【摘要】:根据数控机床所要完成的加工任务的不同,数控机床对进给部分的要求也不尽相同,通常可概括为以下几个方面:1)正、反向可逆运行:加工过程中,机床工作台处于随动状态,能根据加工轨迹的要求,在CNC控制下实时正、反方向运动,且方向变化时不存在反向间隙和运动能量的损失。一般可通过缩短传动链、合理选择丝杠、对滚珠丝杠副和支承部件适当预紧等方式来提高数控机床进给部分的传动刚度。
根据数控机床所要完成的加工任务的不同,数控机床对进给部分的要求也不尽相同,通常可概括为以下几个方面:
1)正、反向可逆运行:加工过程中,机床工作台处于随动状态,能根据加工轨迹的要求,在CNC控制下实时正、反方向运动,且方向变化时不存在反向间隙和运动能量的损失。
2)调速范围宽(最高进给速度和最低进给速度之比):受刀具、工件材质及加工要求的变化,为了获得最佳切削条件和良好的工件加工质量,数控机床要求进给速度可在很大范围内(一般0~24m/min)实时变化,即调速范围宽。在调速范围内速度要均匀、稳定且在0.1r/min的低速或更低速时无爬行现象;零速时伺服电动机处于电磁锁住状态,以确保定位精度不变。
3)高精度:数控机床按预定程序自动加工时,实际位移与指令位移的差值要尽可能小,甚至没有。通常,数控机床的位移精度可达到0.01mm甚至0.001mm,高端数控机床的位移精度可达到0.1μm,甚至可实现纳米级加工。
4)良好的快速响应特性且无超调:为保证轮廓切削的形状精度和加工表面较低的表面粗糙度值,要求进给部分除具有较高的定位精度外,还需具有良好的快速响应特性,即指令信号的跟踪响应要快。这是因为数控系统在启动和制动时,要求加减速度足够大,以缩短进给系统的过渡时间和减小轮廓过度误差;同时要求尽可能小的时间常数和启动电压,以保证伺服电动机在0.2s内从静止起动达到额定转速。
5)低速大转矩和过载能力强:强力切削机床的进给驱动可实现低速大转矩切削,其伺服电动机可长时间过载而不烧毁。一般来说,伺服放大器具有数分钟甚至半小时内1.5倍以上的过载能力,在短时间内可以过载4~6倍而不损坏。
6)高刚度:数控机床进给部分的高刚度取决于滚珠丝杠副或蜗轮蜗杆副及其支承部件的刚度。刚度不足且摩擦阻力大时,将导致工作台爬行、反向死区及影响传动的准确性。一般可通过缩短传动链、合理选择丝杠、对滚珠丝杠副和支承部件适当预紧等方式来提高数控机床进给部分的传动刚度。
7)无传动间隙以确保传动精度:为提高数控机床的位移精度和减小传动误差,要求尽量消除联轴器和齿轮齿条传动副等进给传动部件的间隙,同时CNC装置能根据位置反馈进行间隙的自动补偿(见图5-2)。
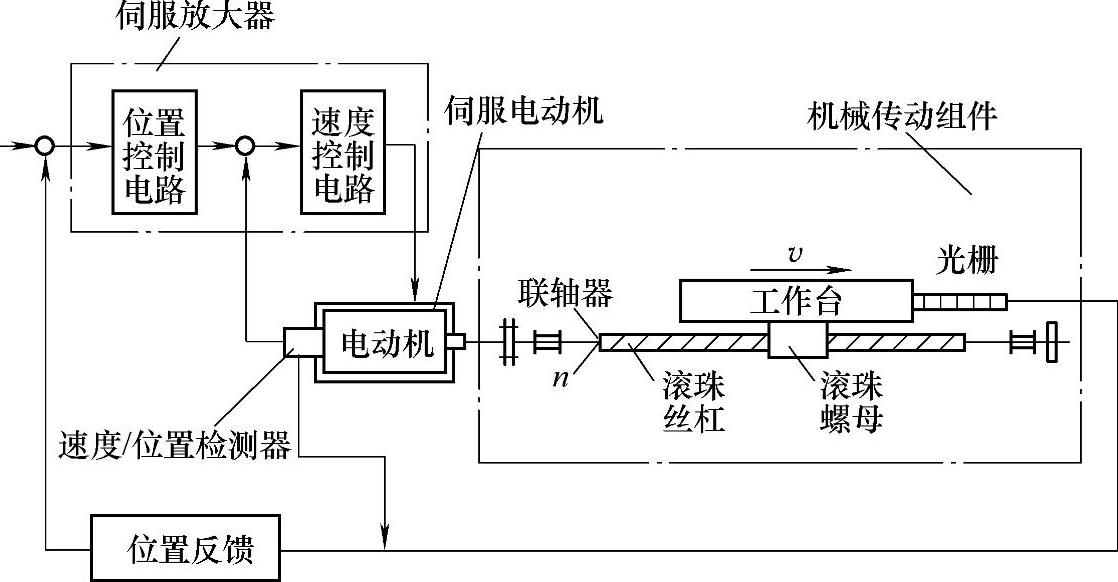
图5-2 数控机床进给部分的全闭环位置控制
相关推荐