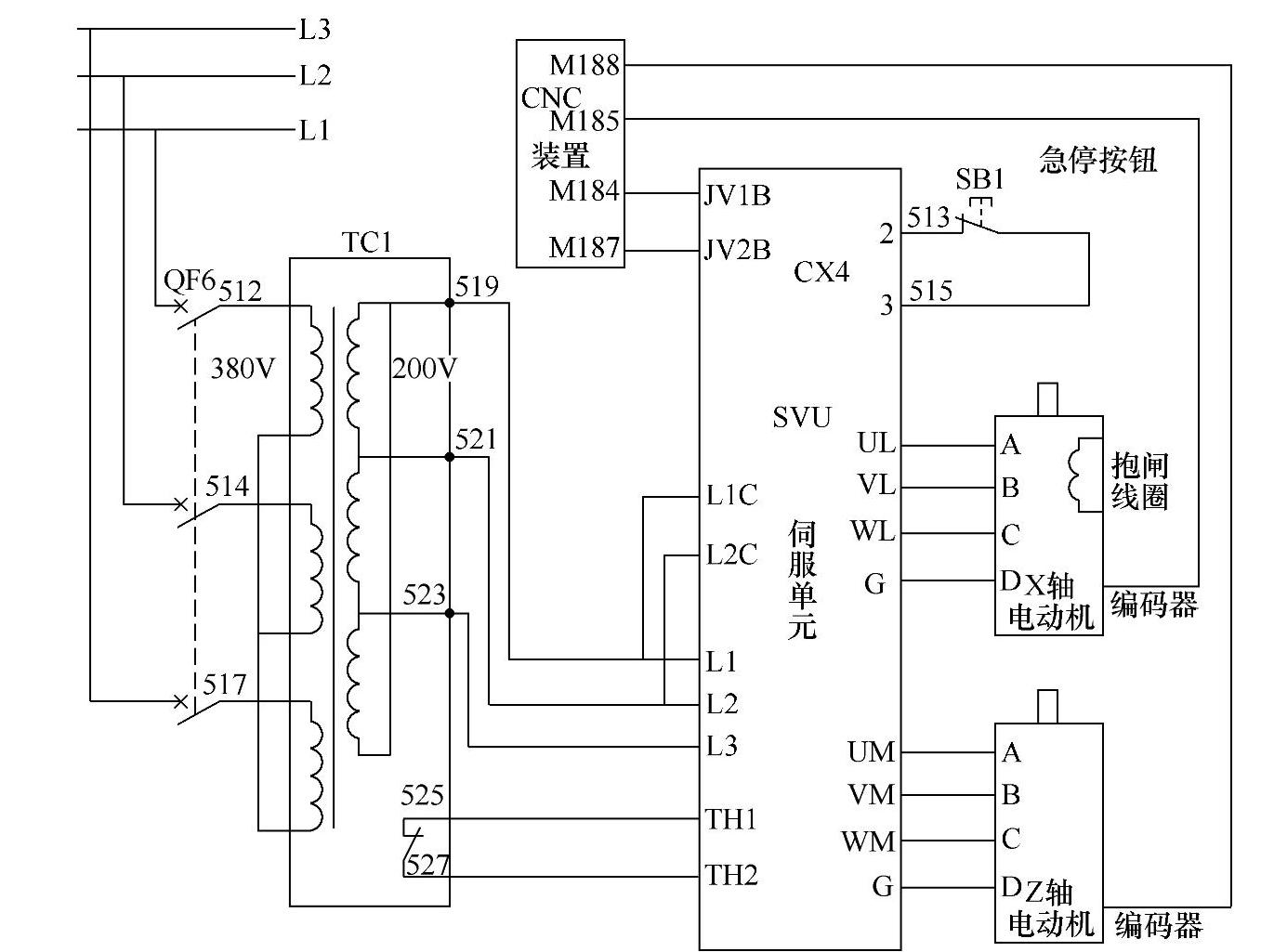
图5-87 SSCK-20卧式数控车床(FANUC 0TD系统)α系列SVU的连接
5)状态显示(7段LED)及相应报警代码的故障原因分析。
7段LED不显示:控制电源未接通。
7段LED显示“0”:伺服就绪。
7段LED显示“-”:伺服未就绪。
7段LED显示“#”:伺服报警代码。
当伺服单元SVU出现故障时,系统会出现“4##”报警,并在SVU状态显示窗口(7段LED)显示相应的报警代码(见表5-6)。
表5-6 α系列伺服单元7段LED显示的报警代码及故障原因
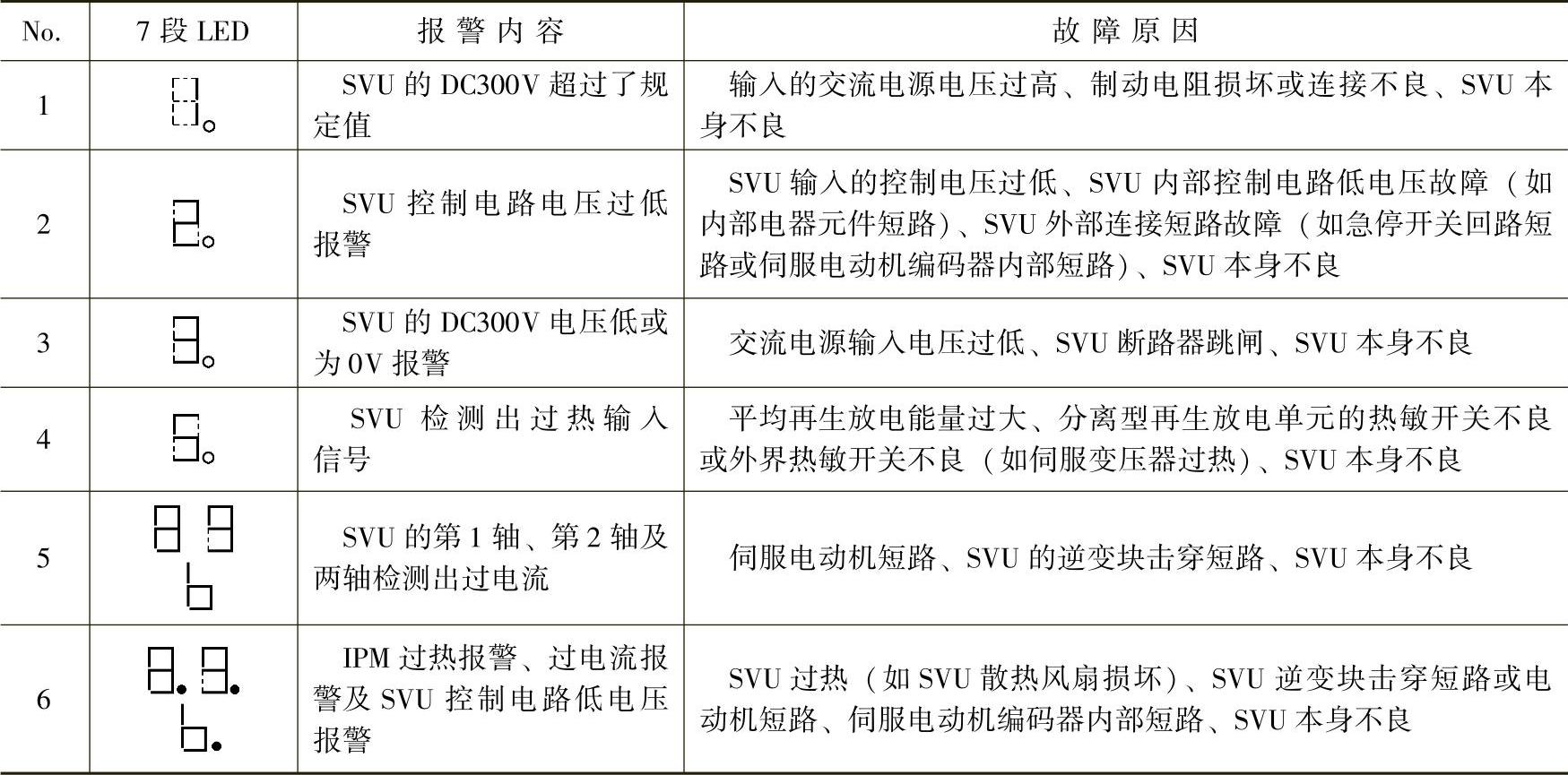
6)测试针的功能。
IRL、ISL:第1轴伺服电动机R、S两相瞬时输出电流测试端。
IRM、ISM:第2轴伺服电动机R、S两相瞬时输出电流测试端。
5V、0V:伺服单元控制电路+5V电源的测试针。
(2)βi系列伺服单元SVU的实物连接及接口布置 βi系列伺服单元SVU是FANUC公司推出的高可靠性和性价比的进给伺服驱动装置。它一般用于小型数控机床进给轴的伺服驱动(如FANUC 0i Mate B/C系统中作为X轴、Z轴的伺服驱动)及中、大型加工中心数控机床的附加伺服轴的驱动(I/OLink伺服单元),如在FANUC 18iMB系统的卧式加工中心中作为刀库旋转或机械手转臂的控制等。
1)接线端子说明(见图5-88)。
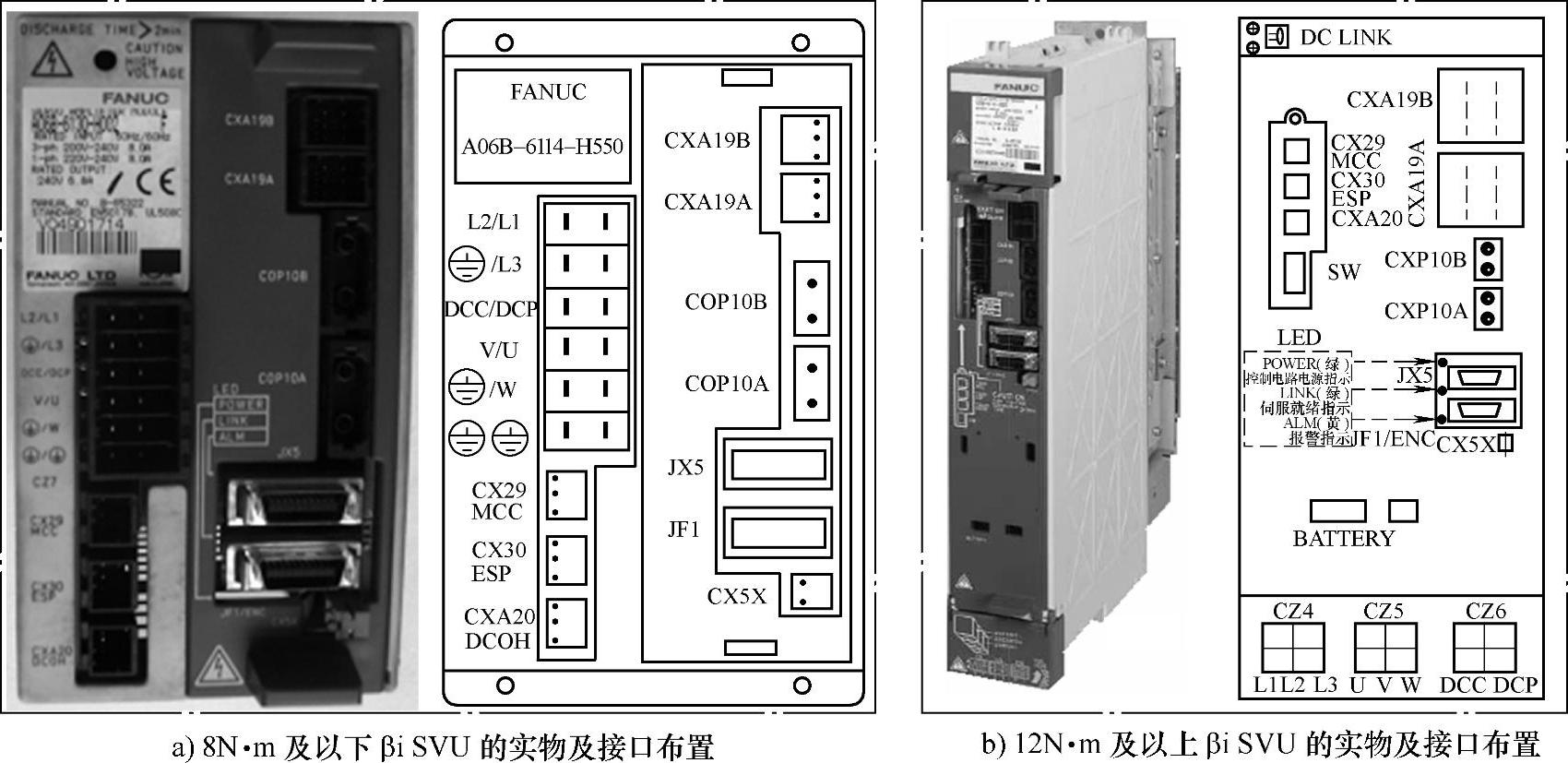
图5-88 βi系列伺服单元的实物连接及接口布置
L1、L2、L3:主电源输入端接口,三相交流电源200V、50/60Hz。
U、V、W:伺服电动机的动力线接口。
DCC、DCP:外接DC制动电阻接口。
CX29:主电源MCC控制信号接口。
CX30:急停信号(∗ESP)接口。
CXA20:DC制动电阻过热信号接口。
CXA19A:DC24V控制电路电源输入接口,连接外部24V稳压电源。
CXA19B:DC24V控制电路电源输出接口,连接下一伺服单元的CX19A。
COP10A:伺服高速串行总线(HSSB)接口,连接下一伺服单元的COP10B(光缆)。
COP10B:伺服高速串行总线(HSSB)接口,与CNC系统的COP10A连接(光缆)。
JX5:伺服检测板信号接口。
JF1:伺服电动机内装编码器信号接口。
CX5X:伺服电动机编码器为绝对编码器的电池接口。
POWER(绿色):控制电源状态显示指示灯LED。
LINK(绿色):FSSB连接状态显示指示灯LED。
ALM(黄色):伺服报警状态指示灯LED。
SW(≥12N·m的伺服单元):DC直流报警级别设定开关。
2)βi系列伺服单元SVU的连接(见图5-89)。
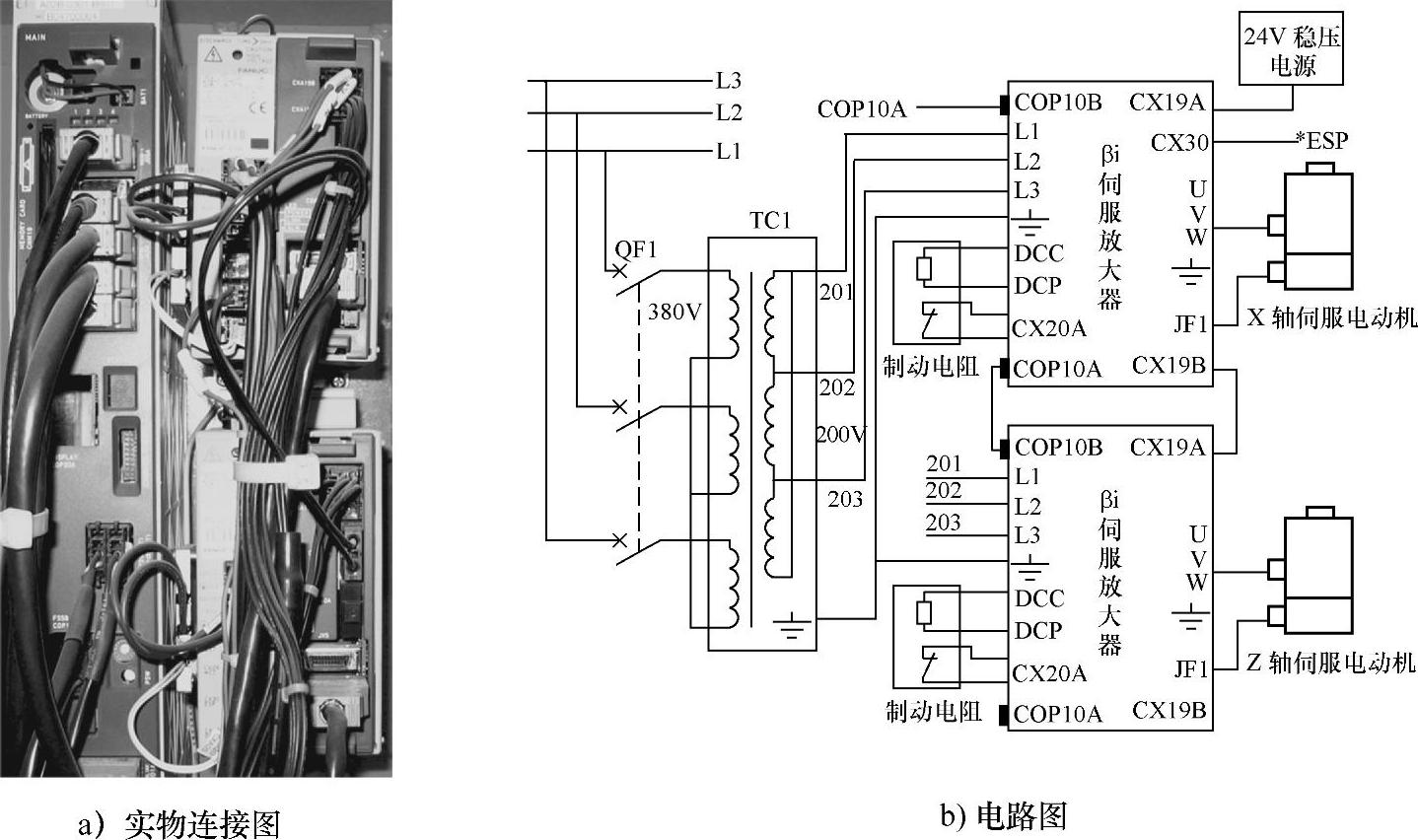
图5-89 YV1200立式数控车床(FANUC 0i MateTC/TD系统)βi系列SVU的连接
3)一体型SVPM的接口布置及连接(见图5-90)。
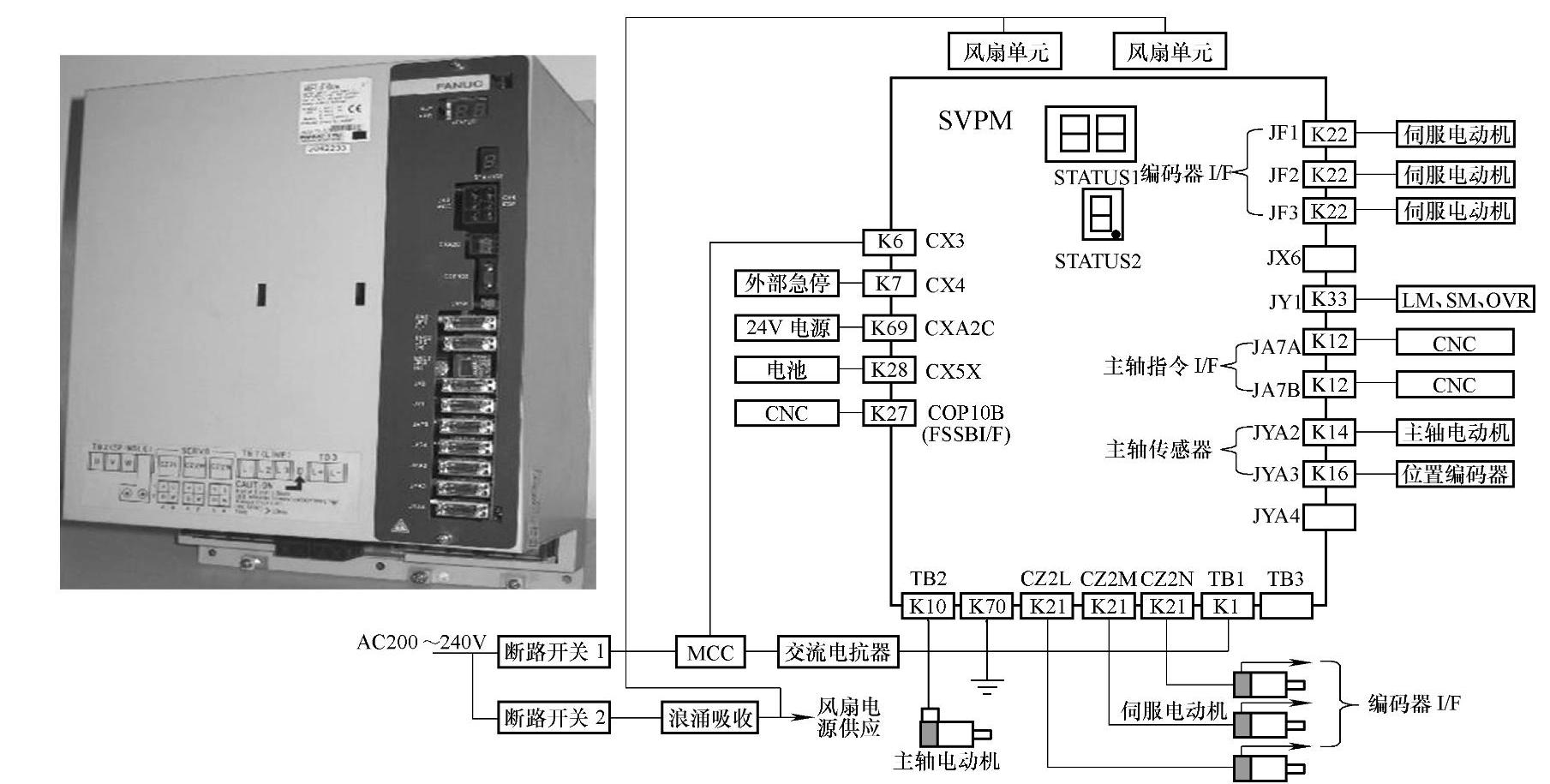
图5-90 一体型SVPM的接口布置及连接
STATUS1、STATUS2:分别为主轴和伺服的状态指示灯。
CX3:主电源MCC控制信号的连接。
CX4:外部急停信号(∗ESP)的连接。
CXA2C:24V电源的输入。
COP10B:伺服FSSB光缆接口。
CX5X:绝对位置编码器用电池插头。
JX6:断电后备模块。
JF1、JF2和JF3:分别为L轴、M轴和N轴编码器的连接。
JA7B:主轴输入接口。
JA7A:主轴输出接口。
JYA4:未使用。
JY1:主轴速度表、模拟倍率表。
JYA2:主轴传感器Mi或MZi。
JYA3:α位置编码器,外部一转信号。
TB1:主电源输入连接端子板。
TB2:主轴电机动力线。
TB3:DCLink端子台。
CZ2L、CZ2M和CZ2N:分别为L轴、M轴和N轴伺服电动机的动力线。
(3)α系列伺服模块SVM的实物连接及接口布置 α系列伺服模块主要用于FANUC 0C/0D/16/18/21/0iA系统的伺服轴驱动,1个伺服模块可驱动1台、2台或3台伺服电动机,其伺服信息通过串行数据线(信号电缆线)传输。
1)接线端子说明(见图5-91)。
DC Link:伺服模块的主电路电源输入接线端子,连接电源模块PSM的DC300V输出端子及后续伺服模块的DC Link输入端子。
BATTERY:伺服电动机绝对编码器的电池盒(DC6V),与伺服模块CX5X连接。
CX5X、CX5Y:电动机绝对编码器电池连接接口,CX5X为输入、CX5Y为输出。
S1、S2:伺服接口类型设定开关,S1短接为A型接口,S2短接为B型接口。
JX5:伺服信号检测板连接接口。
CX2A、CX2B:分别为DC24V及急停信号的输入与输出接口。
JX1A、JX1B:分别为模块之间信息信号输入与输出连接接口。

图5-91 α系列双轴SVM实物及接口布置
JV1B、JV2B:A型伺服信号连接接口(双轴)。
JS1B、JS2B:B型伺服信号连接接口(双轴)。
JF1、JF2:B型伺服接口时,为伺服电动机编码器反馈信号接口(双轴)。
U、V、W:伺服电动机动力线接线端子(双轴)。
STATUS状态指示窗口(7段LED):7段LED不显示,表示控制电源未接通;7段LED显示“0”,表示伺服就绪;7段LED显示“-”,表示伺服未就绪;7段LED显示“#”,表示伺服报警代码。当SVM出现故障时,7段LED将显示相应的报警代码(见表5-7)。
表5-7 α系列伺服模块7段LED显示的报警代码及处理方法
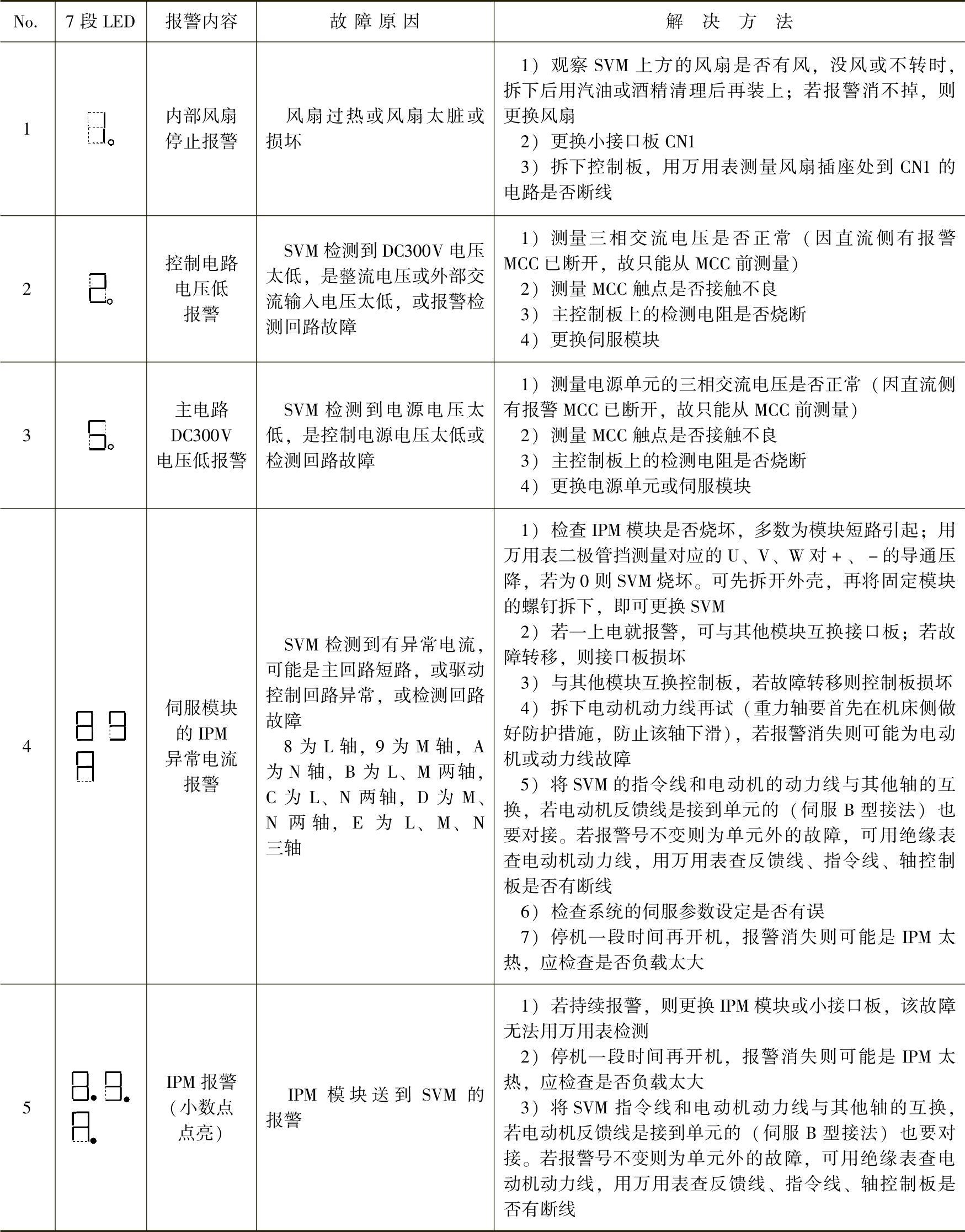
2)α系列伺服模块的连接(见图5-92)。
(4)αi系列伺服模块SVM的实物连接及接口布置 αi系列伺服模块用于FANUC 16i/18i/21i/0iB/0iC/0iD/30i系统的伺服轴驱动,其伺服信息通过高速串行总线HSSB(光缆)传输。
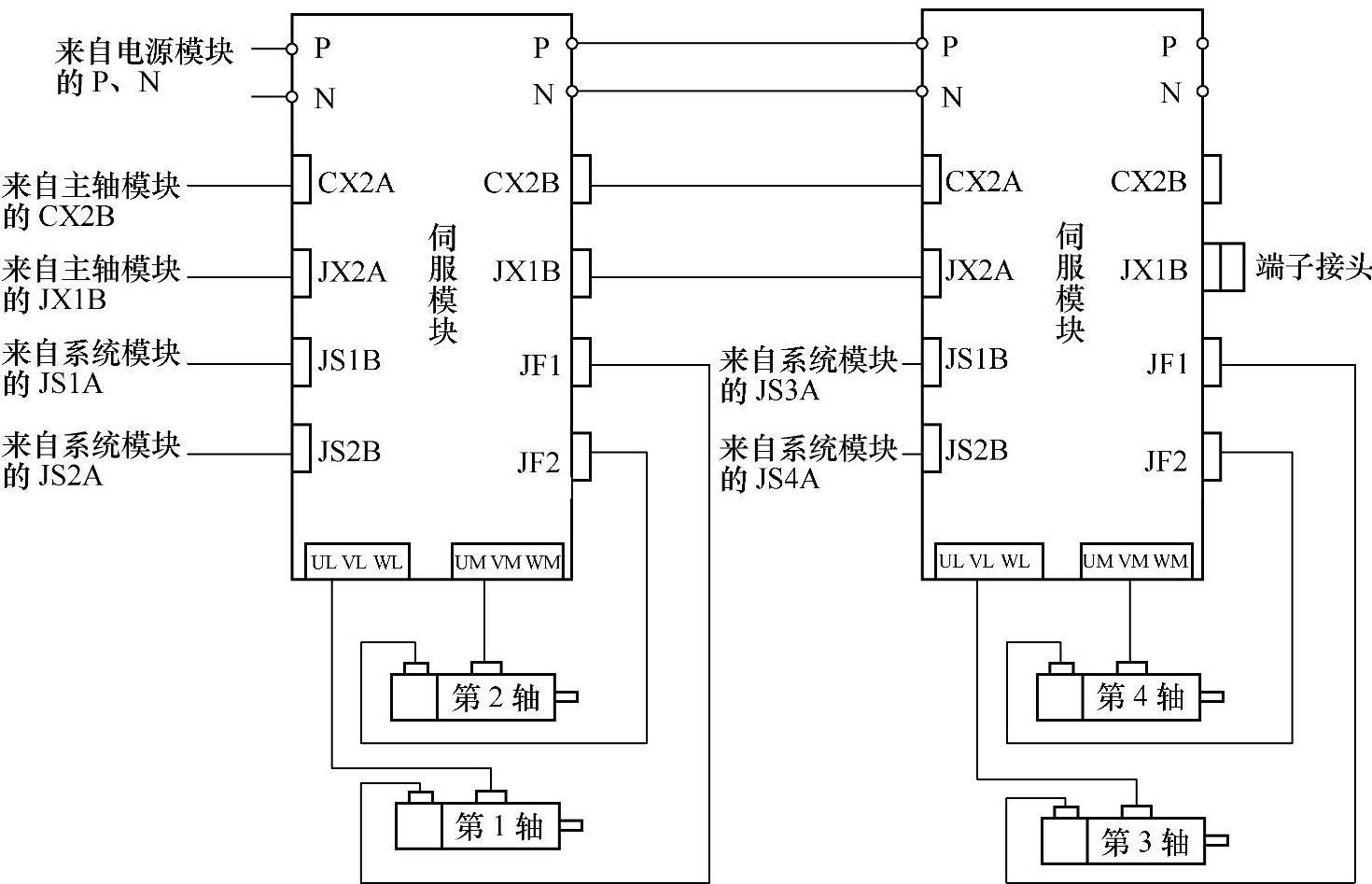
图5-92 FANUC 0iMA系统α系列伺服模块的连接(带第4轴的加工中心)
1)接线端子说明(见图5-93)。
BATTERY:伺服电动机绝对编码器的电池盒(DC6V)。
CX5X:伺服电动机绝对编码器的电池连接接口。
CX2A、CX2B:用于伺服模块间为DC24V电源、∗ESP急停信号、绝对位置编码器电池接线的连接(伺服模块绝对位置编码器供电方式分为由CXA2A、CXA2B供电和由CX5X单独供电两种方式),接线顺序为CXA2A至CXA2B。
COP10A、COP10B:伺服放大器的光缆接口,只要伺服放大器接通电源,每个光缆接口就会有1个光口发光。光缆口的连接顺序为COP10A至COP10B。光缆从CNC系统轴控制卡按轴号顺序依次连接各伺服放大器,连接的装置除了伺服放大器外还包括SDU单元(分离型检测单元和双安检功能时使用的FSSBI/O单元)。
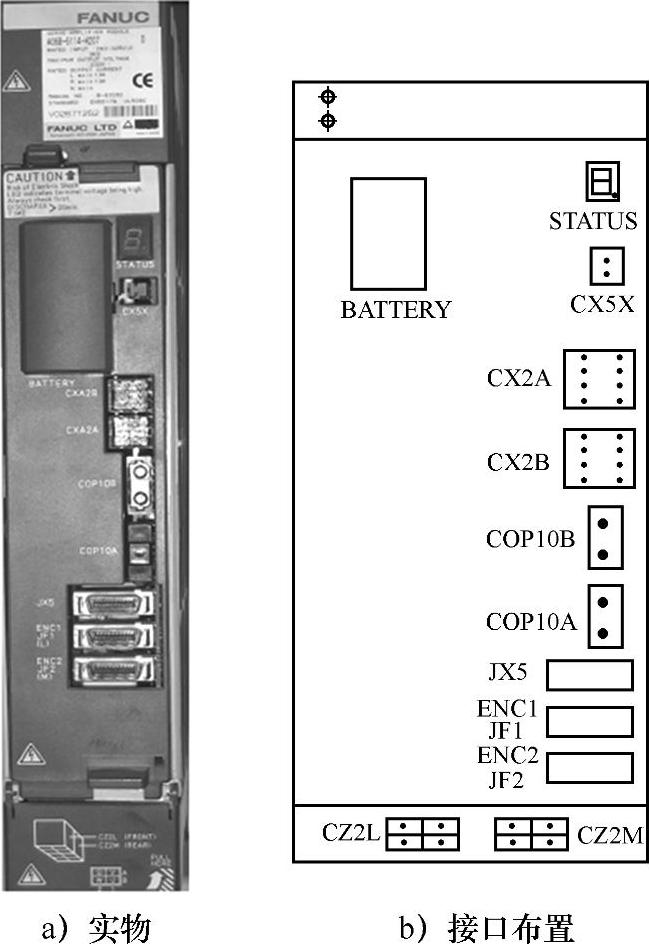
图5-93 αi系列双轴SVM实物及接口布置
JFn:伺服电动机编码器信号接口,单轴SVM仅有JF1,2轴SVM有JF1和JF2,3轴SVM有JF1、JF2和JF3。若编码器损坏或编码器的反馈线断线导致位置信息通信故障,系统将出现368号等伺服报警。信号种类与插接板上测脚号的对应关系见表5-8。
CZ2L/CZ2M:电动机动力线连接插口。
STATUS状态指示窗口(7段LED):伺服模块状态显示,显示报警号及小数点。αi系列伺服模块7段LED的显示状态及其报警内容见表5-9。
表5-8 信号种类与插接板上测脚号的对应关系
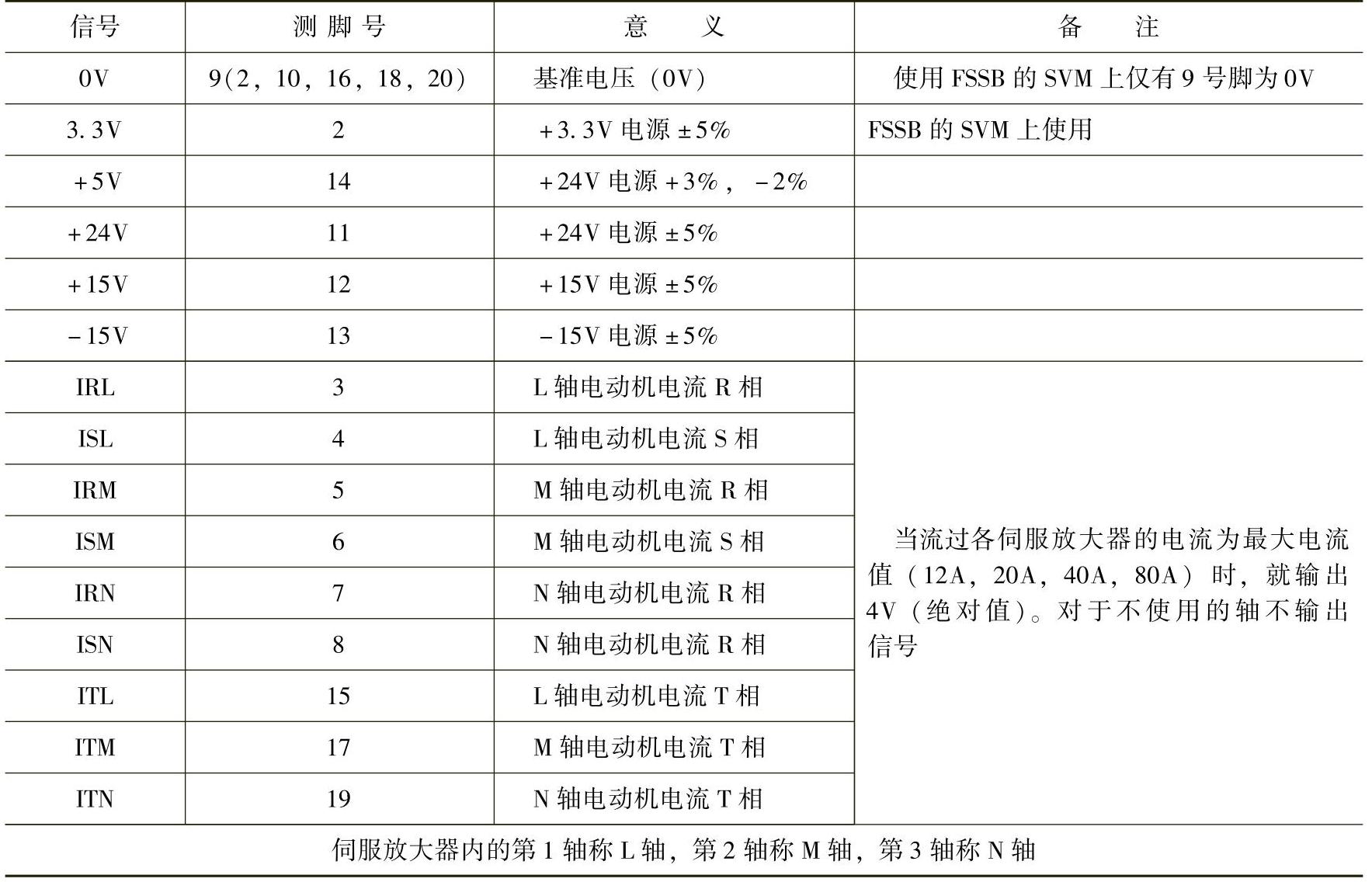
表5-9 αi系列伺服模块7段LED的显示状态及其报警内容
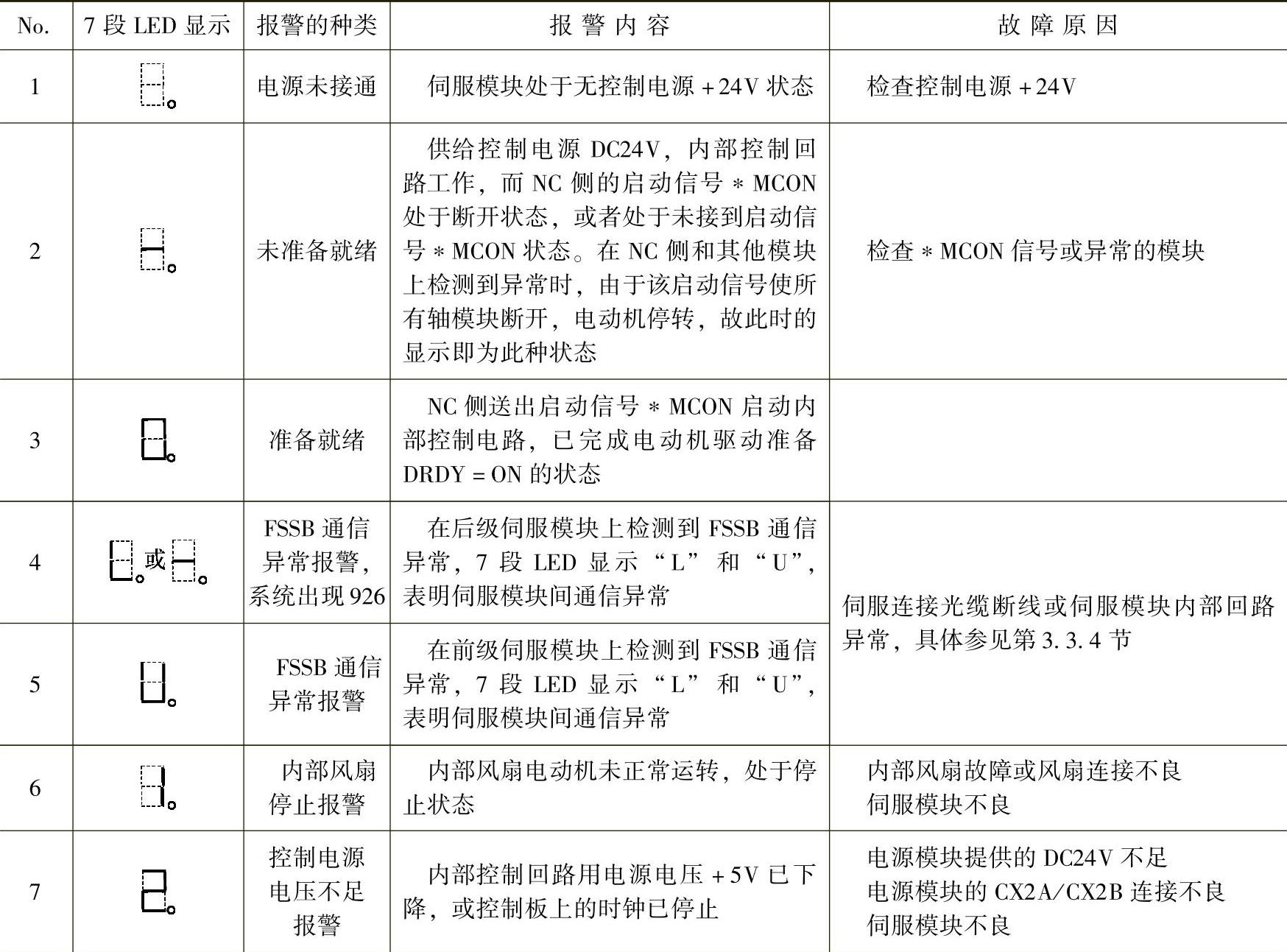
(续)
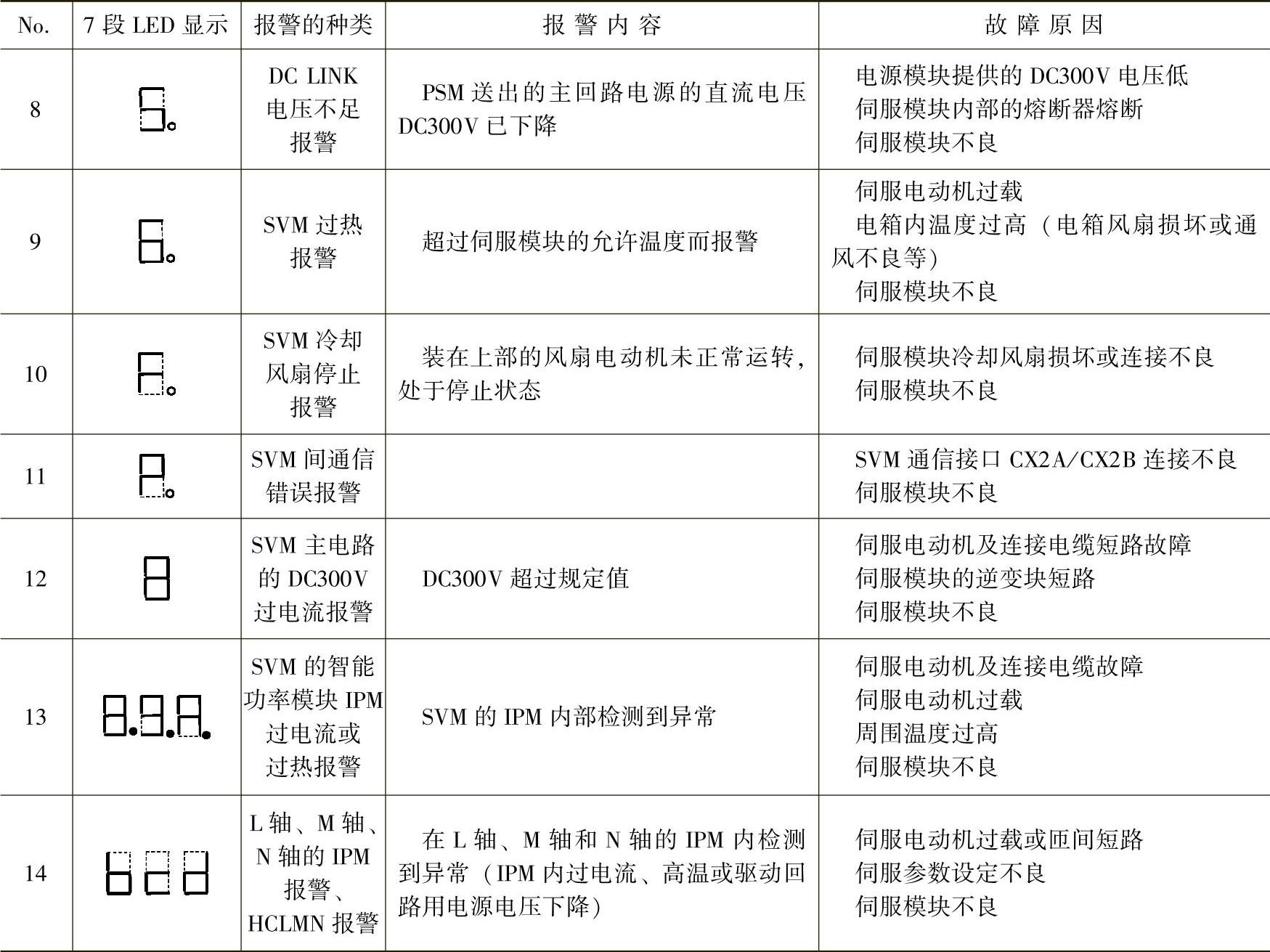
注:○表示小数点熄灭,●表示小数点点亮。
2)αi系列伺服模块的连接(见图5-94)。图5-94中的光缆连接取代了电缆连接,不仅保证了信号传输的速度,而且保证了传输的可靠性,减少了故障率。各模块之间的信息传递通过CX2A/CX2B的串行数据传输完成,而不再由信号电缆JX1A/JX1B(BCD码形式)传输,从而进一步减少了连接电缆。
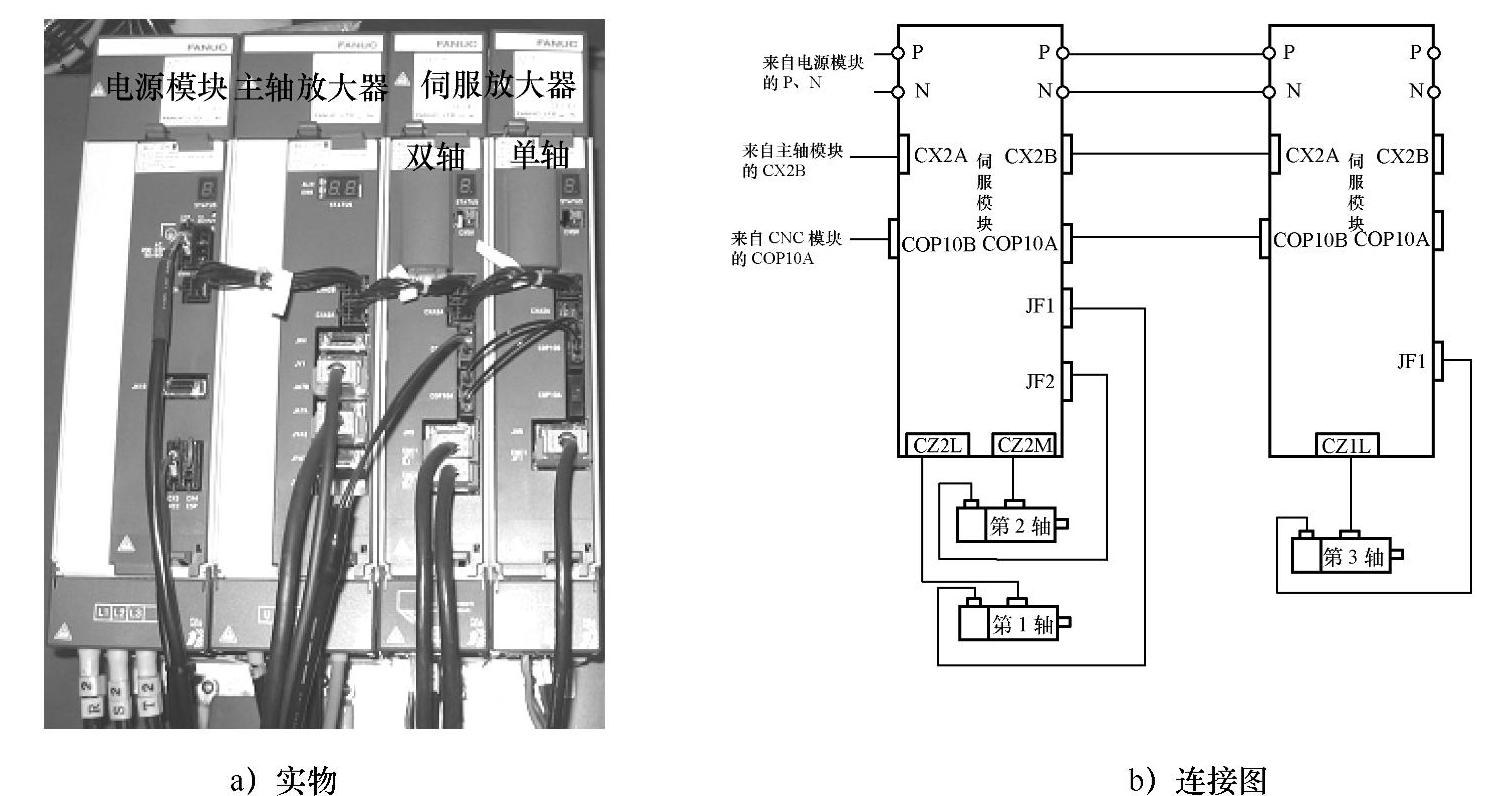
图5-94 FANUC0iMC系统αi系列伺服模块的连接(3轴)
(5)伺服轴虚拟化设置(屏蔽伺服放大器)伺服模块组内任何1个单元出现故障报警,均会引起所有单元VRDY_OFF(伺服准备未就绪)。当无法判断故障点时,可将故障轴虚拟化(又称屏蔽),也就是CNC系统不再向故障轴的伺服放大器发送指令,同时也不再读取该轴的反馈数据,从而将故障轴的信号屏蔽掉,并使其他伺服放大器准备就绪信号VRDY置1,维持其他伺服轴的正常工作。FANUC 18/18i/0i/30i系统的伺服轴虚拟化设置步骤如下:
1)设定CNC参数#1800.1/CVR=1(位置控制就绪信号PRDY接通之前,速度控制信号VRDY先接通时不出现伺服报警),以忽略伺服的上电顺序。
2)设定轴抑制参数#2009.0/DUMY=1,以抑制故障伺服轴的数据传输。
3)对于单轴伺服放大器,将待屏蔽的伺服Y轴的轴号参数#1023设定为-128,其后所对应的轴号设定依次前移(见图5-95)。
4)对于双轴伺服放大器,将待屏蔽的伺服Y轴(奇数轴不能被屏蔽,否则出现伺服参数设定非法417号报警)的轴号参数#1023设定为-128,同时短接相应的管脚:伺服放大器为FSSB接口时,短接插头JFY中的11和12管脚;为TypeA接口时,短接插头JVY中的8和10管脚;为TypeB接口时,短接插头JSY中的8和10管脚。若不插终端插头,双轴伺服放大器的另一伺服轴将出现伺服未就绪401号报警。另外,若要在LCD上不显示被屏蔽的Y轴,可设定CNC参数#3115.0/NDP=1(见图5-96)。
2.伺服电动机及故障
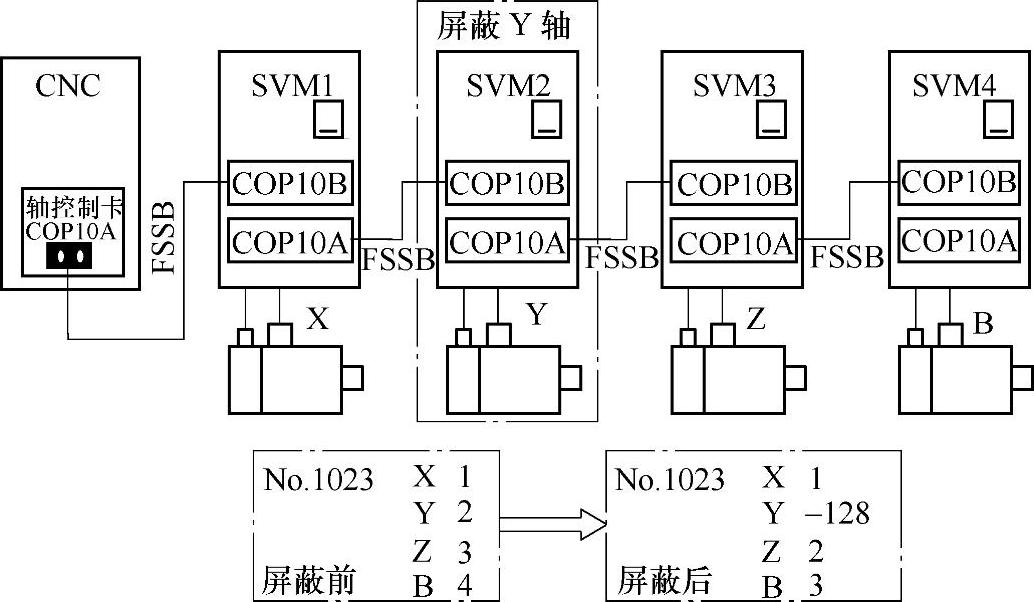
图5-95 单轴伺服放大器屏蔽Y轴的参数设定
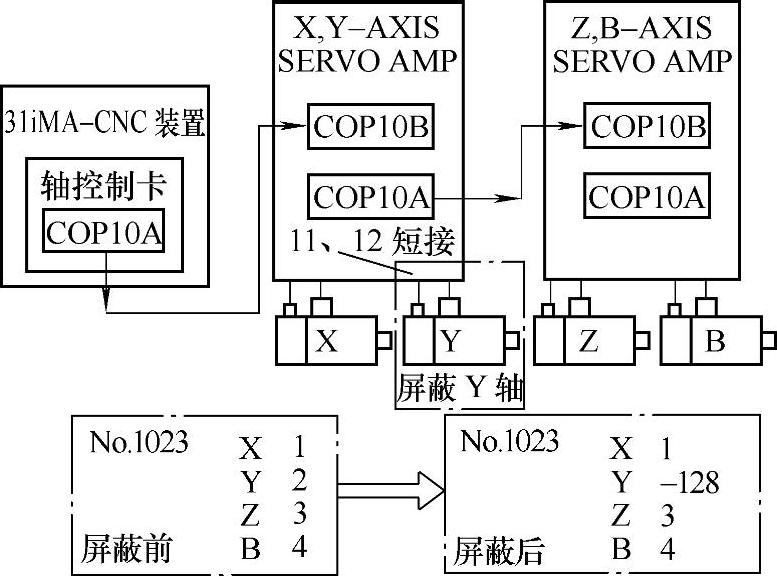
图5-96 双轴伺服放大器中屏蔽Y轴的设定
伺服电动机又称为执行电动机,在数控机床的机械传动中用作执行元件,负责将伺服放大器处理的电信号转换成电动机轴上的角位移或角速度输出,从而带动机械元件运动。目前,交流伺服系统中采用异步型交流电动机和同步型交流伺服电动机,FANUC公司的主轴电动机属于异步型交流感应电动机。而伺服电动机(见图5-97)属于永磁式同步型交流伺服电动机,其驱动回路通过位置环、速度环和电流环实现三环控制,并通过FSSB串行总线实现CNC与伺服放大器的通信。
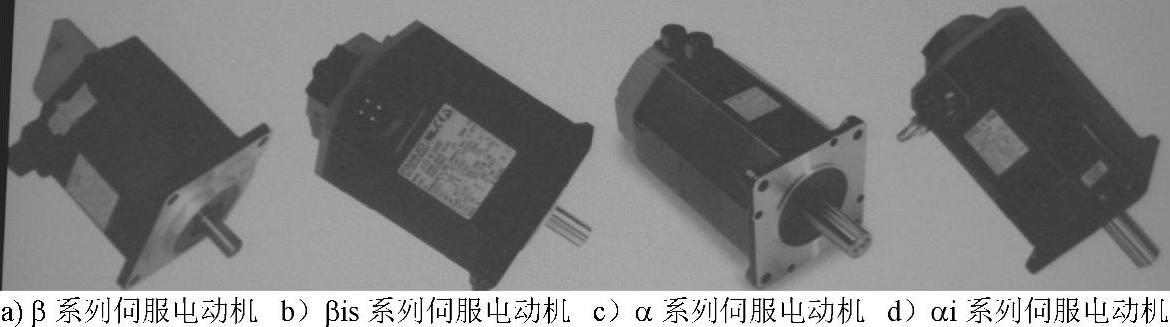
图5-97 FANUC公司的伺服电动机
(1)永磁式同步型交流伺服电动机的结构及控制原理目前,数控机床的进给执行元件都采用永磁式同步型交流伺服电动机,这类电动机主要由转子、定子和检测元件等部分构成(见图5-98)。其中,转子是用高导磁率的永久磁钢6作成的磁极,中间穿有电动机轴1,轴两端用支承轴承13支承并将其固定于机壳上;定子5是用矽钢片叠成的导磁体,导磁体的内表面有齿槽,嵌入用导线绕成的三相绕组线圈3;电动机轴1后端部装有脉冲编码器9。
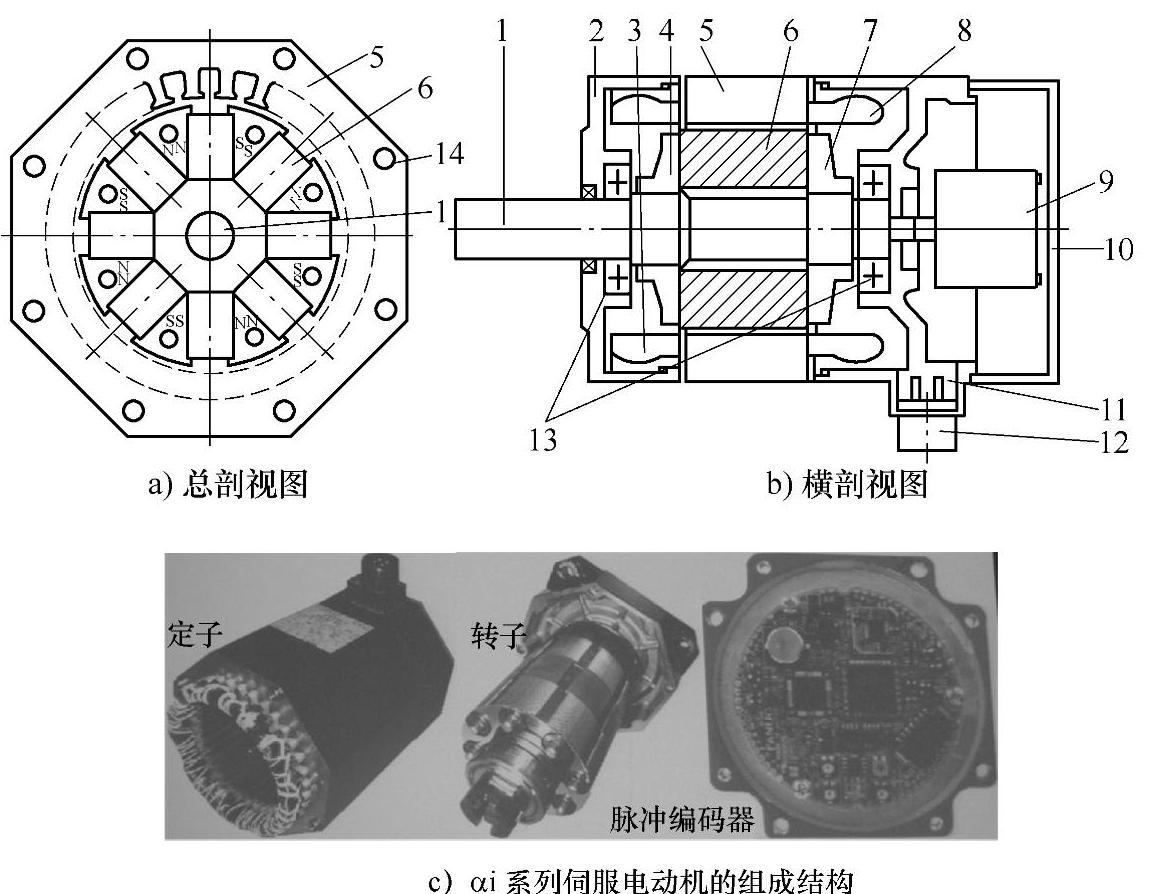
图5-98 FANUC公司永磁式同步型交流伺服电动机结构图
1—电动机轴 2—前端盖 3—三相绕组线圈 4—压板 5—定子 6—永久磁钢 7—后压板 8—后端盖 9—脉冲编码器 10—电动机后盖 11—动力线插头 12—反馈插头 13—支承轴承 14—通风口
当定子5的三相绕组线圈3通有三相交流电流时,产生的空间旋转磁场就会吸住转子上的永久磁钢6同步旋转。同步电动机的速度控制与电功率的提供由三相逆变器实现,逆变器中从直流变到三相交流的功率驱动电路元件需要根据转子磁场的位置实时地换向,这一点非常类似于直流电动机的转子绕组电流随定子磁场位置的换向。因此,为了实时地检测同步电动机转子磁场的位置,在电动机轴1的后端安有一个内装型转子位置检测装置(一般为霍尔开关或具有相位检测的光电脉冲编码器,见图5-99)。由于转子位置检测装置的存在,无论伺服电动机的转速是快还是慢,均可随着电动机轴1的回转实际地测出转子上磁极磁场的位置,并将该位置值送至控制电路后,使控制器实时地控制逆变器功率元件(即定子绕组的开关器件)的换向(即有序轮流导通),实现伺服放大器的自控换向,从而使电动机的转子连续不断地旋转。也就是说,利用转子的位置控制定子的电流,使定子电流产生的磁势超前于转子磁势90°。
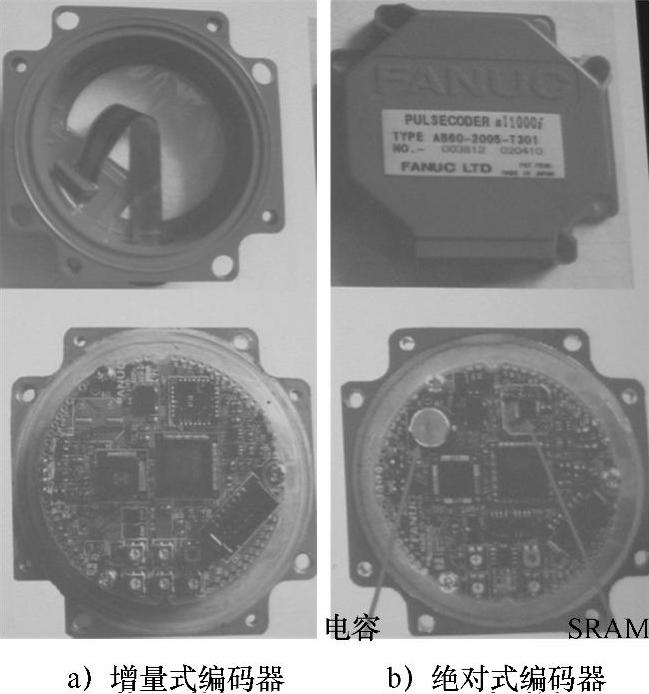
图5-99 FANUC公司αi系列伺服电动机内装编码器
(2)交流伺服电动机的常见故障及处理方法交流伺服电动机不存在电刷的维护问题,所以又称为免维护电动机,但这并不是说交流伺服电动机绝对不出现故障。使用过程中,交流伺服电动机常因接线故障(如动力线插座或反馈插座脱焊、端子接线松开)、转子位置检测装置(霍尔开关或光电编码器)不良或损坏、垂直轴电磁制动未释放(防止系统或伺服断电、报警时伺服电动机成为自由状态情况下的下滑)、伺服轴使能条件未满足等故障,致其不能转动或发热严重等。故障排除过程大致如下:
1)检查交流伺服电动机是否受到碰撞等机械损伤,避免电动机内的转子位置检测装置因碰撞或冲击等产生损坏。
2)检查切削液、润滑油等是否浸入伺服电动机内部(因其防水结构不是很严密),避免电动机绝缘性能的下降或定子三相绕组的短路。当伺服电动机安装在齿轮箱上时,齿轮箱内润滑油的油面必须低于电动机输出轴的高度,以防止润滑油沿输出轴渗入电动机内部。
3)通过PMCLAD梯形图显示画面或PMCDGN诊断画面下的STATUS状态子画面,查看机床伺服准备好信号F0.6/SA是否接通。若F0.6/SA=0,则根据FANUC系统驱动部分上电过程的控制(见图4-134)查找伺服未准备好的原因,并排除之。
FANUC系统驱动部分的上电过程:控制电源2相200V接入→连接器CX4的急停信号∗ESP释放→若无MCC断开信号MCOFF(变为0),则发出请求电源模块准备信号∗MCON给所有SVM→电源模块准备好后发出MCC接触器触点吸合信号→外部MCC接触器吸合→3相200V动力电源接入→电源模块整流输出DC300V并发出就绪信号∗CRDY→若SVM准备就绪,则向CNC发送∗DRDY准备好信号(Digital Servo Ready,DRDY)→CNC向PMC发送伺服准备信号SA(Ser-vo Already,SA)→一个上电周期完成。
4)通过PMCLAD梯形图显示画面或PMCDGN诊断画面下的STATUS状态子画面,查看机床伺服轴移动中信号是否接通(X轴F102.0/MV1,Y轴F102.1/MV2,Z轴F102.2/MV3,B轴F102.3/MV4),若未接通,则为CNC未发出伺服轴控制指令,故障原因可能为轴控制卡或CNC主板故障。更换配件,排除故障。
5)对于垂直轴伺服电动机(见图5-100),应通过PMCLAD梯形图显示画面或PMCDGN诊断画面下的STATUS状态子画面,检查电磁制动器信号Y0009.1是否接通(即伺服电动机励磁后制动器是否打开)。若Y0009.1=1,则检查电磁制动器连接电缆是否断线或电磁制动器自身存在故障;若Y0009.1=0,则核对PMC顺序程序中与制动释放相关的条件是否未满足。通常以伺服准备就绪信号F0000.6/SA为垂直轴制动解除的控制信号,F0000.6=1时制动释放,F0000.6=0时制动关闭。
6)将伺服电动机的动力线拆掉,使用万用表检测电枢电阻、用兆欧表检测电动机的绝缘情况(见图5-101),用钳形电流表或电桥绕组进行平衡检测。
①用万用表检测电动机定子三相绕组分别对地的电阻,正常时为
/无穷大;以及三相绕组之间的电阻,正常为几欧到几十欧,且电阻值应平衡。
②钳形电流表或电桥绕组平衡检测:正常时
,若I0≥5%,则电流小得一相匝间短路;正常时
,若R0≥5%,则电阻值小得一相匝间短路。
7)将故障伺服轴的机械传动装置(如滚珠丝杠副等)与伺服电动机脱开,用手转动电动机的转子,正常情况下应感觉存在均匀的阻力,当转一个角度后放开手,电动机转子有返回现象;若用手转动转子时能连续转几圈并自由停下,说明电动机损坏;若用手转不动或转动后无返回,则伺服轴的机械传动部分存在故障(如导轨副或滚珠丝杠副等状态不良)。
8)当伺服电动机的脉冲编码器不良时,应更换脉冲编码器。注意:原连接部位无定位标记的,编码器不能随便拆离,否则将相位错位;采用霍尔元件换向的,应标记好开关的出线顺序;拆装时,做好电动机转子的失磁防护。
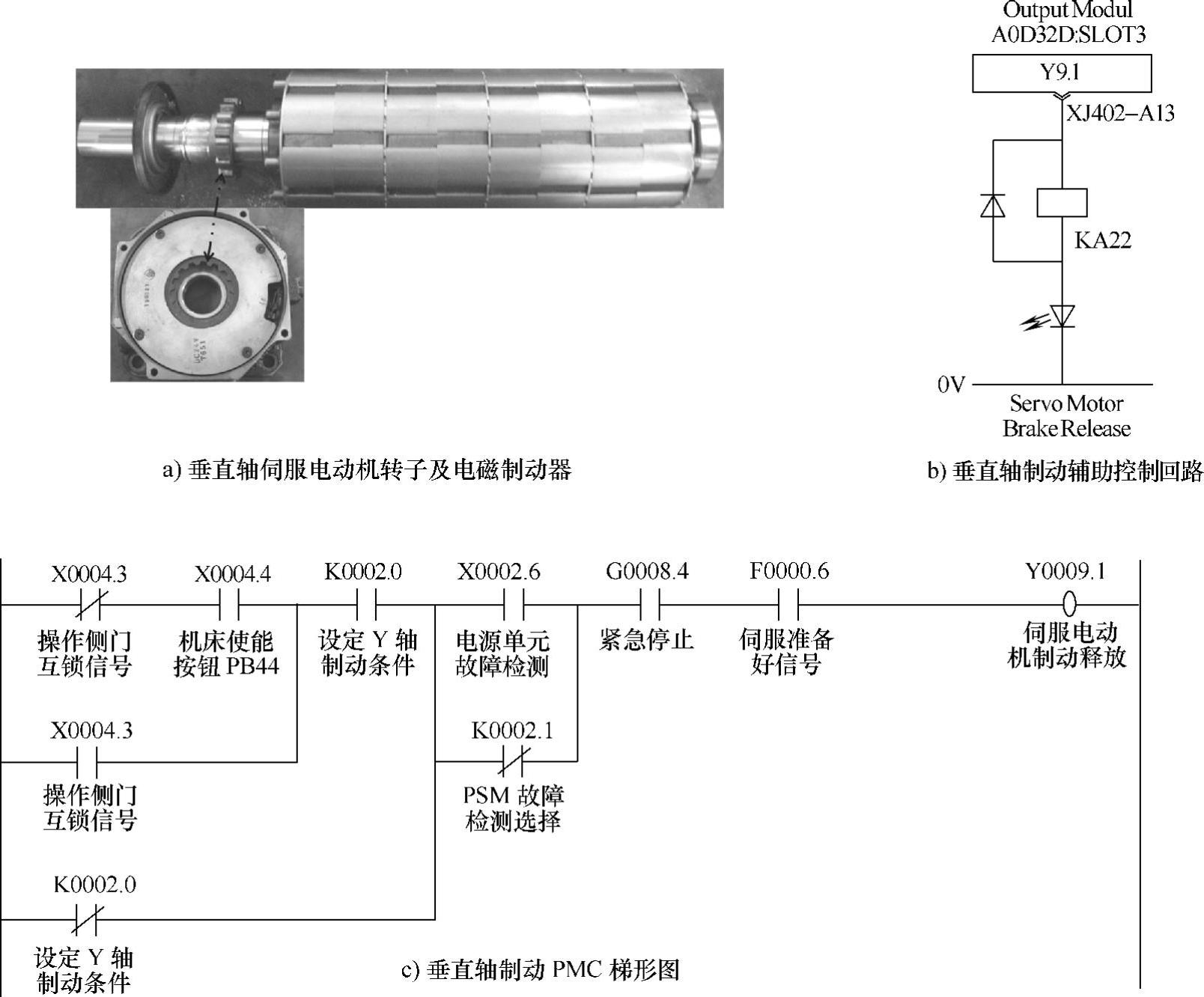
图5-100 HM1250卧式加工中心(FANUC 31iMA系统)Y轴伺服电动机的制动控制
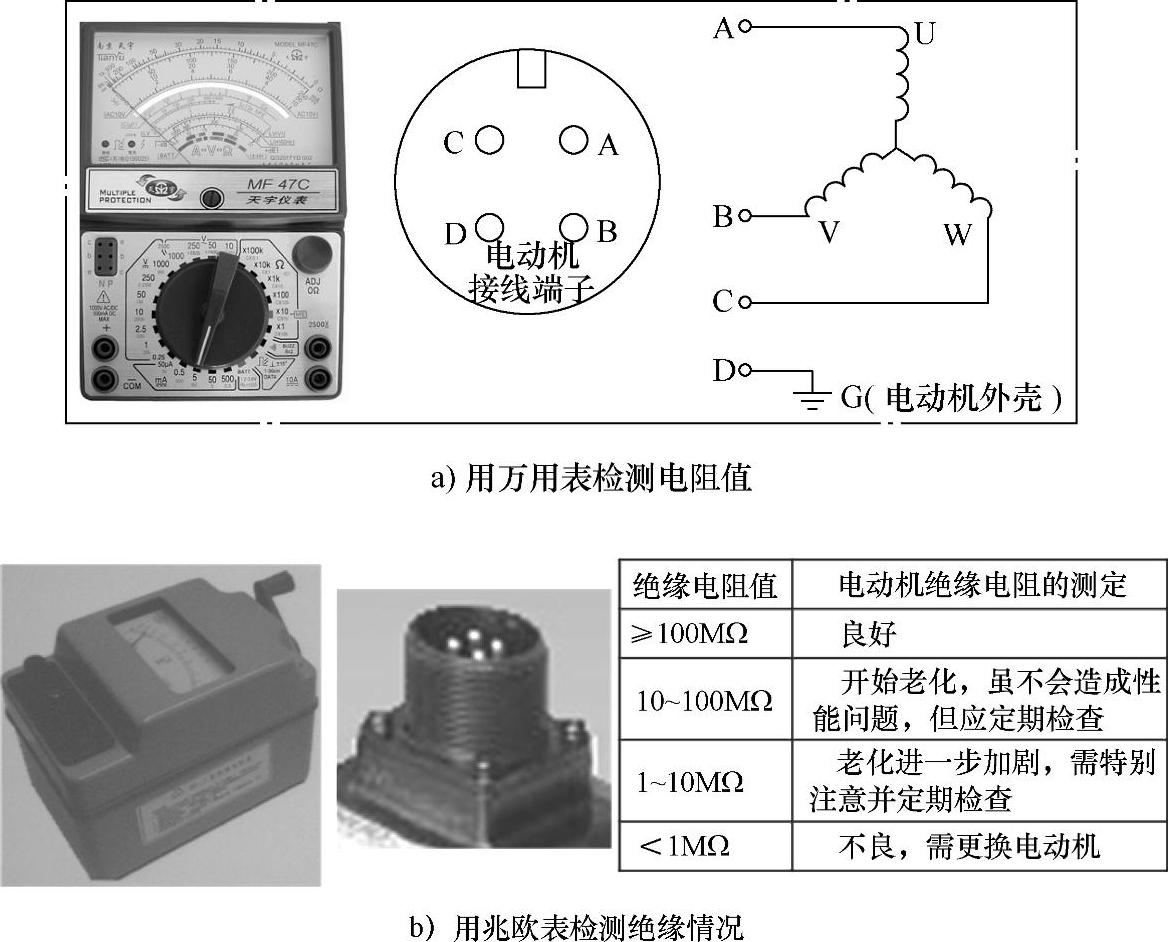
图5-101 FANUC公司交流伺服电动机的检测
9)另外,伺服电动机的定子中预埋有热敏电阻(见图5-102),当出现过热报警时,应检查电动机的热敏电阻是否正常。
10)交流伺服电动机通过联轴器与滚珠丝杠副等连接后,应通过机床操作监视画面(面板上[POS]功能键→最右侧扩展[▶]软键出现“监控”软键条→按[监控]软键即可进入操作监视画面)对伺服轴空载时的负载情况进行监控(空载时的正常负载率<40%,见图5-103),避免因预紧力大造成负载过大而影响电动机的正常运行。
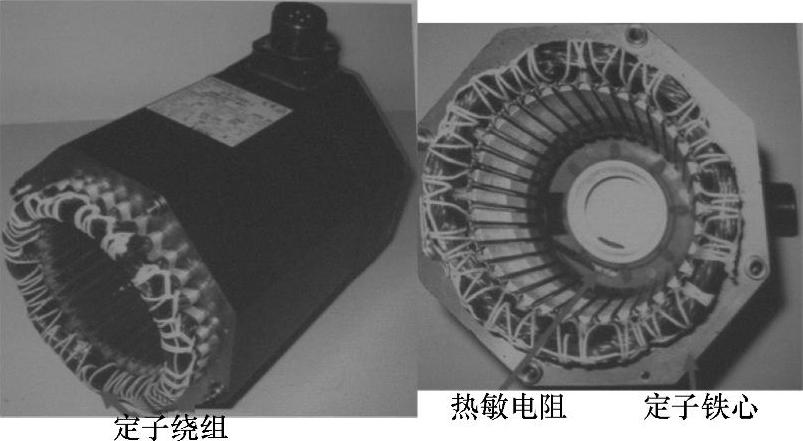
图5-102 αi系列伺服电动机的热敏电阻
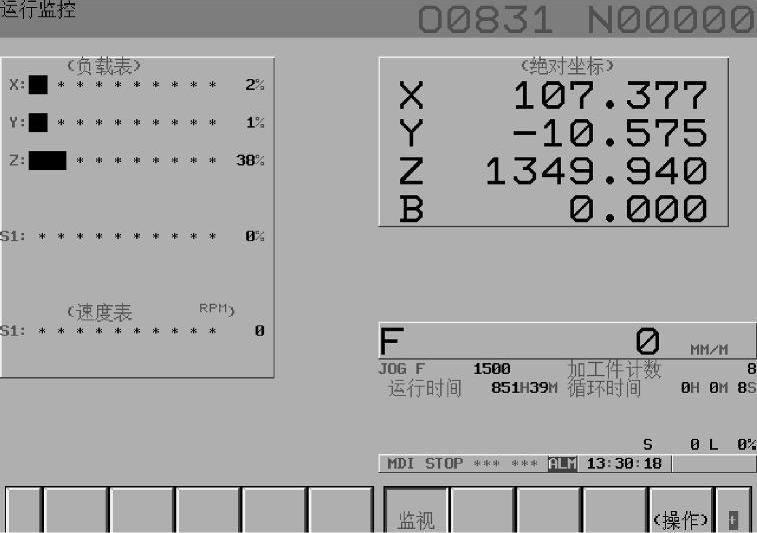
图5-103 ACE-H100卧式加工中心(FANUC 18iMB系统)空载时负载率的监控
3.位置检测装置及故障
CNC装置和位置检测装置是现代数控机床的关键部件,其中,位置检测装置是保证数控机床实现精确定位和高精度加工的前提条件。位置检测装置是闭环(半闭环、闭环或混合闭环)进给伺服系统中重要的组成部分,它检测机床工作台的位移、伺服电动机转子的角位移和速度,并将信号反馈至伺服放大器或CNC装置,与预先给定的理论值相比较,得到的差值用于实现位置闭环控制和速度闭环控制。位置检测装置通常利用光或磁的原理完成对位置或速度的检测,其测量精度一般用分辨率来衡量。分辨率是检测元件所能正确检测的最小数量单位,它由检测元件本身的品质及测量电路决定。在CNC位置检测接口电路中常对反馈信号进行倍频处理,以进一步提高测量精度。位置检测装置也可以用于速度的测量,位置检测和速度检测可采用各自独立的检测元件,如速度检测采用测速发电机,位置检测采用光电编码器;也可共用一个检测元件,如均为光电编码器。
(1)位置检测装置的分类
1)直接测量和间接测量。根据机床的运动方式,可将位置检测装置分为直线型和回转型。若检测元件所测量的指标就是所要求的参数指标,即直线型检测元件测量直线位移、回转型检测元件测量角位移,则该测量方式为直接测量。典型的直接测量装置有光栅、编码器等。若回转型检测元件测量的角位移仅是中间量,由它再推算出与之对应的工作台直线位移,那么该测量方式为间接测量,其测量精度取决于检测元件和机床传动链两者的精度。典型的间接测量装置有码盘和旋转变压器(见图5-104)。
2)增量式测量和绝对式测量。按测量装置编码方式可分为增量式测量和绝对式测量。增量式测量的特点是只测量位移增量,即工作台每移动一个基本长度单位,检测元件便发出一个测量信号,此信号通常是脉冲形式。典型的增量式检测元件为光栅和增量式光电编码器。绝对式测量的特点是被测的任一点的位置均由一个固定的零点算起,每一个测量点都有一个对应的测量值,常以数据形式表示。典型的绝对式检测元件为绝对式光电编码器。
3)接触式测量和非接触式测量。接触式测量的检测元件与被测对象间存在着机械联系,因此机床本身的变形、振动等因素会对测量产生一定的影响。典型的接触式检测元件为光栅。非接触式测量的检测元件与被测对象是分离的,不发生机械联系(通过光或磁联系)。典型的非接触式检测元件有双频激光干涉仪和光电式编码器。
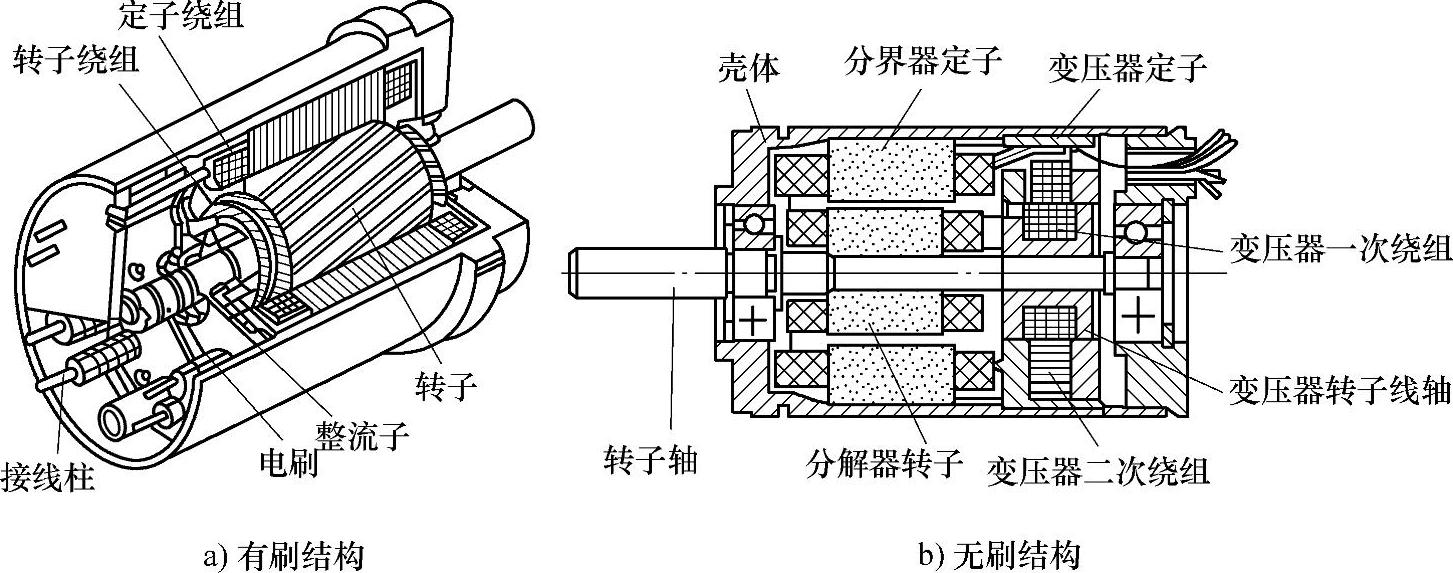
图5-104 旋转变压器的结构图
4)数字式测量和模拟式测量。数字式测量以量化后的数字形式表示被测量,它的特点是检测元件简单、信号抗干扰能力强且便于显示处理。典型的数字式检测元件为光电编码器和光栅。模拟式测量是被测量用连续的变量表示,如用电压、相位的变化来表示。典型的模拟式检测元件为旋转变压器等。
5)内装型和分离型。按连接型式的不同,可分为伺服电动机内装型编码器检测装置和分离型检测装置。内装型编码器检测装置为增量式编码器或绝对式编码器,分离型检测装置的典型代表为光栅尺。
综上所述,数控机床所使用的位置检测装置包括光电编码器、旋转变压器、感应同步器、光栅、磁栅尺等数十种。本书将着重介绍最常用的增量式光电编码器、绝对式光电编码器和光栅3种检测元件。
(2)增量式光电编码器的控制原理光电编码器利用光电原理把机械角位移变换成电脉冲信号,是数控机床最常用的位置检测元件。光电编码器按输出信号与对应位置的关系,通常分为增量式光电编码器、绝对式光电编码器和混合式光电编码器。
增量式光电编码器由光源5(白炽灯、硅光电池或发光二极管等)、透镜6、光电码盘4(玻璃材料)、光栏板7、光敏元件8和信号处理电路等组成(见图5-105)。当光电码盘4随工作轴1一起转动时,光源5通过透镜6,透过光电码盘4和光栏板7形成忽明忽暗的光信号;光敏元件8把此光信号转换成电信号,然后通过信号处理电路的整形、放大、分频、计数和译码后输出给CNC系统。为了测量码盘的转动方向,光栏板7的两个狭缝距离应为m±
/4(
为码盘两个狭缝之间的距离即节距,m为任意整数),这样两个光敏元件的输出信号(分别称为A信号和B信号)相差π/2相位,将输出信号送入鉴相回路,即可判断出码盘的旋转方向。
增量式光电编码器的测量精度取决于它所能分辨的最小角度α(分辨角或分辨率),而这与码盘圆周内所分狭缝的条数有关,且α=360°/狭缝数。由于光电式脉冲编码器每转过1个分辨角就发出1个脉冲信号,因此根据脉冲数目可得出工作轴的回转角度,由传动比换算出直线位移距离;根据脉冲频率,可得出工作轴的转速;根据光栏板上2个狭缝中信号的相位先后,可判断出光电码盘的正反转。
另外,在光电编码器码盘和光栏板的内圈均增加1条透光狭缝,并增加1个光敏元件,每转1圈产生1个零位脉冲信号。在进给电动机所用的编码器上,零位脉冲用于精确确定机床的参考点,而在主轴电动机上则用于主轴准停和螺纹加工等。增量式光电编码器输出信号的种类有差动输出、电平输出和集电极(OC门)输出等。其中,差动信号因抗干扰能力强而得到广泛的采用。CNC装置的接口电路通常对接收到的增量式光电编码器的差动信号作4倍频处理,以提高检测精度。光电编码器的安装有两种形式:一种是安装在伺服电动机的非输出轴端称为内装式编码器,用于半闭环控制;另一种是安装在传动链末端称为外置式编码器,用于闭环控制。

图5-105 增量式光电编码器的控制原理
1—工作轴 2—滚动轴承 3—透光狭缝 4—光电码盘 5—光源 6—透镜 7—光栏板 8—光敏元件 9—编码器壳 10—反馈电缆
伺服电动机上常用的增量式光电编码器规格有2000P/r、2500P/r、3000P/r、1024P/r、2048P/r等,也有高分辨率的可达20000P/r、25000P/r和30000P/r等。
(3)绝对式光电编码器的控制原理绝对式光电编码器通过读取码盘上所刻的透光和不透光的编码图案来确定位置,图案可采取二进制、二进制循环码(格雷码)或二至十进制编码等编码方式。图5-106b中码盘上有4圈码道(按二进制规律将码盘刻制成透明和不透明相间的同心圆),在码盘的一侧安装LED光源,另一侧安装一排径向排列的光电管(受光元件),每个光电管对准1条码道。当光源照射码盘时,透明区的光线被光电管接受并转变成电信号,输出信号为“1”;不透明区的光电管不接受光线,输出信号为“0”。被测工作轴带动码盘旋转时,光电管输出的信息就代表了轴的对应位置(绝对位置)。
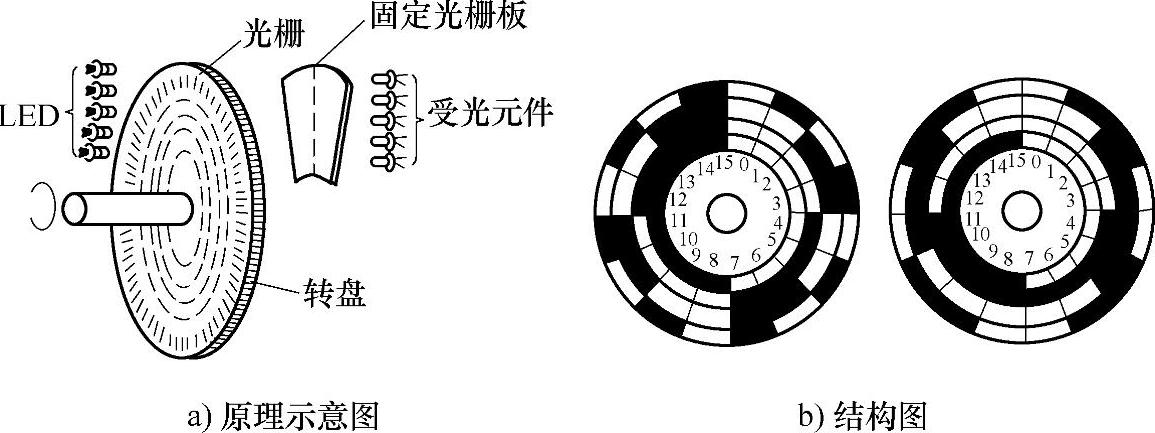
图5-106 绝对式光电编码器的控制原理
绝对式光电编码器多采用格雷码方式的码盘,编码盘的数码表见表5-10。格雷码的特点是码盘转至相邻区域时编码中仅有1位发生变化;这样即使制作和安装不十分准确,产生的误差最多仅为最低位的1位数。绝对式光电编码器的分辨率与码盘的码道数有关,即码道数越多,其分辨率越高(如4位格雷码盘的分辨率为α=360°/24=22.5°)。目前,码盘的码道数可达18条,分辨率为α=360°/218=0.0014°。
绝对式光电编码器转过的圈数由RAM保存,断电后则由后备电池供电,以保证机床的位置在断电或断电后虽移动过也可正确地记录下来。因此,采用绝对式光电编码器作为伺服电动机检测元件的数控机床,只要出厂时建立好机床坐标系,以后就不用再进行返回参考点的操作(后备电池失电或更换编码器时除外)。
表5-10 编码盘的数码表
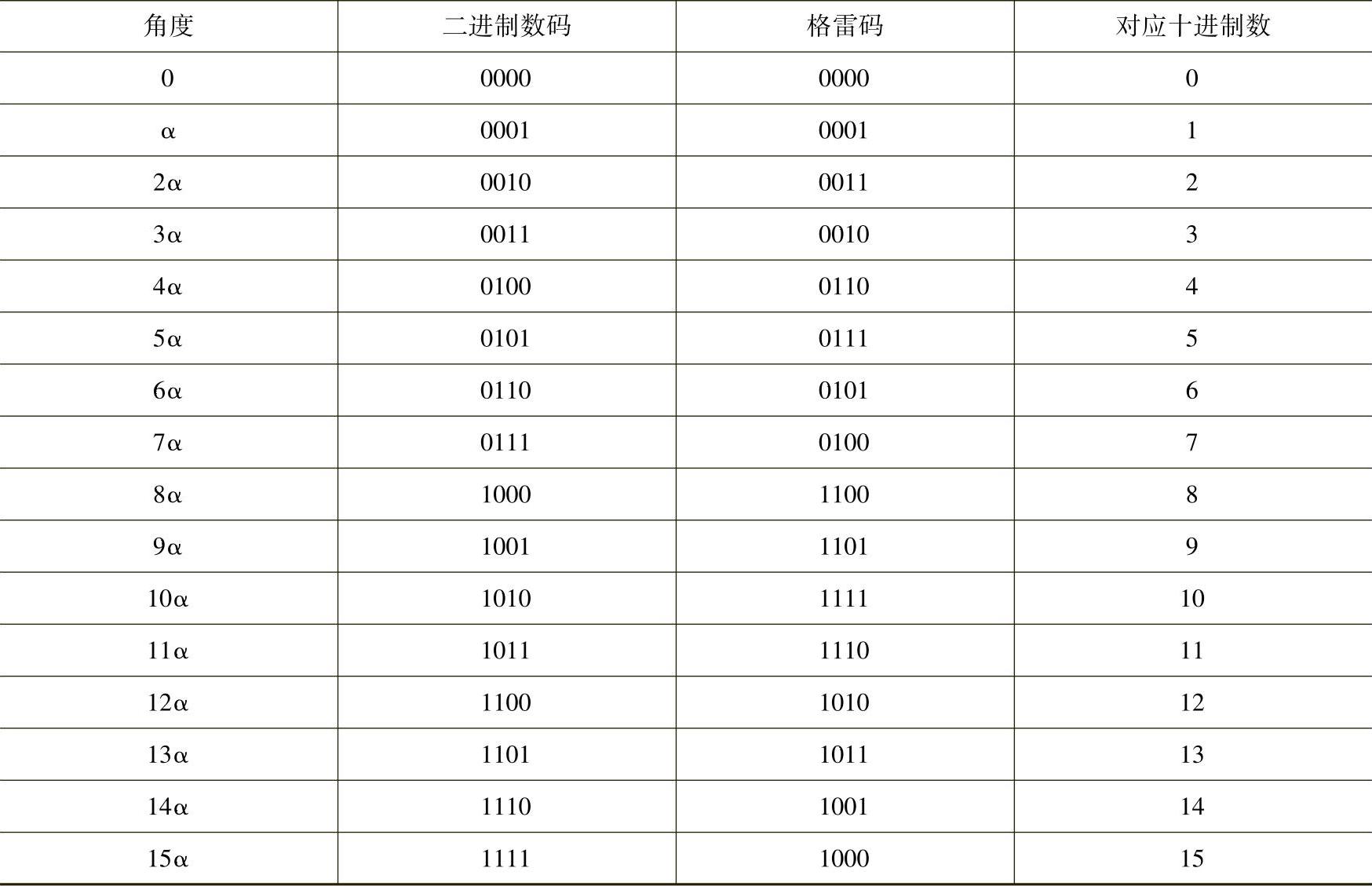
(4)伺服电动机内装型编码器的报警及故障维修
1)内装型增量式编码器与内装型绝对式编码器的区别。通过伺服电动机内装型编码器实现进给伺服的位置和速度反馈控制,属于半闭环控制。内装型编码器有增量式和绝对式两种。采用增量式光电编码器时,机床的位置依靠系统电池记忆,但记忆的坐标值为机床断电前的位置,当增量式光电编码器上电时仅与系统进行通信而不进行数据的交换(不更新机床坐标值),所以采用增量式光电编码器的数控机床开机时必须返回参考点。采用绝对式光电编码器时,系统开机时不仅与编码器进行通信控制,而且实现数据的交换(更新机床坐标值),使系统机械坐标值与机床的实际位置保持一致,所以采用绝对式光电编码器的数控机床开机可不进行返回参考点的操作。
2)FANUC系统串行编码器(SPC)的报警代码及故障原因。目前,伺服电动机内装编码器数据传输采用串行数据传输,当编码器传输出错或异常时,CNC系统出现报警号及相关报警信息。FANUC0C/0D系统伺服电动机内装编码器报警为“3n9#串行编码器通信报警”(n为伺服轴号),FANUC 16/18/21/0iA系统报警为“350#串行编码器异常报警”和“351#串行编码器通信异常报警”,FANUC 16i/18i/21i/0iB/0iC/0iD/30i系统的串行编码器的报警代码及故障原因见表5-11。FANUC 16i/18i/21i/0iB/0iC/0iD/30i系统串行编码器报警不仅能诊断出伺服电动机内装编码器报警,而且还可以诊断出分离型编码器报警,系统的故障诊断内容更加具体,可为维修提供详细的故障信息。
3)FANUC系统串行编码器(SPC)报警故障的诊断方法。当FANUC系统出现串行编码器报警时,可通过系统诊断画面(按[SYSTEM]功能键→[DGNOS]软键便显示该画面)相应的诊断号进行故障原因的判别,FANUC 0C/0D系统诊断号为760~767和770~777,FANUC 18/18i/0i/30i系统诊断号为202和203;也可通过系统伺服调整画面的报警3和报警4进行判别(见图5-107)。
表5-11 FANUC 16i/18i/21i/0iB/0iC/0iD/30i系统串行编码器的报警代码及故障原因
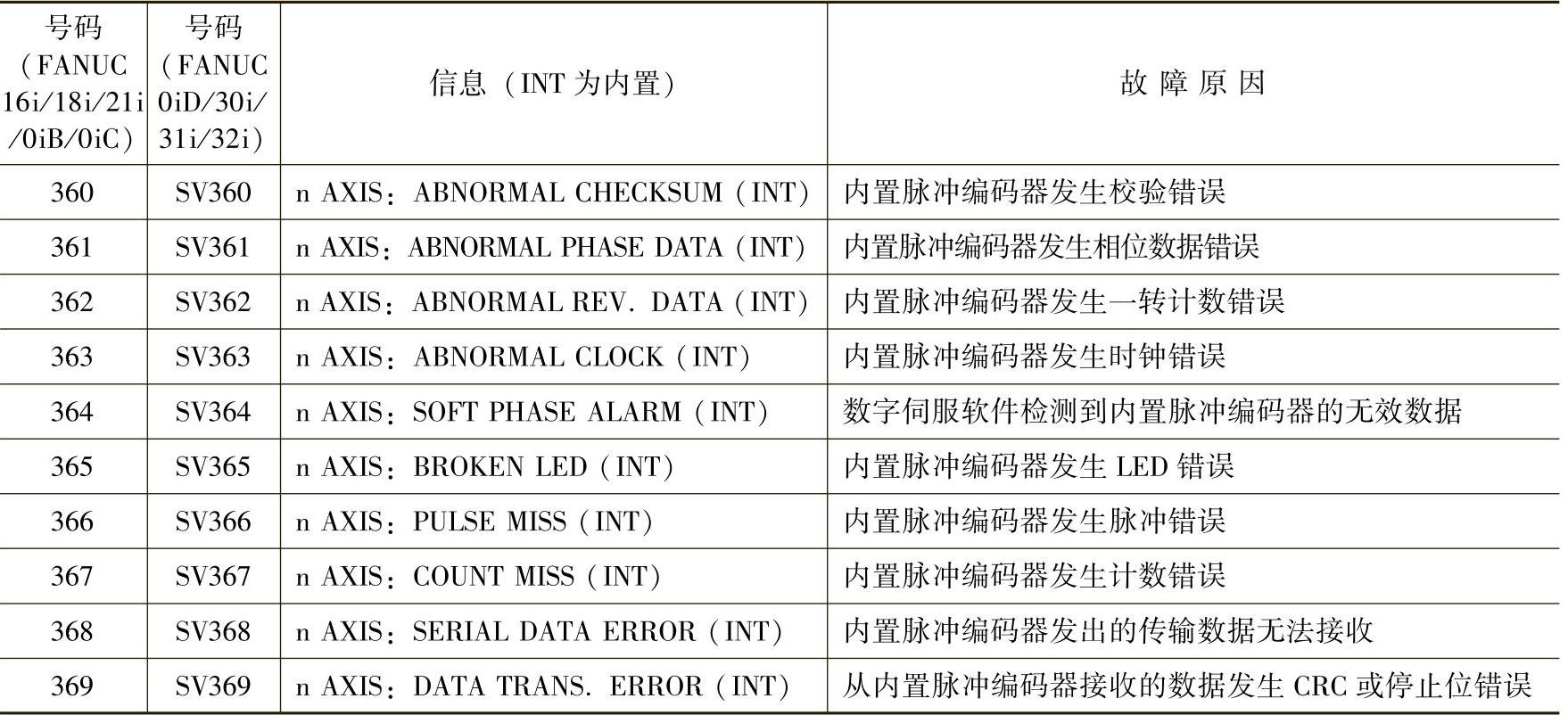
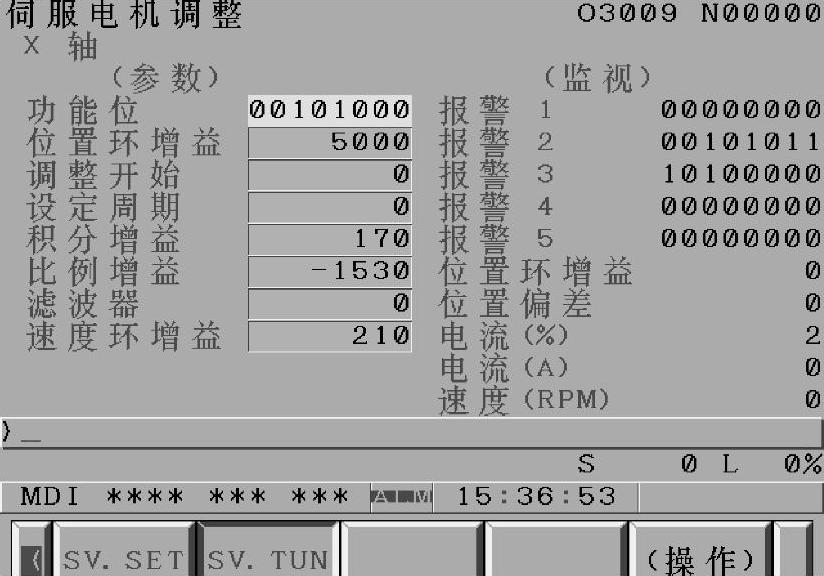
图5-107 FANUC系统的伺服调整画面

系统伺服调整画面的报警3
#6(CSA)1:串行脉冲编码器硬件异常报警;需要更换串行脉冲编码器
#5(BLA)1:电池的电压不足报警,与No.350报警无关;需要更换电池
#4(PHA)1:串行脉冲编码器或反馈电缆异常报警(反馈信号计数器错误);需要更换
#3(RCA)1:串行脉冲编码器异常报警(转速计数器错误);需要更换
#2(BZA)1:电池的电压为0报警,与No.350报警无关;需要更换电池,并重设参考点
#1(CKA)1:串行脉冲编码器异常报警(内部时钟停止);需要更换
#0(SPH)1:串行脉冲编码器或反馈电缆异常报警(反馈信号计数器错误);需要更换

系统伺服调整画面的报警4
#7(DTE)1:串行脉冲编码器通信异常报警(通信无应答);有可能是编码器、反馈电缆
或反馈接收电路存在故障;需要更换之
#6(CRC)1:串行脉冲编码器通信异常报警(传送数据错误);有可能是编码器、反馈电
缆或反馈接收电路存在故障;需要更换之
#5(STB)1:串行脉冲编码器通信异常报警(传送数据错误);有可能是编码器、反馈电
缆或反馈接收电路存在故障;需要更换之
#4(PRM)0:No.417:nAXIS Parameter Incorrect报警(CNC侧参数设定错误);进一步查
看诊断号280
1:No.417:nAXIS Parameter Incorrect报警(数字伺服侧参数设定错误);进一步
查看诊断号352中描述的原因和对策
对串行编码器(SPC)故障的具体诊断方法为:
①对调伺服放大器(见图5-108)上的编码器电缆插头,观察故障是否转移,若对调后故障转移至另一伺服轴,则故障在串行编码器侧,原因可能是编码器连接电缆不良或接口插头故障、编码器本身故障(如编码器内部电路+5V电源电压低、控制电路板不良或玻璃板脏等);若对调后故障未移至另一伺服轴(仍为该轴报警),则故障为伺服放大器控制电路板或CNC系统轴控制卡不良。
②对调同规格的伺服放大器控制电路板,若故障移至另一伺服轴,则故障在伺服放大器控制电路板上;若对调后故障未转移,则系统轴控制卡有问题。
③进行伺服参数的初始化,若故障解除,则说明伺服参数存储软件不良;若伺服参数初始化后仍报警,则故障为系统主板不良。
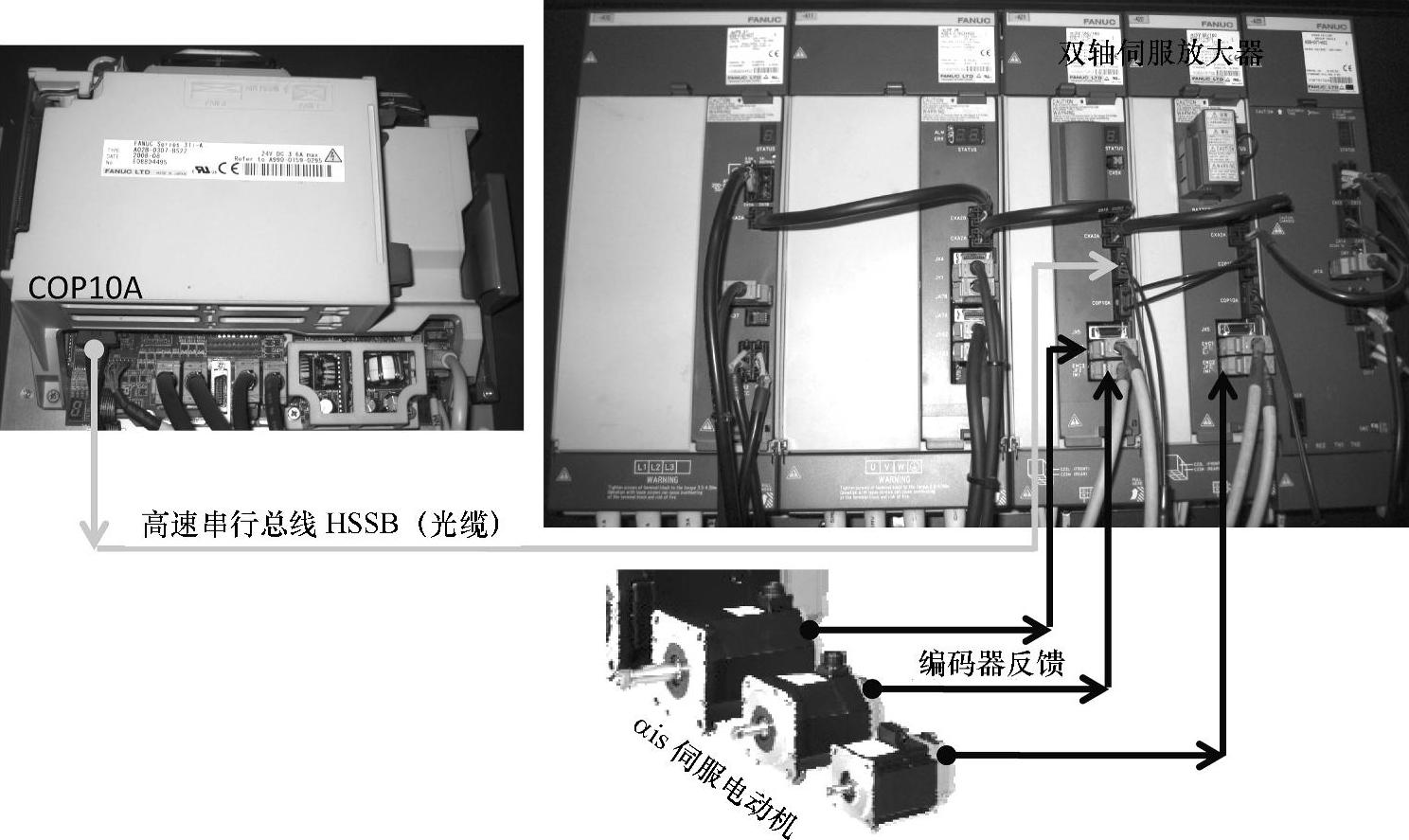
图5-108 HM1250卧式加工中心(FANUC31iMA系统)进给伺服系统的实物连接图
(5)绝对位置检测装置(APC)的报警及故障维修数控机床的进给伺服采用绝对位置检测装置时,系统断电后靠备用电池(标准为DC6V)来进行机床位置的记忆。绝对位置检测装置可为伺服电动机内装编码器,也可为外接独立编码器或光栅尺。表5-12为FANUC 16i/18i/21i/0iB/0iC/0iD/30i系统绝对位置检测装置的报警代码及故障原因。
表5-12 FANUC 16i/18i/21i/0iB/0iC/0iD/30i系统绝对位置检测装置报警代码及故障原因
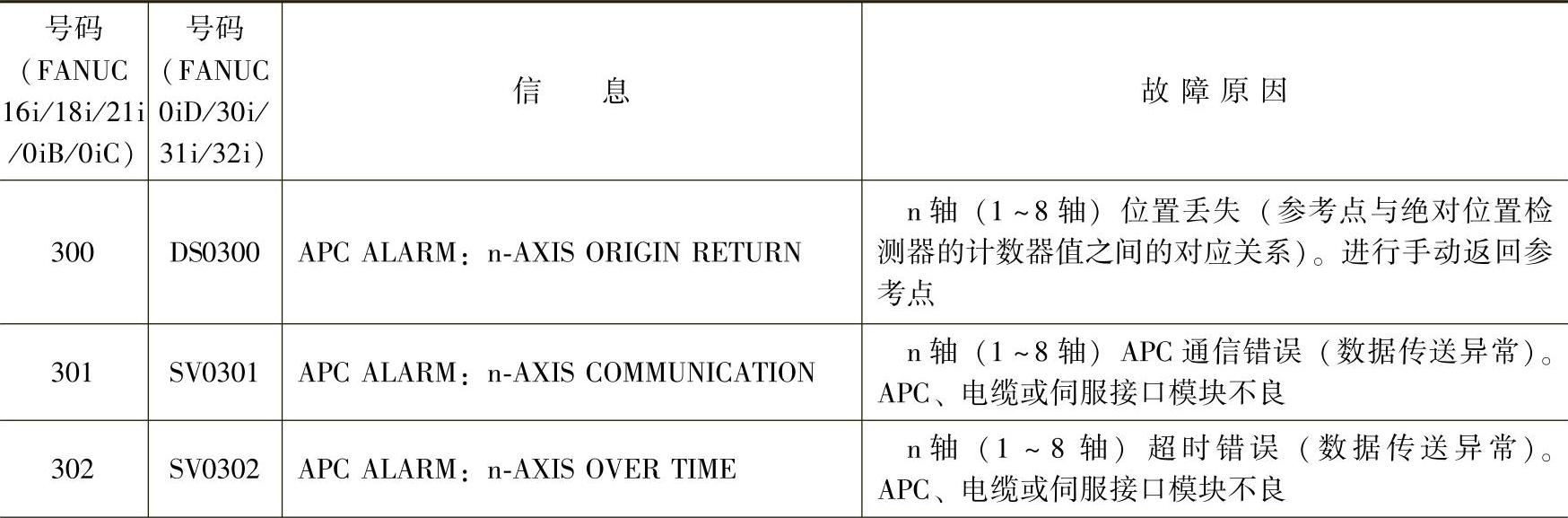
(续)
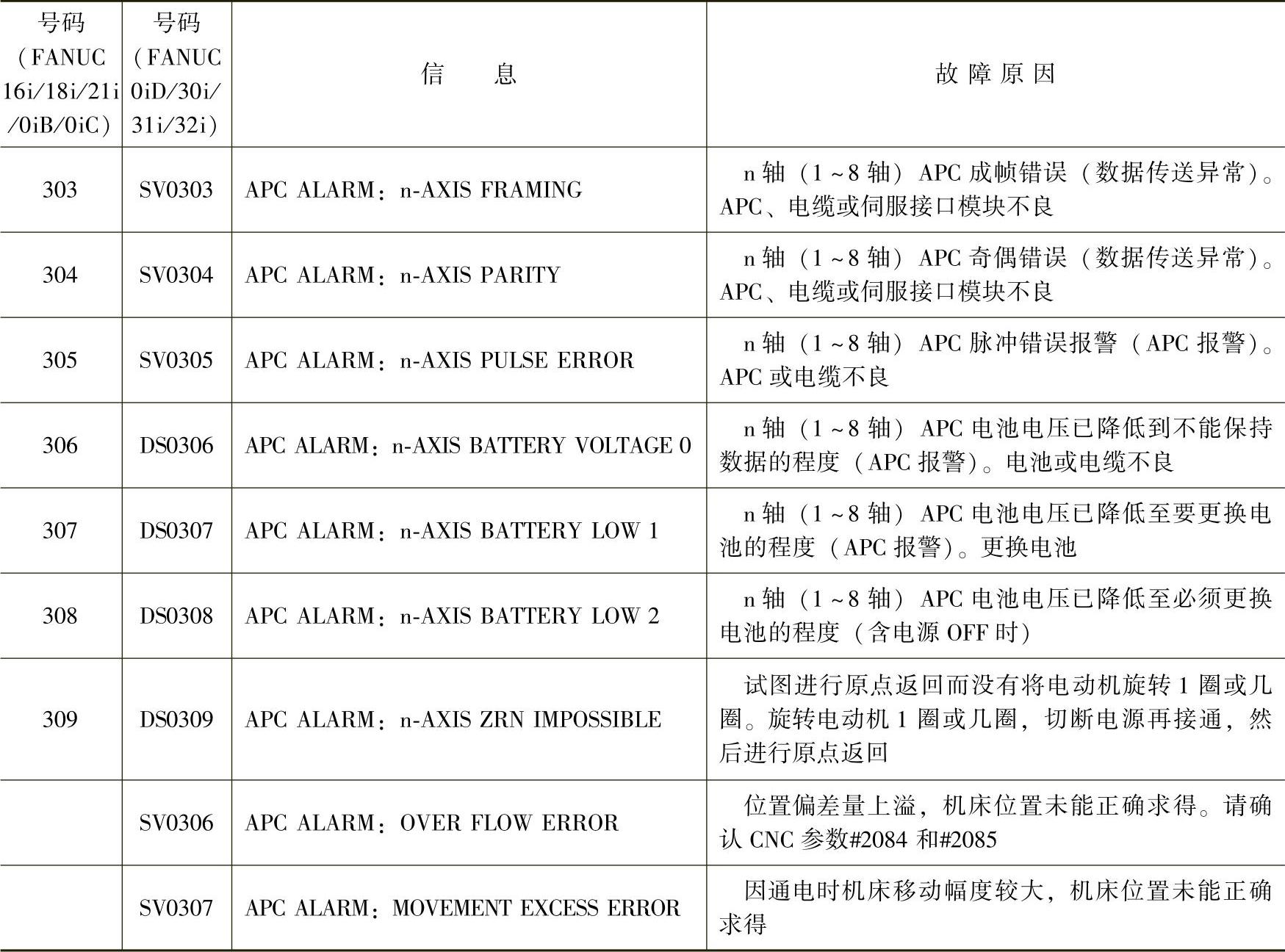
1)数控机床绝对位置丢失故障(报警号为#300/#DS0300)的原因(见图5-109)。
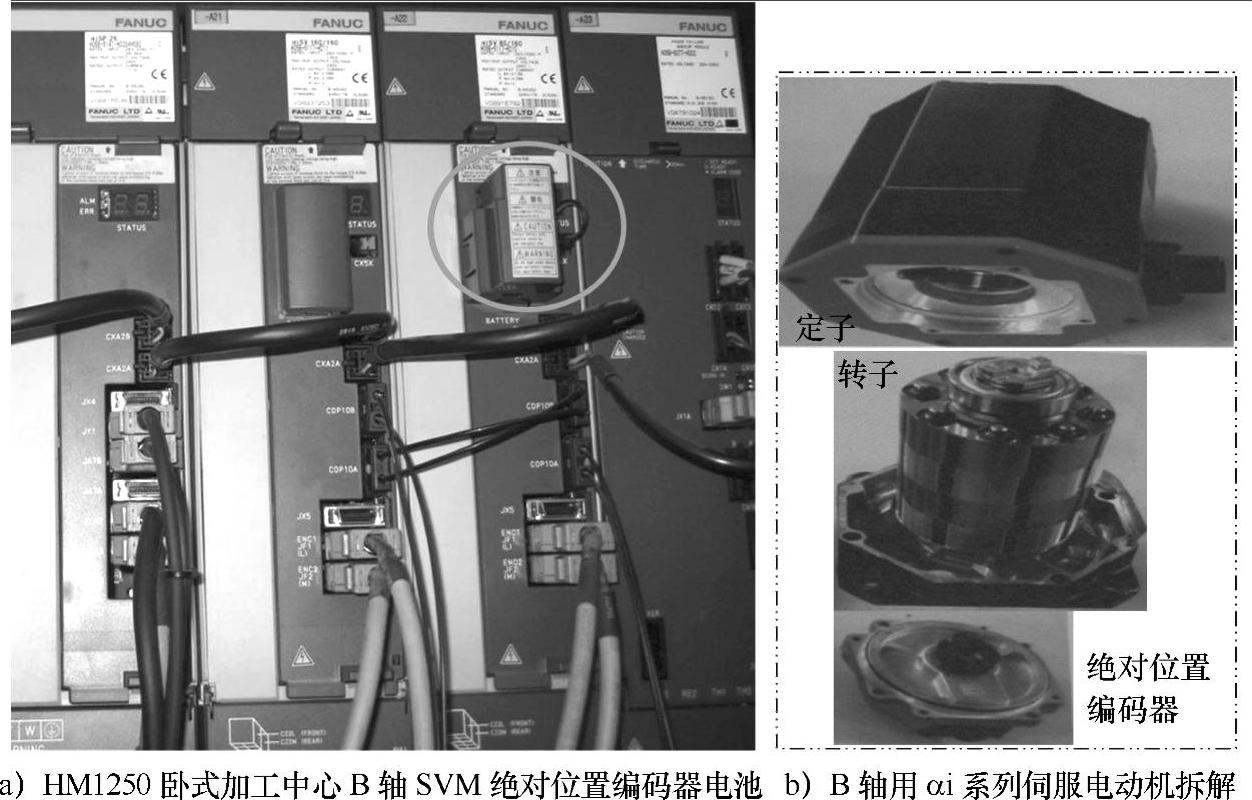
图5-109 数控机床绝对位置丢失故障
①由于维护不当,绝对位置编码器电池电压不足导致机床绝对位置丢失。
②伺服电动机或伺服放大器故障修复后导致机床绝对位置丢失。
③机械故障拆修后导致机床绝对位置丢失。
④系统参数覆盖及参数初始化操作后导致机床绝对位置丢失。
2)无挡块返回参考点控制的数控机床出现绝对位置丢失故障的处理方法。
①MDI方式下,修改FANUC 16/16i/18/18i/21/21i/0i/30i系统CNC参数#1815.5/APCx=0,不使用绝对位置编码器使系统为增量式光电编码器方式,以防止“飞车”现象发生;CNC提示#000报警(要求关机)。
②系统断电重启,手动移动各伺服轴返回机床参考点。
③MDI方式下,设定CNC参数#1815.5/APCx=1(使用绝对位置编码器)和#1815.4/APZx=1(使用绝对位置编码器时,机械位置与绝对位置编码器的位置一致);CNC又提示#000报警(要求关机)。此时观察机械坐标系跳变为参数#1240设定的值。
④系统断电重启后,观察参考点建立信号F120/ZRFn=1(n为伺服轴号)。
3)有挡块返回参考点控制的数控机床出现绝对位置丢失故障的处理方法。
①MDI方式下,修改FANUC 16/16i/18/18i/21/21i/0i/30i系统CNC参数#1815.5/APCx=0,不使用绝对位置编码器使系统为增量式光电编码器方式,以防止“飞车”现象发生。
②系统断电重启后,手动控制各伺服轴到机床参考点位置。
③手动移动各伺服轴离开参考点一定的距离(电动机1转以上位置),以防止返回参考点时系统出现90号报警(因返回参考点的起点离参考点太近或速度太低,使返回参考点不能正常进行)。
④MDI方式下,设定CNC参数#1815.5/APCx=1(使用绝对位置编码器);CNC提示#000报警(要求关机)。
⑤系统断电重启,手动控制各伺服轴到参考点位置,测量当前参考点位置与未丢失参考点之前正确位置之间的差值(轴移动至参考点位置后,自屏幕读取“机械坐标”,将此时产生的误差换算为补偿的脉冲偏移量,如检测单位0.001mm/脉冲的机床,停止位置误差为1.0mm时,栅格偏移量为1000个脉冲)。
⑥对机床的栅格偏移量参数#1850进行修正(基于原设定值),输入“shift+新偏移量”,按[+输入]软键即可完成设定。若轴的停止位置比以前的位置提前时,以“-”值输入新偏移量;无符号时系统默认为“+”值。
⑦系统断电重启后,执行手动返回参考点操作,此时参数#1815.4/APZx由0自动变为1;确认参考点停止位置的正确性,若存在误差,可以同样的操作更改栅格偏移量参数#1850,对参考点停止位置进行微调整。
4)数控机床绝对位置丢失故障修复过程中的注意事项。
①事先掌握数控机床实际出厂时机床参考点的具体位置。
②若机床参考点位置偏移或与出厂实际位置不符时,调整后需要重新进行机床螺距误差补偿和刀具补偿。
③若数控机床为加工中心,需重新调整换刀点,否则换刀时易出现“撞刀”现象。
④更换绝对位置编码器电池时,需在系统通电状态下进行。
(6)分离型检测装置(光栅尺)的控制原理
1)光栅的组成结构及分类。光栅利用光的透射或衍射原理,通过光敏元件测量莫尔条纹移动的数量来测量数控机床工作台的位移量,一般用于数控机床进给伺服系统的闭环控制。光栅主要由标尺光栅和光栅读数头(包括指示光栅、光源、透镜、光敏元件和转换电路)两部分组成。通常,标尺光栅固定在机床的运动部件上(如工作台或滚珠丝杠),光栅读数头安装在机床的固定部件上,标尺光栅和指示光栅的平行度及两者之间的间隙(0.01~0.1mm)要严格保证。
从位移量的测量种类分类,光栅分为直线光栅和圆光栅。直线光栅用于测量直线位移量,如机床X、Y、Z、U、V、W等直线轴的闭环控制;圆光栅则用于测量旋转位移量,如机床A、B、C等回转轴的闭环控制。
从光信号的获取原理分类,光栅可分为玻璃透射光栅(长度3m以下)和金属反射光栅(长度超过3m)。其中,玻璃透射光栅是在透明的光学玻璃上用真空蒸镀的方法镀上一层不透明的金属膜,然后用光刻或照相腐蚀的办法制成平行且等距的透光和不透光相间的密集线纹(圆光栅为向心线纹/同心圆),最终由光的透射现象形成光栅。玻璃透射光栅的特点:光源的垂直入射使其信号幅度大及读数头结构简单;刻线密度大,分辨率高;标尺光栅相对移动时读数头获得脉冲信号,其位移与脉冲数成比例。金属反射光栅一般在不透明的金属材料上刻细线纹,利用光的全反射或漫反射形成光栅。金属反射光栅的特点:标尺光栅的线膨胀系数易与机床材料一致,易于接长或制成整根的长光栅,不易碰碎但怕弯折,且分辨率比玻璃透射光栅低。
另外,光栅的输出信号有TTL电平脉冲信号和电压或电流正弦信号两种形式。
光栅安装在机床上,容易受到油雾、切削液的污染而造成信号丢失,从而影响位置精度的控制,所以得对光栅定期维护(通入干燥、精过滤的低压压缩空气和无水酒精或丙酮擦拭)以保持其清洁;同时玻璃透射光栅需要防止振动和敲击,以免光学元件损坏。
2)四场扫描玻璃透射光栅的工作原理(见图5-110)。四场扫描玻璃透射光栅的测量系统由光源、透镜、标尺光栅、指示光栅、光敏元件和信号处理电路组成,而信号处理电路又包括放大、整形和鉴向倍频等。通常情况下,标尺光栅与机床工作台装在一起并随工作台移动。将光源、透镜、指示光栅、光敏元件和信号处理电路装在一个壳体内,做成一个单独的部件固定在机床上,这个部件称为光栅读数头,其作用是将莫尔条纹的信号转换成所需的电脉冲信号。
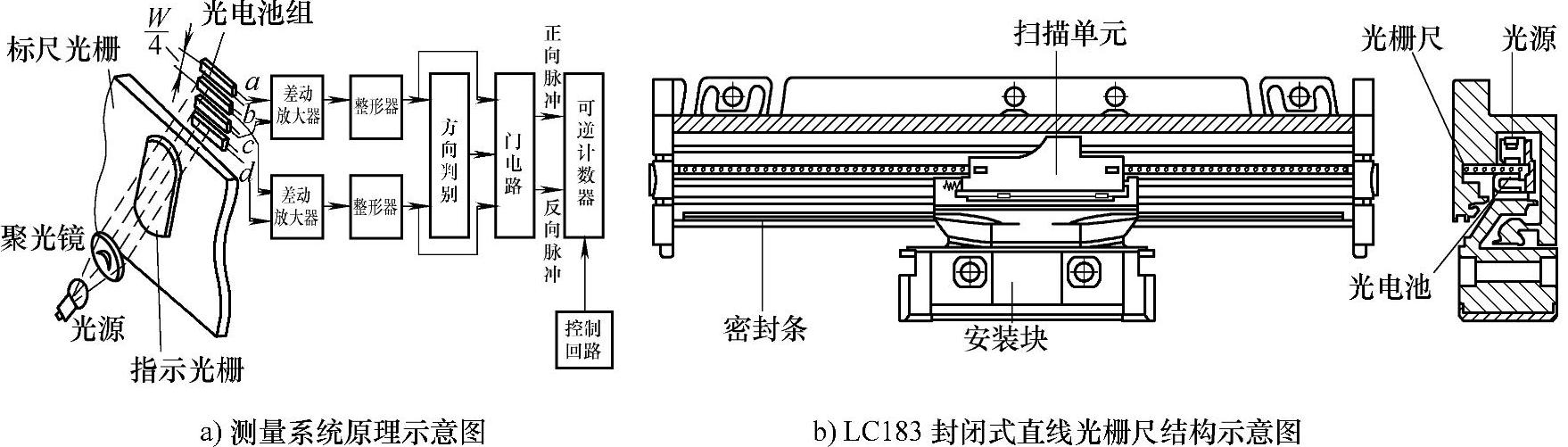
图5-110 四场扫描玻璃透射光栅的工作原理及结构示意图
当标尺光栅随机床工作台一起移动1个栅距,莫尔条纹便移动1个节距。光源通过聚光镜、透过标尺光栅和指示光栅形成忽明忽暗的莫尔条纹光强信号(光强变化近似1个正弦波),光敏元件把光强信号转换为同频率的电压信号,然后经信号处理电路中差动放大器放大至幅值足够大的(16V左右)同频率电压波形,再经整形器整为方波及微分电路使方波的上升沿产生1个脉冲信号,如此对脉冲计数便得到光栅尺的移动距离。为了判断光栅移动的方向,测量系统中至少放置2个光敏元件,两者相距1/4莫尔条纹节距;当莫尔条纹移动时,根据2个光敏元件受光的先后顺序,得到2路相位相差π/2的波形,将输出信号送入鉴向电路,即可判断出光栅的移动方向。
为了提高光栅的分辨率,除了增大刻线密度和提高刻线精度外,还可用倍频的方法细分。通常采用4倍频的细分电路,即莫尔条纹由原来的1个节距变成4个相位依次滞后90°的信号,从而将精度提高4倍。若光栅栅距0.01mm,则工作台每移动0.0025mm就送出1个脉冲,其分辨率为0.0025mm。由此可见,光栅尺测量系统的分辨率不仅取决于光栅尺的栅距,而且取决于鉴相倍频的倍数n,即分辨率
。倍频细分数n除了4以外,还有10、20甚至到50、100倍频细分,可使分辨率达到很高的等级,以应用于更加精密的数控机床中。
3)莫尔条纹的形成(见图5-111)。光栅尺的读数是利用莫尔条纹的形成原理进行的。图5-111中将2块栅距相同、黑白宽度相同(W=π/2)的标尺光栅和指示光栅尺面平行放置,中间保持0.01~0.1mm的间隙,且指示光栅在其自身平面内倾斜一很小的角度,以便使指示光栅的刻线与标尺光栅的刻线间保持一很小的夹角θ。当光源照射光栅时,在a-a线上2块光栅的线纹彼此重合,形成1条横向透光亮带;在b-b线上2块光栅的线纹彼此错开,形成1条不透光的暗带,这些横向明暗相间出现的亮带和暗带即为莫尔条纹。
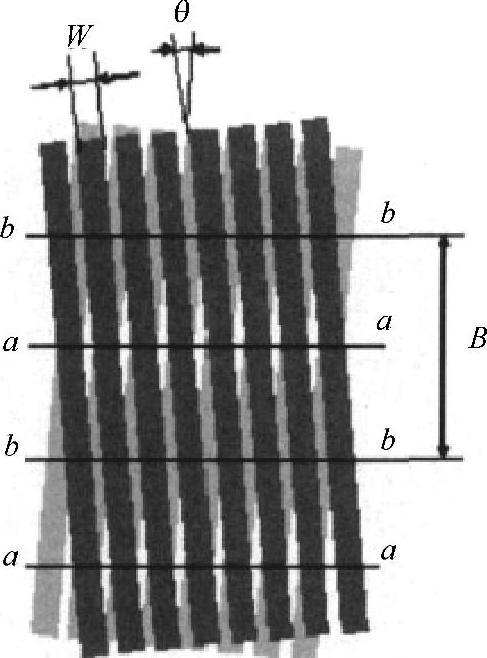
图5-111 莫尔条纹
2条暗带或2条亮带之间的距离称为莫尔条纹的节距B。若光栅的栅距为W,两光栅线纹夹角为θ,则它们之间的几何关系为
。因夹角θ很小,故可取sin(θ/2)≈θ/2,从而上式可改写为B=W/θ。由此可见,θ越小,B越大,即把栅距W扩大了1/θ倍后,转化为莫尔条纹。如栅距W=0.01mm,夹角θ=0.001rad,则莫尔条纹的节距B=10mm,即扩大了1000倍。
2块光栅每相对移动1个栅距,光栅某一固定点的光强按“明→暗→明”规律变化一个周期,即莫尔条纹移动1个节距。因此,光电元件只要读出移动的莫尔条纹数,就可得知光栅移动了多少栅距,从而得出运动部件的准确位移量。
4)单一场扫描金属反射光栅的工作原理(见图5-112)。由于玻璃透射光栅对工作环境的要求较高,机床不能产生过大的振动,且光栅长度不能超过3m,故通常适用于中小型的数控机床。
1968年,海德汉公司研制出由2个不同周期的扫描光栅和钢基标尺光栅(采用AUDIADUR工艺在长度>3m的钢带上镀金光栅条纹)组成的单一场扫描金属反射光栅,它利用光的衍射性能,光线通过扫描光栅产生相位移。该光线经标尺光栅反射,在光源的同侧由光电池接收到4个交变的正弦信号,最终生成2个相位差为90°的正弦交流信号并输出(与四场扫描相同)。
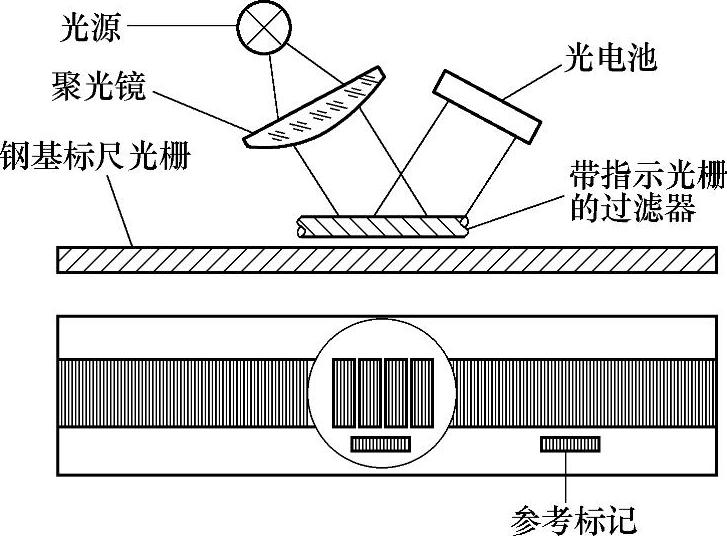
图5-112 单一场扫描金属反射光栅的工作原理图
采用单一场扫描的标尺光栅上局部污染对各组信号的影响大致相同,相对玻璃光栅尺,其污染造成的测量误差较小;可适用于较大测量行程的数控机床。
(7)分离型检测装置(光栅尺)的报警及故障维修FANUC 16/18/21/0iA系统把光栅尺的信号直接反馈至CNC系统的主板,由主CPU进行处理;而FANUC 16i/18i/21i/0iB/0iC/0iD/30i系统把光栅尺信号反馈至系统的位置模块,通过伺服总线完成与CNC系统轴控制卡的数据交换(见图5-113)。当分离型检测装置传输出错或异常时,CNC系统出现的报警代码及故障原因见表5-13。
海德汉直线光栅尺常见故障及处理方法。
①维护不当或光栅尺密封不良造成光栅尺被污染(见图5-114)。光栅尺被污染的原因多为机床切削液、液压油或油脂直接进入,及粉尘、油雾或水雾的浸入等。据统计,污染因素占光栅尺故障因素的63%,因此非常有必要采取措施避免光栅尺被污染。
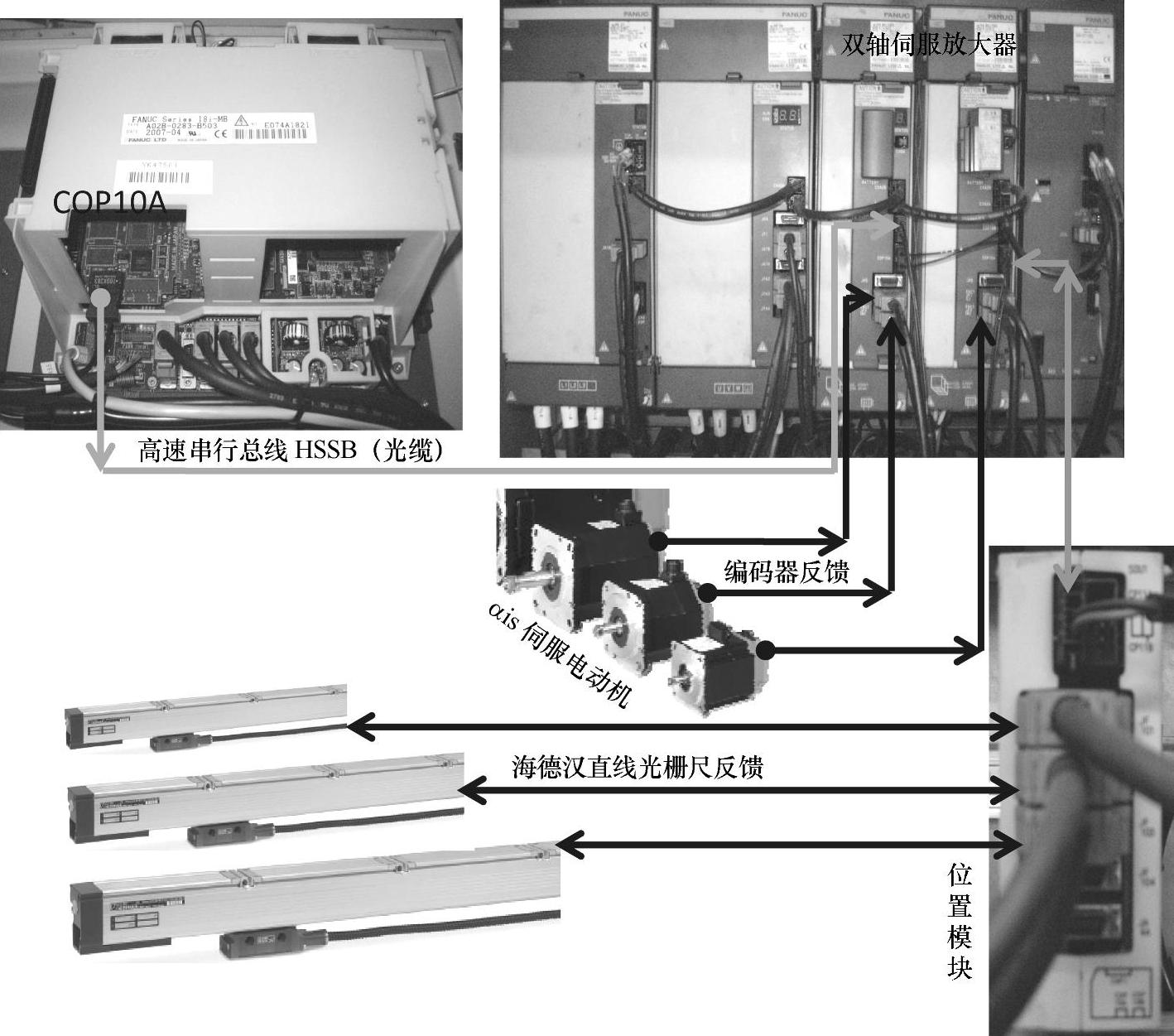
图5-113 HB500卧式加工中心(FANUC 18iM系统)全闭环进给伺服系统的实物连接
表5-13 FANUC 16i/18i/21i/0iB/0iC/0iD/30i系统分离型检测装置的报警代码及故障原因
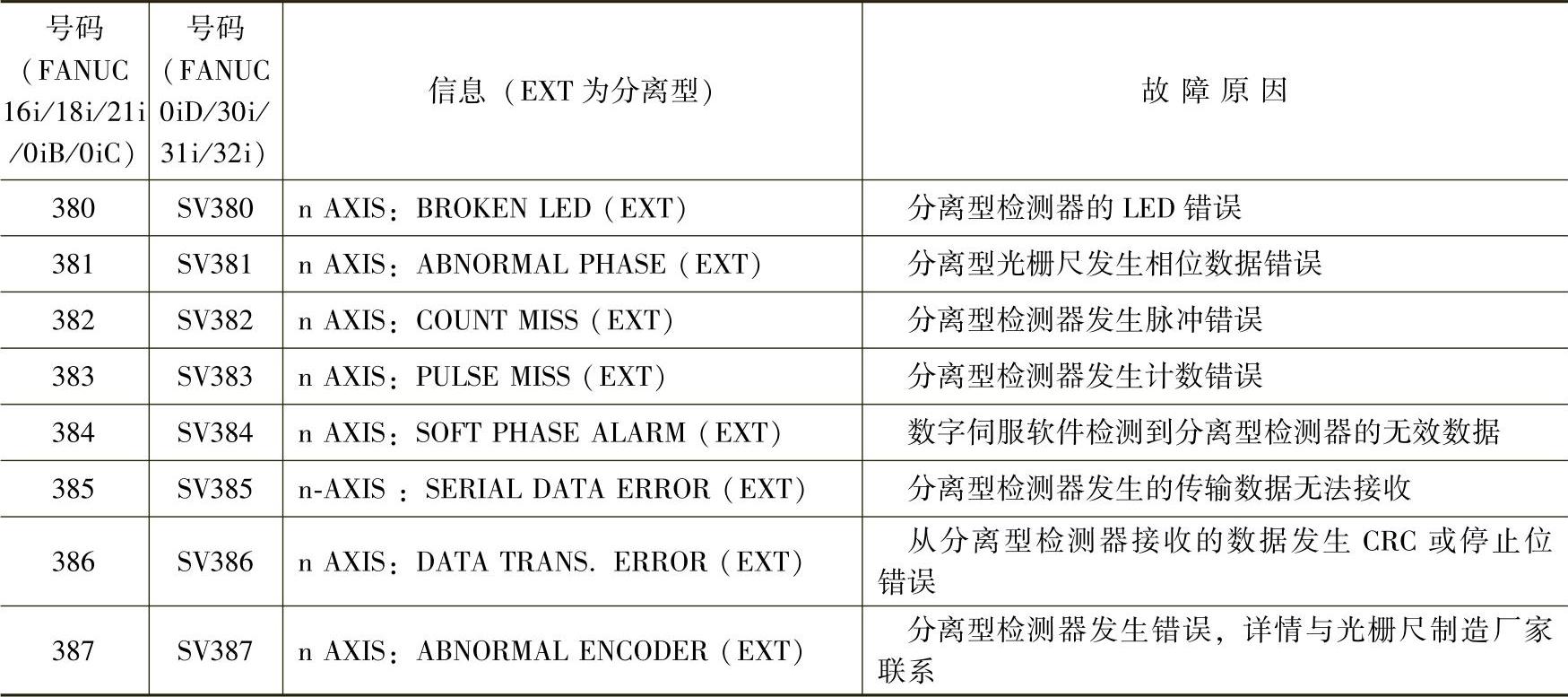
避免光栅尺污染的措施有4条:在光栅尺外面加装防护罩,避免油污的浸入;保持环境清洁,定期清理光栅尺防护罩下面的灰尘和金属碎屑;对光栅尺使用的压缩空气增加带干燥功能的精过滤装置(如DA300),防止油水冷凝以避免读数故障;定期检查并更换光栅尺的密封唇条。
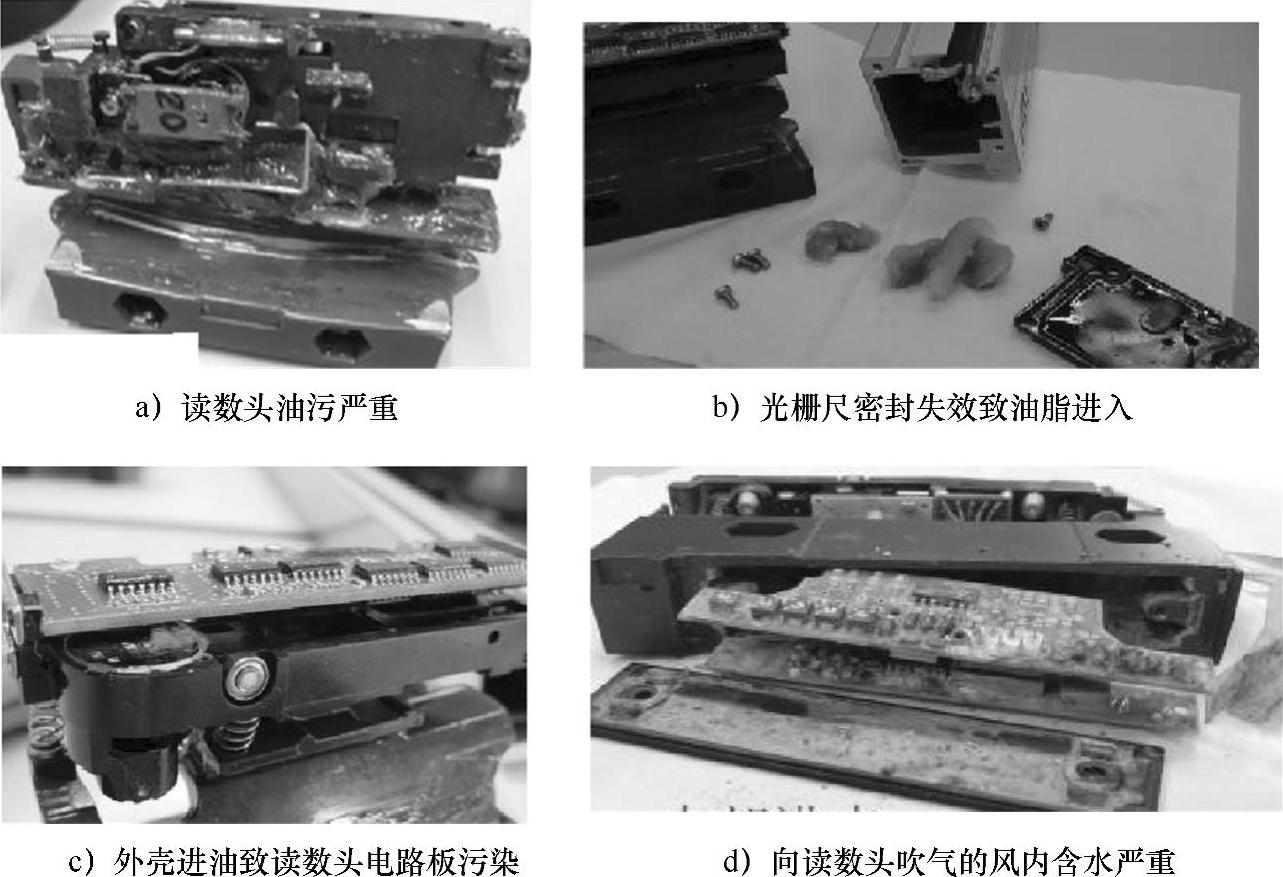
图5-114 维护不当或光栅尺密封不良造成光栅尺被污染的实例
②光栅尺安装不当造成其机械部分损坏(见图5-115)。光栅尺损坏主要是读数头、光栅尺外壳、玻璃标尺光栅及多段光栅尺的钢带标尺光栅等部件的损坏。据统计,安装不当因素占光栅尺故障因素的20%。
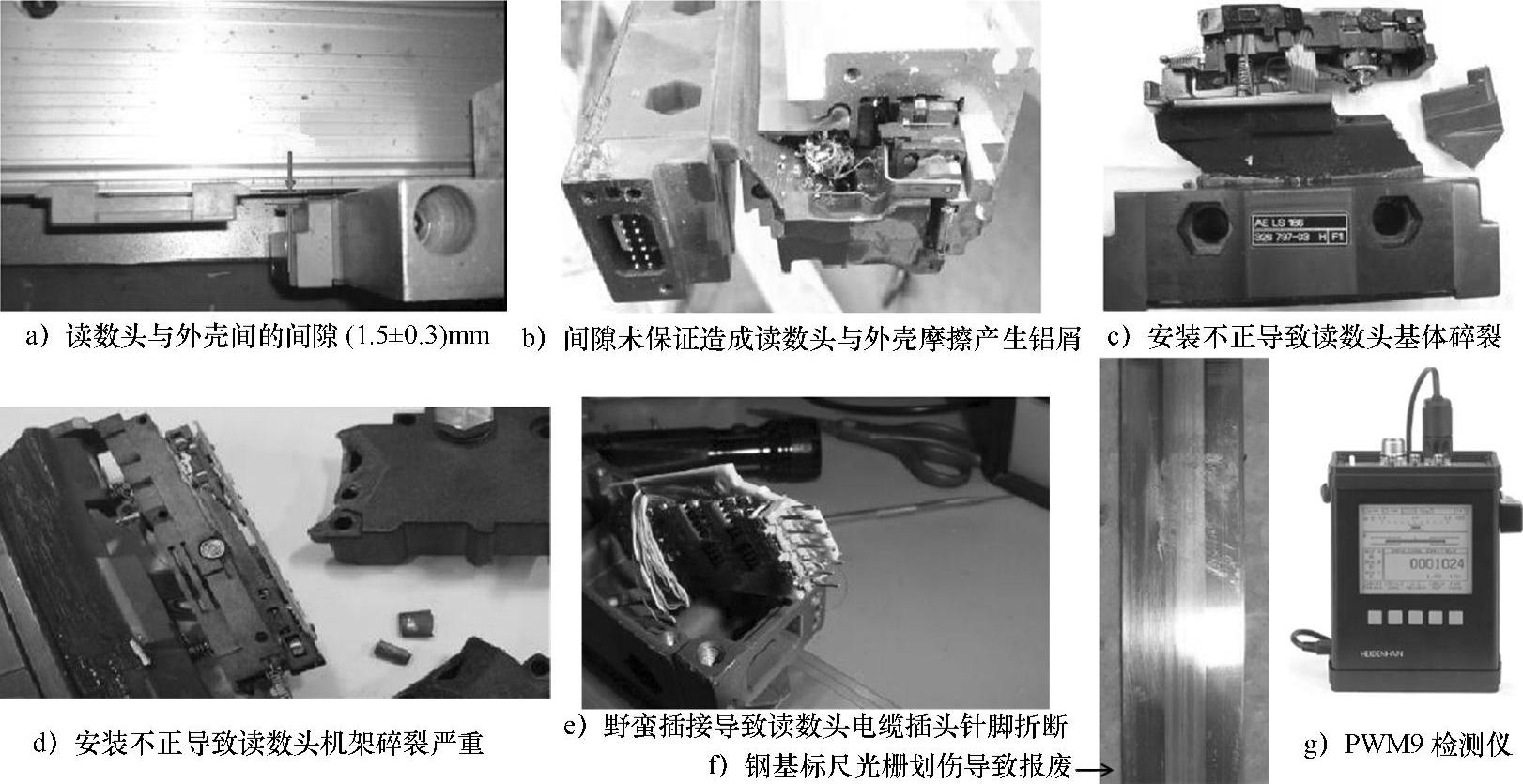
图5-115 光栅尺安装不当造成其机械部分损坏的实例
维修人员应当严格按照《光栅尺安装说明书》的要求,认真细致地安装光栅尺,用指示表检查安装基面等部位的平行度和垂直度;采用光栅尺制造厂家提供的读数头专用卡具,辅助安装读数头,以确保读数头与光栅尺外壳配合的位置正确。有条件的话,可借助专业检测仪(如海德汉的PWM9)检测光栅尺的安装是否正确。
③光栅尺读数头光源及电路、电缆损坏(见图5-116)。导致读数头LED(光源)或电路板损坏的原因有读数头的电路被电源瞬间高压冲击损坏,光栅尺电缆线接错(如电源正负极接反)致电路短路,或读数头电路板上存在导电异物而致电路短路。此时,应检查光栅尺的供电电源电压DC5V是否正常,读数头电路板是否清洁干燥等。
电缆损坏可能导致电路短路、无信号、信号幅值低或信号干扰等故障,此时应检查电缆插头是否正确连接,电缆的外部损伤(破损或挤压等),可用新电缆测试光栅尺信号是否正常等。
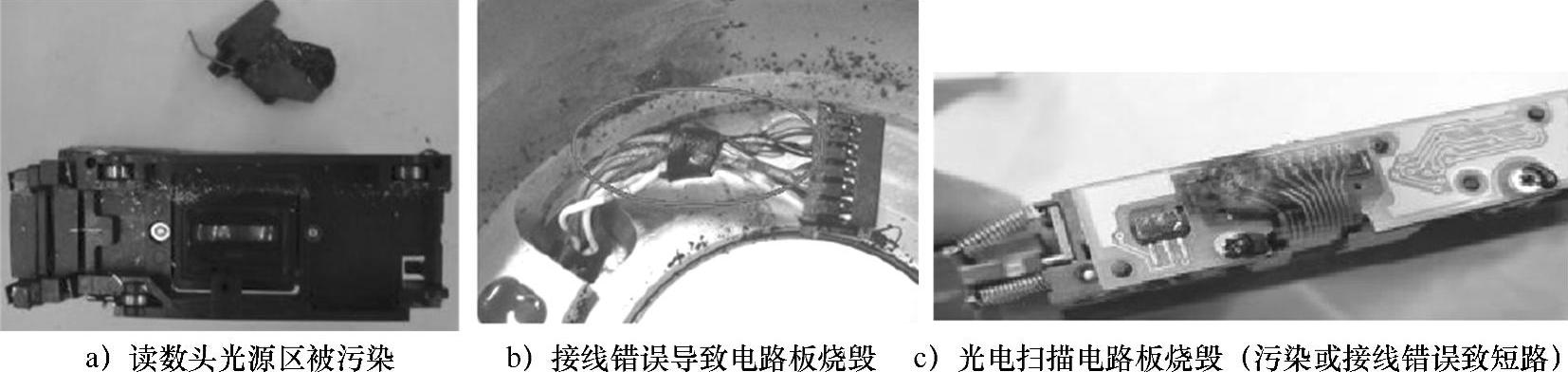
图5-116 光栅尺读数头光源及电路、电缆损坏的实例
④因光栅尺接地、屏蔽等导致反馈信号被干扰(见图5-117)。反馈信号被干扰一般与光栅尺电缆的屏蔽、信号电缆与交流强电布线不合理、机床接地不合理、系统供电主电路的滤波不良等有关,造成机床出现伺服轴位置漂移、跟随误差大或定位不稳定。此时应检查电缆屏蔽、电缆布线方式、机床接地或系统主电路滤波以及光栅尺的接地电阻小于1Ω。
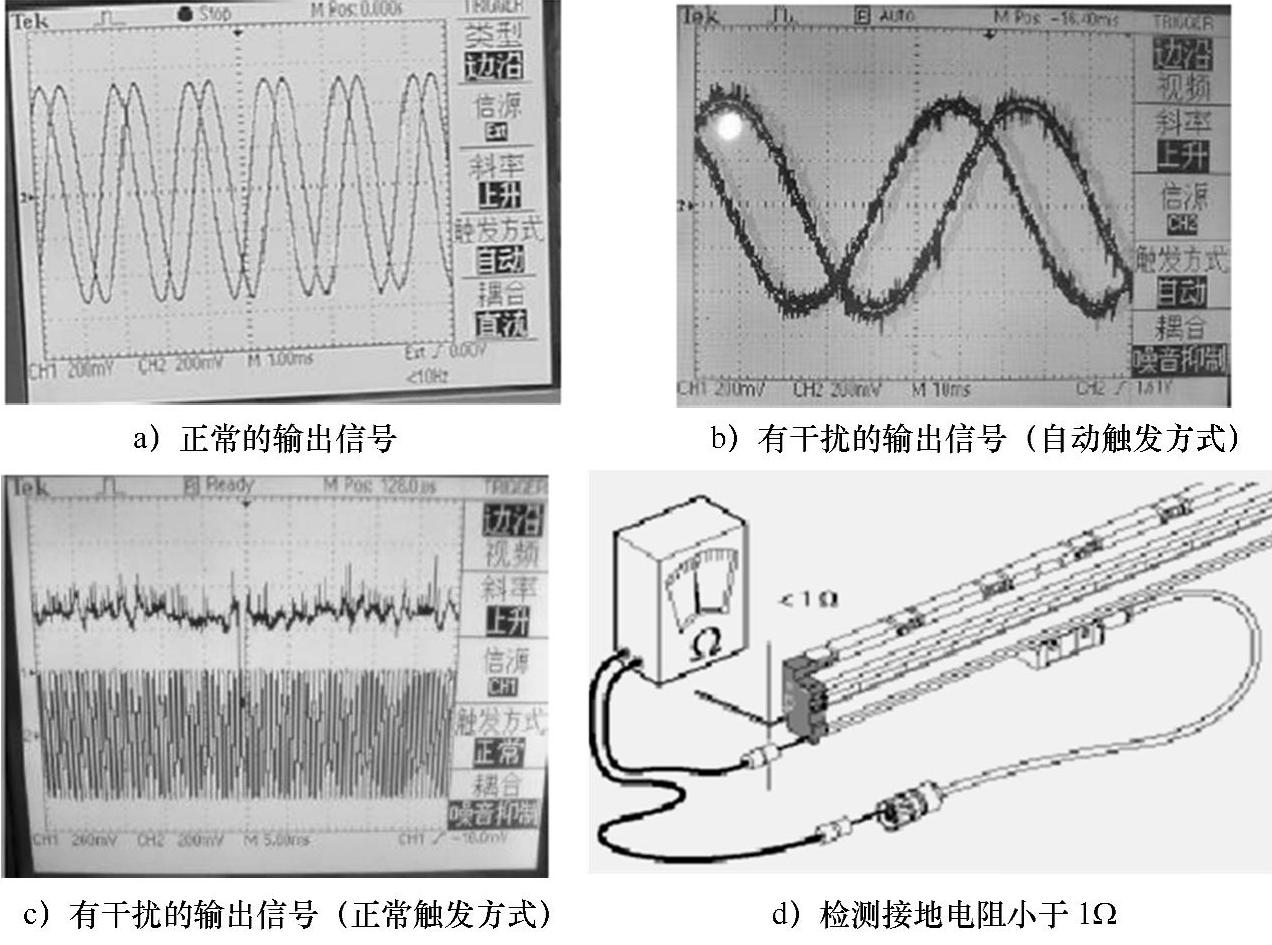
图5-117 因光栅尺接地、屏蔽等导致反馈信号被干扰
⑤除以上几点外,还可能由于光栅尺安装基面和支架的机械结构不正确、光栅尺故障、机床进给伺服的参数未调整好或机床机械故障(滚珠丝杠副或导轨副磨损)等,会导致数控机床出现强烈的振动现象。
(8)屏蔽光栅尺的方法及注意事项数控机床实际维修中因故障诊断或应急处理,常对光栅尺进行屏蔽处理。
1)FANUC 16i/18i/21i/0iB~D/30i系统屏蔽光栅尺的具体步骤。
①屏蔽光栅尺前,在系统开机BOOT引导画面下对系统数据进行系列备份,以便对光栅尺的数据进行恢复。
②修改CNC参数#1425(故障伺服轴返回参考点时的FL速度)的数值,由原来的100mm/min增大为200mm/min。
③系统是否使用反向间隙加速功能(#2003.5/BLEN):由原来的1改为0。
④当系统使用分离型检测装置时,将系统的双位置反馈功能(#2019.7/DPFB)由原来的1改为0。
⑤故障伺服轴由全闭环控制方式变为半闭环控制方式(#1815.1/OPTx):由原来的1改为0。
⑥按半闭环控制方式设定该轴的伺服参数,包括柔性进给齿轮比N(#2084)/M(#2085)、位置反馈脉冲数#2024和参考计数器容量#1821。
⑦设定振荡抑制系数#2033=0,系统断电重启即可。
2)屏蔽光栅尺的注意事项。
①机床参考点位置发生了变化(即由光栅尺的标记位确立栅位改为由电动机内装编码器确立),加工工件坐标系变化,尤其是带有自动换刀和自动对刀器时要重新调整。
②机床的精度要下降,加工工件的工艺要求能否满足。
③重新进行机床反向间隙的测量(操作方法见第5.3.1节)和CNC参数的补偿(#1851为切削进给方式的反向间隙补偿量,#1852为快速进给方式的反向间隙补偿量)。
相关推荐