【摘要】:在深共晶成分附近,化学镀镍(磷)在刚完成镀覆状态时通常为非晶状态,且具有较低的内应力。图7.6由X射线面式扫描所得的跨界面区域的元素分布图锡;镍;铅;磷图7.7150℃环境下反应500 h后锡铅共晶焊料与化学镀镍(磷)间界面的SEM横截面照片虽然由于化学镀镍(磷)层足够厚而不会发生金属间化合物的剥落现象,但是它与介电保护材料硅的氧氮化物之间的界面强度较弱。
化学镀镍(磷)中含有原子百分含量为15%~20%的磷,且可通过无掩模工艺沉积在已具有图案花样且镀锌的铝表面上。其生长模式为各向同性,且其外观呈蘑菇状。根据Ni-P二元相图,可知在磷成分为19%时,镍与磷具有深共晶点,因此即便不经快速淬火工艺在该成分附近也非常容易形成镍-磷非晶合金。在深共晶成分附近,化学镀镍(磷)在刚完成镀覆状态时通常为非晶状态,且具有较低的内应力。对于在UBM层中的应用,其厚度可超过10μm。
图7.5(a)所示为化学镀镍(磷)UBM层上,锡铅共晶焊球的横截面示意。在镀锌的铝表面上,限定接触窗口的介质材料为氧氮化硅(SiON)。图7.5(b)所示为化学镀镍(磷)UBM层上,直径为100μm的锡铅共晶焊球的SEM横截面照片,在镍(磷)UBM层上,可观察到一层Ni3 Sn4,且其形貌为多面体,其晶粒与Cu6 Sn5的笋钉状形貌有所不同,呈现出粗块型或针状型。然而,在粗块和针状晶粒之间均存在深谷状凹陷。图7.5(c)所示为镍(磷)UBM层拐角处的高倍率SEM照片,从中可观察到在Ni3 Sn4和化学镀镍(磷)之间存在着一层Ni3 P化合物,而在化学镀镍(磷)和氧氮化硅之间也存在着一层Ni3 Sn4化合物。
该Ni3 P化合物呈层状形貌,图7.6(a)~(d)所示为由X射线面扫描所得的跨界面区域中锡、镍、铅和磷的元素分布图,其中,锡的分布与Ni3Sn4中镍的分布相匹配,而磷的层状分布则与Ni3 P层相对应。在Ni3 Sn4生长过程中,它从非晶态镍(磷)中消耗镍元素,并不断提高磷的富集程度,直到其浓度变为75Ni25P,然后结晶成为Ni3P化合物。该过程为非晶镍(磷)通过焊料反应的增强结晶过程,且该反应为守恒反应过程,其中Ni3 P的形成消耗了非晶镍(磷)中几乎所有的磷元素,且几乎没有磷元素会进入焊料中。而由于Ni3 P很容易产生裂纹,因此若形成较厚的Ni3P层,很容易导致脆性断裂。
Ni3 P的生长是扩散控制型生长,其激活能为0.33 eV/原子。而目前尚不清楚主导Ni3 P生长过程的是Ni(P)/Ni3P界面处镍原子的扩散,还是Ni3Sn4/Ni3 P界面上磷原子的扩散。毋庸置疑,Ni3 Sn4中的凹陷或沟道可使镍快速溶解至熔融焊料中。如果磷是主要的扩散原子,这意味着Ni3 P会在Ni3Sn4/Ni3 P界面处分解。随后,当镍原子扩散到熔融焊料中时,磷原子会扩散回到Ni3 P/Ni(P)界面处,从而使镍(磷)富集并结晶。另外,若镍是主要的扩散原子,则它会离开Ni3 P/Ni(P)界面,并通过Ni3 P层扩散至Ni3 Sn4/Ni3 P界面。但是此处更值得关注的是即使Ni3P作为扩散阻挡层发挥作用,整个反应过程所需要的激活能依然很低。此外,在200~240℃环境下的润湿反应中,几分钟时间便可耗尽几微米的镍(磷)层。
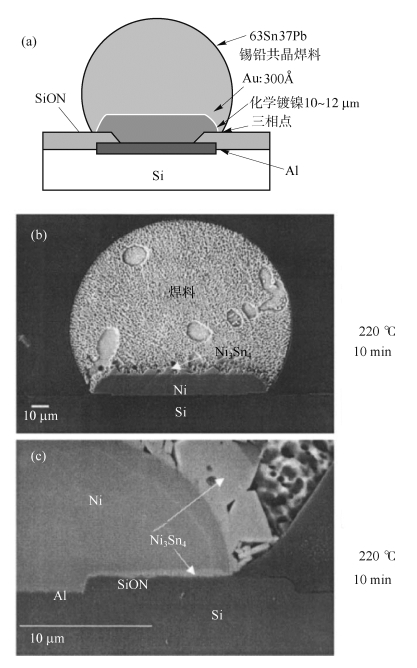
图7.5 化学镀镍(磷)UBM层上锡铅共晶焊球的横截面和SEM照片
(a)化学镀镍(磷)UBM层上锡铅共晶焊球的横截面示意;(b)化学镀镍(磷)UBM层上直径为100μm的锡铅共晶焊球的SEM横截面照片;(c)Ni3 Sn4沿SiON和镍(磷)间界面渗透的SEM横截面照片
然而,在化学镀镍(磷)上的共晶锡铅焊料的固态老化过程中,Ni3 Sn4的生成速率要慢得多。图7.7所示为试样在150℃环境中老化500 h后界面处的SEM横截面照片。Ni3 Sn4的厚度仅为几微米,而我们也不清楚在这样的低温下能否生成Ni3 P。然而此时的Ni3Sn4呈层状形貌,而非粗块型或针状型。通过对比润湿反应和固态反应可再次得出结论:这与锡铅焊料与铜之间的反应相似,润湿反应的速率更快,且自由能增益率更高。
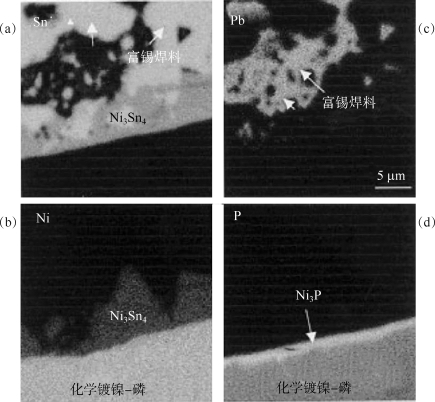
图7.6 由X射线面式扫描所得的跨界面区域的元素分布图
(a)锡;(b)镍;(c)铅;(d)磷
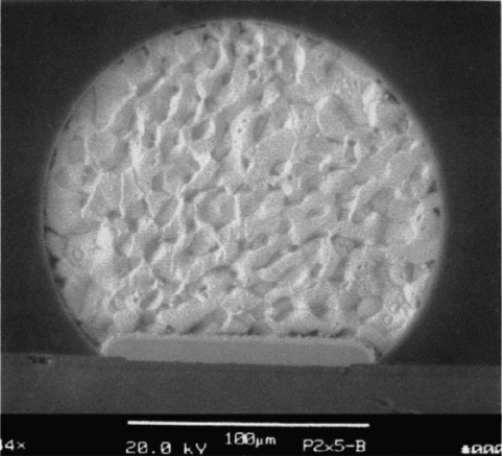
图7.7 150℃环境下反应500 h后锡铅共晶焊料与化学镀镍(磷)间界面的SEM横截面照片
虽然由于化学镀镍(磷)层足够厚而不会发生金属间化合物的剥落现象,但是它与介电保护材料硅的氧氮化物之间的界面强度较弱。图7.5(c)所示为化学镀镍(磷)上焊球的横截面照片,其中,熔融焊料可从化学镀镍(磷)、硅的氧氮化物和熔融焊料的三相点处渗入该界面。该渗透过程在化学镀镍(磷)层和硅的氧氮化物之间形成了Ni3 Sn4化合物,并一直延伸到铝界面。除焊料外,腐蚀性反应物也可以渗透该界面,而这将导致可靠性问题。由于该渗入过程涉及界面扩散和金属间化合物的形成过程,因此研究渗入过程的动力学具有重要意义。该渗入过程的解析解如下[16]:

式中,y0是渗透深度;δ是界面的有效宽度;Di是界面扩散率;b=C34/Ci是金属间化合物中(C34)和界面处(Ci)的成分浓度之比;C0是三相点或界面原点处的浓度;Dc是金属间化合物中的扩散率。从该解析中,可发现渗透深度与
线性相关,这与扩散过程中晶界渗透现象的经典Fisher分析的理论结果相似。
相关推荐